From Chaos to Control: Unleash the Full Potential of Parts Inventory Management Software
How often have you faced the challenge of managing parts inventory and wished for a simpler solution? Picture a system that not only streamlines your parts inventory management but also transforms it into an efficient, almost effortless process. With ToolSense, businesses can monitor which parts are utilized in specific work orders, optimize reorders, and maintain a comprehensive audit trail for all parts and inventory.
Key Features of Parts Inventory Management Software: Revolutionize Your Asset Control With ToolSense
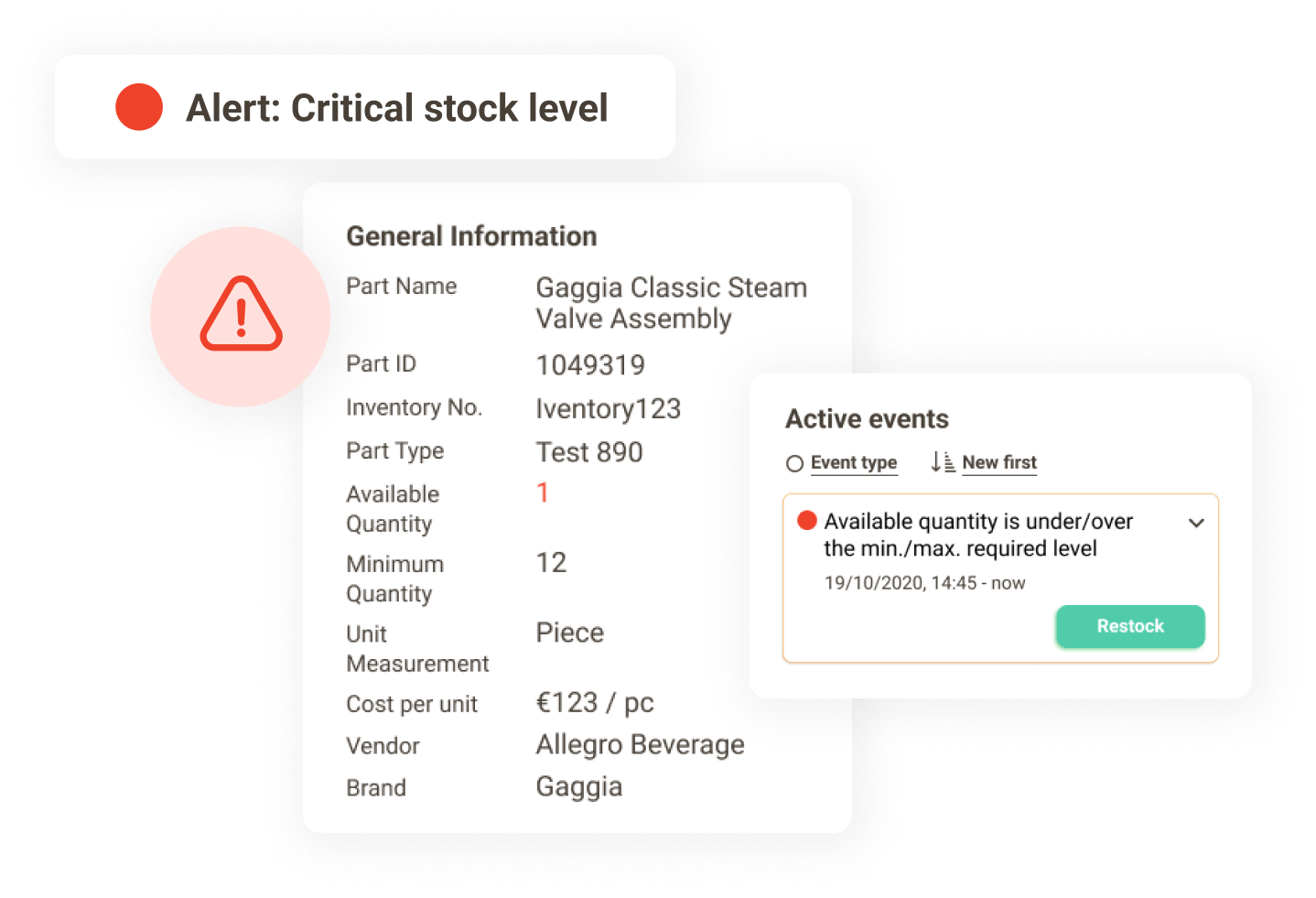
Low Inventory Alerts
Low inventory alerts play a crucial role in proficient parts management, as they monitor the quantity of each part in stock and generate alerts when the quantity drops below a predetermined minimum quantity threshold. The ToolSense inventory control system ensures that businesses stay abreast of low stock levels, allowing them to take necessary steps such as reordering or adjusting production schedules to prevent stock outs and disruptions in asset operations. Setting up low inventory alerts in ToolSense is as simple as it gets!
Full Inventory Insights and Reporting
Exhaustive inventory reporting is integral for improving equipment uptime, supply chain management, effective asset tracking and ordering, and forecasting and planning. A full inventory report typically includes inventory counts, stock levels, fastest-selling products, category performance, inventory status, and performance. ToolSense’s comprehensive inventory reporting feature provides comprehensive reporting and analytics for spare parts inventory, enabling real-time tracking and monitoring of stock levels and usage patterns.
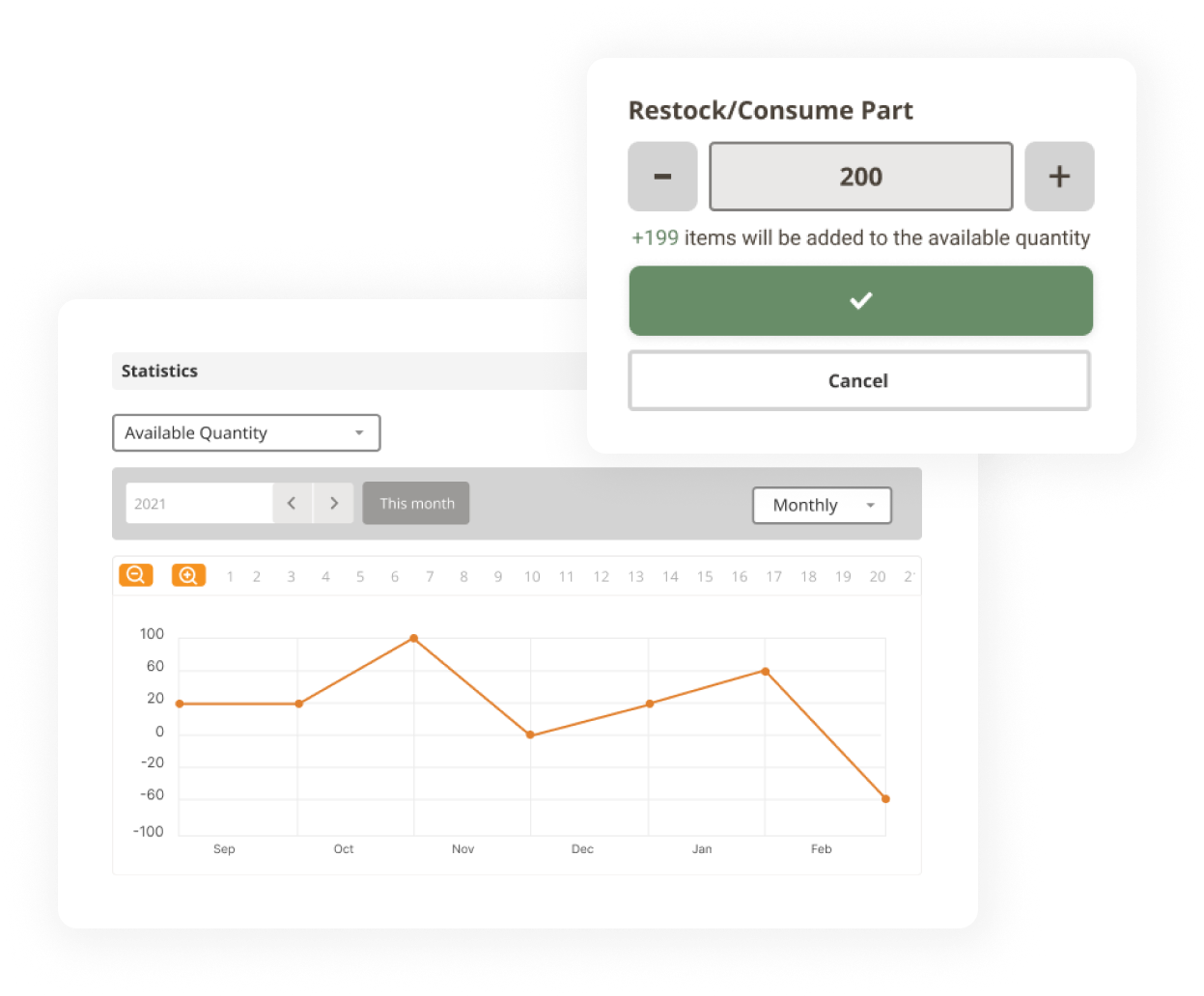
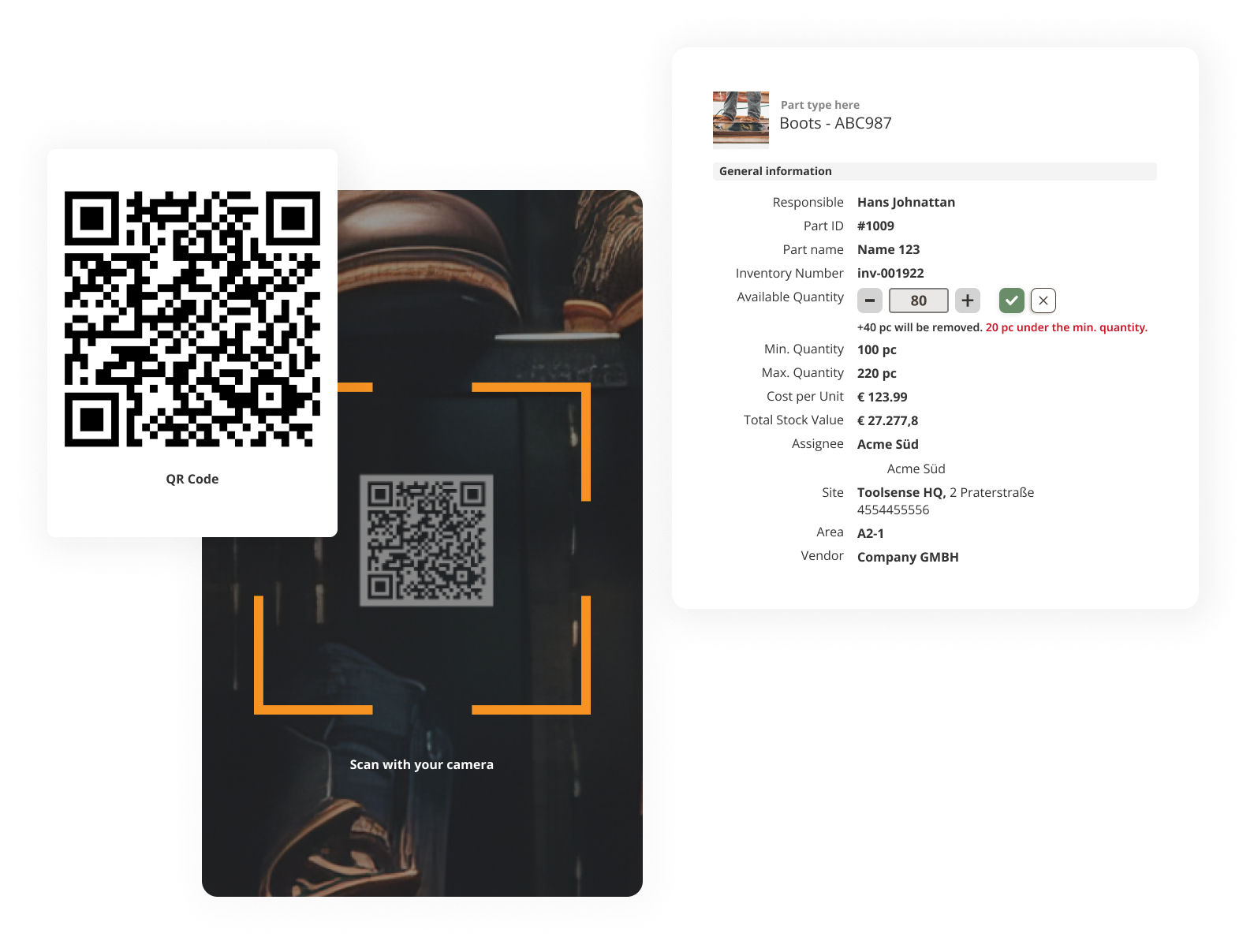
Streamlined Inventory With QR Code Integration
ToolSense leverages QR codes in their parts inventory software to effectively track and manage inventory. Each part is assigned a unique QR code, which can be scanned using a mobile device. This allows managers and frontline staff to promptly and accurately identify and locate specific parts within their inventory, enable real-time updates and notifications, ensure inventory levels are constantly up-to-date as well as minimize the risk of stock outs or overstocking. Additionally, QR codes enable accurate tracking of items and assets in multiple locations, regardless of their specific location.
Transparent Asset and Parts Tracking
When employed for inventory and asset tracking, ToolSense’s IoT hardware provides real-time data on elements like location, runtime, battery voltage, among other aspects. This cutting-edge technology provides a solution for managing assets effectively, as it allows businesses to have comprehensive visibility and control over their inventory. ToolSense IoT hardware is capable of tracking a variety of assets, including tools and equipment, vehicles, machinery, and parts inventory items. By providing accurate and dependable data for effective inventory management, we empower your business to optimize operations and stay ahead of the competition.
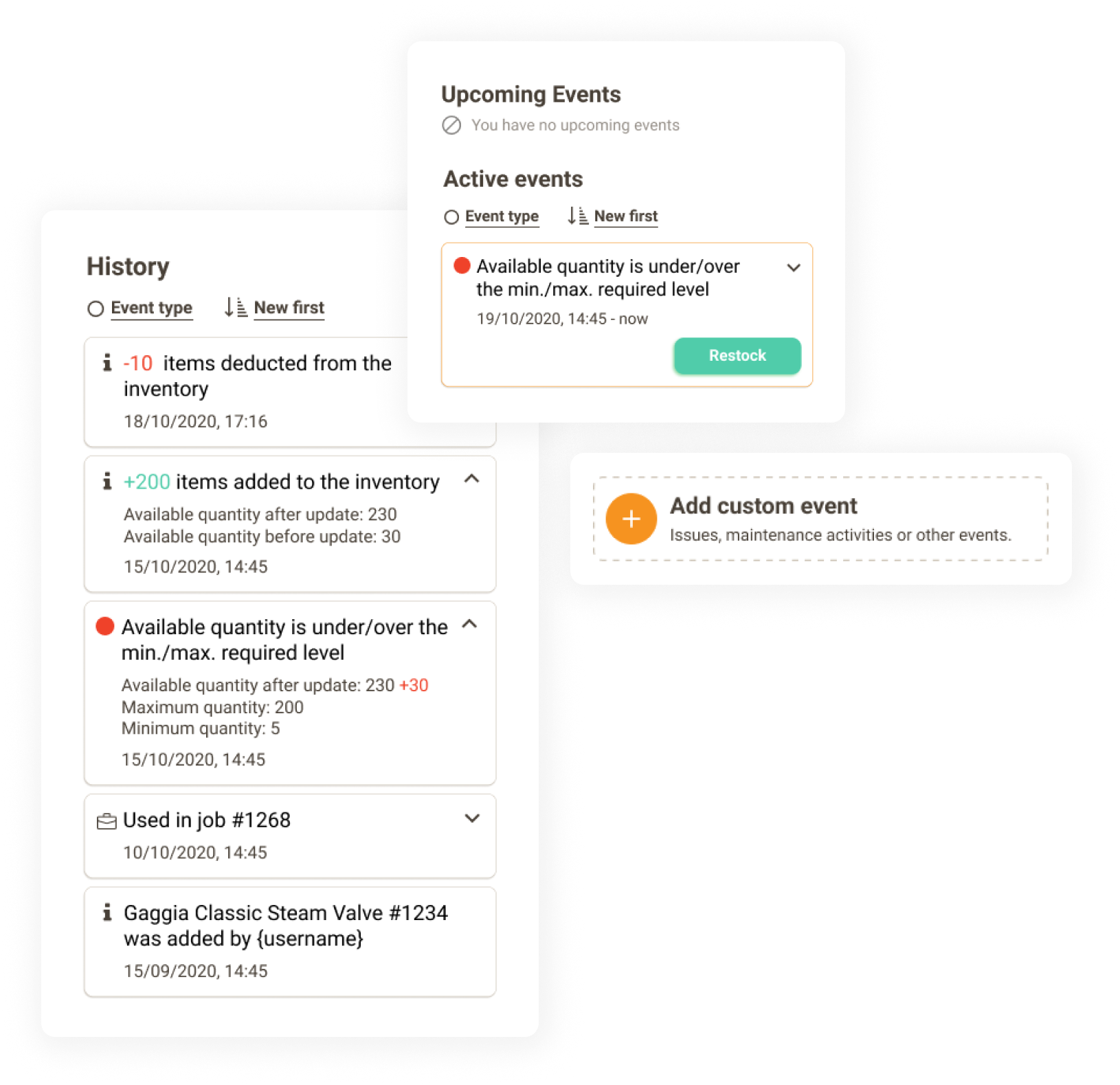
Alexander Manafi (CEO) gives you a private tour
Our CEO, Alexander Manafi, gives you a quick private tour. See the actual product and how it is used to improve your parts and inventory management operations. If the video embed isn’t working as expected, please find the full video here.
Proven Track Record
Reduction in time of operational staff spent managing assets, handling inspections and locating asset information
Reduction of annual asset costs (buying, repair & parts)
Example: For FM company with 3K employees this results in €150K asset cost reduction / year
Reduction of unplanned downtime
Example: For FM company with 3K employees this results in €200K cleaner personnel cost reduction / year
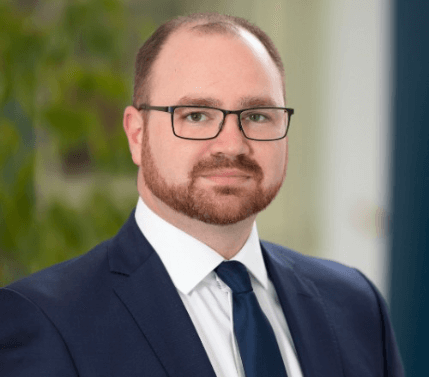
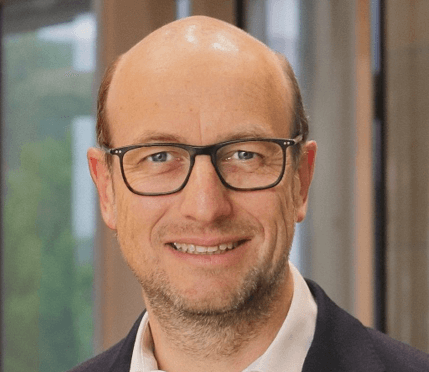
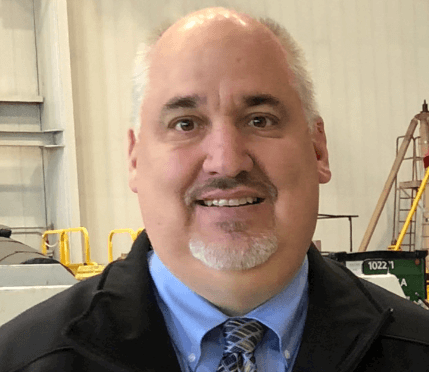
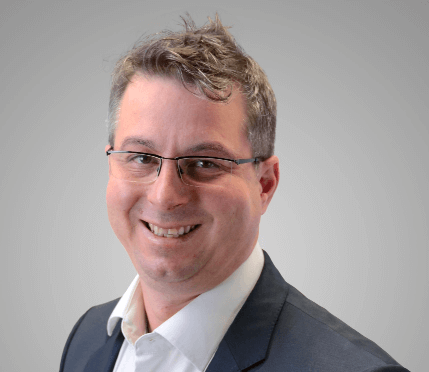
Start your digital transformation now
Join Hundreds of Asset-Intensive Companies Operating on ToolSense
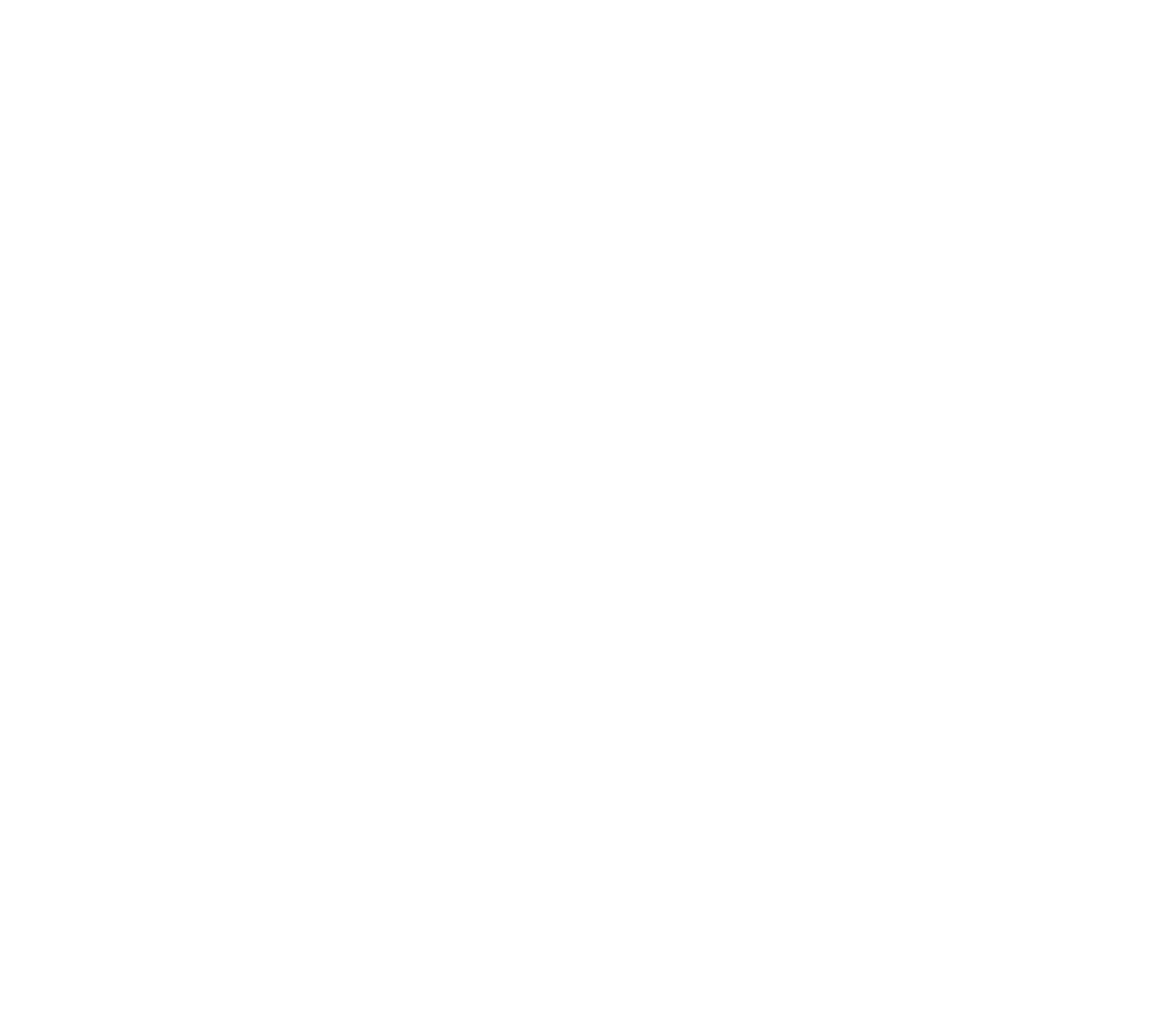
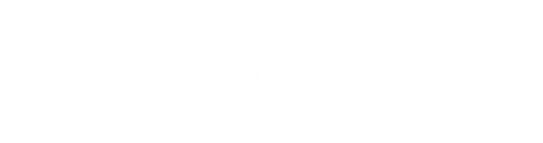
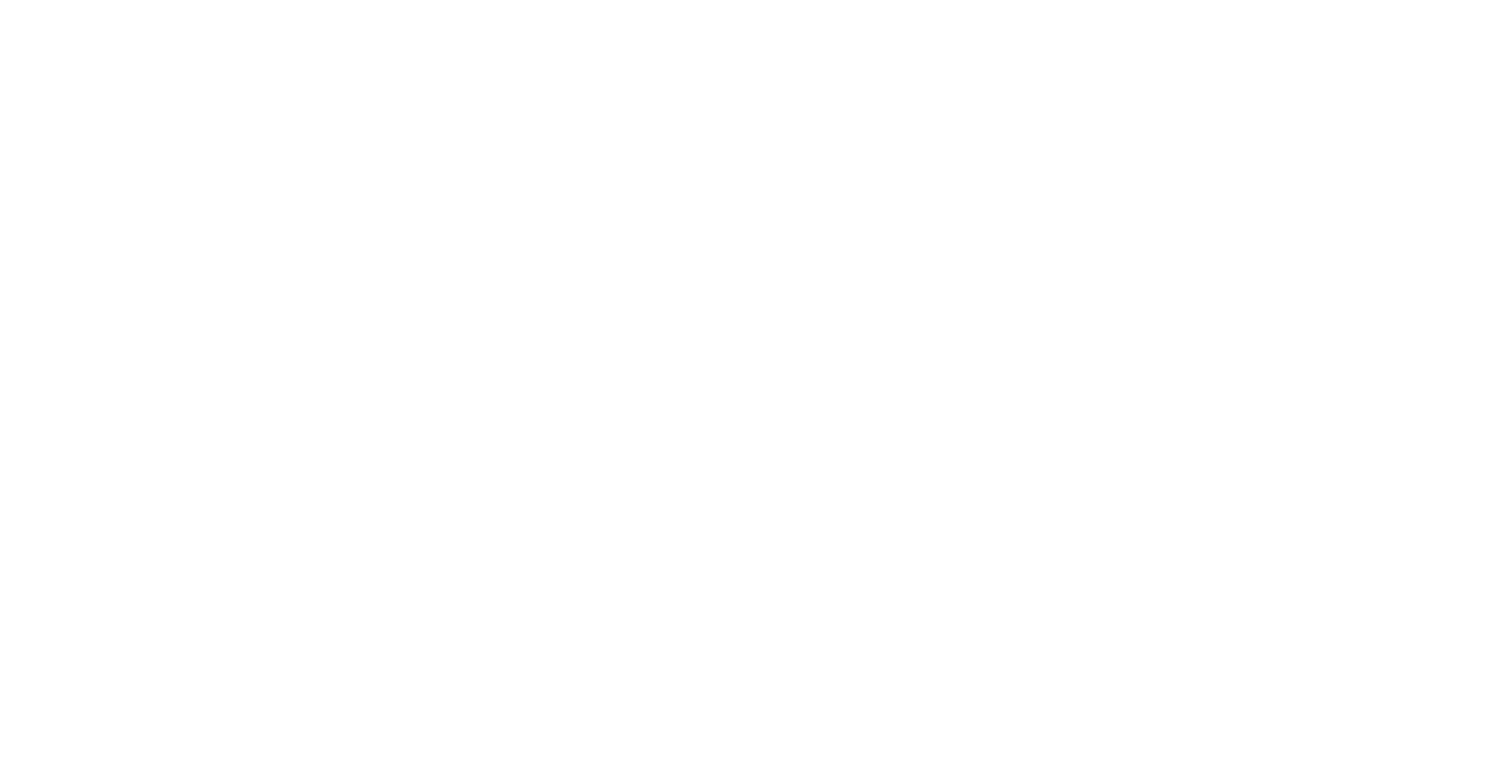
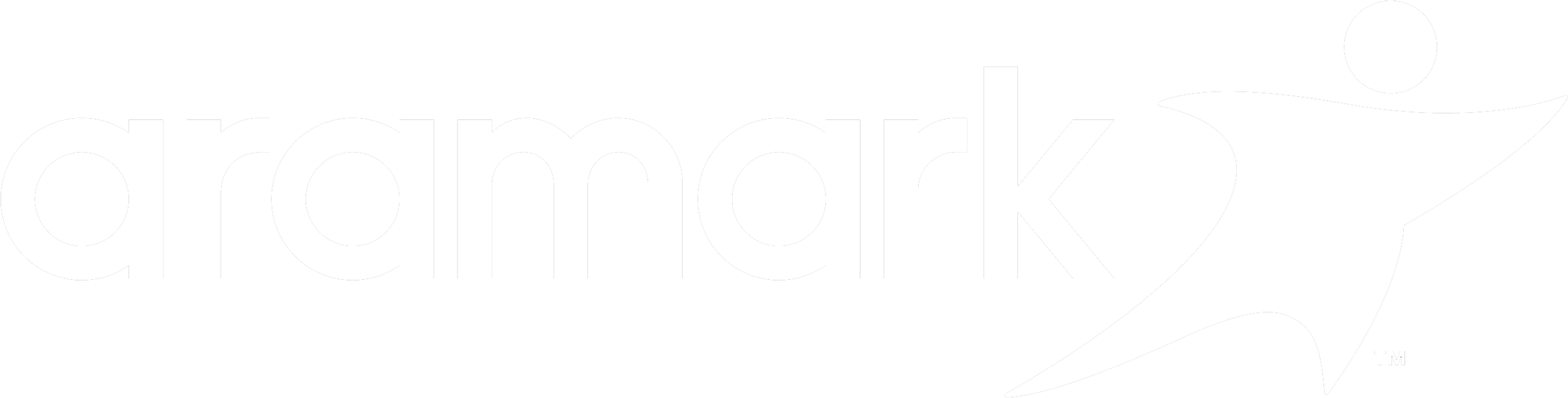
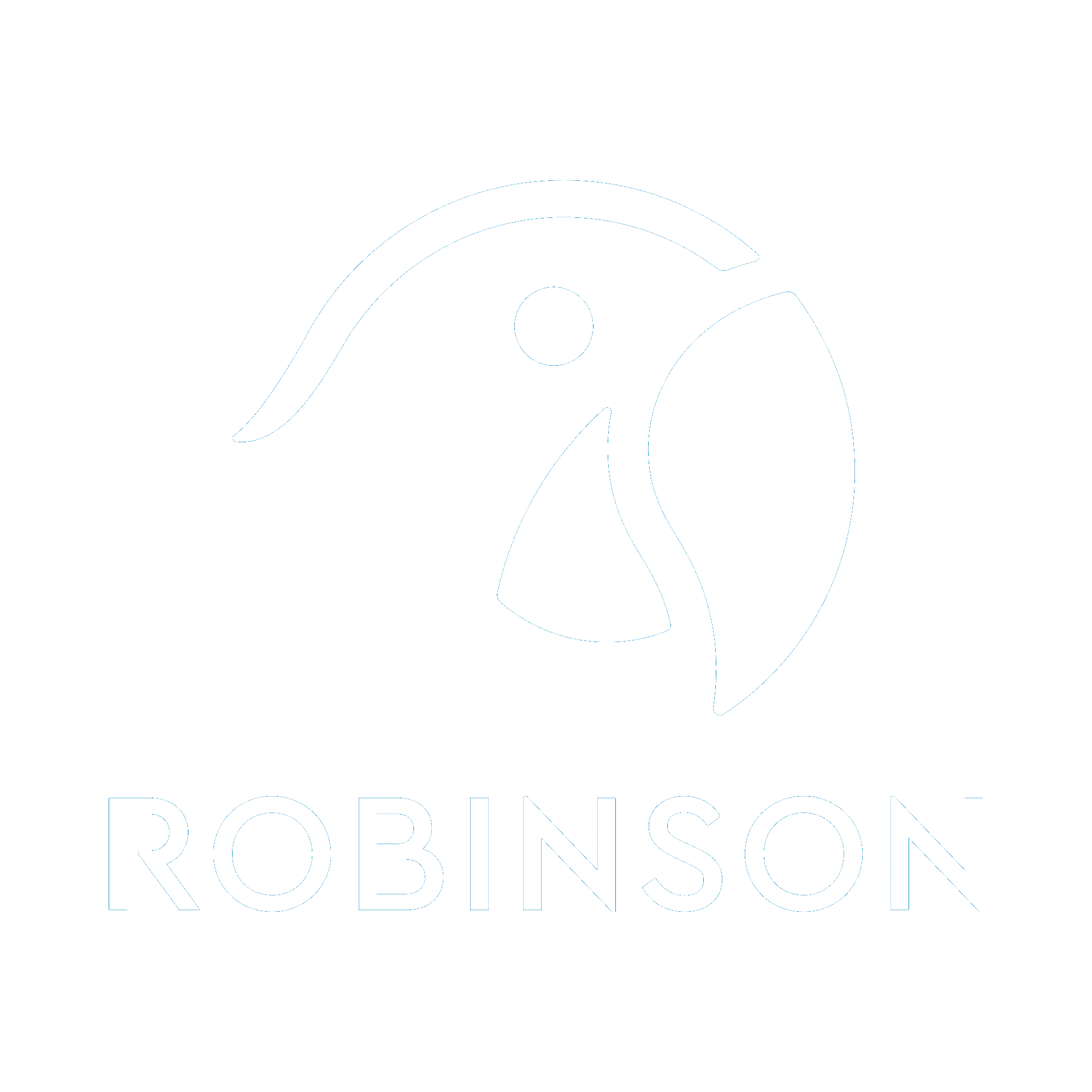
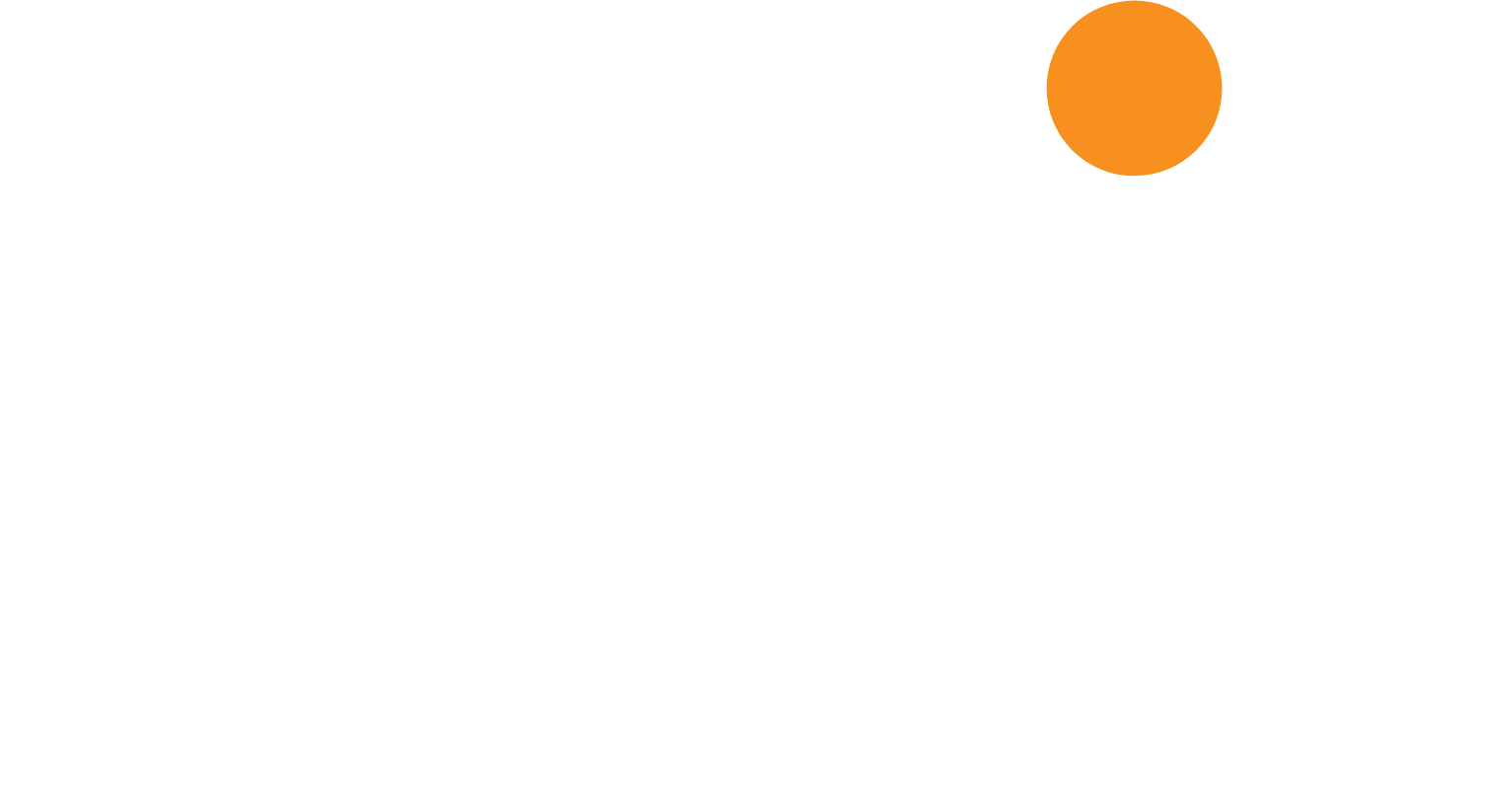
A Pain-free Way to Purchase, Organize, and Use Inventory: Benefits of Parts Inventory Management Software
Reduce Downtime
Minimizing downtime is pivotal for businesses in asset-intensive industries, as it directly impacts productivity and profitability. ToolSense takes various measures to reduce downtime, such as providing easy issue reporting through QR codes and implementing efficient maintenance workflows with the help of a dedicated maintenance team. This streamlined process allows businesses to quickly identify and address potential issues before they escalate into major problems, ultimately reducing downtime and enhancing overall efficiency without sacrificing quality.
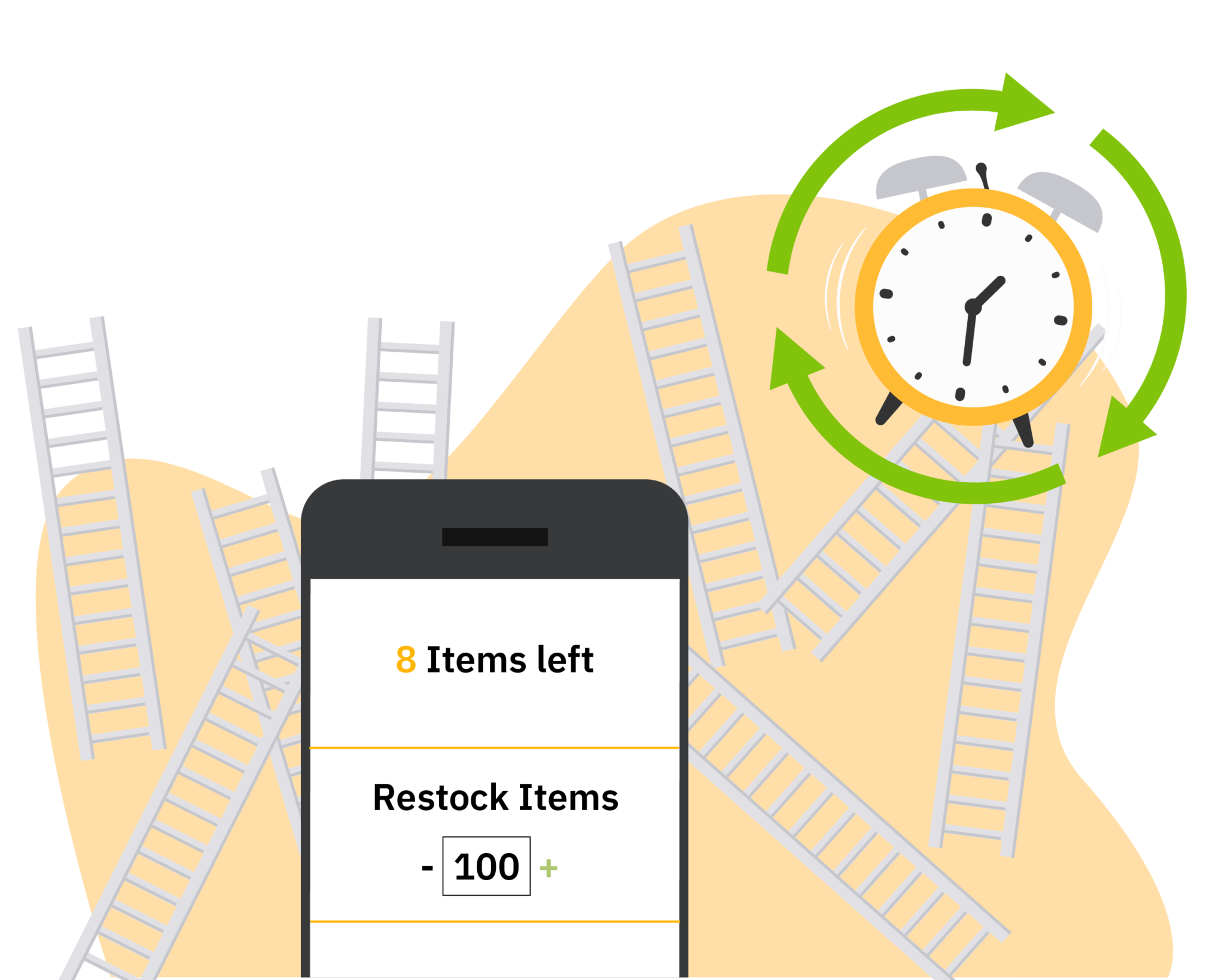
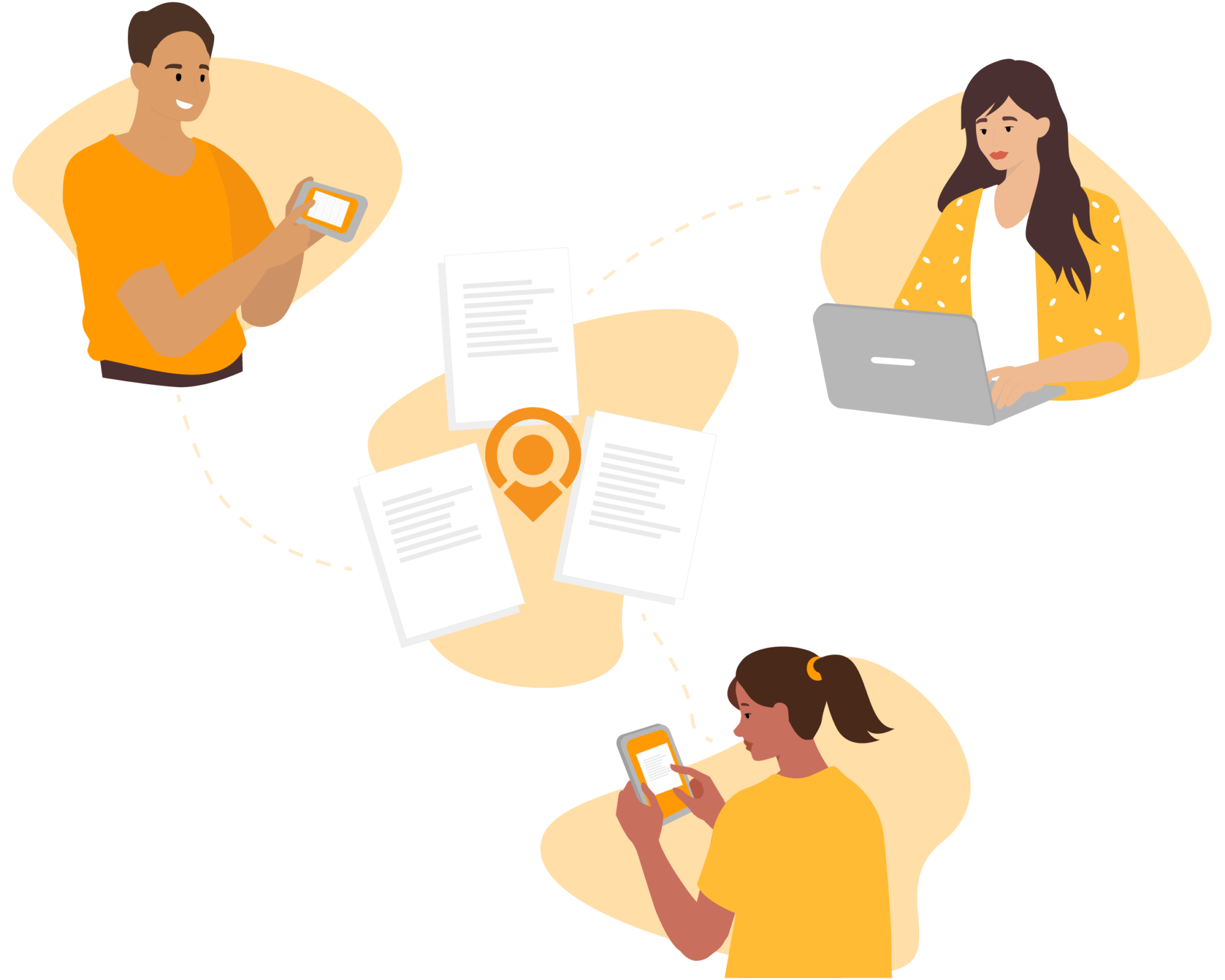
Increased Productivity
ToolSense dramatically increases productivity by automating the inventory management process. With features like real-time tracking, low inventory alerts, and QR code scanning, businesses can save valuable time that would otherwise be spent on manual inventory checks and data entry. Moreover, ToolSense’s full inventory reporting provides businesses with valuable insights into their inventory, enabling them to make data-driven decisions to optimize their operations. An example could be identifying fast-moving items to prioritize their stocking, or pinpointing less popular items to reduce their storage space.
Cost Savings
ToolSense helps businesses save money by automating inventory management, reducing labor and time costs. It optimizes stock levels with real-time tracking and alerts, preventing overstocking and shortages. The software supports data-driven decision-making, allowing for efficient inventory and storage management. Integration with ERP systems enhances vendor negotiations, leading to potential discounts. Additionally, ToolSense reduces equipment downtime through efficient maintenance workflows, avoiding costly operational delays and equipment failures.
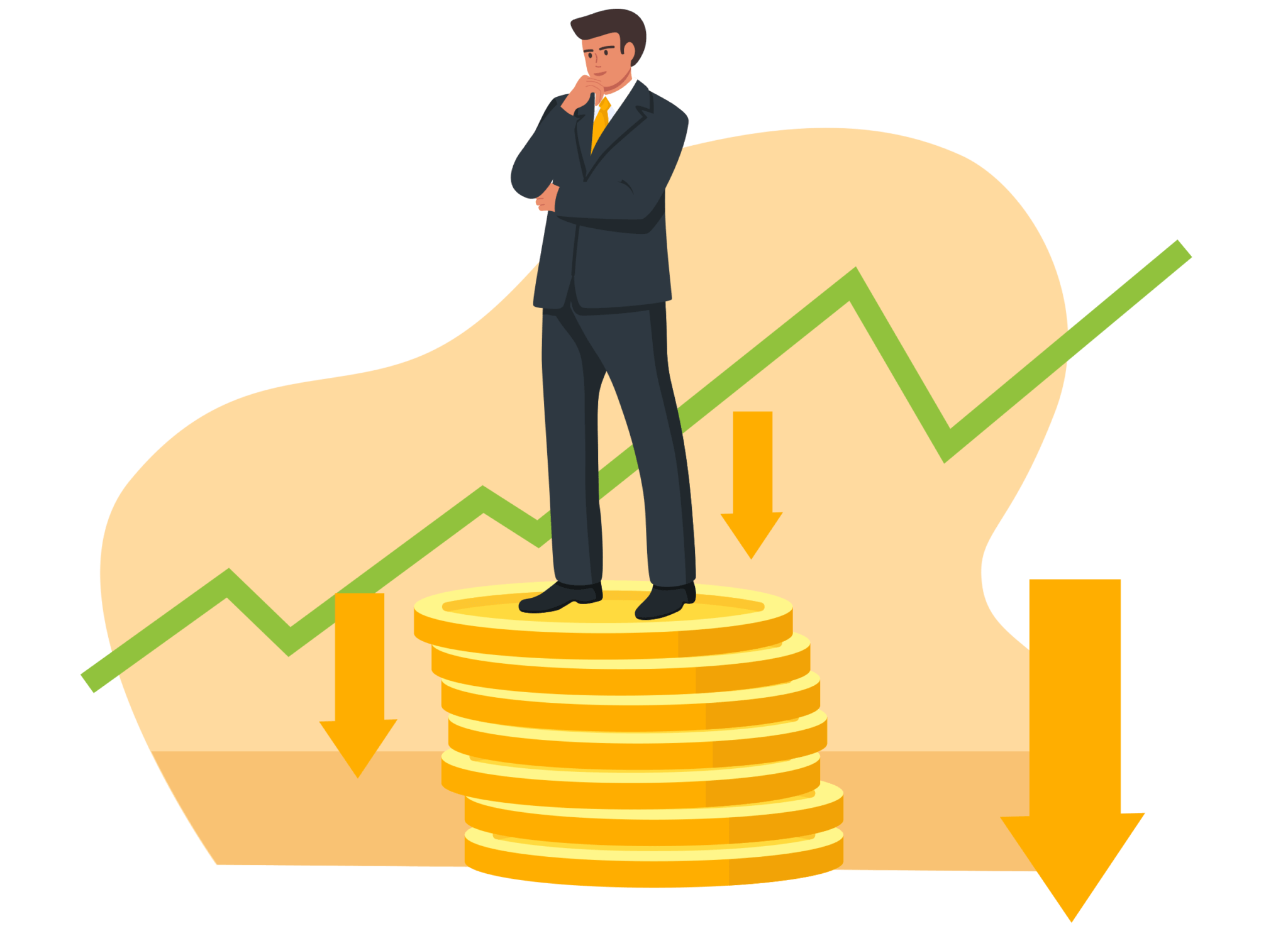