Von Maschinen können durch ihre bloße Anwesenheit, noch mehr aber durch ihren Betrieb Gefahren verschiedenster Art für in der Nähe befindliche Personen, für die Infrastruktur und für die Umwelt ausgehen. Häufig besteht das Gefährdungspotenzial in Form von Verletzungsgefahren oder Gesundheitsgefährdungen durch Emissionen oder unkontrolliert austretenden Betriebsstoffen. Zur Minimierung aller potenziellen Gefahren ist die Einhaltung von Richtlinien und Normen der europaweit gültigen Maschinenrichtlinie seit Ende 2009 obligatorisch. Sie ist der Leitfaden Maschinensicherheit in Europa und betrifft den gesamten Werdegang einer Maschine.
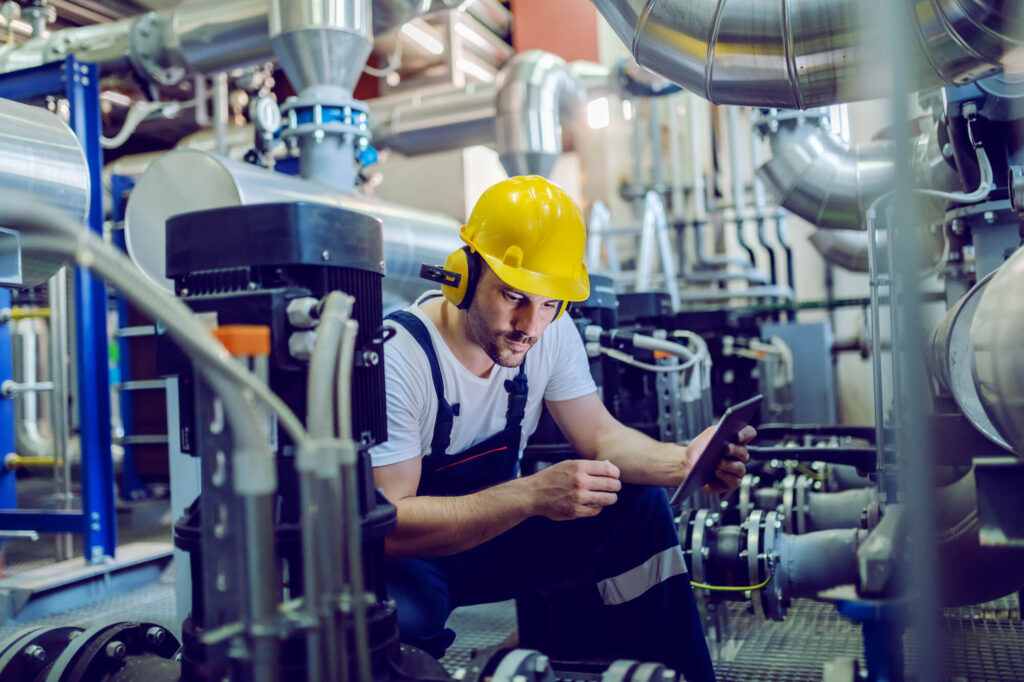
Das Thema kurz und kompakt
- Die Maschinensicherheit ist gemäß DIN EN ISO 12100:2010 eine EU-weit einheitliche Richtlinie zur Eindämmung potenzieller Gefahren, die von Maschinen für Menschen und Umwelt ausgehen können.
- Maschinensicherheit bezieht sich auf den gesamten Produktzyklus einer Maschine und dient der Minimierung von Verletzungsgefahren.
- Eine Maschine gilt als sicher, wenn bei regelgemäßem Betrieb und anzunehmender Bedienfehler kein Gefährdungspotenzial mehr ausgehen kann.
- Seit 2009 ist die Maschinenrichtlinie 2006/42/EG in der EU verbindlich anzuwenden.
Was bedeutet Maschinensicherheit?
Maschinensicherheit dient der Minimierung des Gefährdungspotenzials, das von einer Maschine ausgehen kann. Sie beginnt bereits in der Konzeptionsphase mit einer Risikobeurteilung und Analyse des Gefährdungspotenzials, und hat Einfluss auf konstruktive Merkmale der neuen Maschine.
Aspekte der Maschinensicherheit begleiten das Produkt über den gesamten Lebenszyklus bis hin zur Außerbetriebnahme, Abbau, Zerlegung und umweltgerechten Entsorgung. Verletzungsgefahren für das Bedienpersonal und für in der Nähe befindliche Personen sollten ausgeschlossen, zumindest aber minimiert sein. Das schließt auch denkbare Bedienfehler ein, die durch Unachtsamkeit oder eine mangelhafte Einweisung der Maschinenführerin oder des Maschinenführers entstehen.
Ab wann gilt eine Maschine als sicher?
Falls ein Gefährdungspotenzial für Personen im Umfeld der Maschine besteht, muss dafür gesorgt werden, dass dort durch Absperrungen oder Warnhinweise während des Betriebs Sicherheitsabstände gewahrt werden. Zwischen der Sicherheit einer Maschine und ihrer Funktionssicherheit kann es zu Zielkonflikten kommen. Die Konstrukteure müssen dann einen akzeptablen Kompromiss zwischen Funktionalität und Sicherheit finden. Eine Maschine gilt dann als sicher, wenn bei regelgemäßem Betrieb oder Gebrauch einschließlich anzunehmender Bedienfehler aufgrund von Unachtsamkeit keine Gefahr ausgehen kann.
Schließen Sie sich 700+ Unternehmen an, die mit ToolSense arbeiten
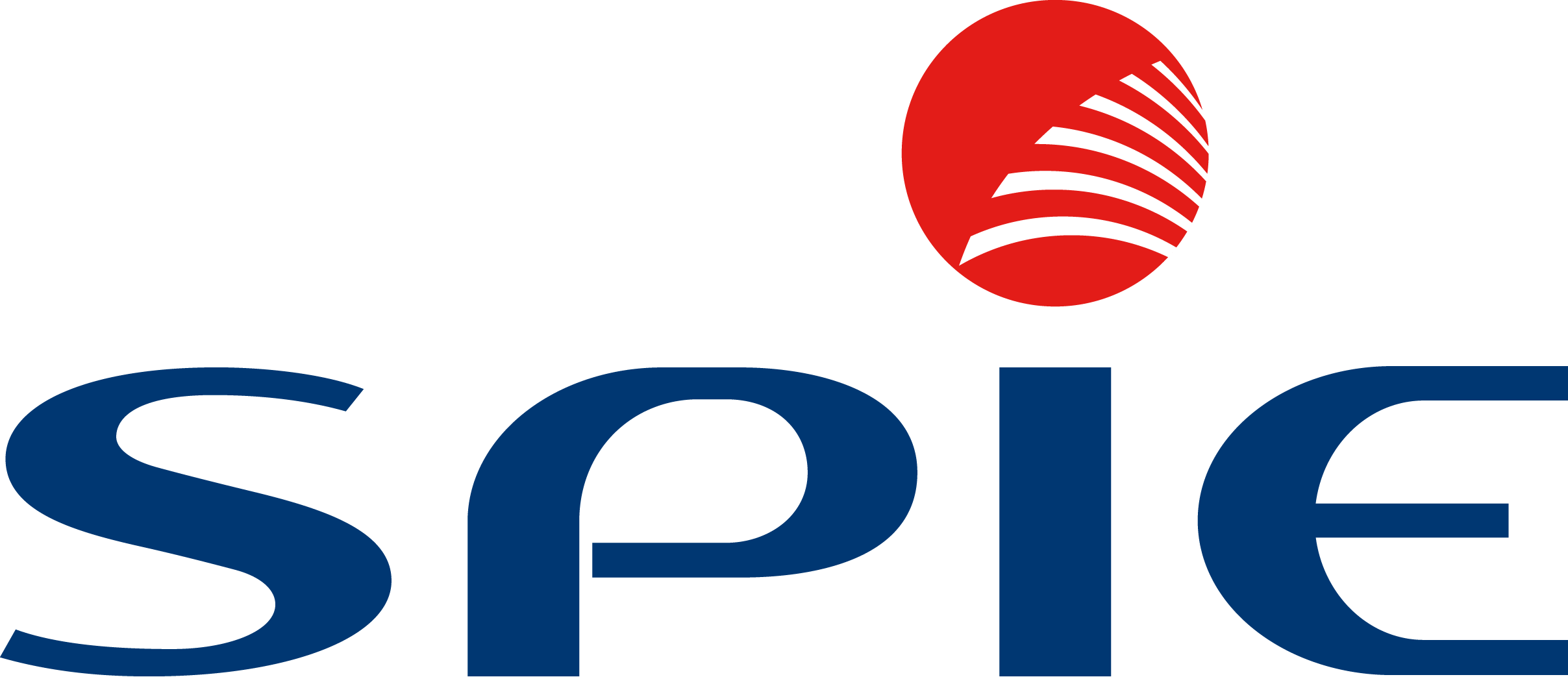
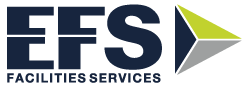
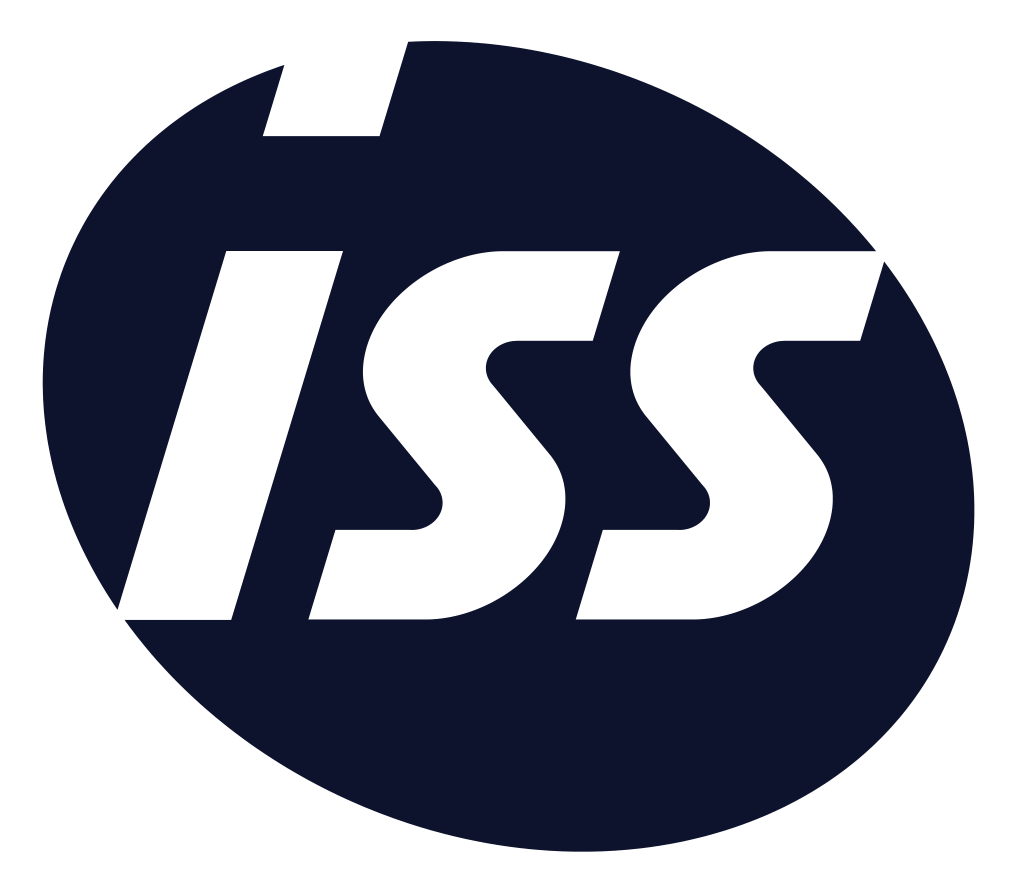
Praxis-Beispiel für Maschinensicherheit
Ein anschauliches Beispiel für die funktionale Sicherheit bieten motorgetriebene Heckenscheren. Um zu verhindern, dass es zu Verletzungen an einer Hand kommt, kann die Heckenschere nur durch ständiges und gleichzeitiges Niederdrücken von zwei Handhebeln in Betrieb genommen werden. Die Hebel sind so angeordnet, dass für ihre Betätigung beide Hände benötigt werden.
Die Hände werden gezwungenermaßen von der Gefahrenquelle ferngehalten. Ein zweites konstruktives Sicherheitsmerkmal bei motorisierten Heckenscheren ist ihr Schnellstopp. Sobald sie einen der beiden „Betriebshebel“ auslassen, schaltet sich das Gerät aus und die Messer stoppen augenblicklich, damit nicht durch Unachtsamkeit oder aus sonstigen Gründen eine Verletzung am Körper entstehen kann.
Welche konkreten Gefahren können von einer Maschine ausgehen?
Das nicht vollständig vermeidbare Gefährdungspotenzial von Maschinen und Anlagen zeigt sich meist während ihres Betriebs. Konkrete Gefahren, die die Maschinensicherheit betreffen, sind wie folgt:
- Mechanische Gefahren; insbesondere direkte Verletzungsgefahr durch nicht abdeckbare rotierende Teile in Maschinenbau, Konstruktion usw.
- Verbrennungs- oder Verbrühungsgefahren; falls sich Teile der Maschine entsprechend aufheizen oder heiße Dämpfe oder Flüssigkeiten austreten.
- Gefahr eines Elektroschlags durch spannungsführende Teile; unsachgemäße Bedienung oder defekte Maschine.
- Gefahr durch Lärmemissionen; bei Überschreitung bestimmter Werte müssen Lärmschutzrichtlinien beachtet werden.
- Gefahr durch ionisierende, radioaktive oder UV-Strahlung; beispielsweise Röntgen und CT-Geräte.
- Gefahr von Gesundheitsgefährdung durch Emissionen; Stickoxide, Kohlendioxid und andere Gase.
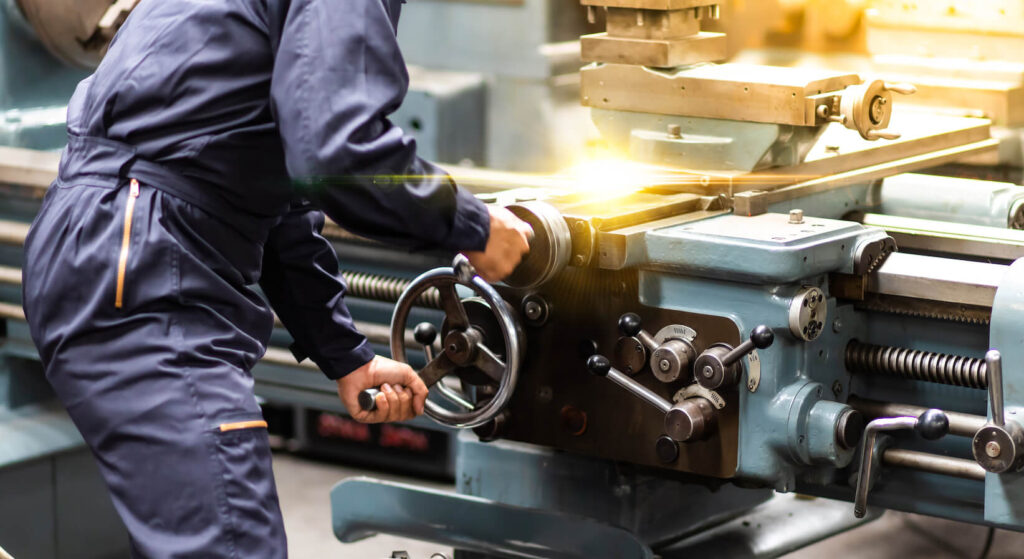
Was beinhaltet die EU-weite Maschinenrichtline 2006/42/EG?
Zur Eindämmung von Arbeitsunfällen mit Maschinen nimmt die Einhaltung von Bestimmungen und Normen der Maschinenrichtlinie 2006/42/EG einen wichtigen Stellenwert ein. Die Richtlinie ist seit Ende 2009 in Ländern der EU und in weiteren Ländern wie Schweiz, Liechtenstein, Türkei, Norwegen und Island verbindlich anzuwenden. Für Geräte und Behälter, die unter Druck stehen, gilt analog die Druckgeräterichtlinie 97/23/EG.
Was bedeutet die CE-Kennzeichnung?
An der CE-Kennzeichnung lässt sich erkennen, ob ein Produkt mit den maßgeblichen Bestimmungen der EU übereinstimmt. Das CE-Zeichen – CE steht für Communauté Européenne (EG/ EU) – entspricht damit nicht einem Gütesiegel, sondern lediglich einer Konformitätsbestätigung. Der Hersteller ist je nach Produktkategorie selbst für die Einhaltung aller geforderten Richtlinien und Normen, die die Maschinensicherheit und den Umweltschutz betreffen, verantwortlich. Er bestätigt die Konformität mit seiner Konformitätserklärung, die als Grundlage für die CE-Kennzeichnung dient. In bestimmten Fällen muss der Entwickler und Hersteller eines Produktes eine offizielle Konformitätsbewertungsstelle zur Bestätigung der Konformität hinzuziehen.
Die Risikobeurteilung – ein wichtiger Bestandteil der Maschinensicherheit
Mit Inkrafttreten der Maschinenrichtlinie 2006/42/EG wurde der Begriff „Gefahrenanalyse“ durch den Begriff „Risikobeurteilung“ ersetzt. Die Risikoanalyse betrifft sämtliche Lebensphasen einer Maschine von der Konzeption bis zur fachgerechten und umweltfreundlichen Entsorgung wie die Maschinenrichtlinie selbst.
Für Hersteller ist die Norm DIN EN ISO 12100:2010 (Sicherheit von Maschinen), die Leitfäden für Ablauf und Gestaltung der Risikobeurteilung aufstellt, rechtlich bindend. Sie ist durch geltende Gesetze vorgegeben. Da sich die Gefährdungsbeurteilung auf alle Lebensphasen einer Maschine bezieht, ist ihre Erstellung kein Einmalvorgang, sondern entspricht eher einem fortlaufenden Prozess. In den beispielsweise auch Erkenntnisse einfließen, die erst im Laufe der Betriebsphase gewonnen werden.
Ergebnisse der Risikoanalyse
Die Ergebnisse der Risikoanalyse fließen in das Safety-Konzept und in die Betriebsanleitung ein, sind aber nicht Teil des Lieferumfangs. In der Risikoanalyse könnten sich Betriebsgeheimnisse verbergen, die der Hersteller nicht öffentlich zugänglich machen möchte. Auf Verlangen muss der Hersteller die Risikobeurteilung den zuständigen Behörden vorlegen.
Die Risikobeurteilung nach DIN EN ISO 12100:2010 folgt einem festgelegten Schema
Die Risikobeurteilung ist ein schrittweiser, also iterativer Prozess, der bereits während der Konstruktionsphase beginnt. Grundsätzlich ist der Entwickler und Hersteller einer Maschine für die Risikobeurteilung verantwortlich, allerdings können Institutionen wie der Technische Überwachungsverein (TÜV Maschinensicherheit) und DEKRA, die für derartige Aufgaben zertifiziert sind, den Prozess der Risikobeurteilung teilweise oder gänzlich übernehmen.
Ein identifiziertes Einzelrisiko wird analysiert und bei Bedarf zur Risikominderung eine konstruktive Änderung entwickelt, die wiederum eine erneute Risikoanalyse nach sich zieht. Die Analyse eines Einzelrisikos erfolgt in den drei Einzelschritten; Festlegung der Grenzen der Maschine, Identifizierung der Gefährdungen und Risikoeinschätzung.
Die drei Schritte der Risikoanalyse
Im ersten Schritt der Risikoanalyse werden die relevanten Eckdaten der Maschine im Ruhezustand, beispielsweise Gewicht, äußere Abmessungen, elektrische Anschlüsse, Betriebsstoffe und dergleichen ermittelt und festgeschrieben.
Anschließend werden die maximal erreichbaren Betriebsdaten wie Temperaturen, Emissionen von Lärm, Abgasen und eventuellen Strahlungen ermittelt sowie Schwingungen, Bewegungen und viele weitere Parameter. Die ermittelten Grenzwerte bilden die Grundlage zur Identifizierung möglicher Gefahren.
Die identifizierten Gefahren werden einer Risikoeinschätzung unterzogen, um zu erkennen, ob eine konstruktive Änderung die Gefahr mindern kann. Falls keine konstruktive Lösung des Problems möglich ist, weil dadurch die Funktionalität der Maschine leiden würde, bleibt die Möglichkeit, die Gefahrenquelle abzuschirmen, so dass sich niemand verletzen kann. Alle Einzelmaßnahmen werden anschließen auf ihre Wirksamkeit überprüft und neu analysiert.
Melden Sie sich jetzt an, um Zugang zu den neuesten Marktinformationen zu erhalten und die Effizienz Ihrer Asset Operations zu verbessern.
Das dreistufige Safety-Konzept setzt auf funktionale Sicherheit
1. Stufe
Das vorrangige Ziel der Risikoanalyse besteht darin, eine erkannte Gefahr durch konstruktive Änderungen so zu minimieren, dass eine funktionale Sicherheit der Maschine erreicht wird, die keine weiteren Sicherheitsmaßnahmen erforderlich macht und mögliche Bedienungsfehler durch Unachtsamkeit toleriert, ohne dass die Gefahr von Verletzungen besteht. Die konstruktive Verbesserung entspricht der ersten Stufe des dreistufigen Safety-Konzepts, das mit der DIN EN ISO 12100:2010 kompatibel ist.
2. Stufe
Die zweite Stufe des Safety-Konzepts greift, sofern die Herstellung der funktionalen Sicherheit dem eigentlichen Zweck der Maschine entgegenlaufen würde. In diesen Fällen besteht der Ausweg meist darin, die festgestellte Gefahrenquelle an der Maschine abzuschirmen, damit keine Verletzungen entstehen können. Beispiele bieten Handkreissägen, spanabhebende Werkzeuge und viele weitere Werkzeuge, deren gefährliche Sägeblätter, Fräsen oder Bohrer so abgeschirmt sind, dass bei sachgemäßer Handhabung keine Verletzung entstehen kann.
Schließen Sie sich 700+ Unternehmen an, die mit ToolSense arbeiten
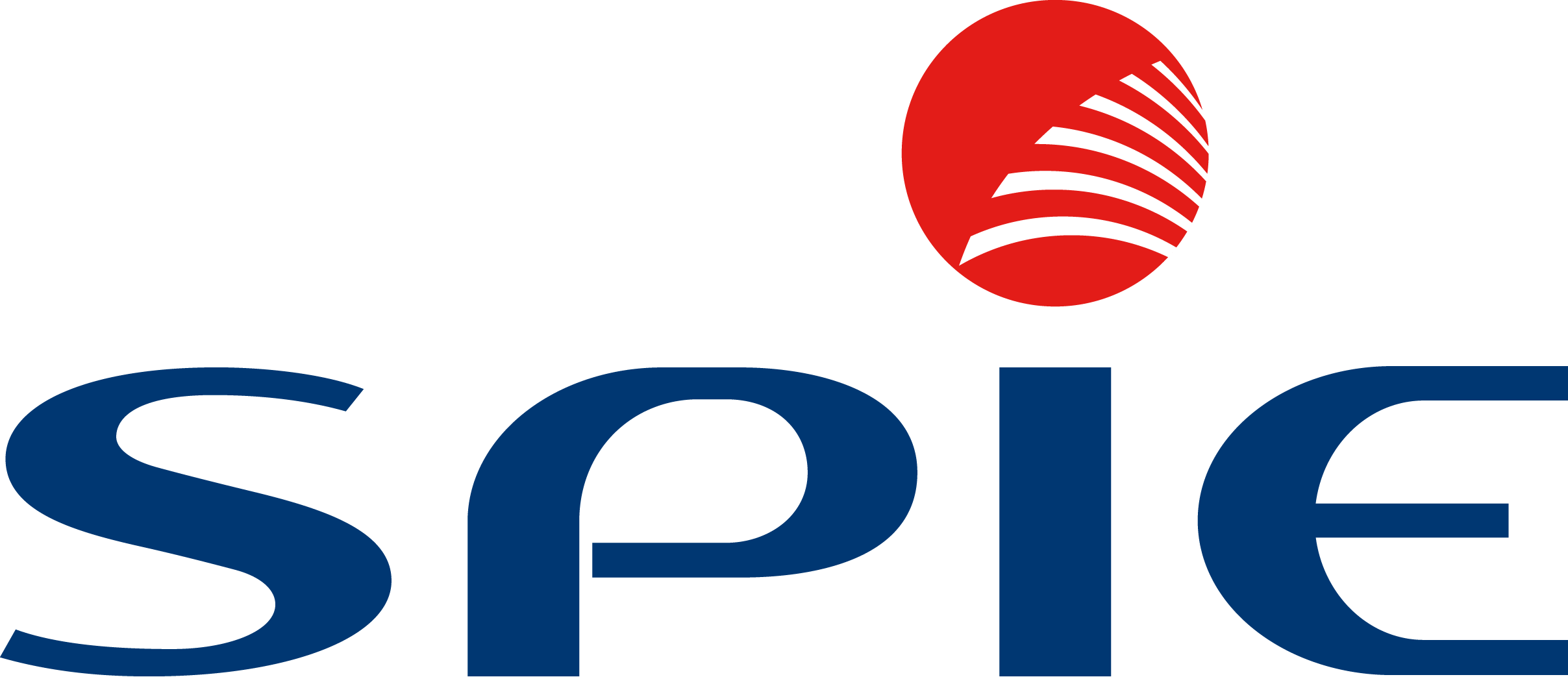
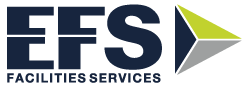
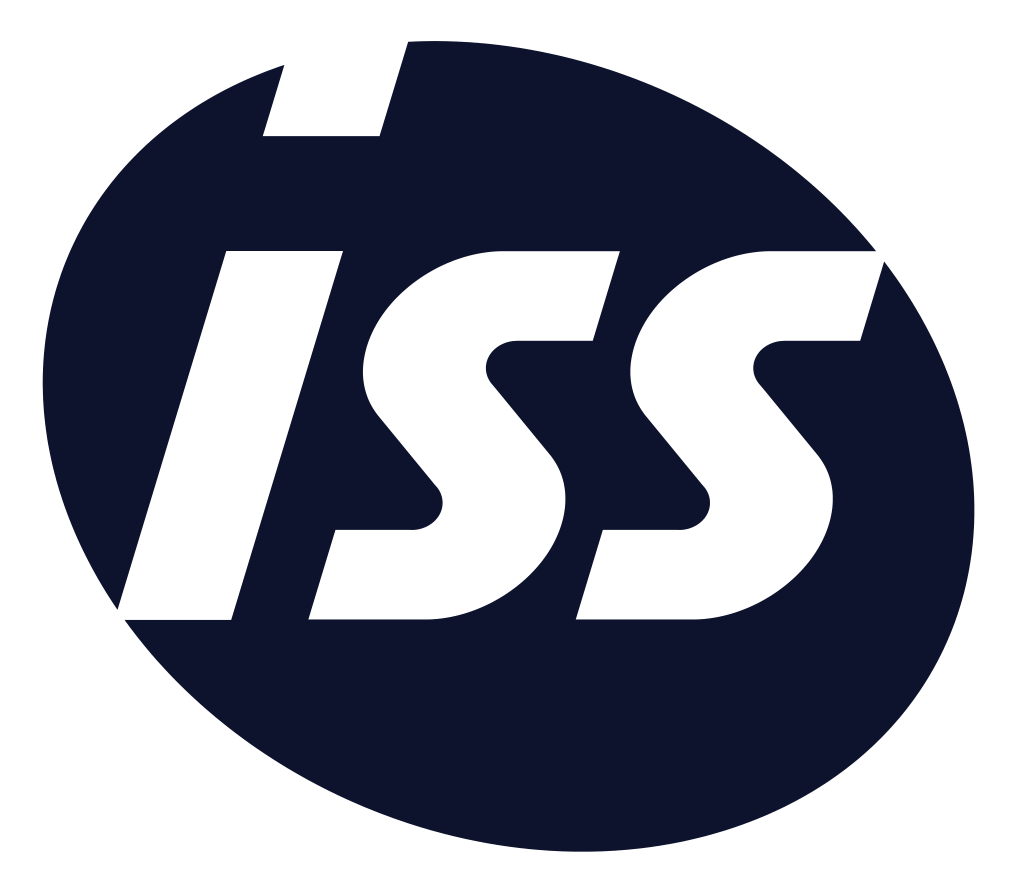
3. Stufe
Die dritte Stufe des Safety-Konzepts entspricht einer Verlegenheitslösung. Diese kommt immer dann zur Anwendung, wenn der Konstrukteur keine Möglichkeit zur Herstellung der funktionalen Sicherheit sieht und auch die Abschirmung der Gefahrenquelle nicht möglich ist. Jetzt bleibt nur noch die Warnung vor der Gefahr als dritte Stufe des Safety-Konzepts.
Fazit
Die Maschinensicherheit gemäß DIN EN ISO 12100:2010 ist eine EU-weit einheitliche Richtlinie zur Eindämmung potenzieller Gefahren, die von Maschinen für Menschen und Umwelt ausgehen können. Das oberste Ziel besteht darin, für die Maschine in einem iterativen Prozess durch konstruktive Maßnahmen eine funktionale Sicherheit zu erreichen, die ein erkennbares Gefährdungspotenzial ausschließt. Das entspricht der ersten und vorrangigen Stufe des Safety-Konzepts.
Falls das vorrangige Ziel nicht erreicht werden kann, ohne dass die Maschine nicht mehr ihren Zweck erfüllen kann, erfordert die Maschinenrichtlinie eine Abdeckung der „gefährlichen“ Stelle einer Maschine wie rotierende Messer oder ähnliches, um Verletzungen vorzubeugen. Abdeckungen entsprechen der zweiten Stufe des Safety-Konzepts. Sofern auch Abdeckungen aus operativen Gründen nicht möglich sind, bleibt die dritte Stufe in Form von Warnhinweisen oder Absperrungen, um Gefährdungen zu vermeiden.
Wie ToolSense helfen kann
Maschinensicherheit stellt einen unverzichtbaren Teil des Maschinenmanagements dar. Mit der Softwarelösung von ToolSense können Maschinen unterschiedlicher Hersteller in einer zentralen Oberfläche verwaltet werden. Zudem können alle Betriebsmittel mit QR Codes überwacht, Maschinen-Prozesse digitalisiert und Service-Prozesse transparent und effizient gesteuert werden. Mit ToolSense können Sie die Maschinensicherheit effizienter überwachen, dokumentieren und Maßnahmen schneller ergreifen.
FAQ
Die Maschinensicherheit dient dazu, eine Maschine so zu konstruieren, dass von ihr möglichst keine Verletzungsgefahr und keine Gefährdung der Gesundheit weder während des regulären Betriebs noch im abgeschalteten Zustand ausgeht. Auch mögliche Bedienungsfehler durch Unachtsamkeit sollten folgenlos bleiben.
Für die Sicherheit der Maschine sind Hersteller, Händler und Betreiber verantwortlich.
Miteinander verbundene Teile oder Vorrichtungen, von denen mindestens ein Teil beweglich ist, werden als Maschine gemäß der gültigen Maschinenrichtline 2006/42/EG als Maschine definiert. Neu gegenüber veralteten Versionen der Maschinenrichtlinie ist, dass für die verbundenen Teile kein Antriebssystem mittels Energiequelle – kann auch Handkraft sein – vorhanden sein muss, um als Maschine definiert zu werden.
Konstruktive Sicherheitseinrichtungen an Maschinen sollen die funktionale Sicherheit der Maschine bei sachgemäßer Handhabung garantieren. Die funktionale Sicherheit muss auch bei möglichen Fehlbedienungen durch Unachtsamkeit abdecken, nicht aber absichtliche oder grob fahrlässige Fehlbedienungen. Falls die funktionale Sicherheit nicht hergestellt werden kann, muss die Gefahrenstelle der Maschine abgedeckt werden, so dass keine Gefährdungen mehr bestehen.