Efficient Asset Lifecycle Processes Make Your Site Manager’s Life Easier
There are numerous processes that happen during an asset’s lifecycle like requesting new machines, moving locations and more. Managing all of them in a single platform dramatically improves your operations’ efficiency.
If the video embed isn’t working as expected, please find the full video here.
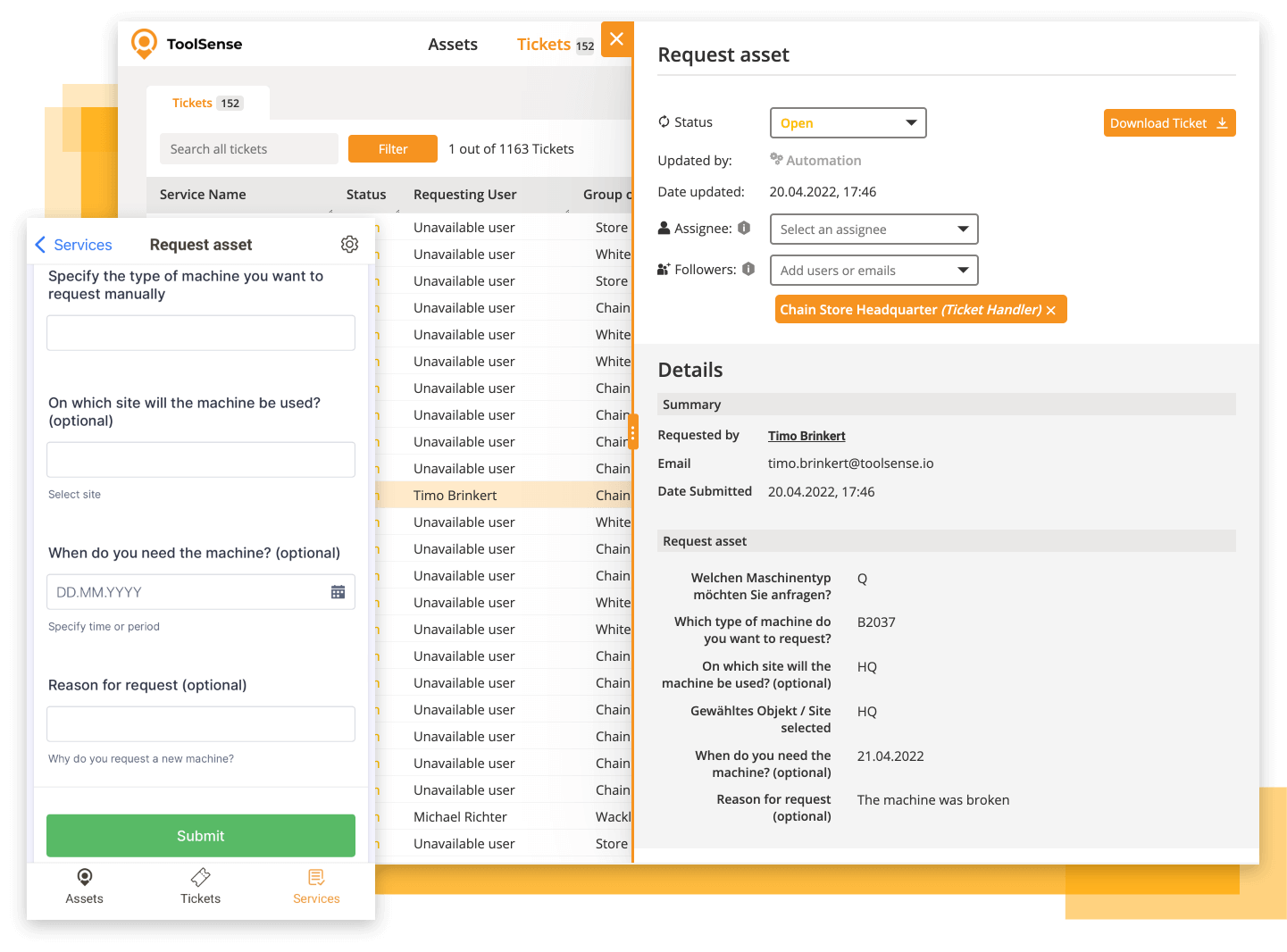
Trigger processes directly from the ToolSense mobile or web app
Get rid of printed forms and complicated process descriptions for tasks like asset lifecycle management requests. Simply use the ToolSense mobile or web app with it’s integrated service workflows to submit your request. We automatically create a corresponding ticket and notify the responsible person.
Check the availability with powerful filters
Stop assets from being bought or leased unnecessarily, and just check if something is available in the warehouse. Empower procurement to maximize the productivity of all assets in your operation with powerful filters in your dashboard.
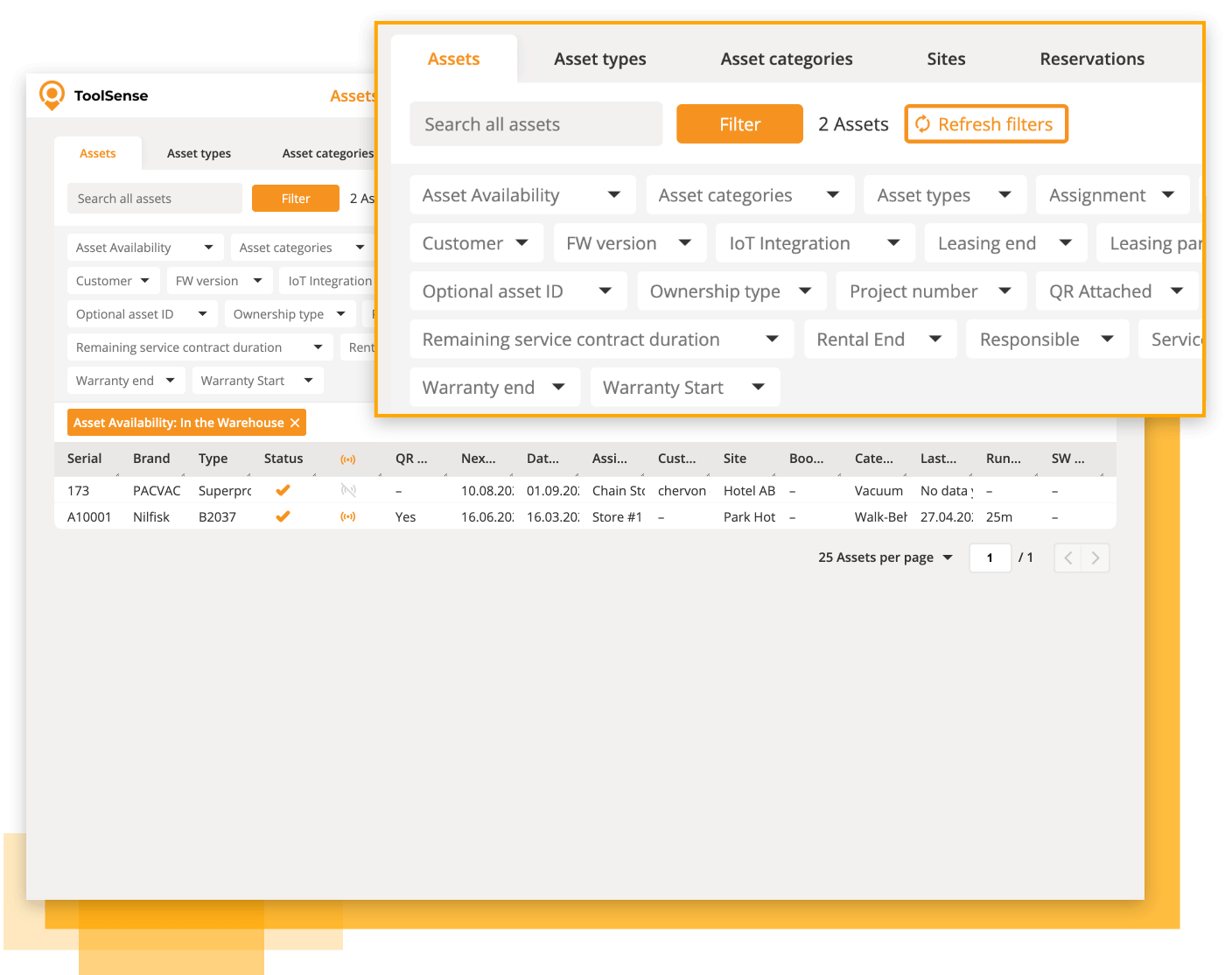
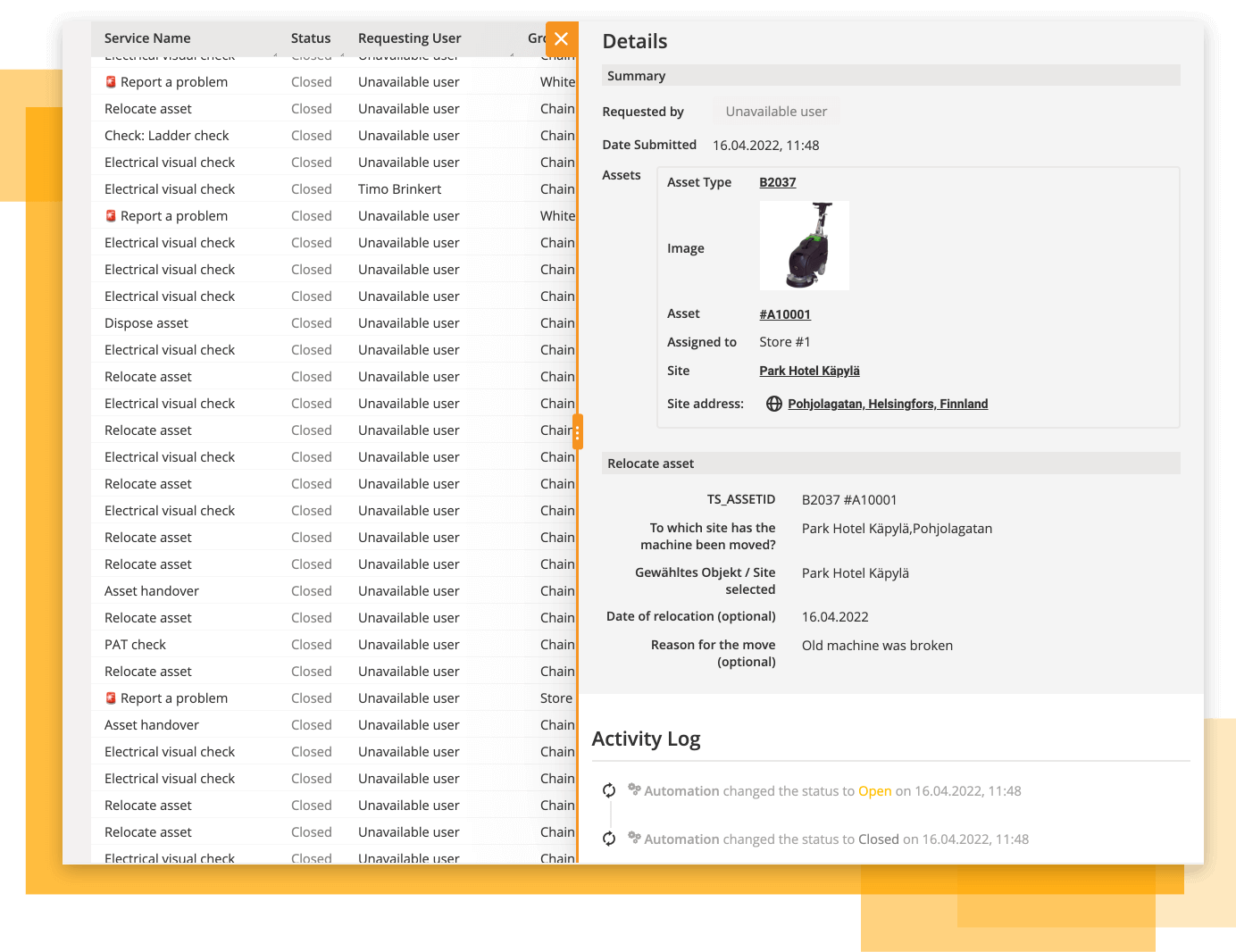
Your asset's new single source of truth is here
With multiple Excel spreadsheets, communication via mail or WhatsApp and even printed forms, one easily looses track of an asset’s history. Asset management software like ToolSense enables you to track everything that changed its status. In addition, communication between everyone involved is efficiently organized.
Alexander Manafi (CEO) gives you a private tour
Our CEO, Alexander Manafi, gives you a quick private tour. See the actual product and how it is used to improve your asset operations. If the video embed isn’t working as expected, please find the full video here.
Ready to ditch Excel and Paper?
Join 700+ Operations, Maintenance & Repair Teams Simplifying Their Daily Business With ToolSense
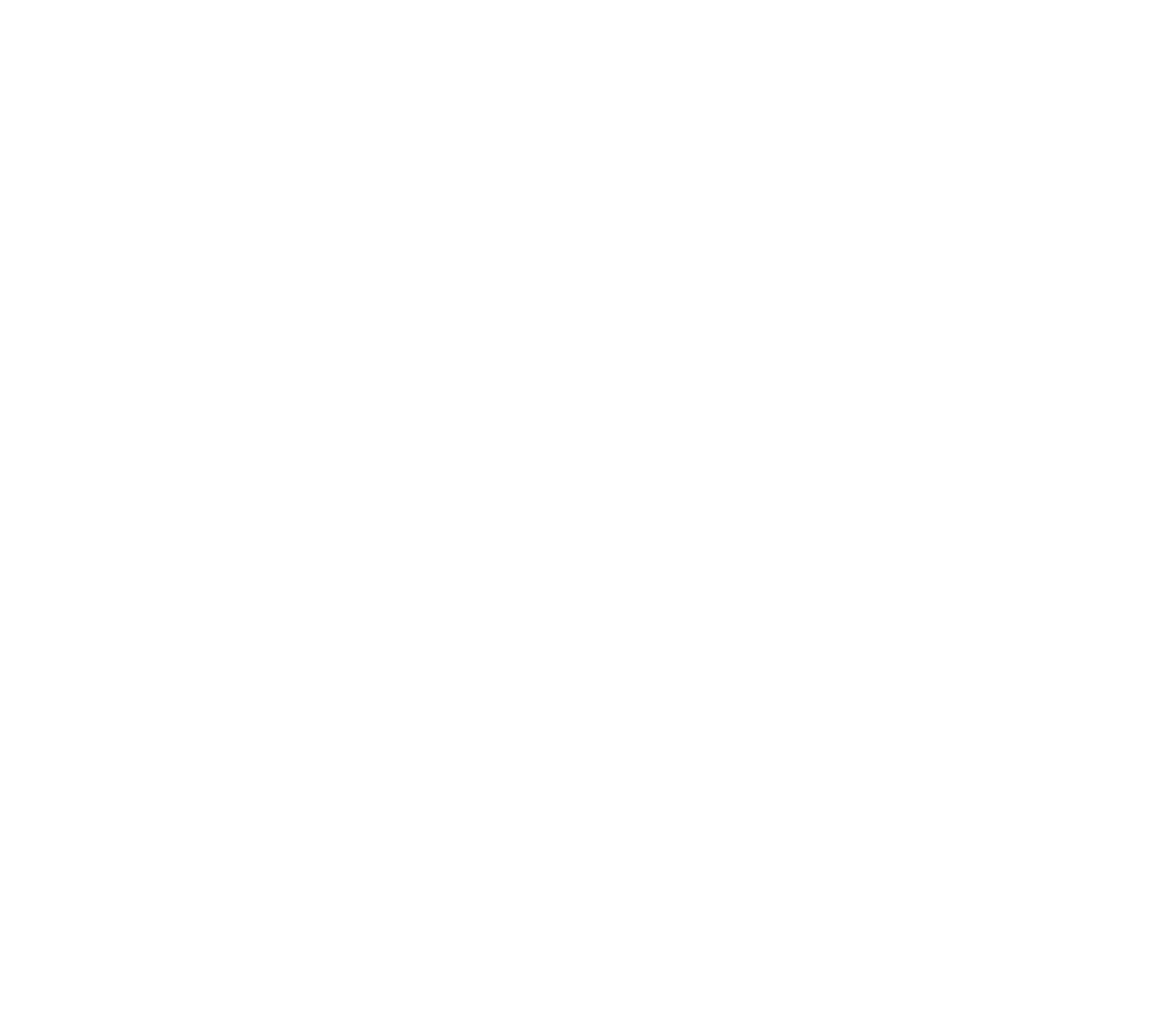
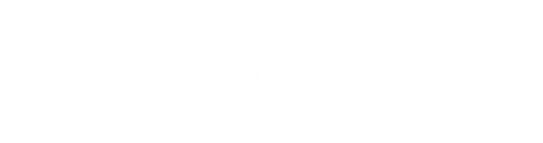
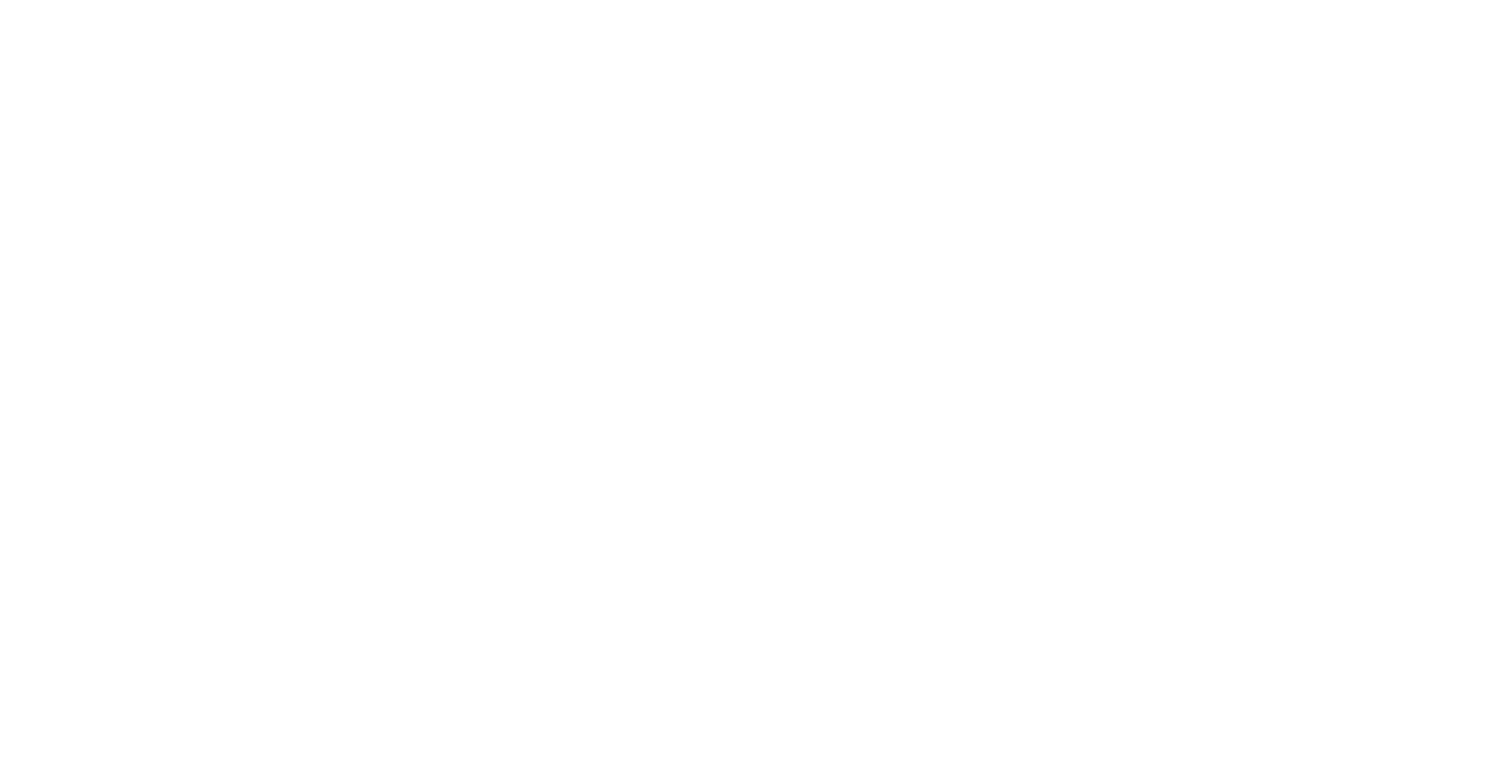
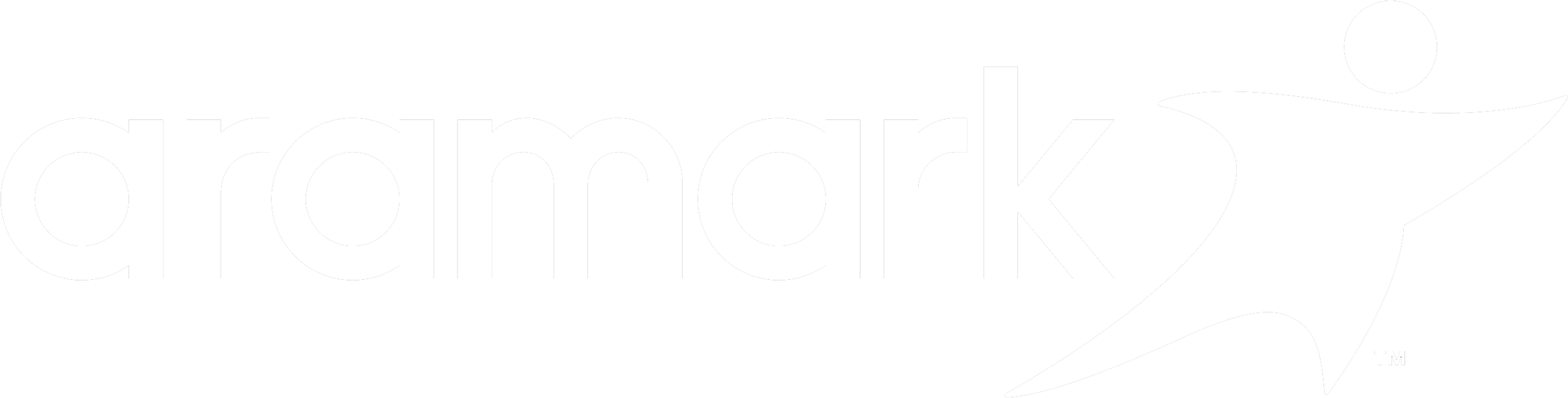
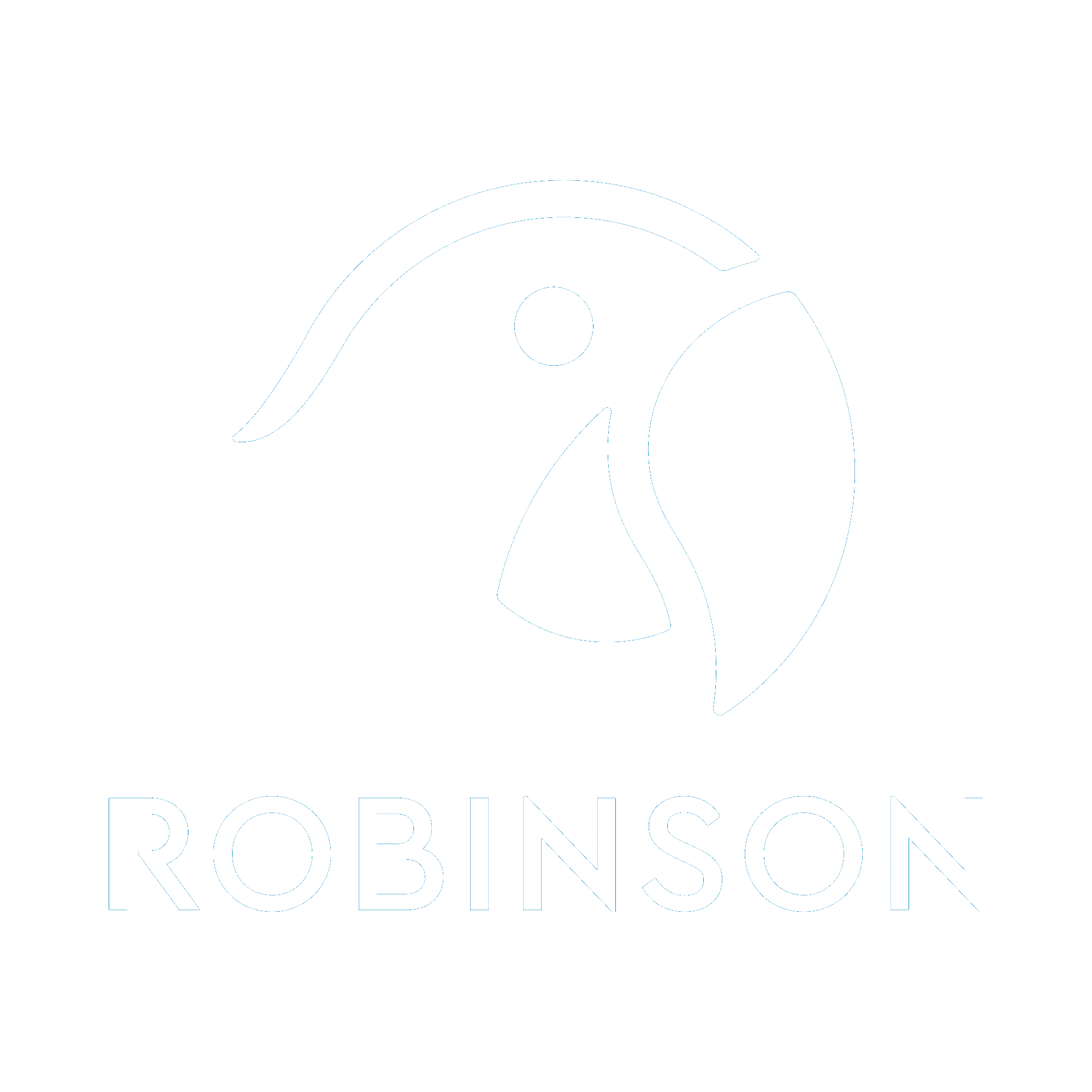
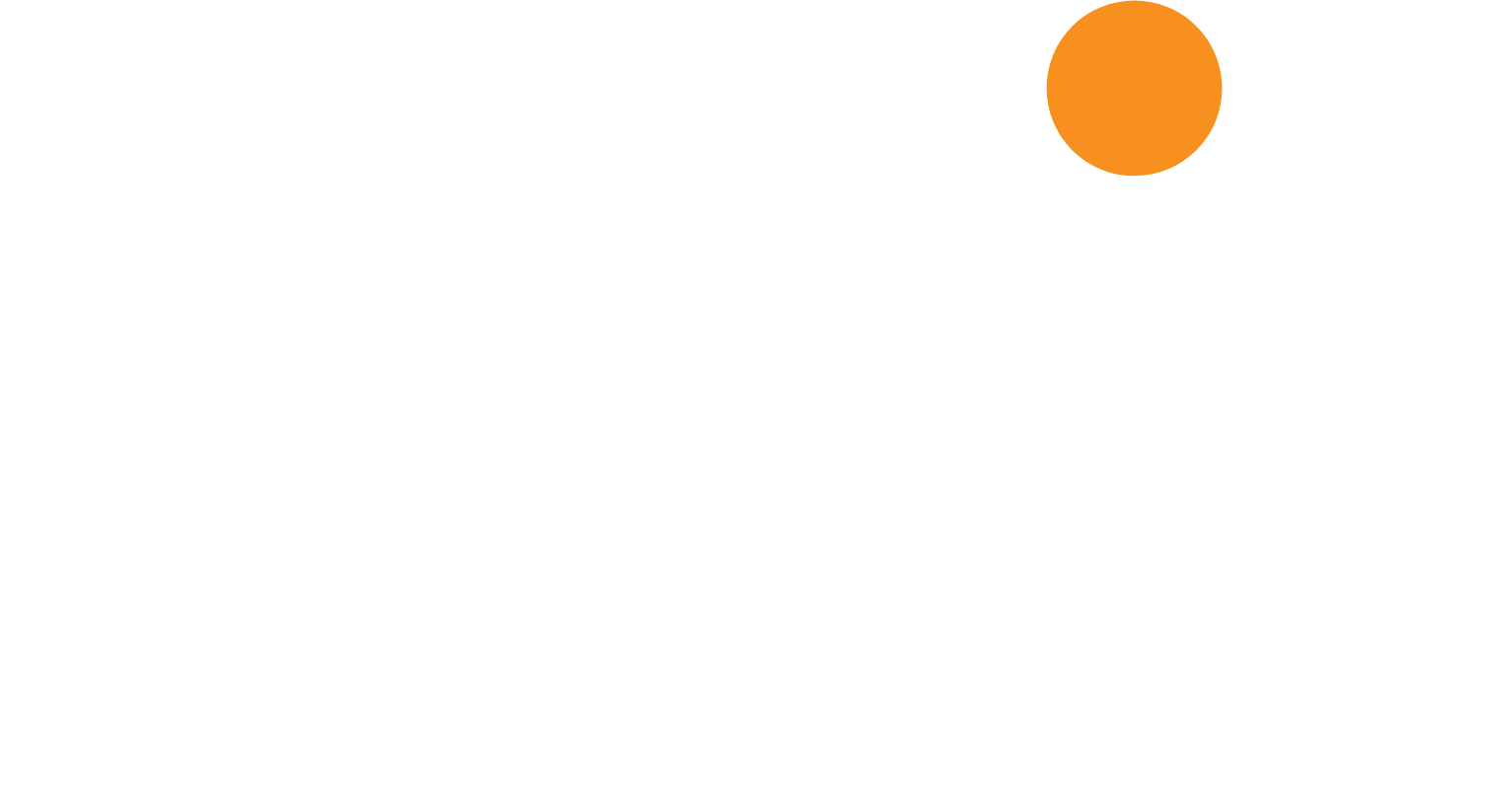
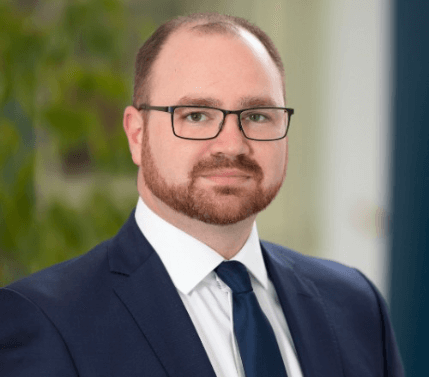
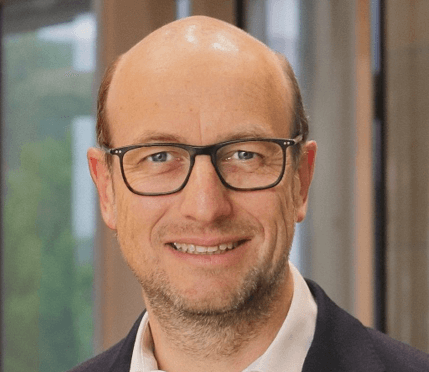
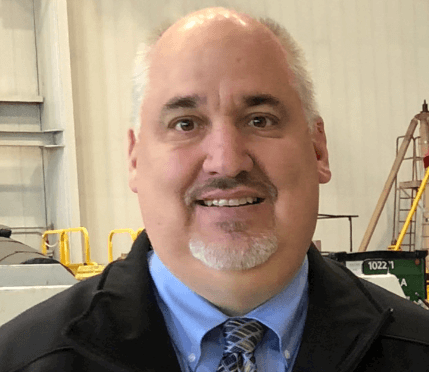
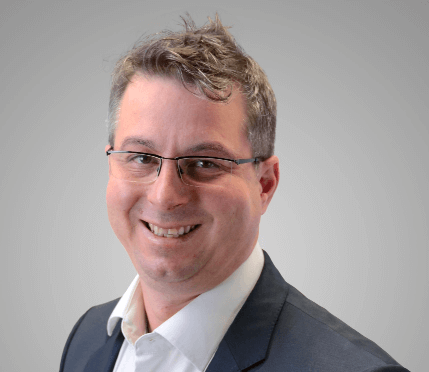