General Construction
Stay in Control of Your Job Site with ToolSense
Construction companies rely on heavy machinery and complex operations to meet tight deadlines. However, poor asset tracking, unplanned downtime, and inefficiencies often lead to costly delays.
If the video embed isn’t working as expected, please find the full video here.
Are these your challenges?
- Difficulty tracking large fleets of excavators, loaders, dumpers and other heavy machinery across multiple job sites.
- High costs from unplanned maintenance and underutilized equipment.
- Poor communication between teams and reliance on siloed IoT systems that don’t integrate.
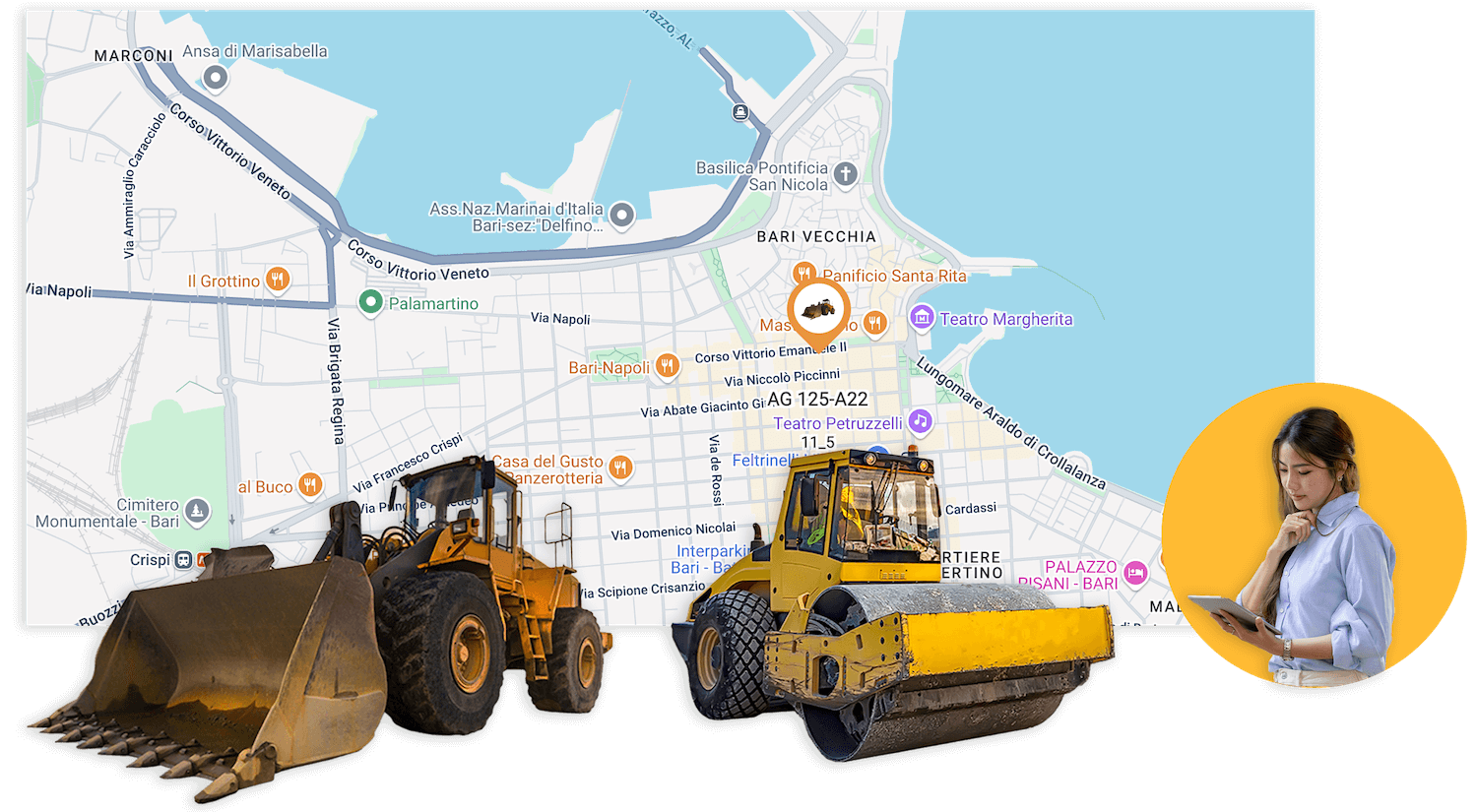
Ready to ditch Excel and Paper?
Join 700+ Operations, Maintenance & Repair Teams Simplifying Their Daily Business
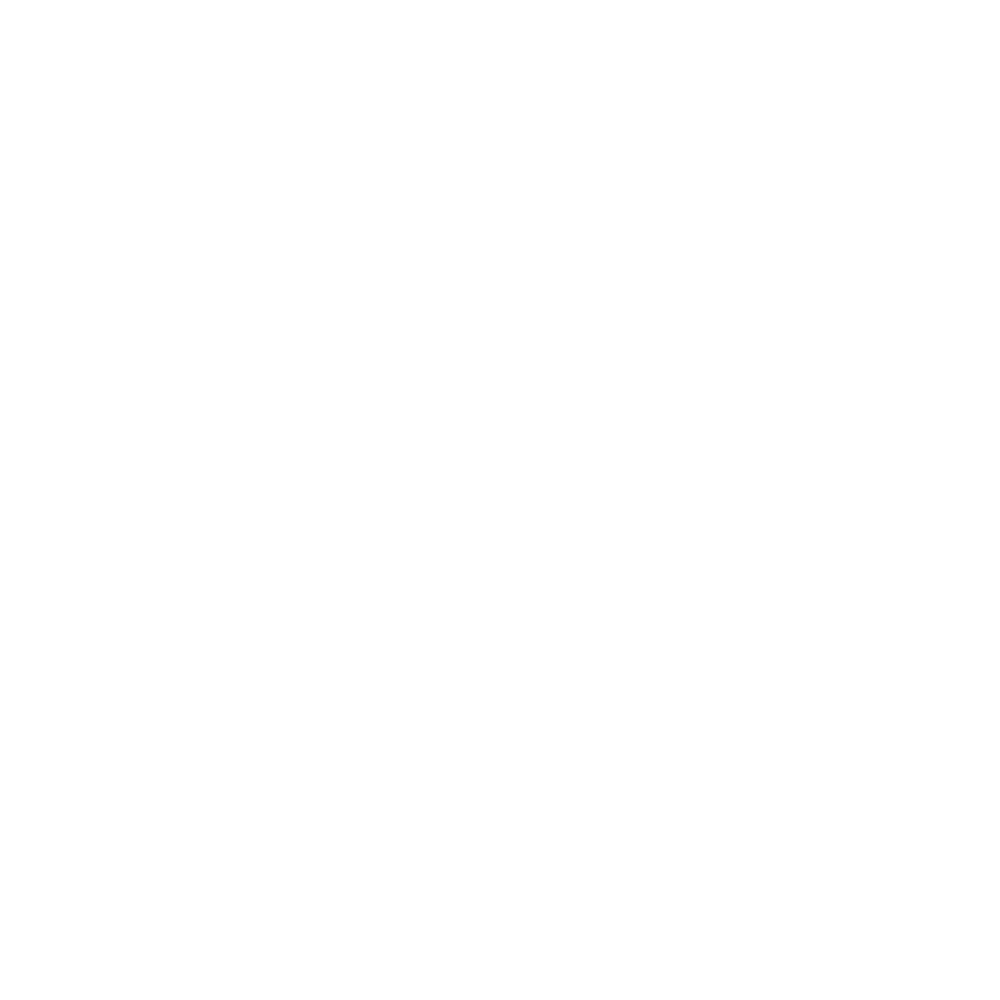
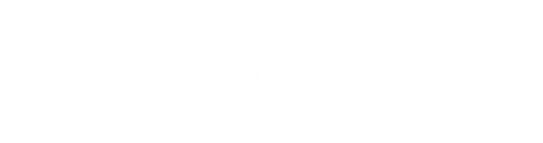
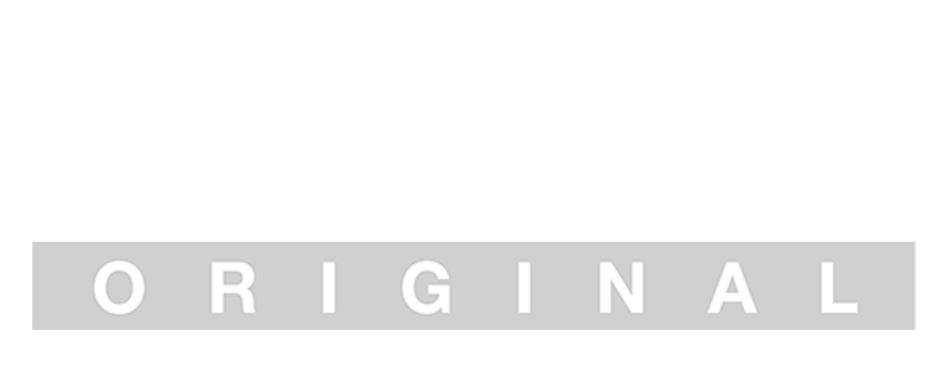
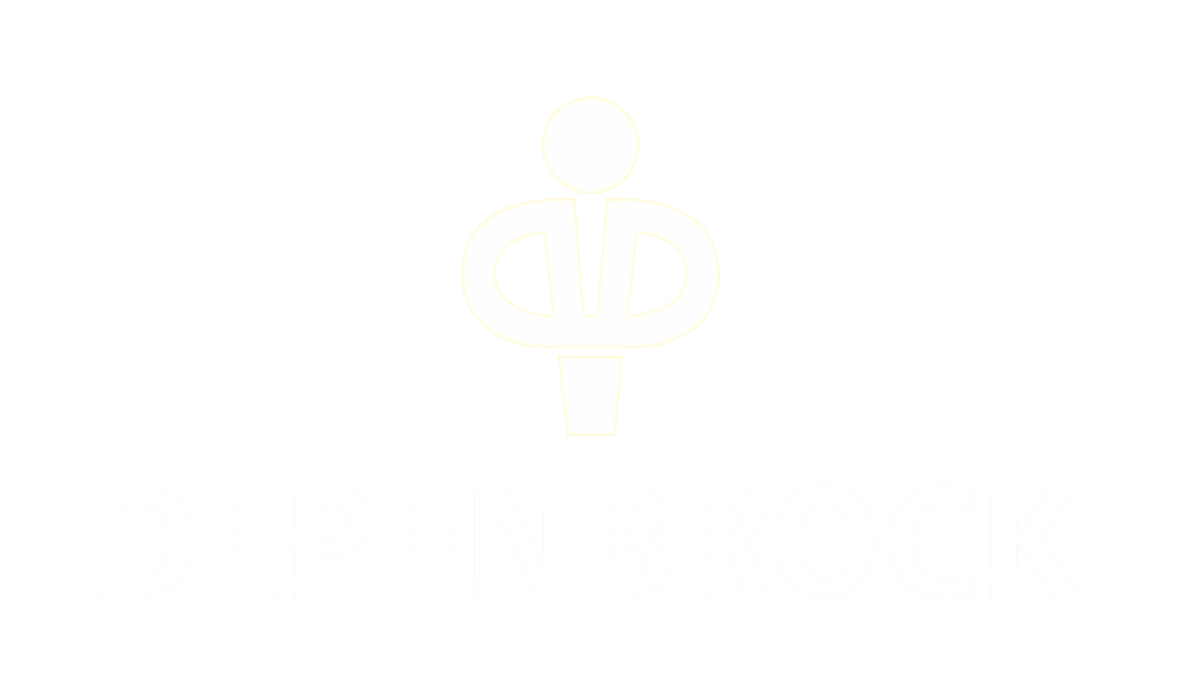
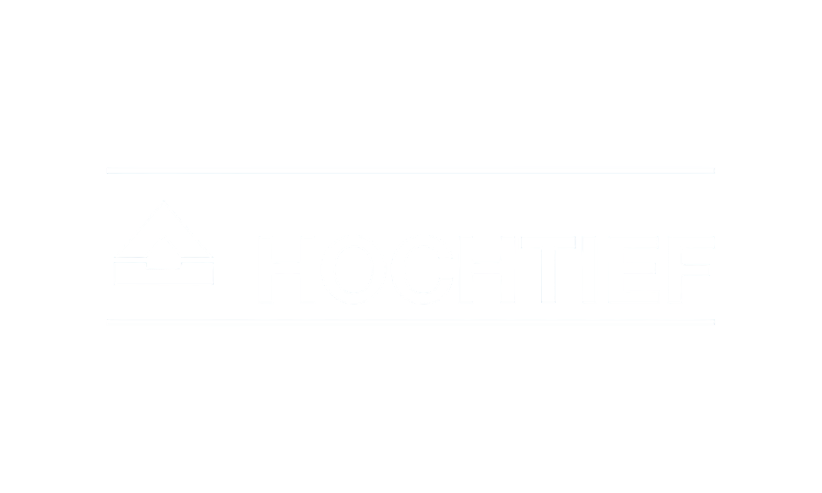
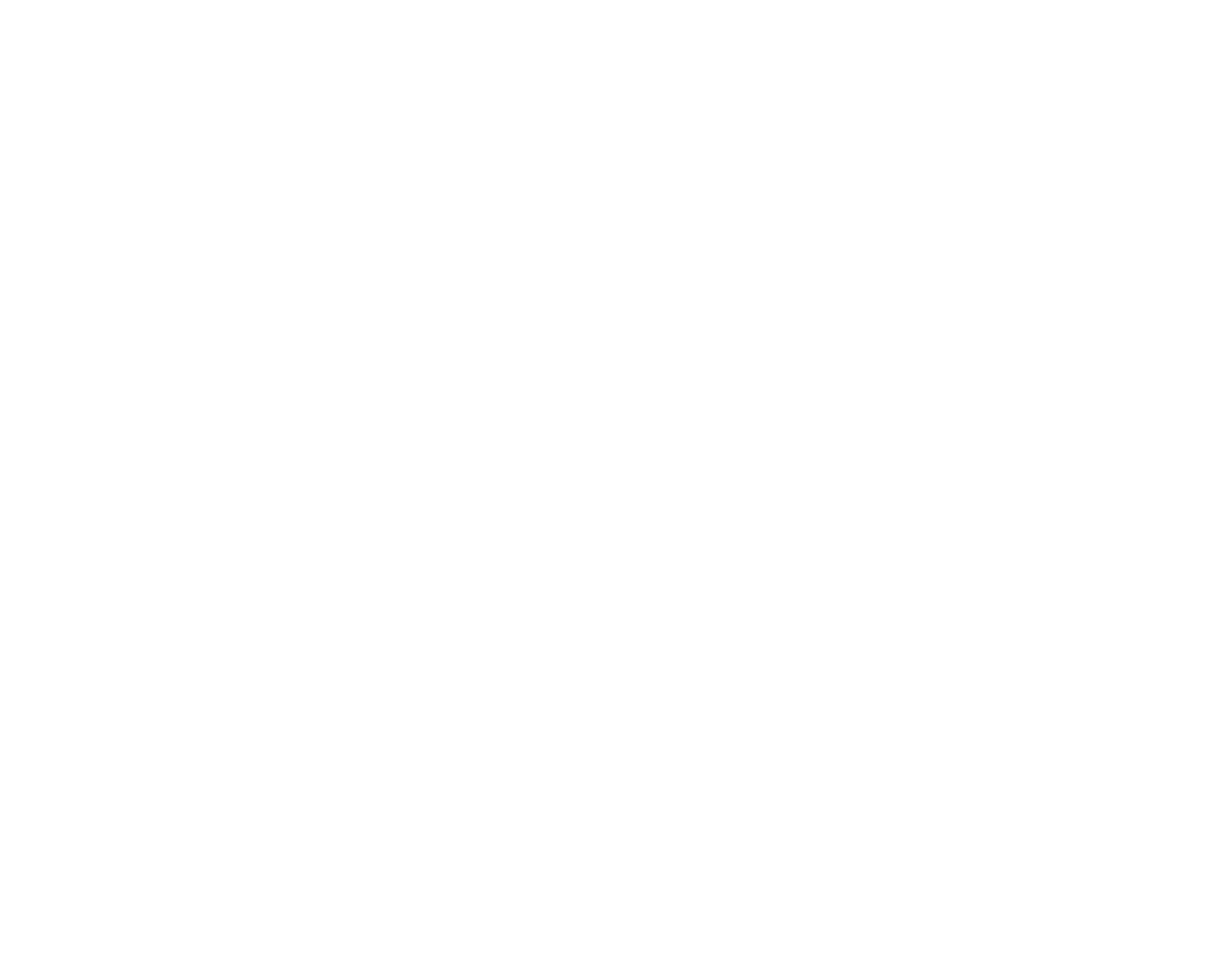
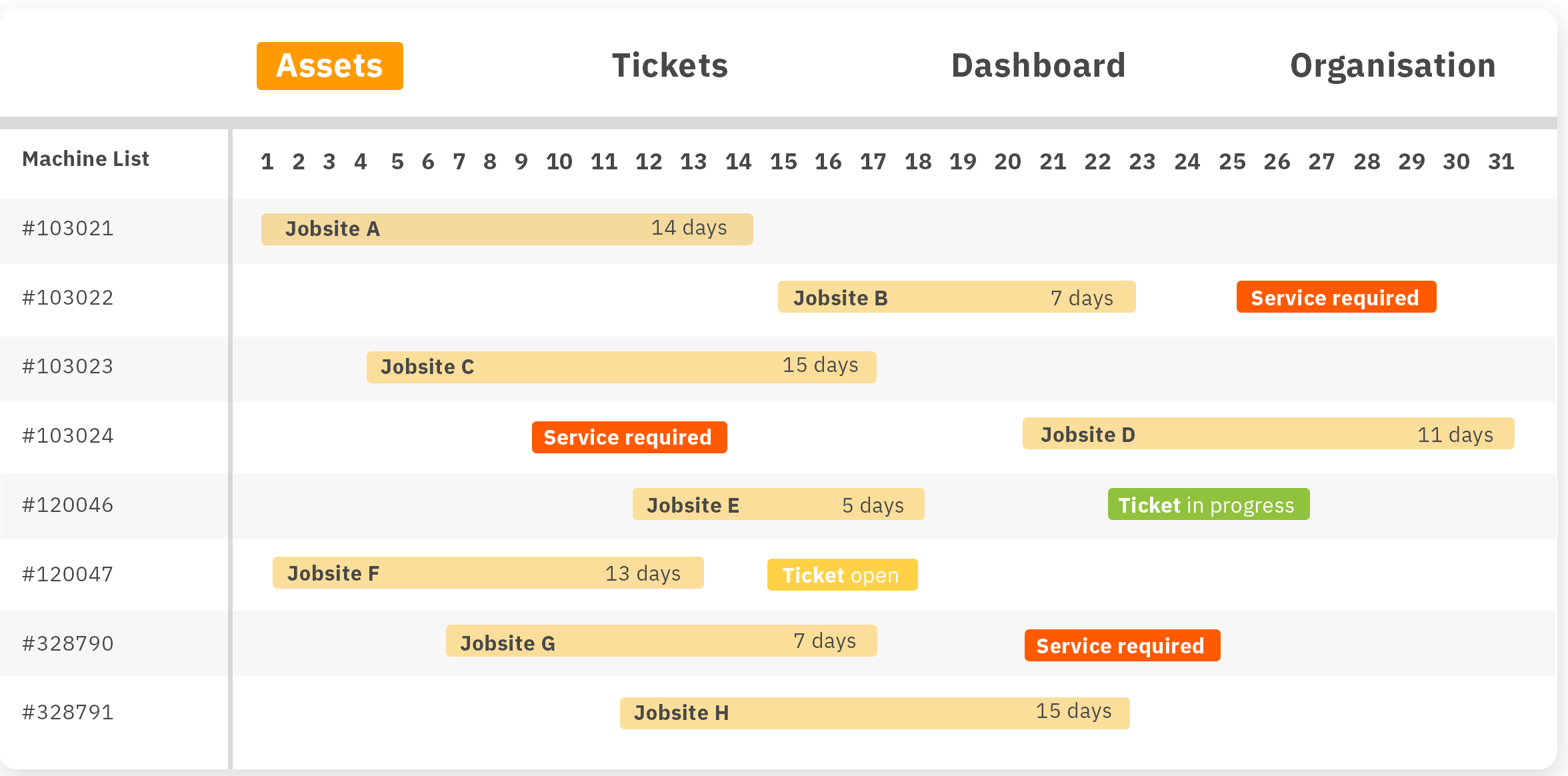
Digital Scheduling & Assignment
ToolSense digitizes your entire scheduling, cost assignment and dispatching processes. From machine requests to planning and logistics. The QR code-based solution enables real-time tracking of equipment locations and availability status, while automated notifications keep all stakeholders informed without time-consuming phone calls.
Detailed digital documentation creates complete transparency across projects and cost centers, helping you optimize resource allocation and reduce equipment downtime. Save time, money, and nerves by digitizing your asset operations.
Unified Telematics & Tags
Digitize all your machines, equipment, and resources with ToolSense. From ladders to vibratory plates, to excavators or trucks. Either with the ToolSense IoT hardware in retro-fit – or via the AEMP 2.0 standard using existing OEM telematics devices, for example from Caterpillar, Komatsu, or Volvo.
The platform’s flexible integration capabilities allow you to consolidate data from diverse equipment types and manufacturers into a single, comprehensive dashboard, eliminating information silos. This unified approach provides construction managers with actionable insights across their entire fleet, regardless of equipment size, type, or brand origin.
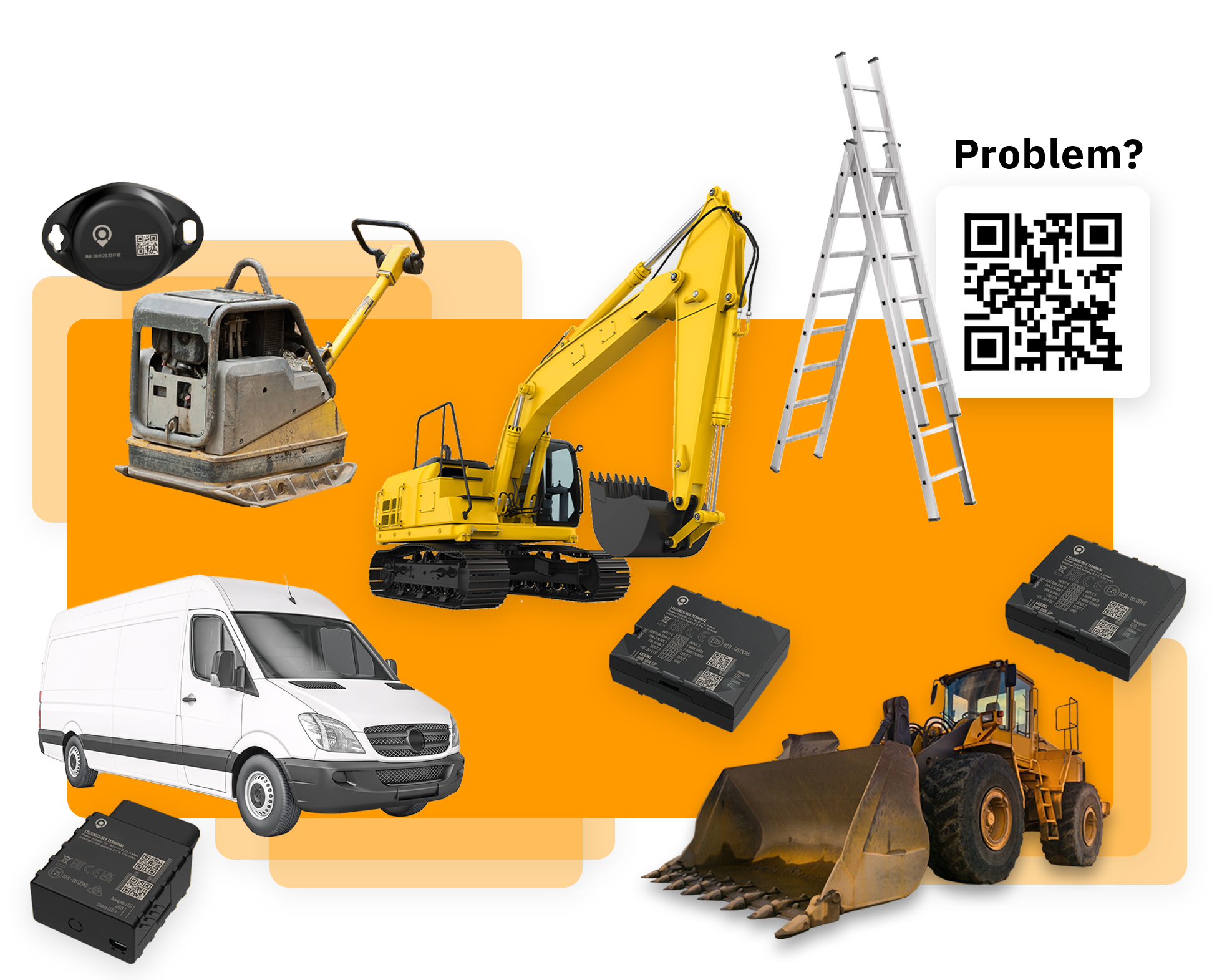
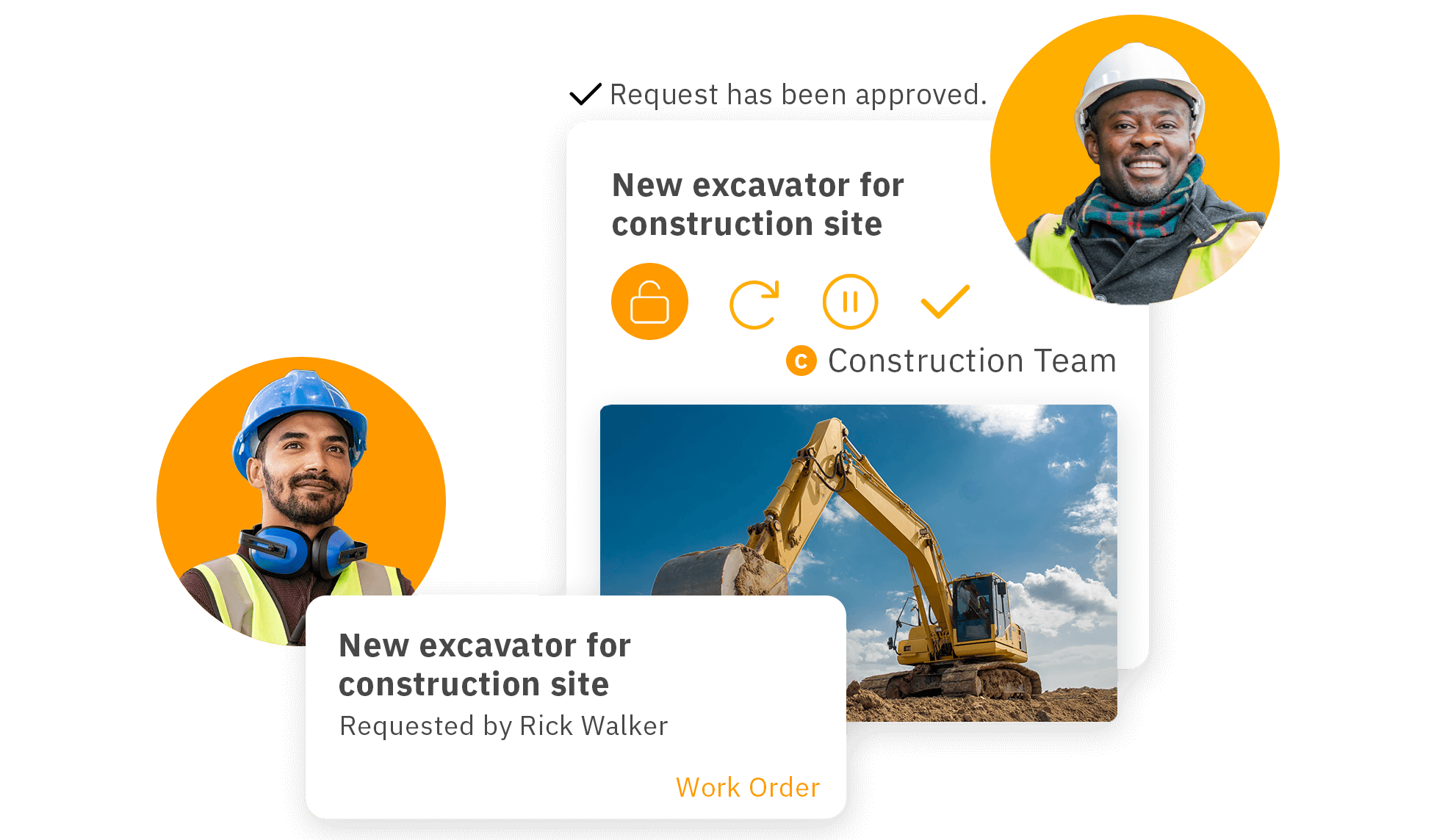
Digital Machine Requests & Delivery Bills
Use ToolSense for digital internal and external transport organization, automated form creation and digital transmission to the responsible driver. Pickup and delivery locations can also be defined in the app.
The system streamlines documentation by generating digital delivery notes that can be signed directly on mobile devices, creating a paperless workflow that reduces administrative burden and eliminates lost paperwork. Real-time status updates allow project managers to track equipment movements precisely, ensuring that critical machinery arrives exactly when and where it’s needed on your construction sites.
Andreas Hüttner
Head of Business Administration
Leithäusl
Our processes have fundamentally changed. Even during the pilot phase, we completely rethought our workflows, seriously questioning what we actually needed, what we should continue using, and what we should eliminate. We streamlined extensively, and now we have a unified database with all employees having access to the same information – this is a substantial advantage. And of course, we no longer waste so much time with paper forms.
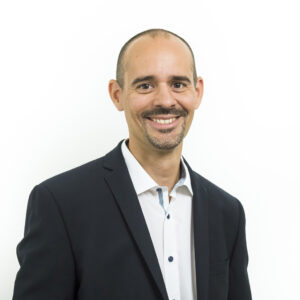
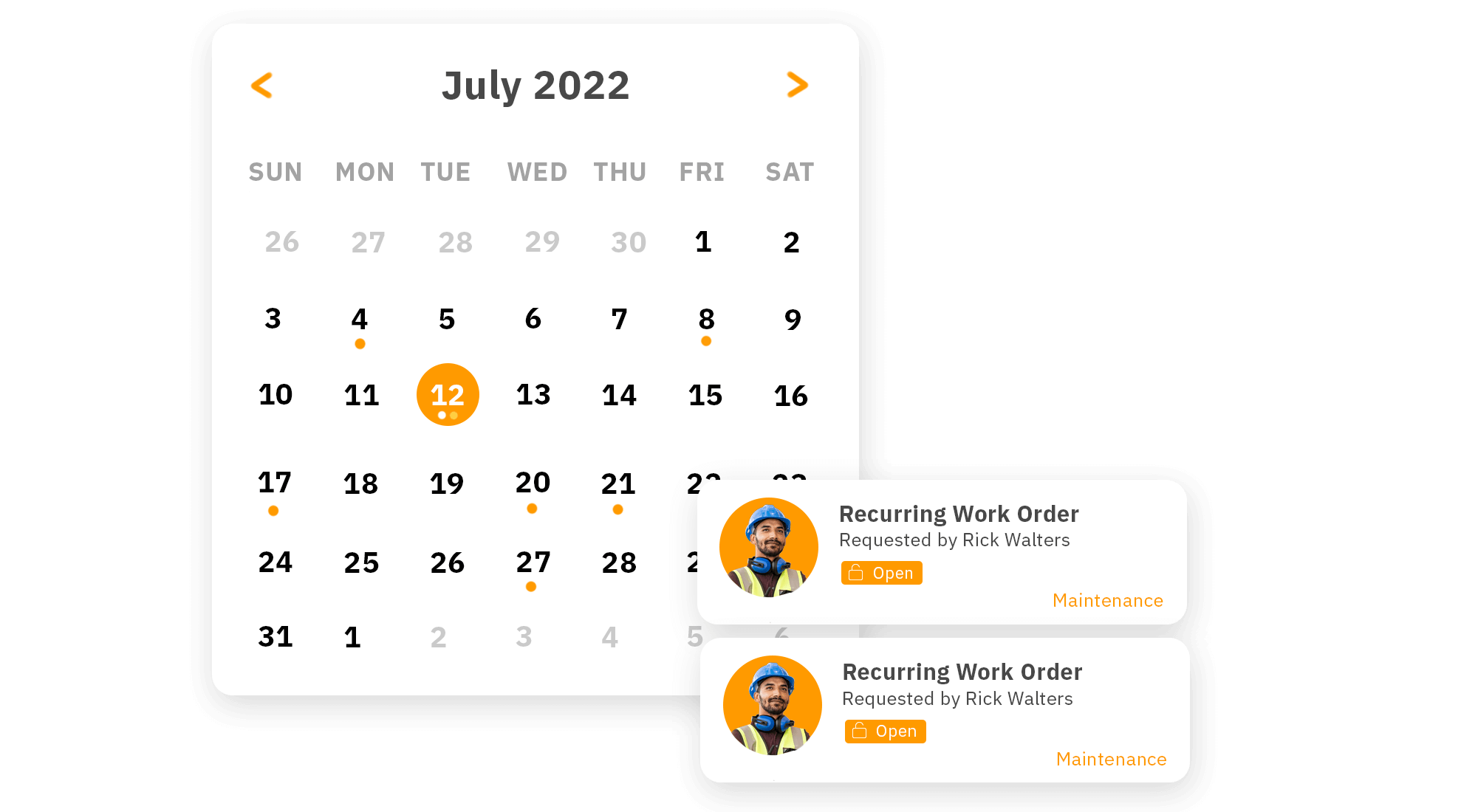
Digital Checks & Inspections
Staying ahead of the requirements for safety inspections without proper tools takes plenty of time and effort. Flexible rules, preconfigured and custom inspections and powerful automations ensure a flawless operation of your assets.
ToolSense offers construction-specific inspection templates compliant with industry regulations, including ladder checks, LOLER inspections, and equipment safety protocols that can be completed quickly via smartphone. The system automatically flags overdue inspections and documents all compliance activities with time stamps and photo evidence, providing critical protection against liability issues while significantly reducing the administrative workload for your safety personnel.
Streamline Parts Consumption & Procurement
Ensure consistent documentation with QR-codes applied to all your assets, reduce downtime with accurate parts quantities, and finally simplify purchase orders and avoid stockouts.
The intelligent inventory management system within ToolSense tracks consumption patterns across your entire construction fleet, automatically triggering reorder alerts when supplies reach predetermined thresholds. By connecting maintenance records directly to parts usage, you gain valuable insights into which components require frequent replacement, enabling data-driven decisions about equipment reliability and potential upgrades that can significantly reduce your total cost of ownership.
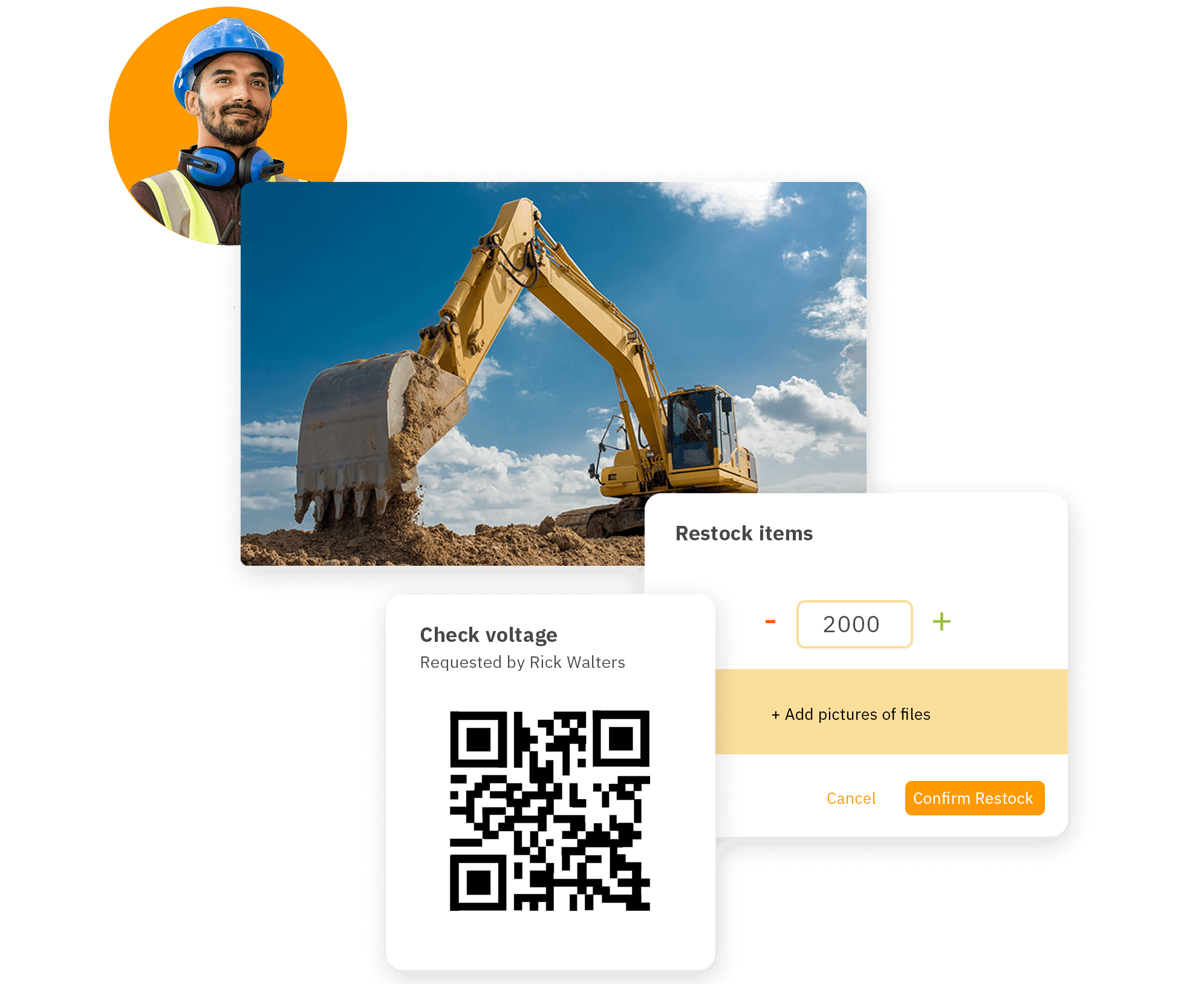
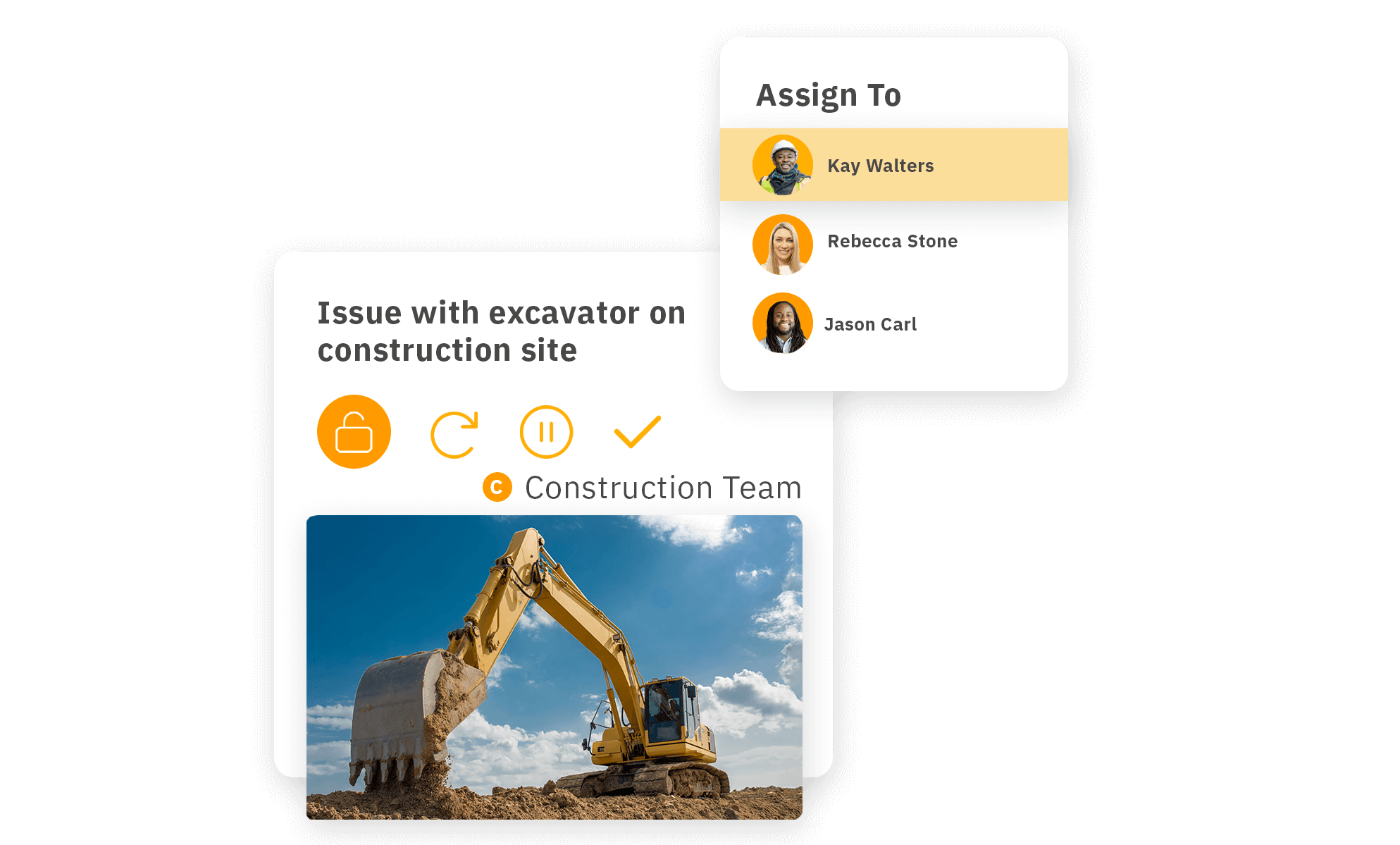
Reactive Work Orders Made Easy
Know what’s working and what isn’t, and who is fixing what when. Assign Work Orders to your technicians to fulfill maintenance requests for machines, assets, and other equipment. The intuitive mobile interface allows field technicians to access complete equipment history, service manuals, and troubleshooting guides directly at the point of repair, dramatically improving first-time fix rates on construction sites.
Improve Your Business Impact
Save 20% on cut repair costs and reduce equipment idle time by 25%. Improve your project delivery timelines with fewer delays due to equipment failure.
Customer Success Story: Leithäusl Bau GmbH
Austrian construction company Leithäusl Bau GmbH faced significant inefficiencies in managing its machines, tools, and equipment due to outdated, manual processes.
With ToolSense, Leithäusl achieved:
- €22,500 in annual savings by reducing time and resource waste.
- 609 work hours, or approximately 76 workdays, freed up for more productive tasks.
- Significant improvements in transparency and efficiency in machine management.