Supply chain interruptions caused by the Covid-19 pandemic and geopolitics have forced virtually all businesses to revisit their inventory management systems. Across industries, more advanced and effective methods for efficiently maintaining property inventory levels. Here are 14 of the most popular inventory management trends.
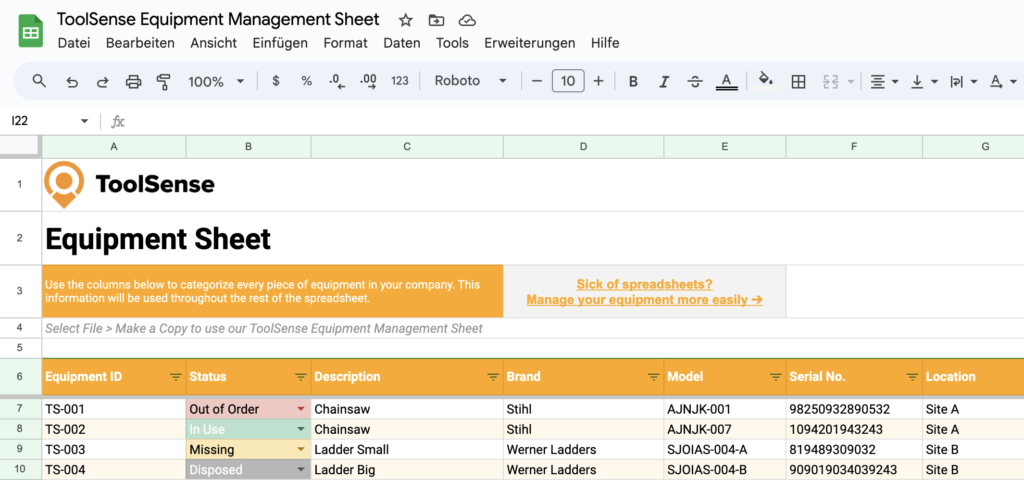
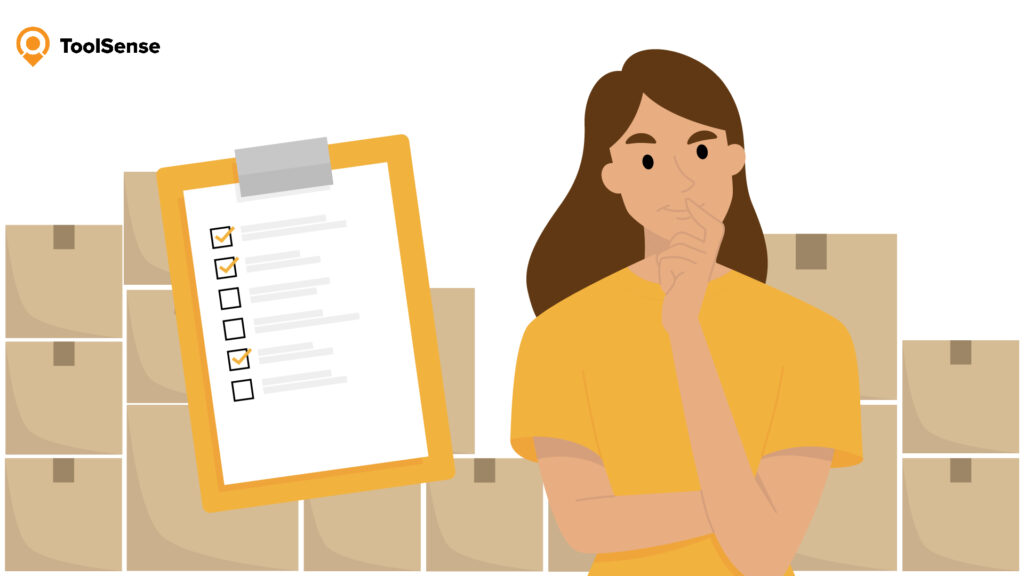
Key Takeaways
- Inventory management systems are becoming more spread out yet also more connected.
- Artificial intelligence, data analytics and cloud-based software are essential to modern inventory management.
- Trends are toward faster, more cost-efficient and more reliable supply chains and distribution networks.
What Is Inventory Management?
Inventory management is the method by which businesses ensure they have a steady stock of goods, whether they be supplies, finished products, or other assets necessary to operations.
Successful business owners and managers usually use a combination of inventory management processes to devise an efficient system that navigates inventory level, location, pricing, logistics and supply chain factors. The inventory management process is very time-consuming, and it involves many users and intermediaries, especially for manufacturers and enterprises.
ToolSense is trusted by 700+ companies
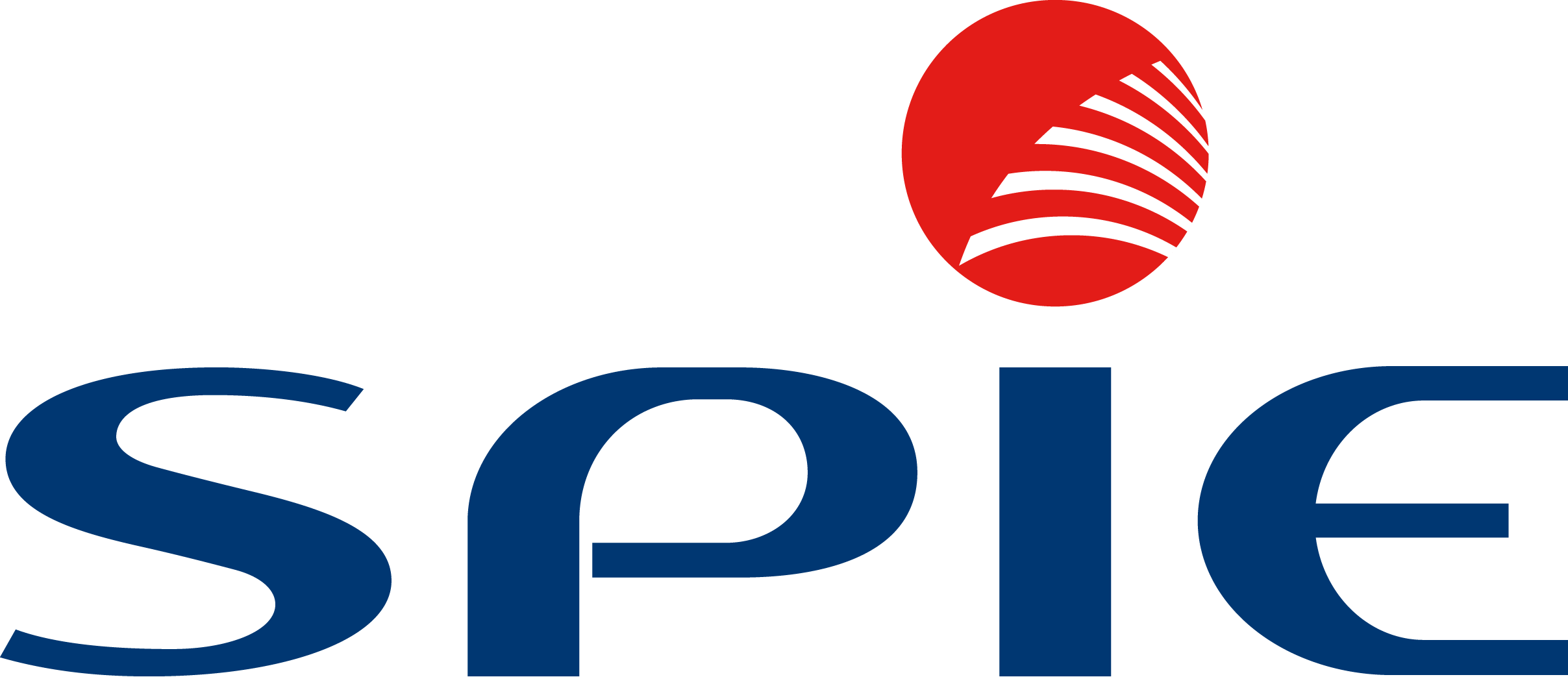
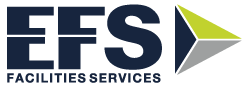
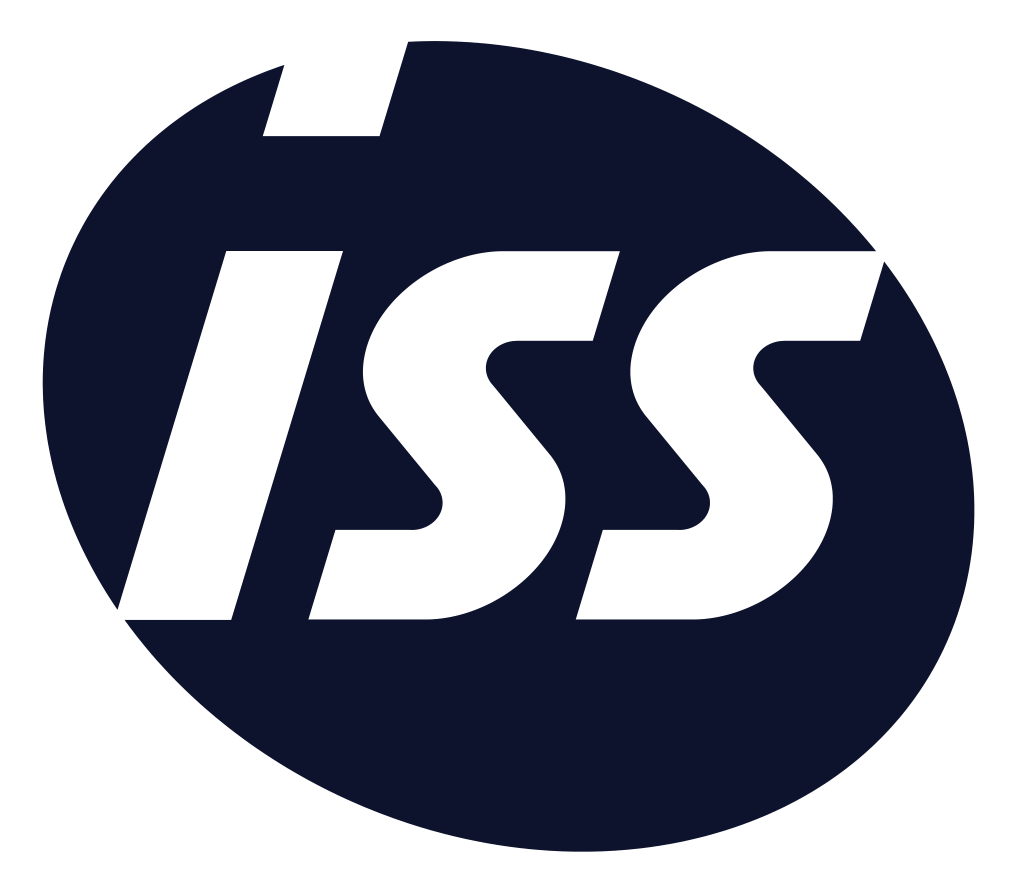
Why Are Inventory Models Important?
Inventory models are the systems that businesses use to establish and develop the most efficient way to maintain necessary inventory levels. While there are many methods by which inventor levels can be maintained, no one method is ideal for every situation.
Inventory models can help determine which of the various methods is most suitable, and then how to maximize the chosen method’s efficiency. Some different models that businesses might use for their inventory are:
Just in Time (JIT) | Useful for minimizing storage and inventory overhead, but susceptible to supply chain disruptions and price changes. |
Day Sales of Inventory (DSI) | Useful for managing perishable goods and space in smaller retail outlets. |
Materials Requirement Planning (MRP) | Useful for reliably sourcing manufacturing materials across complex supply chain processes. |
Centralized Inventory Model (CIM) | Useful for controlling inventory levels and tracking movement of goods, in order to minimize shrinkage. |
Economic Order Quantity (EOQ) | Useful for minimizing inventory costs, including order costs, shortage costs and holding costs. |
Economic Production Quantity (EPQ) | Useful for managing costs and shrinkage in manufacturing and other production. |
There are still more inventory models that businesses use in select situations, and technological innovations are increasingly giving rise to hybrid and combination models that take advantage of multiple models.
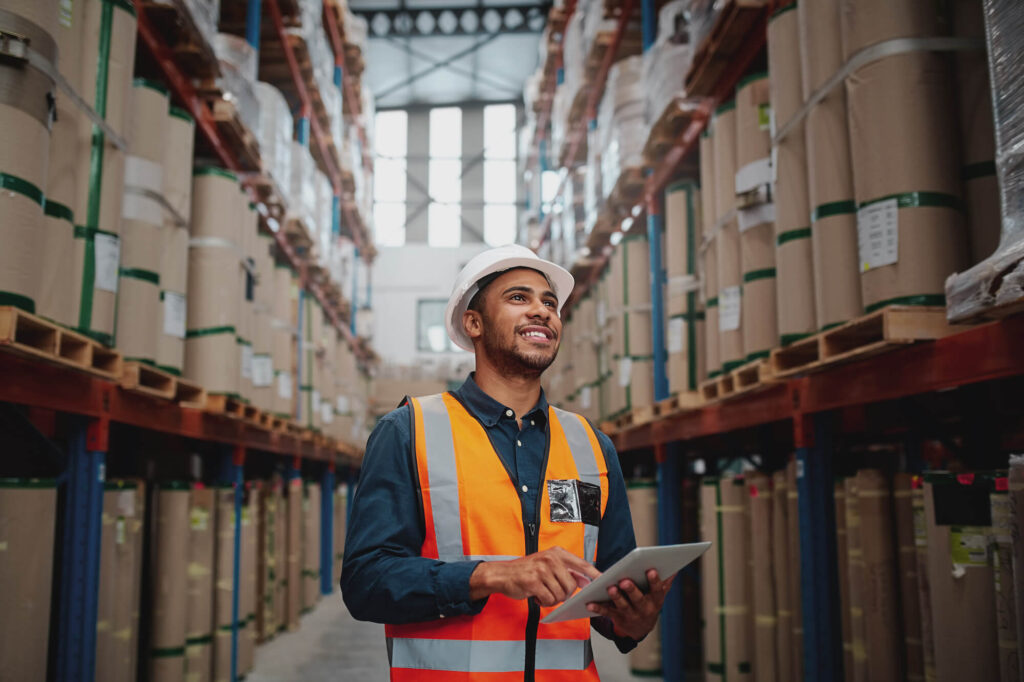
Top 14 Trends in Inventory Management
1. Cloud Technology for Hybrid Work
Cloud technology improves inventory management efficiencies. Businesses have fewer information technology issues to monitor, as a third party oversees servers (and sometimes program updates). The cloud can also sync inventory levels, purchases and other data across supply chain, warehouse and store locations.
As cloud computing continues to improve, its usage in inventory management has steadily been increasing. The transition to work-from-home and hybrid work setups has accelerated the technology’s implementation. An inventory management app is one of the easiest ways to sync inventory details across business locations and employees’ homes.
The best inventory management software isn’t just compatible with the cloud, but is mostly or entirely cloud-based.
2. Internet of Things for Complete Connectivity
One of the most important inventory management trends is the IoT. The internet of things (IoT) takes cloud technology and integrates it throughout locations. Not only do computers communicate with one another, but virtually everything in a business location can join the local network. Scanners, loading bays, equipment, and even goods themselves can be added onto a location’s IoT network.
3. Artificial Intelligence/Machine Learning for Improvement
Artificial intelligence (AI) and machine learning (ML) provide constant improvement as computer programs learn more about a particular business’s inventory system. These programmes can better integrate inventory movement and levels across complex networks, and they can identify weaknesses that create increased costs. For example, AI/ML might show that a particular product’s packaging results in above-average shipping damage rates.
AI and ML get more powerful as businesses integrate IoT technology, for the technology gives AI/ML more data to analyse.
4. Data Analytics for Predictive Picking
Once extensive data is recorded and analysed, that information can be used to improve picking rates in warehouses. Analysis can show products that are commonly purchased together and/or that are usually purchased by customers with certain behaviours.
Commonly combined products can be placed next to one another, so pickers spend less time going between aisles, and sometimes it’s even possible to pick orders before they occur. That not only improves picking efficiencies, but also allows for even faster delivery times.
Data analytics is reliant on IoT, ML, and AI. As these three advance, more businesses will be able to initiate predictive picking.
5. Warehouse Automation for Labor Reduction
The more that can be automated in warehouse management, the less businesses must spend on employee wages. In most cases, it costs less to maintain a robot than it does to pay an employee.
Warehouse automation will become more prevalent for a few reasons. Improvements in AI, ML and robotics make for more automation possibilities, and costs are decreasing as equipment and software are more available. Additionally, rising wage rates create greater potential savings.
Get the insight you need to reduce downtime, lower equipment maintenance and replacement costs, and more with ToolSense and IoT Tracker.
6. AVGs and AMRs for Better Automation
Automation requires equipment, and that equipment includes both automatic guided vehicles (AVGs) and autonomous mobile robots (AMRs). AVGs have been used in warehouses for well over a half-century, and they still have use today. AMRs are able to do even more than their predecessors.
Both AVGs and AMRs are essential for greater automation.
7. Multi-Warehousing for Distribution
Distributed inventory management uses multiple distribution locations throughout a region, a country, or the world. Storing supplies allows for a more geographically streamlined supply chain management, and storing products makes faster delivery possible. It’s also easier to scale, grow and manage emergencies.
Amazon has long used multiple warehouses to provide its fast shipping and reduce transportation costs. As others must keep up with customer delivery time expectations, more businesses are following suit. The Covid-19 pandemic has also made managers keenly aware of how having multiple locations can help when navigating local emergencies (e.g. lockdowns or natural disasters).
Cloud technology is essential for multi-warehousing, so this management option will become increasingly viable as cloud-based inventory management software cost comes down and capabilities expand.
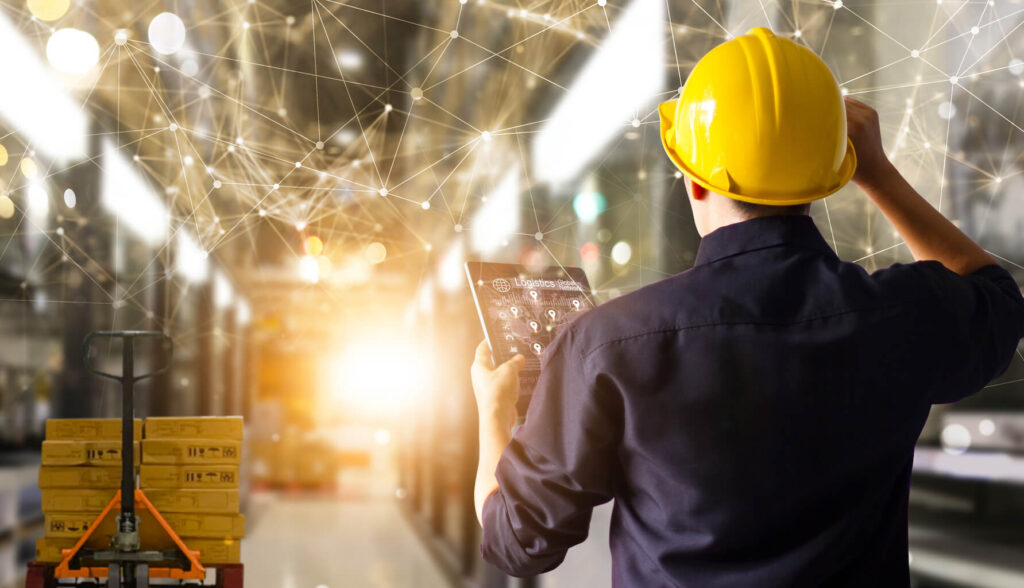
8. Third-Party Logistics for Affordability
Making the most of some inventory management methods requires specialized software, equipment, and warehouse designs. Not all small- and medium-sized businesses (SMBs) have the resources to afford these.
For SMBs, outsourcing to a third-party logistics (3PL) provider eliminates the need for costly capital investments. A 3PL specialist will have the necessary resources, while charging an ongoing fee that’s more manageable on finite budgets.
9. Smart Inventory Forecasting for Improved Purchasing
As AI and data analytics provide more insights into sourcing and sales, businesses get information that enables better purchasing decisions. Smart inventory forecasting will improve inventory levels, as businesses can forecast how much inventory they’ll need due to changing conditions.
ToolSense is trusted by 700+ companies
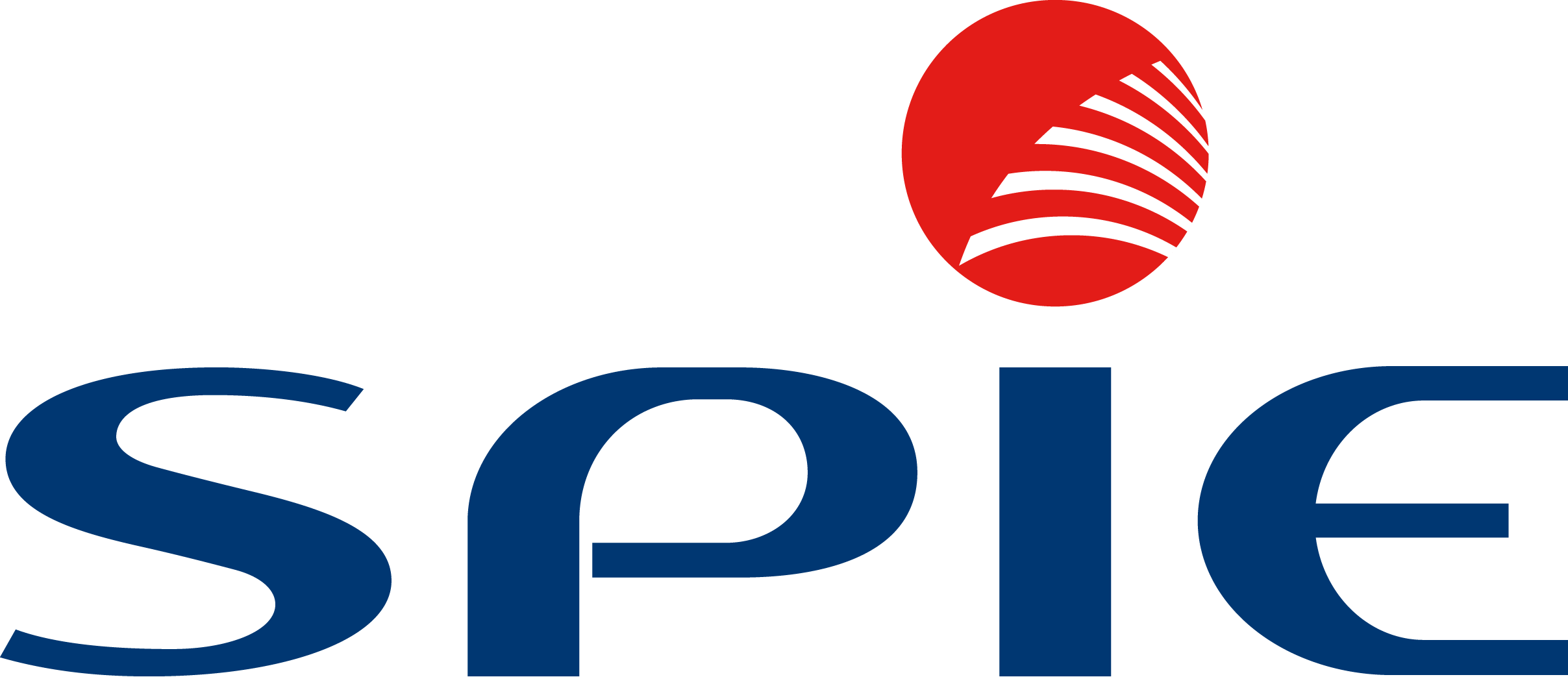
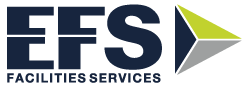
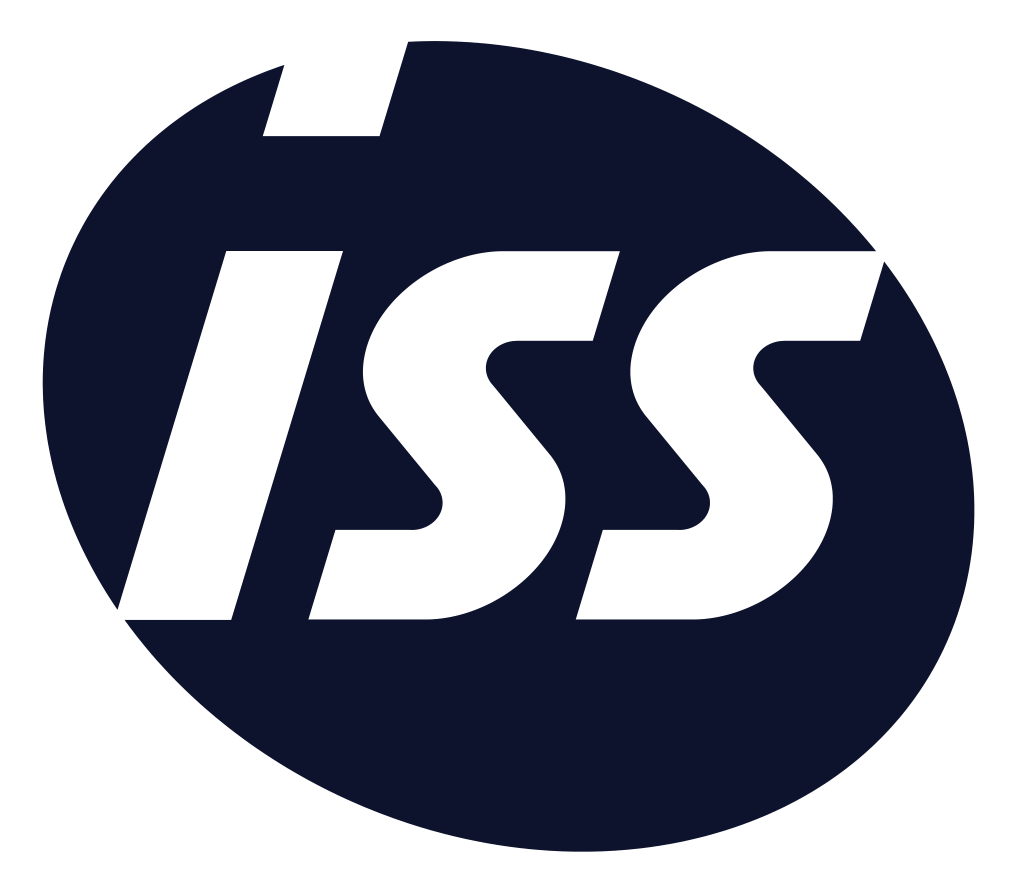
10. Personalization for Better Anticipation
Smart inventory forecasting reaches its pinnacle in the form of personalization. Personalization prompts customers with product suggestions based on their past habits, and it also sometimes includes pre-ordering products based on expected future purchasing habits.
11. Safety Stock for Fluctuations
Safety stock is excess inventory that’s intentionally kept as a hedge. The “safety stock” or “buffer stock” protects against changes in production and/or sales.
Should machinery malfunction or supply chains be interrupted, the safety allows businesses to continue selling products and delivering on existing orders. Should a spike in customer demand deplete standard inventory levels, the safety allows businesses to continue selling as production is ramped up (and to continue taking advantage of the demand spike).
Some businesses have long been keeping safety stock as a best practice. With the supply change interruptions and changing consumer demand that Covid-19 waves have created, more businesses are realizing the benefits of having safety/buffer goods.
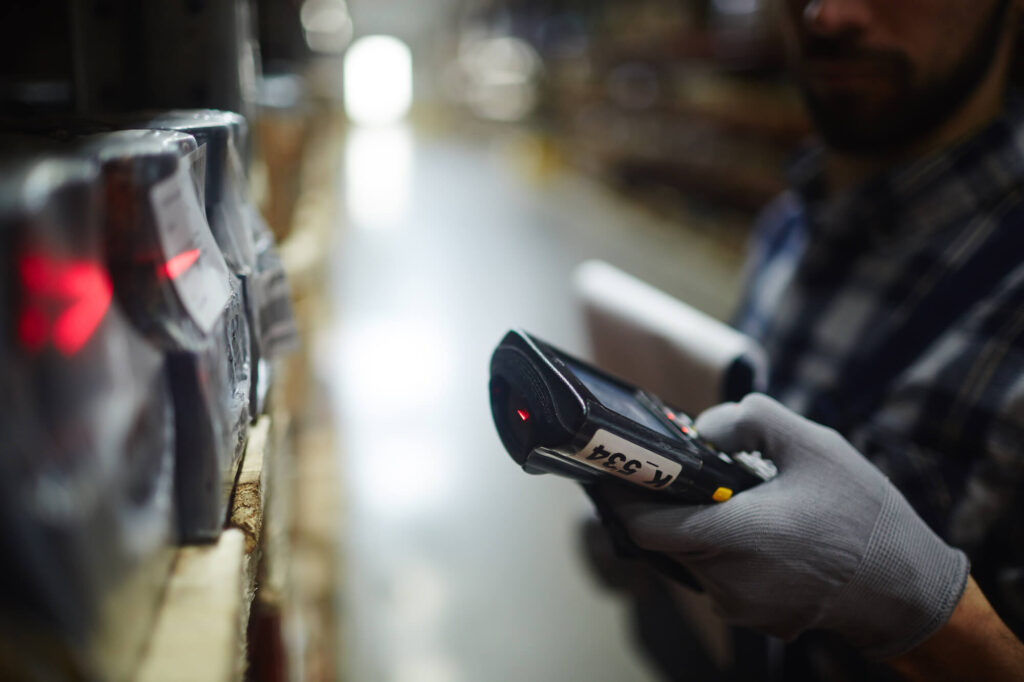
12. Sustainable and Resilient Supply Chains for Greater Dependability
Technological changes in cloud capabilities, AI, and IoT allow for greater communication across inventory management networks. Decentralizing methods such as multi-warehousing reduce dependency on a particular region.
Changes like these will make more sustainable and resilient supply chain processes across industries and for individual businesses.
13. Omnichannel Customer Service for Better Communication
Customers want to know their orders’ status, and they should immediately be apprised of any issues that could cause delays. Omnichannel customer service ensures customers have the most current information that’s available.
Omnichannel customer service goes beyond communicating via whatever means customers prefer. It gives customers access to supply chain, warehouse and distribution data, so they’re truly informed.
Customers have understandably had more questions throughout the pandemic, and this is one solution many logistics services have made. It’s a change that’s here to stay.
14. Investing in Inventory Managers for Improving
All of these current trends in inventory management are bringing tremendous change, and managers have to keep up with the new technologies and methods. Because businesses have a vested interest in their managers’ skill set and knowledge, many businesses are reinvesting in their inventory managers.
Courses, certifications, seminars and on-the-job training are all ways that managers can learn practical steps in inventory management processes that will have positive results.
Improve Your Asset and Inventory Management With ToolSense
Need a software that keeps up with these new technologies and trends? ToolSense is a brand-independent asset and inventory management software solution that integrates many of these emerging trends in inventory management.
ToolSense gives you the information you need to reduce downtime, lower equipment maintenance and replacement costs, minimize labour hours, and improve order fulfilment. Leverage IoT data, QR codes, reports and more for efficient, modern inventory management. Properly managing inventory is critical to any business, and as technology advances, companies have more opportunities to leverage these insights and remain competitive.
FAQs
Emerging trends in inventory management largely focus on incorporating new technologies and mitigating supply chain disruption risks. Technologies such as cloud computing, artificial intelligence, machine learning, internet of things, and data analytics are all used to better maintain inventory levels. The most advanced methods go so far as to predict what inventory will be needed based on past demand and consumer habits. Methods such as safety stock and multi-warehousing have long been used in certain situations. More businesses are adopting these, as the Covid-19 pandemic and geopolitical situations have shown that even UK supply chains can be significantly disrupted.
Which inventory management methods work best for a business depends partly on what inventory the business has. The four types of inventory are raw materials, works-in-progress, finished goods, and maintenance, repair and operations (MRO) goods.
While there are many different types of inventory management techniques, most rely on one of the three major ones in some way. The three major techniques are just-in-time (JIT), economic order quantity (EOQ) and materials requirements planning (MRP).
The future of inventory management continues to evolve. Advancements are making systems more automated, more efficient, faster, and more connected even as they’re increasingly spread out.