What Is Overall Equipment Effectiveness?
OEE means overall equipment effectiveness and is a widely used metric in manufacturing — it measures how efficiently a factory or production line runs and the availability of the equipment concerning its capacity.
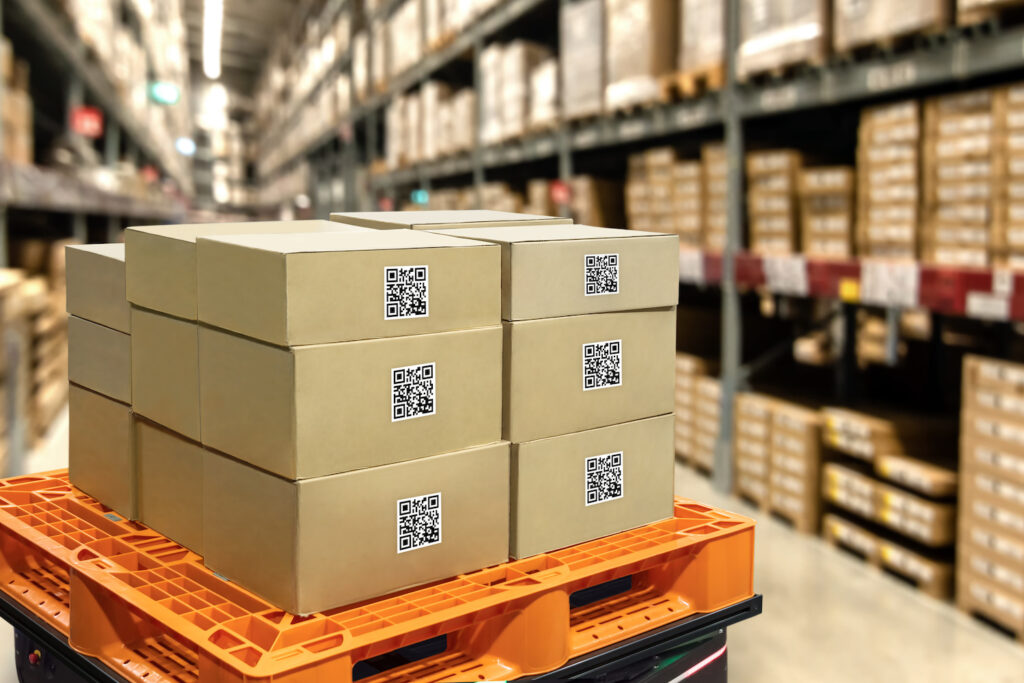
KEY TAKEAWAYS
- Overall equipment effectiveness is a measure of how well a manufacturing operation (equipment, time, and material) is being used compared to its full potential during the periods it is expected to run.
- OEE indicates the percentage of manufacturing time that is truly productive. Currently, an OEE of 85% is considered excellent.
- Overall equipment effectiveness consists of three main parts: availability, performance, and quality.
Why Is OEE Being Used?
The daily production efficiency of your plant is key to its success. This can be determined by using the overall equipment effectiveness formula. OEE takes into account the total output of a machine or department and then divides that number by the maximum possible outcome, which is calculated based on all resources available for use during a shift.
That is to say, it is used to gauge the overall performance of machines and equipment in an assembly line. Regardless of whether it’s small or large, the goal of any business should always be to maximize productivity.
ToolSense is trusted by 700+ companies
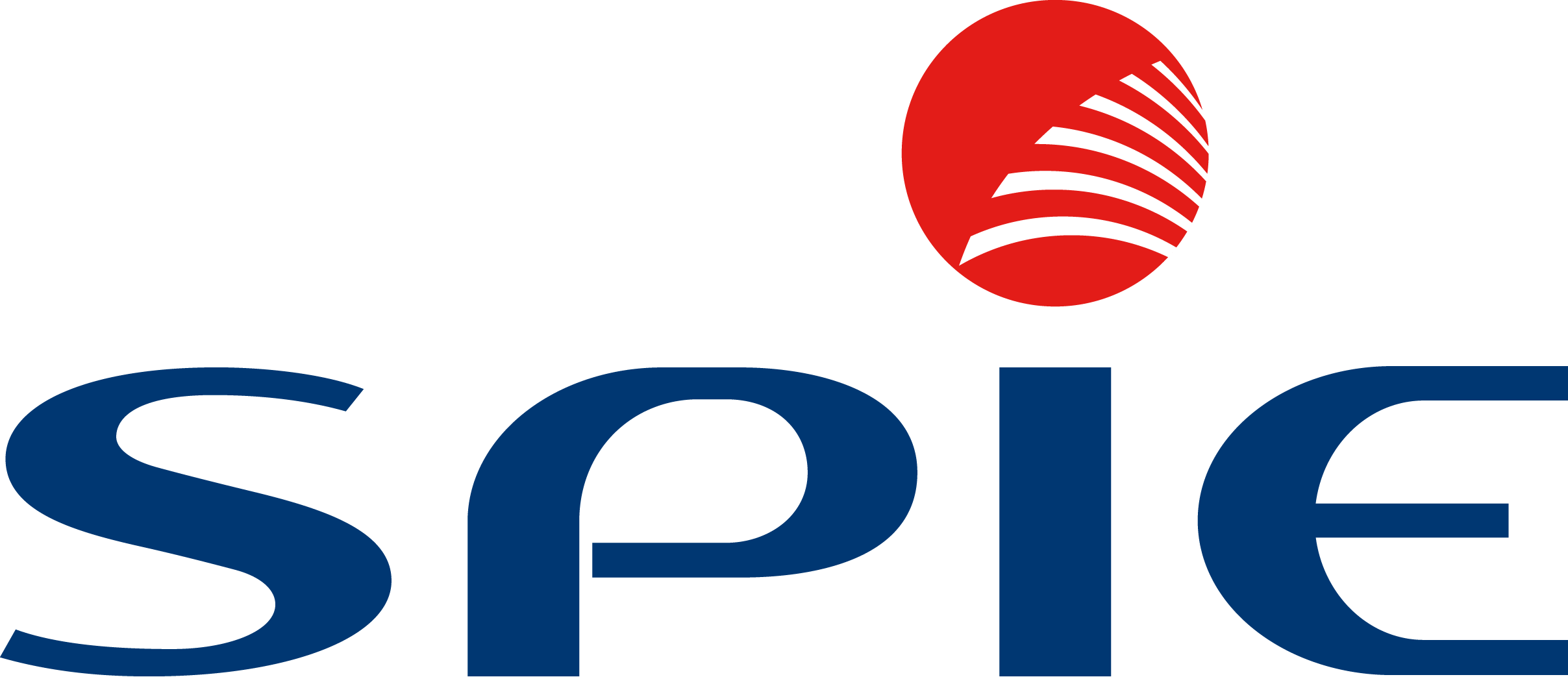
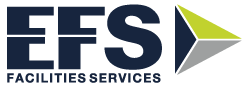
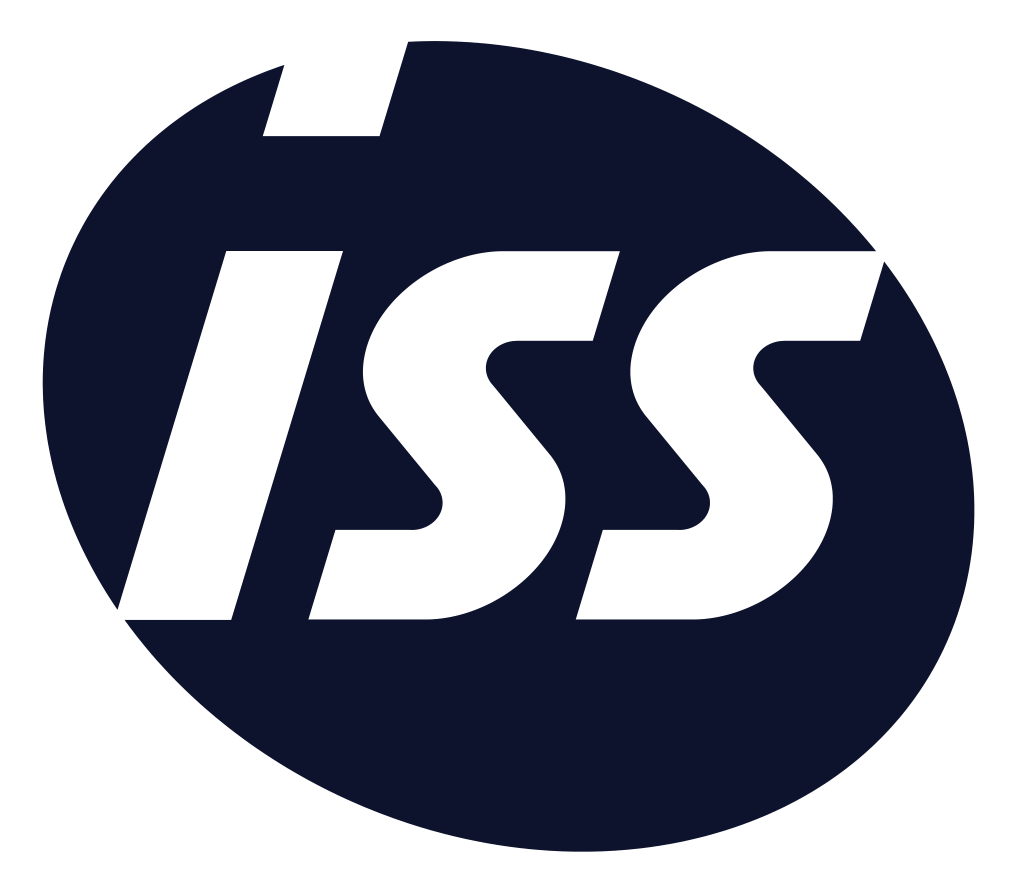
Importance of Equipment Effectiveness
OEE measures the uptime, availability, and quality of your manufacturing process. OEE is most commonly used in manufacturing but can be applied to any industry where products are manufactured.
You may have significant capacity potential in your factory that can be unlocked through OEE optimization. This will increase production and make your operation more efficient and cost-effective.
In addition, measures to improve OEE are almost always more cost-effective than the alternatives. This is especially true in the long term, but often also in the short and medium term. Alternatives include adding a new shift, purchasing new equipment, outsourcing production, increasing overtime or opening a new facility.
Currently, an OEE of 85 percent is considered very good. The fact of the matter is that many production facilities are well below this level, so significant improvements are possible.
Where Is OEE Being Used?
In manufacturing, this metric is being used in several different ways. First of all, it’s essential to recognize that OEE isn’t a new concept. It has been around for over half a century and has been used primarily in the manufacturing industry. However, OEE is only now starting to make its way into other industries such as healthcare and hospitality.
A manufacturing company has different departments like engineering, production, and quality. Each department relies on the other to ensure that the product is good and can be produced at a low cost. If any of these departments fail to do their job properly, the entire process becomes faulty and expensive. This leads to loss of time and money, and at times it even leads to rejection of goods by customers.
Components of OEE
The overall equipment effectiveness is a system that consists of three main parts: availability, performance, and quality. OEE can be used to track the performance of any process that must meet a standard level of quality while producing a product or service.
OEE is the only metric that goes beyond standard efficiency metrics like first-pass yield, scrap rate, and change over time. It is a powerful indicator of an organization’s overall effectiveness in managing its resources. If the OEE were the fuel gauge on your car, it would tell you how much gas you had, where you were going, and how many miles until empty.
Availability
Availability is one of the key performance indicators in production management. However, its exact definition has not been agreed upon by all experts. It is typically defined as when a product or service is available for use or sale to customers. Availability of a product may be described as the period between its delivery to the customer and recovery back through repair or recovery through scrapping.
Performance
Do you know that the performance in OEE is directly linked to the quality of business? Hiring a professional company to perform an audit can be very useful, as they will provide recommendations for improving the performance.
As part of the audit process, you’ll need to look at how your organization measures and tracks OEE and productivity metrics. The measurements should track how many parts are produced each day and measure your ability to produce those parts with zero defects.
Quality
We often talk about the three pillars of lean manufacturing: quality, delivery, and cost. This is because, without any one of these, the whole structure would be compromised. Quality is integral to all aspects of our business; it has to be right the first time, or there can be no further progress.
In the manufacturing industry, quality is not of secondary importance. If a product fails, you will lose your customer’s trust and reputation — for good. Your business depends on your customers to buy your products or services. Although some companies can recover from one failure, this example shows why it is very important to focus on quality improvement in every process throughout the whole company.
See How ISS Improved Their Asset and Maintenance Processes With ToolSense
The Six Largest Equipment-Based Losses
The largest equipment-based losses in manufacturing include equipment failure, setup and adjustments, idling and minor stops, reduced speed, process defects, and Reduced yield.
Availability Loss
- Equipment Breakdown: Whenever a piece of equipment is temporarily shut down owing to a fault, it is referred to as an equipment breakdown.
- Setup and Adjustments: To make a product accurately and efficiently, a machine must be adjusted.
Performance Loss
- Minor Stoppage: A minor stoppage is a temporary interruption in the manufacturing line.
- Reduced Speed: Slower cycle times indicate that a machine is not operating at its maximum pace.
Quality Loss
- Start-up Scrap: The notion that fresh components produced by a machine do not meet production requirements.
- Product Scrap: Later in the production process, defects, and rejections occur, rendering equipment or goods unacceptable.
How Is OEE Being Calculated?
OEE calculation relies on three determinants; they are the availability of a machine, its productivity, and the quality of the output product. The factors, which are availability, performance, and lastly quality, are all multiplied to get the OEE metric.
OEE = availability x performance x quality
Availability = run time / planned production time
Run Time = scheduled production time – stop time
Stop time refers to all-time when the manufacturing process was supposed to be operating but wasn’t due to unplanned or planned stops; they can either be breakdowns, maintenance, or changeovers.
Performance = (ideal cycle time x total count) / run time
Small stops and the slow cycles are two examples of industrial processes that operate at below the highest speed.
Ideal cycle time is the shortest cycle time that an operation can achieve under optimal conditions. As a consequence, when you multiply it by total count, you get net run time, which is referred to as the quickest feasible time for the items to be manufactured.
Quality = good count / total count
Quality in OEE is the concept of ensuring that every process within a manufacturing plant is executed properly. When quality is added to OEE it will increase production, improve quality and reduce costs. It starts with the basic premise of identifying customer needs by having an effective dialogue with all stakeholders involved in the manufacturing process.
Example
An example of OEE calculation is to calculate the number of hours that each machine takes to produce a part. If you have 10 machines and 5 out of those 10 took 1 hour each to complete their tasks, then it will take 5 hours for all the machines together.
How to Improve the OEE Rating?
Operating efficiency is one of the key success factors for any company. That’s why it’s important to understand what your current OEE rating is.
Overall equipment effectiveness measures how efficiently an organization uses its resources. With a high OEE, you’ll produce more while spending less time and energy on maintenance costs. A good production system is one that has high levels of overall efficiency.
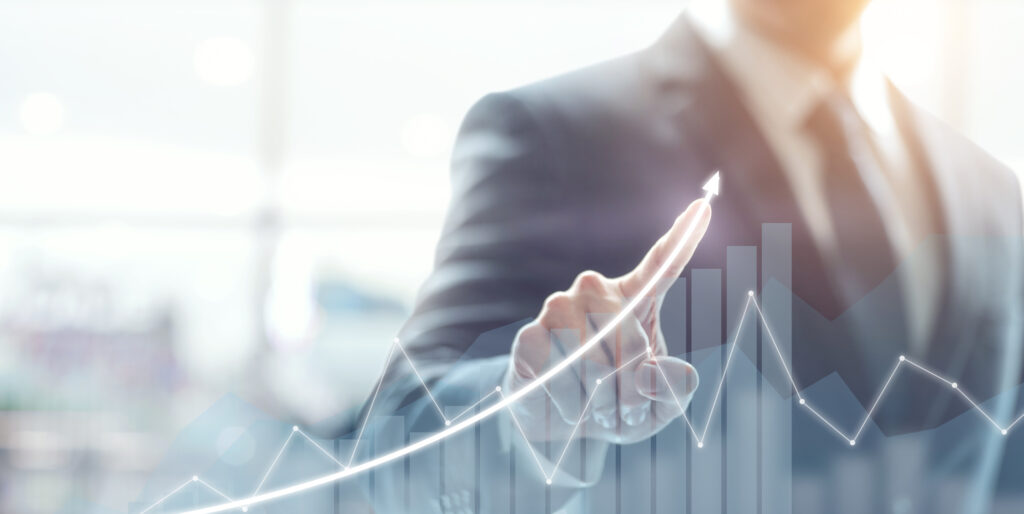
OEE Benchmarks
- 100% OEE is very good production: This means, manufacturing only good parts, as fast as possible, with no stop time.
- 85% OEE is considered good for manufacturers. For many companies, it is a suitable long-term goal.
- 60% OEE is fairly typical for discrete manufacturers, but indicates there is substantial room for improvement.
- 40% OEE and under is not uncommon for manufacturing companies. It is a low score and in most cases can be easily improved through straightforward measures.
ISS Austria
„We wanted to have a solution that does not only track expensive assets but also cheap ones. In Austria, ISS operates over 6,500 cleaning machines alone, without even counting vacuum cleaners and other pieces of equipment. With ToolSense we bring them together on a single platform, leveraging data from IoT hardware and improving maintenance and inspection processes.“
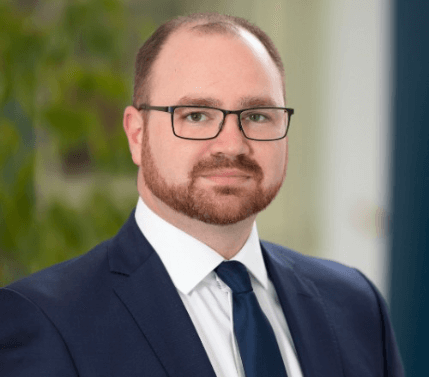
Benefits of OEE
By using OEE, businesses can ensure they are running at maximum efficiency and effectively managing costs associated with production. Understanding what OEE means and how it can be applied will help small business owners closely monitor their operating metrics.
The biggest advantage of OEE is that it does not require any additional equipment as the measurement systems are directly integrated into the production process. In addition, it facilitates preventive maintenance work through the early detection of problems. Finally, the improvement potential of OEE is much higher than that of other performance indicators.
1. Great Returns on Investment
Companies spend a lot of money on machinery and want to get the best return on their investment (ROI) in the shortest amount of time. The goal of OEE is to maximize the productivity of these processes, and the OEE return on investment has been high since its inception. Furthermore, the remuneration is quick.
2. Competitive Advantage
Reduced manufacturing losses and increased competitiveness are critical. For example, if a production line can generate 100 pieces per hour but only produces 60. In that case, the OEE might assist the organization in boosting its competitiveness by indicating why the line is failing.
3. Maximize Machine Capability
One of the most significant advantages of employing an OEE system is that machine performance improves immediately after adoption. Its use is ideal for getting the most out of new production line equipment, as well as incorporating it into existing machines.
4. Enhanced Process Quality
Defective product expenses are one of the most significant sources of financial loss for businesses worldwide. Businesses can acquire more effective traceability systems by integrating OEE with technology, which helps to discover the source of quality deterioration. Minimize duplication and poor items, and you’ll save a lot of money.
5. Scalability
You can begin utilizing an OEE system on a single process and gradually increase its use until it is used across several manufacturing facilities. Because of its scalability, becomes a highly adaptable system that can be tailored to any firm, regardless of its size.
Conclusion: How ToolSense Improves Your Maintenance Management
Overall equipment effectiveness (OEE) is a vital concept in the modern manufacturing environment. It allows you to determine the efficiency of each part of your production process and identify problems that may arise. Moreover, it also lets you plan maintenance activities and keep costs down by planning for machine failures and potential downtime.
FAQ
OEE can be used to identify potential problems before they occur to deal with any issues quickly. OEE ensures that your production line keeps running smoothly at all times. A good OEE Benchmark is 85%.
OEE can be improved by using electric actuators. Also, using electric actuators instead of hydraulic or pneumatic actuators is another technique to enhance OEE. Machine vision can be used to identify problems, take preventive measures and lastly, perform OEE calculations regularly.
OEE, or overall equipment effectiveness, is one of the most important metrics in any manufacturing facility. It can be calculated using several different methods, but they all boil down to the same thing: how much time your equipment spends making product and how much time it spends sitting idle. This metric has a direct impact on your profits because you’re paying for that downtime — whether it’s equipment repair costs or lost production.
TPM, or total productive maintenance, is an effective, proactive approach to preventative maintenance using the concepts of JIT (just-in-time), JSS (just-in-sequence), 5S, TQC (total quality control), and QIS (quality improvement system). Based on the premise that if equipment can be maintained in a condition where it will not malfunction.