Winter Services
Simplify Snow Clearing Operations with ToolSense
In the winter services industry, efficiency, accountability, and equipment reliability are critical to meeting client expectations. Without robust tracking and maintenance solutions, companies often face operational and reputational challenges.
Are these your challenges?
- Clients complain about incomplete snow removal, even when the work was done, because there’s no proof of service.
- Lack of visibility into whether teams visited the site, how long they stayed, and whether they performed the required work.
- Equipment breakdowns during peak winter months caused by missed maintenance in the off-season.
How ToolSense can transform your operations
- Proof of service documentation: Track and log each vehicle’s location, time spent on-site, and work performed. Share proof with clients to build trust and accountability.
- Real-time fleet monitoring: Gain full visibility into your fleet’s status, fuel levels, and performance metrics in one centralized system.
- Automated maintenance scheduling: Prevent costly breakdowns by creating proactive servicing schedules for snowplows, snow blowers, and other vehicles.
- Digitize paper forms and workflows: Digitize any kind of paper-based forms such as maintenance checklists, handover forms, or inspections with the ToolSense Procedure builder.
- Keep track of all inventory and spare parts: Digitize your warehouse management and keep track of all parts, consumables and inventory you have on stock.
- Streamlined task management: Assign tasks to teams in real-time and monitor their progress to ensure work is completed efficiently.
Processes before and after using ToolSense
Teams relied on manual reports and verbal confirmations to assure clients of completed work. Maintenance was reactive, leading to unexpected breakdowns that disrupted schedules.
Using real-time tracking and automated reports, companies now provide transparent proof of service. Maintenance schedules are automated, ensuring all vehicles are in peak condition before winter begins.
Improved business impact
- Client trust: Transparent proof of service improved client satisfaction and retention rates by 15%.
- Cost savings: Reduced emergency repairs and downtime, saving 20% on maintenance costs.
- Customer success story: A regional winter services provider used ToolSense to streamline operations, improve customer trust, and reduce equipment failures during peak season.
Ready to ditch Excel and Paper?
Join 700+ Operations, Maintenance & Repair Teams Simplifying Their Daily Business With ToolSense
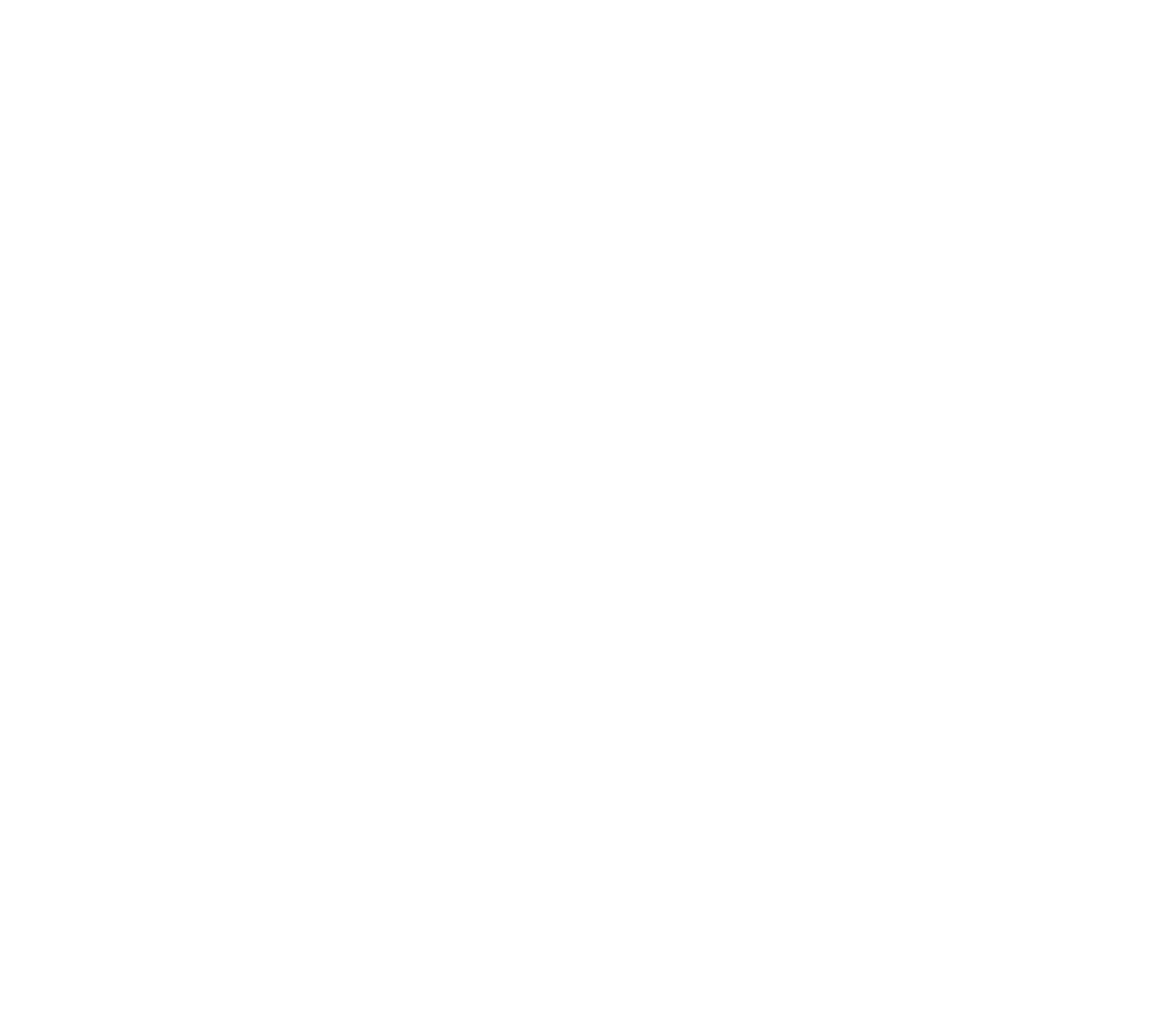
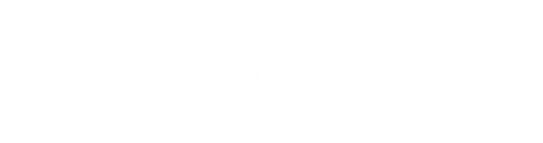
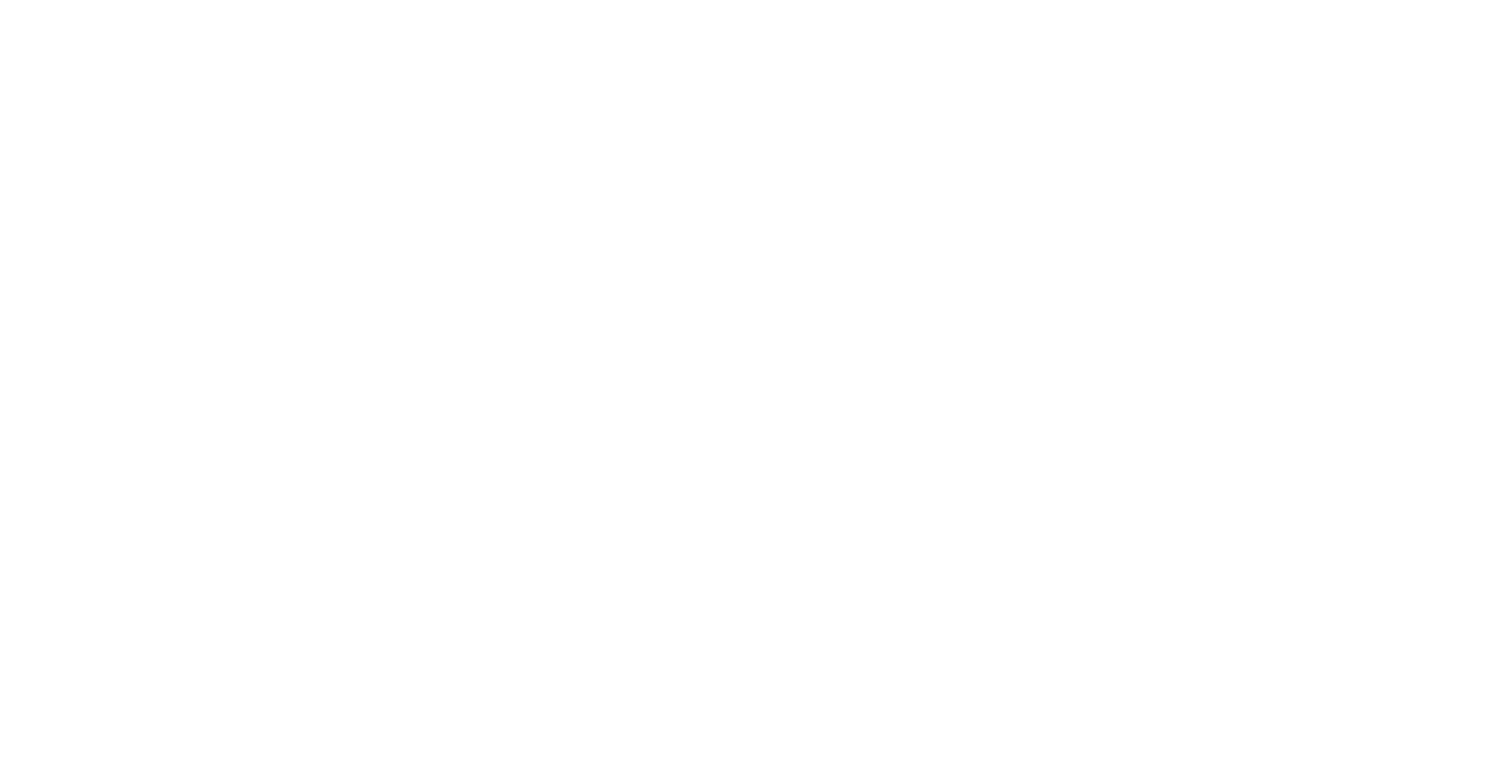
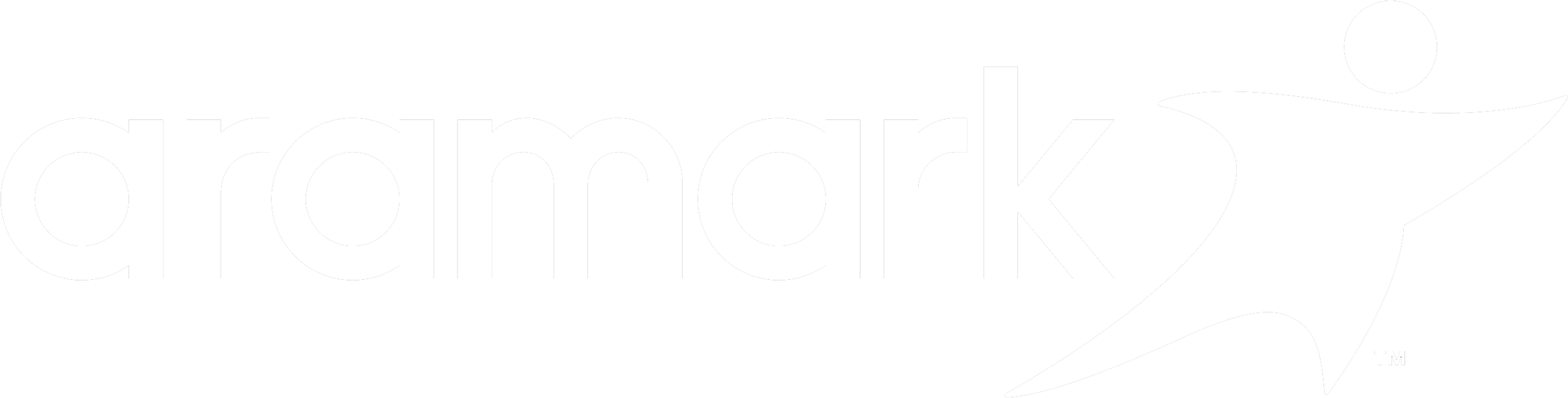
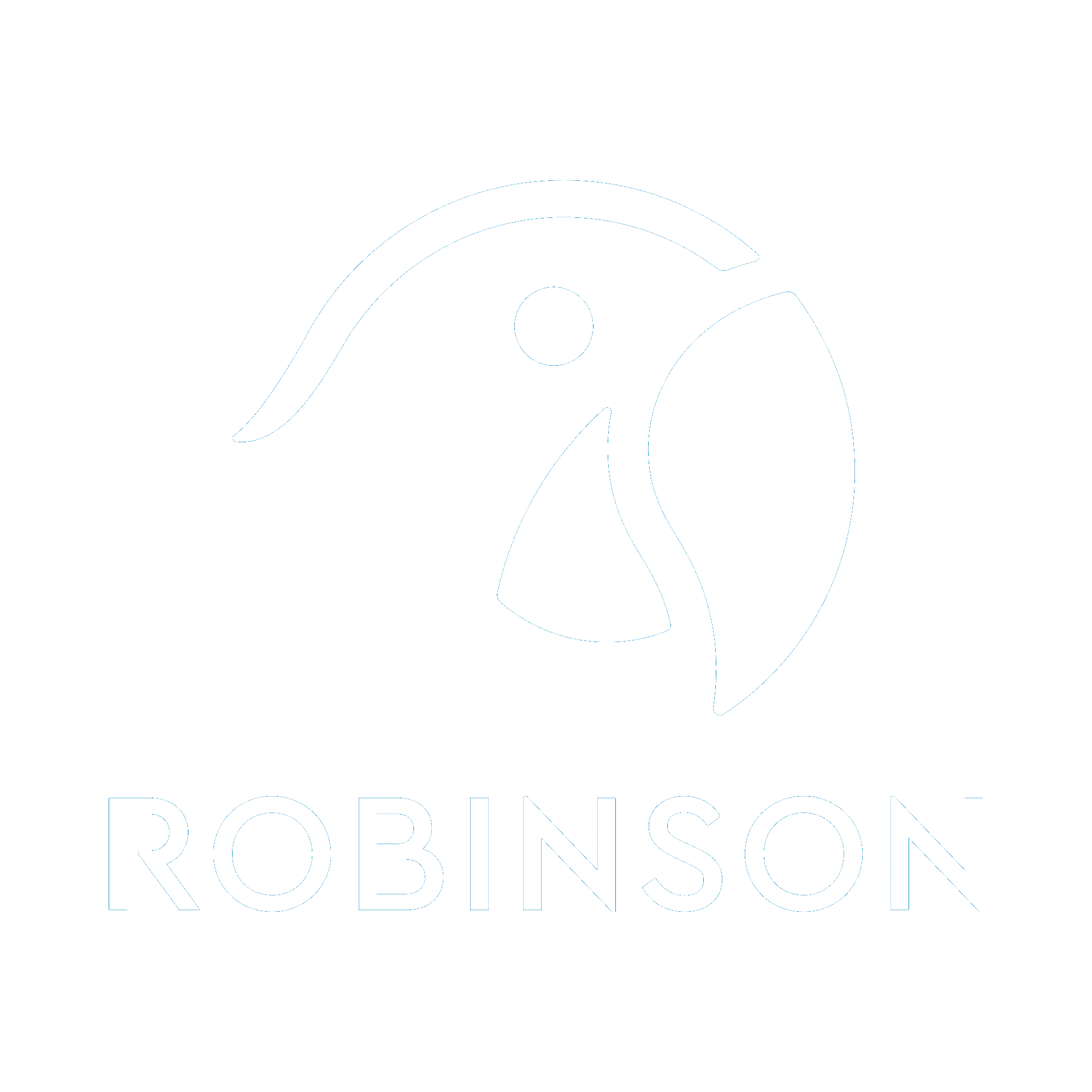
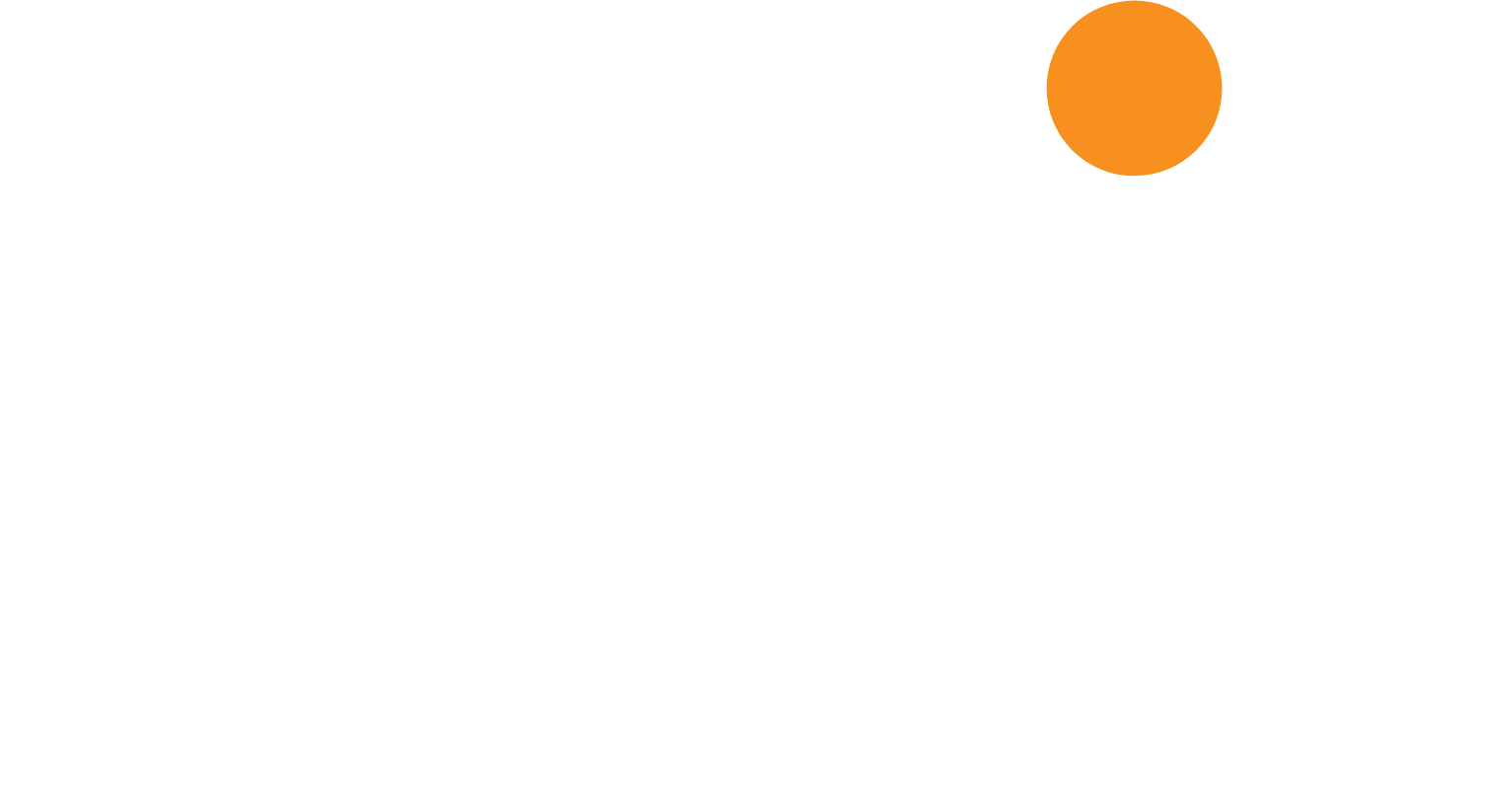
Verified review
5/5
We wanted a solution that does not only track expensive assets but also cheap ones. In Austria, ISS operates over 6,500 cleaning machines alone, without even counting vacuum cleaners and other pieces of equipment. With ToolSense we bring them together on a single platform, leveraging data from IoT hardware and improving maintenance and inspection processes.
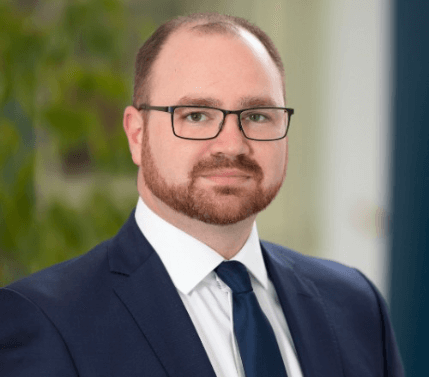
David Hiersche
Director Operations Performance @ ISS Austria
Verified review
5/5
With ToolSense we no longer have duplicated data stored in Excel sheets but a central and synchronized system that contains all relevant information and documentation. We save a lot of time and therefore I have an immediate positive economic impact. In addition to that we wanted to stay in charge of our own data which required a manufacturer-independent solution.
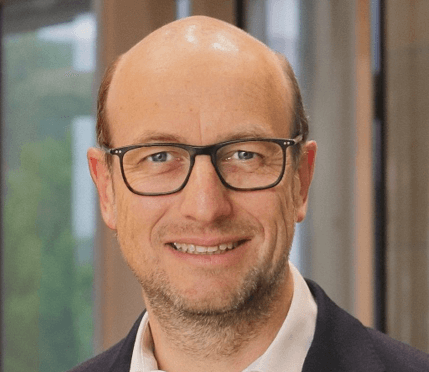
Ralf Lüddemann
Head of Machine Technology @ Leonhard Weiss
Verified review
5/5
Being able to combine equipment on one dashboard, where we have motorized and non-motorized equipment, is key for ABM. We currently have 5,000–6,000 non-motorized pieces of equipment out there in the field. Bringing that all together into one system is a big benefit.
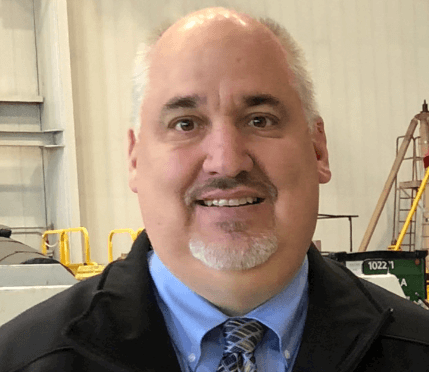
Michael Ostendorf
Senior Vice President Service Delivery @ ABM Industries
Verified review
5/5
We finally have a single digital platform, that makes a lot of manual processes obsolete. Our goal is to retain merchants and clients with great digital services that save them time and money. Additionally, we build up a unique set of first-party data that help us to improve our products and services even more.
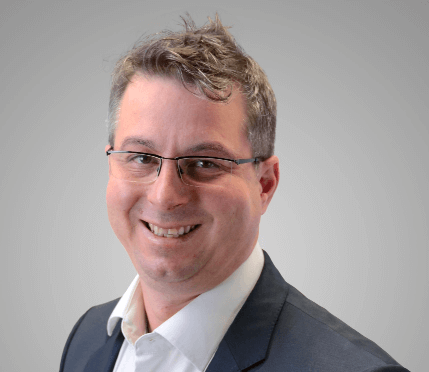
Benedikt Schneider
Head of Product Management @ Knauf PFT