Imagine standing on the edge of a skyscraper, your heart racing. You’re safe, but only because of the slender harness wrapped around you. How often do we pause and think about the silent guardians in our lives, like the safety harnesses used by countless workers every day?
These harnesses, often unnoticed, play a crucial role in preventing falls from heights, saving lives and livelihoods. But what ensures these harnesses remain reliable? Regular inspections and proper usage are key. Let’s dive into the world of safety harness and lanyard inspection, unraveling their significance and the life-saving protocols behind them.
Harness and Lanyard Inspection: How to Inspect and Wear a Harness Correctly
A safety harness is a vital component for many workers in different industries, where they may be at risk of falling or losing balance when working at heights above ground. Primarily, a safety harness is used to avoid critical injury, but can also be a prerequisite for commercial insurance. Some insurers will ask to see relevant certification. A functioning safety harness can become a vital lifeline in the event of an accident, but any failure could result in life-changing injuries or even death. Regular safety harness inspection is an essential routine that can save lives.
Key Takeaways
- All fall protection equipment should be inspected regularly, with a detailed inspection at least every twelve months.
- Safety harness inspections can be completed by individuals deemed competent and could include external providers or trained and certified staff.
- Any safety equipment that fails an inspection should be discarded and replaced immediately.
We did the research for you and compiled a list of the best 15 equipment management software solutions.
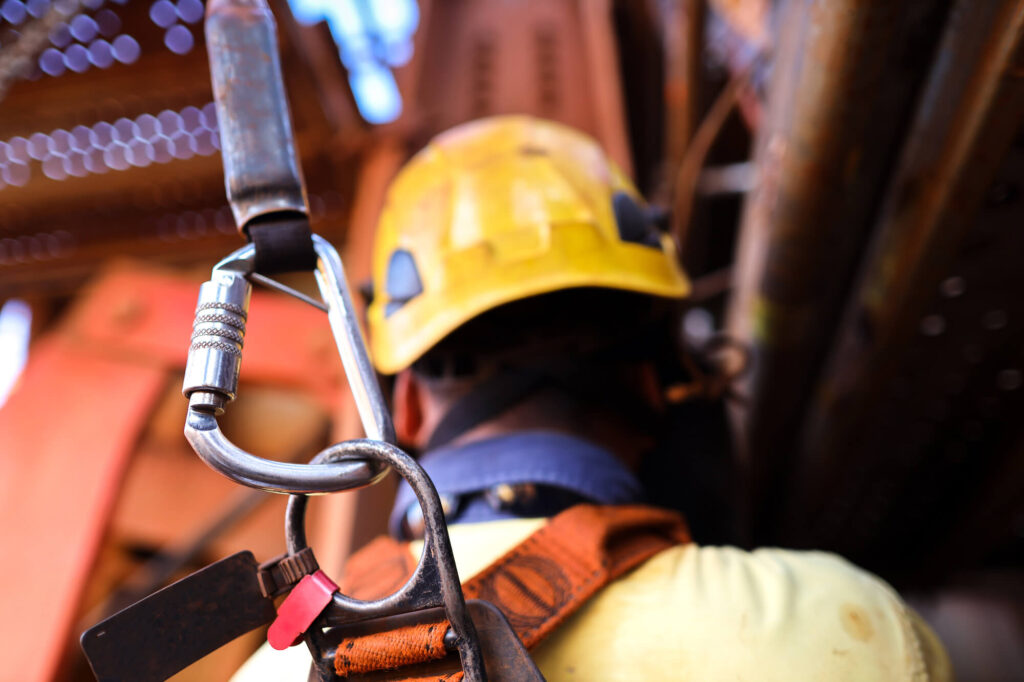
What Is a Safety Harness?
In short, a safety harness is a system of straps or full body harness worn by a person at risk of a potential fall. The safety harness needs to be attached to an immovable object that can support a person’s weight should they lose their balance. In addition, the harness must be strong enough to sustain the additional force generated by the fall without harming the wearer.
ToolSense is trusted by 700+ companies
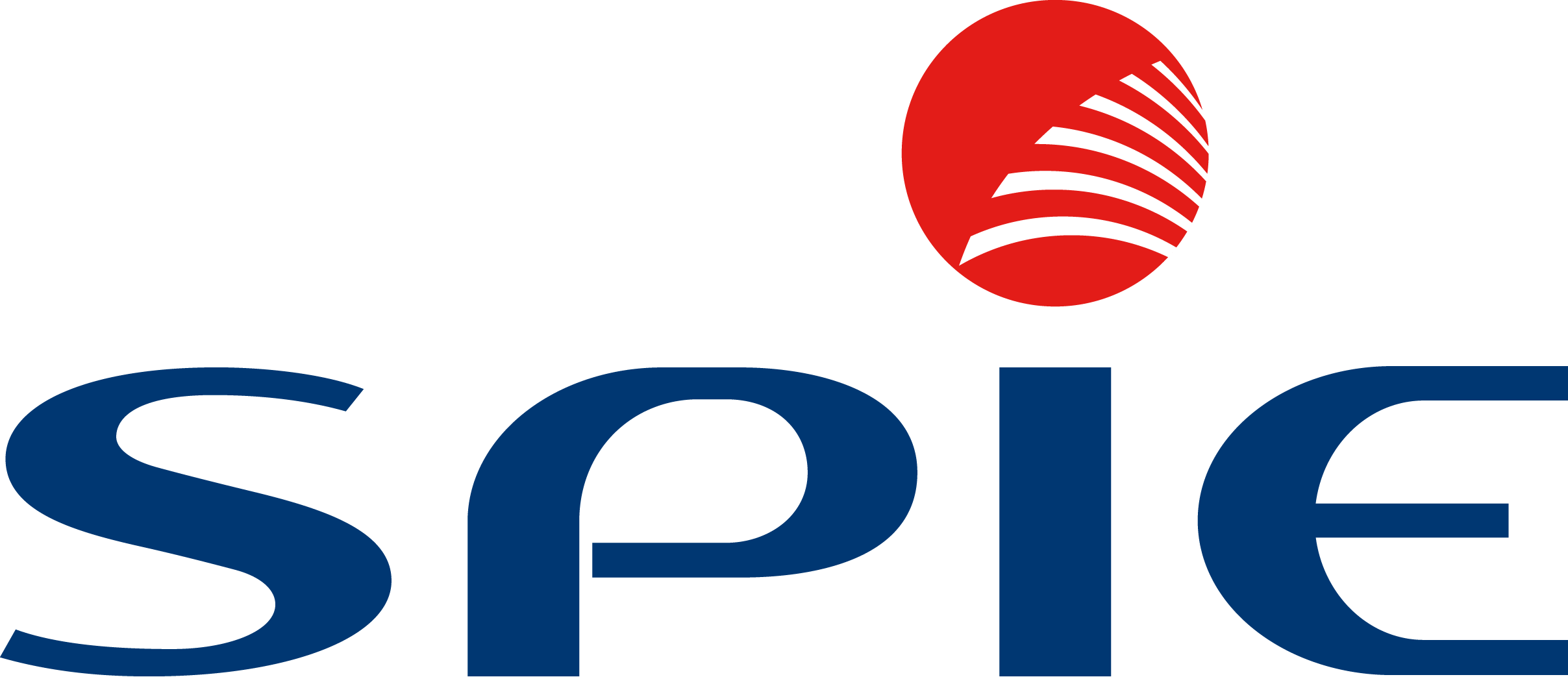
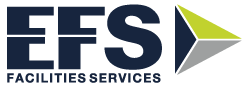
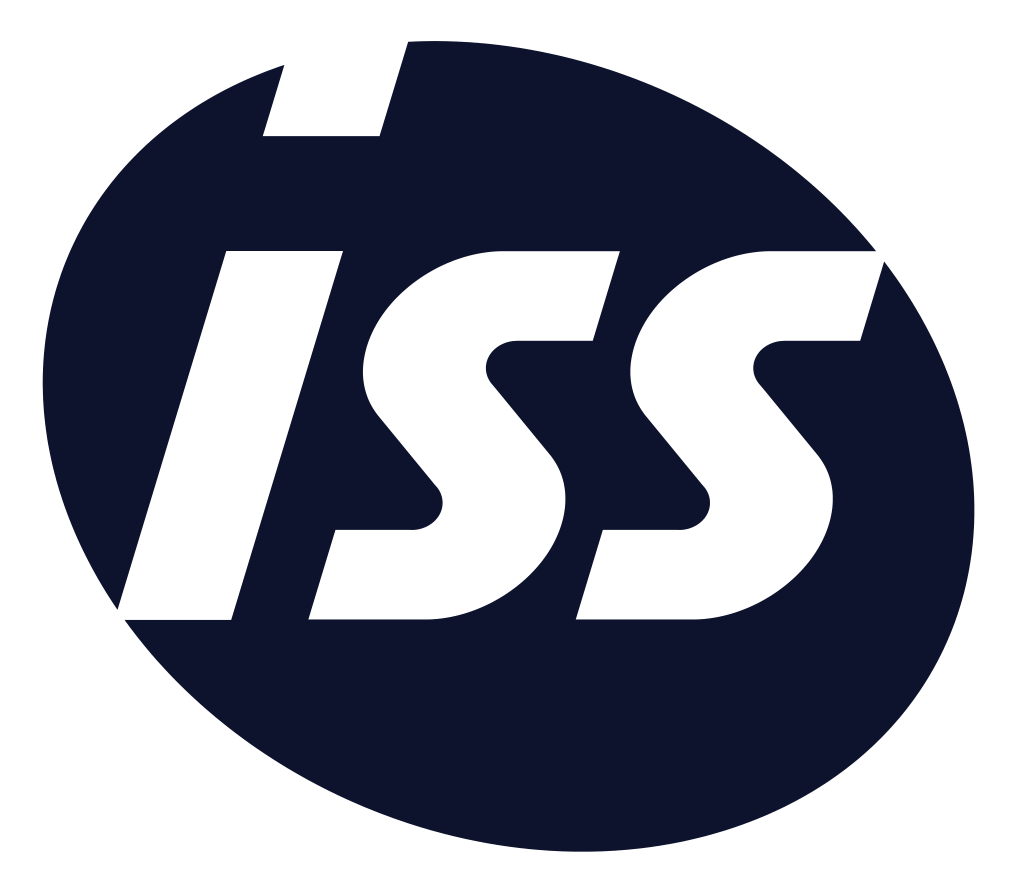
Fall Arrest Components
A fall arrest system includes three main parts:
- Achor point
- Lanyard
- Safety harness
What Is a Lanyard?
Importantly, when securing a safety harness to an immovable object for support, the strap that attaches the two is called a lanyard. Clearly, this lanyard will need to hold the weight of the person wearing the safety harness and will also need to withstand the force of the fall and any jerking action or additional pressure this will cause.
Restraint and Fall Arrest Lanyard
There are two different kinds of lanyards. Firstly, a lanyard can be used to stop the wearer from climbing above a certain height by restricting the length of the strap. This type of lanyard is often called a restraint lanyard. For example, it could be particularly useful for someone working on a platform at height if the length of the lanyard makes it impossible for them to step over the edge.
Alternatively, the second type is called a fall arrest lanyard. It is mostly used when a fall is likely. This lanyard needs to be strong enough to sustain the force of the fall and reduce the force of the impact on the person’s body without causing injuries. It also needs to minimize the impact on the anchor point to avoid damage.
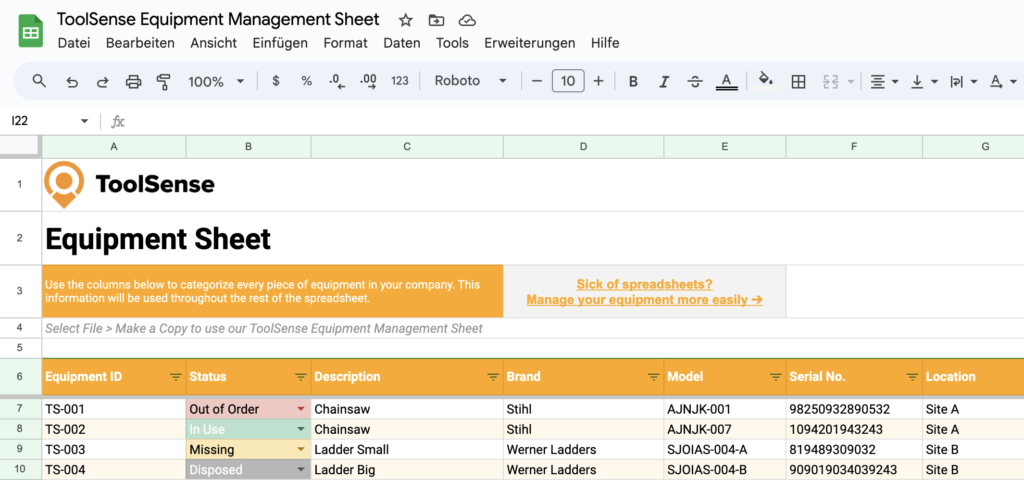
Importance of Safety Harness
Fall arrest harnesses are an important component of personal fall protection systems. This is because they keep your body suspended in the event of a fall. As the person in charge, you should make sure that everyone wears a fall arrest harness. They are the best tool because they distribute any kind of force evenly across the body, minimizing the risk of injury.
Safety Harness Components
In general, a safety harness includes important straps that fit around a person’s shoulders, legs, and chest area. In most examples, these straps are connected with a central panel that sits on the back, which also holds the dorsal D ring. There are also usually D rings on both the right and left straps. It is vital that the safety harness fits snugly to reduce the impact of the fall. Therefore, each strap has an adjustable buckle, with a chest buckle used to secure the wearer firmly into the harness. Next, the dorsal D ring is connected to the lanyard using a strong snap hook. In addition, the lanyard will include a shock absorber that will reduce the force of the impact of the fall.
In many cases, the lanyard is then secured to an anchor point using a D ring or snap hook. However, in some examples, the lanyard may be secured to another strap or rope sometimes called a lifeline. This approach will be used when the wearer needs to move around further than the length of the lanyard will allow. Next, the lanyard is connected to the lifeline using a D ring and a rope grab.
Key Terms in a Safety Inspection Checklist
Webbing | Most harnesses are made from webbing straps. These should be inspected for fraying or cuts, badly pulled webbing, loose stitching, as well as UV damage. |
Buckles | Buckles connect the straps. They can be rigid plastic or metal. They need to be checked for wear and tear. |
D-Rings | D rings attach the lanyard to the safety harness. There may be several D rings, some of which can be used to attach tools or accessories. These need to be checked to make sure their shape has not distorted and there are no visible cracks, sharp edges, or rust. |
Plastic Loops | Loops are used to hold excess strap or rope and ensure the harness is snug and streamlined. Again, these plastic loops need to be checked for distortion or breakages. |
Straps and Rope | The harness tends to be made of straps, often made of webbing material. A lanyard can be either rope or webbing, depending on preference and the type of job. |
Label | The label contains important written information, including the date of last inspection and life expectancy of the safety harness or lanyard. |
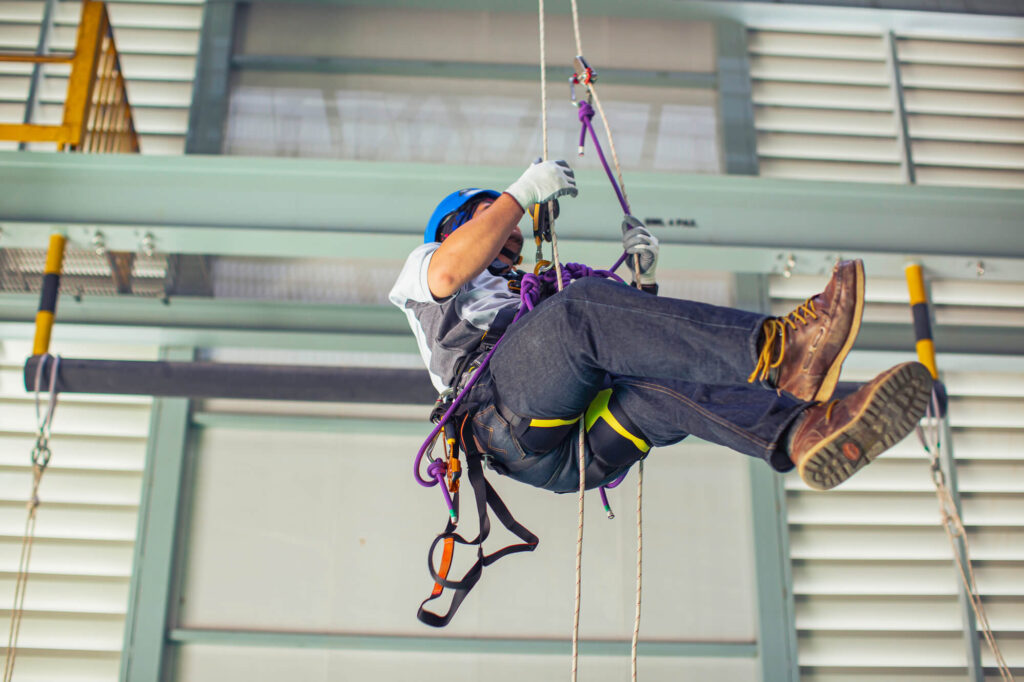
Safety Harness Inspection Requirements
All the safety harness components must be regularly inspected by a competent person. In short, this is someone fully trained and often authorized by the manufacturer of the harness, usually after undertaking safety harness training offered or approved by the manufacturer or external provider. Anyone inspecting a harness will also need to be fully insured, typically with appropriate public liability and a professional indemnity policy.
However, it is good practice for all staff to inspect safety harnesses routinely in addition to formal inspections. This pre-use inspection may be undertaken by an external provider rather than a business owner or employee.
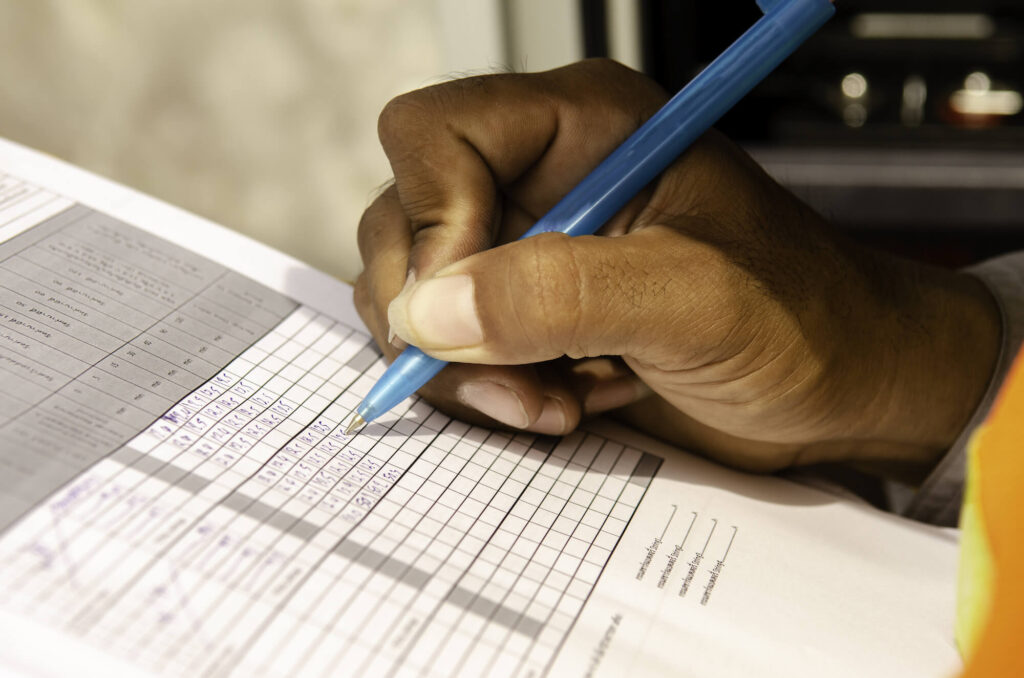
Safety Harness Checklist UK: Fall Protection Inspection
The elements of a safety harness checklist in the UK remain much the same, although harnesses can vary slightly in style. The fall protection inspection should be performed as followed:
- First, examine the label to check the individual serial number and find the date of the last formal inspection. If this date is outside the agreement interval period, do not use the harness until it is fully checked. Most harnesses also carry a life expectancy, after which they are not considered safe to use. Therefore, you will also need to check the manufacturer date and the length of time the harness has left.
- Next, check the hardware, starting with the rear D ring. Signs of wear or fatigue include a change of shape or distortion, cracking, rust, or nicks and burrs. If there is any sign of excessive wear, the harness should not be used. Make sure the ring pivots freely.
- To continue, check the remainder of the harness looking for damage, cracks or discolouration. This should include checking the backplate and any fastenings, buckles, adjusters, and connectors.
- Check webbing: Once you have checked the hardware, you need to move on to the software. This will include the webbing straps and the general shape of the harness. Buckle up the harness evenly and hold it up to view: it should hang evenly. The webbing must be free of tears, cuts, fraying or excessive abrasion; loose seams or fading may also mean that the fibre structure is compromised.
- Next, check the straps for any damage or distortion, especially UV, chemical damage or if the harness appears brittle. For example, checking the colour is a good indicator of whether or not a harness has been affected by too much sun. In addition, the texture of the webbing straps can also reveal if they have been damaged by chemicals as they become hard or brittle.
- Finally, check each strap for signs of fraying or broken fibres. It is crucial that the fibre structure has not been compromised.
Safety Harness Inspection Checklist / Safety Harness Inspection Register Template
How to Wear a Safety Harness Correctly
Because a safety harness is the last defence that might protect someone’s life should they fall, wearing the harness correctly is vital. The harness connects the user to the lanyard and the anchor, therefore should the harness fail the entire fall prevention system will be useless. For that reason, fitting the harness correctly is of vital importance.
- Holding by the back panel D ring, give the harness a thorough shake to allow the straps to fall into place.
- Secondly, undo all the buckles and release straps.
- Put the correct straps over your shoulders and adjust so that the back panel and D ring are positioned exactly over the middle section of your back. Should you fall, this will be the highest point supporting your body and your weight will need to be distributed evenly to avoid serious injury. Connect all buckles and ensure harness is not distorted and hangs correctly.
- Fasten the leg straps using the correct approach for the type of buckle on your harness. Make sure the leg straps are tight enough so that you can squeeze no more than a hand between your leg and the strap. Inspect clips on straps and check for loose stitching.
- Connect the waist strap, if there is one.
- Next, connect the chest strap and adjust to make sure it keeps the shoulder straps taut and rests evenly in the middle of your chest.
- Check every strap and make necessary adjustments, so it feels tight enough and even throughout.
- Should there be any overhanging straps, be sure to secure them out of the way using loop keepers. Look out for cracked, damaged or broken loops.
Wearing the wrong type of harness or putting the harness on incorrectly can result in serious injury or even death in the event of a fall. In short, ensuring the harness is worn correctly is just as important as inspecting the harness regularly.
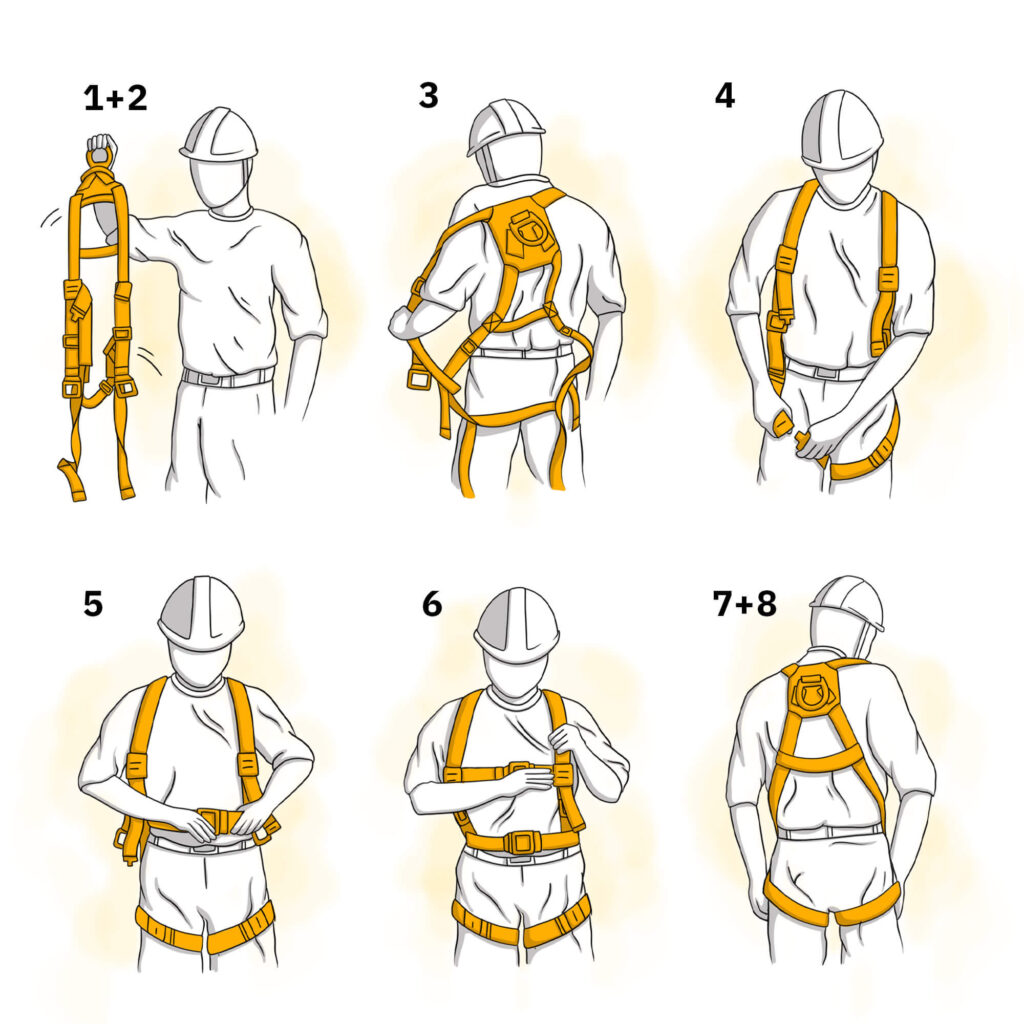
How Often Should Testing Take Place?
Safety harness inspection frequency can differ depending on how often the equipment is used. British safety standards also stipulate that this should be at least every twelve months, although it is recommended that testing happens more frequently.
Testing can be divided into different types including pre-use checks, detailed inspections and interim checks. For example, pre-use checks should be part of the routine each time the equipment is used in between safety harness inspection intervals. Ideally, all users would carry out these checks. Thorough detailed inspections by a designated person should take place every six to twelve months, or more often if the equipment is in heavy use, with detailed periodic inspections and interim checks in between.
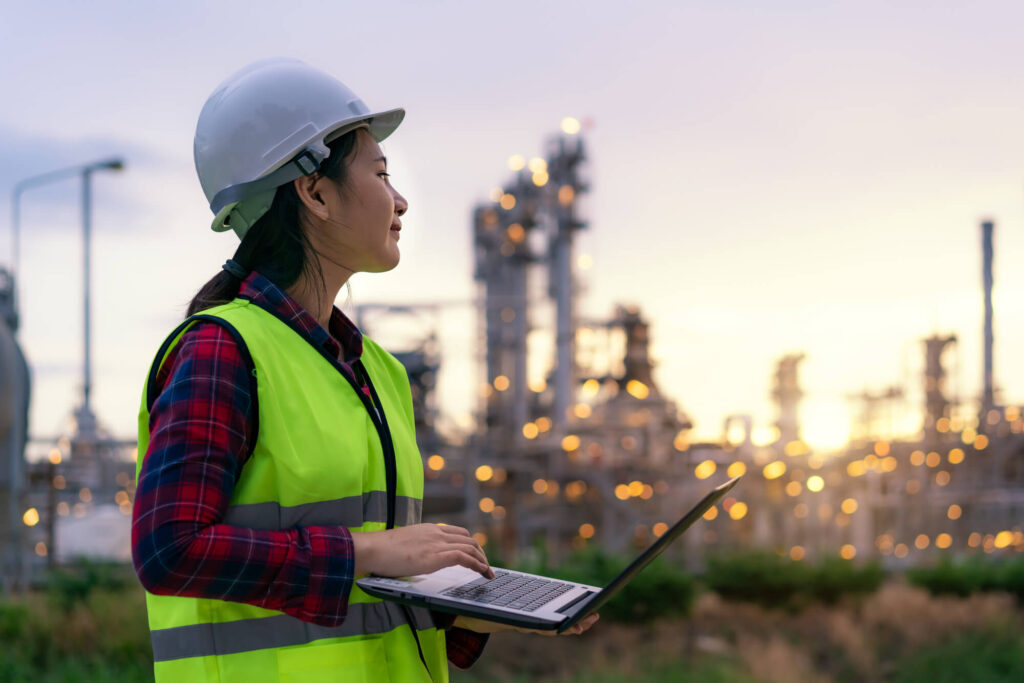
Who Can Inspect a Safety Harness?
The personal protective equipment at work regulations and work at height regulations state that it is the responsibility of the employer to ensure safety equipment is kept in good condition and regularly tested. As mentioned above, a detailed inspection needs to be carried out by someone identified as competent, although this doesn’t always mean they have to be externally employed.
On the other hand, it is recommended that the inspector is independent, so the decisions they make are based on the equipment alone. For example, an inspector may need to decide that faulty lanyards or harnesses should be discarded, which could mean delayed work while spares are found.
Pre-use checks should be carried out by all staff every time the safety equipment is used. This will include checking all straps for fraying and ensuring all buckles and rings are free from distortion. Interim inspections could also be undertaken by designated employees as often as deemed necessary. Safety harness inspection checklist templates and harness inspection guidelines are available to support staff undertaking inspections at all levels.
Ideally, all users and managers should be trained in harness selection, inspection, and use of fall arrest harnesses. They should know exactly how to ensure the equipment is appropriate and safe. Many external providers also offer height courses and detailed safety equipment inspections and can provide a valid safety harness inspection certificate. These will vary in price depending on the amount and the type of equipment requiring testing.
See How ISS Improved Their Asset Processes With ToolSense
Safety Harness Inspections With ToolSense
To get regular reminders about inspections and not lose track of time, it’s best to use equipment management software like ToolSense offers. Staying ahead of the requirements and quality control for safety inspections without proper tools takes plenty of time and effort. Flexible rules, pre-configured and custom inspections and powerful automations ensure a flawless operation of your assets and reduce costs.
In the ToolSense equipment inspection software, we have all kinds of safety inspections—like ladder checks, LOLER checks and more—pre-configured. Additionally, you can easily build your own safety inspections with our custom form editor. Our safety harness inspection software also allows you to report on equipment with impending recertification requirements to allocate inspections to engineers.
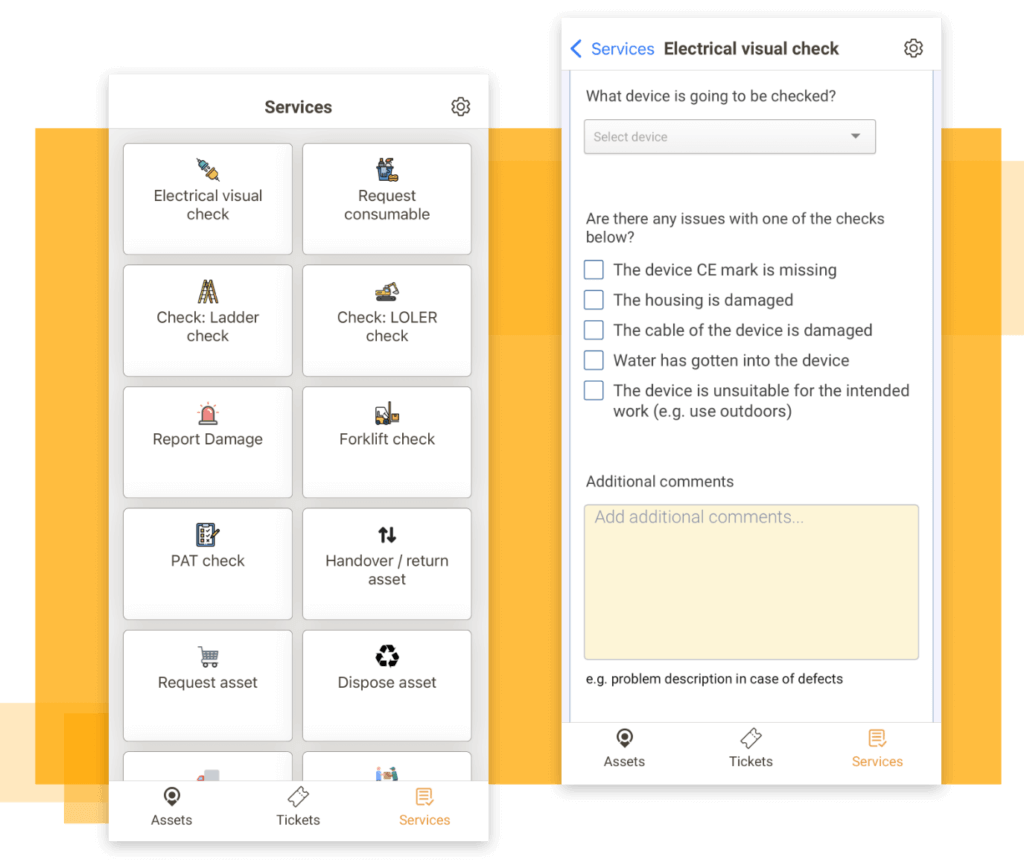
How ToolSense Improves Your Equipment Safety Inspections
FAQ
Yes. British safety standards require that fall arrest systems are certified by a competent person at least every twelve months.
There are many external companies available who can inspect and certify safety equipment including lanyards, and designated employees can also complete these checks provided they have received sufficient safety harness training and certification.
All equipment that fails a safety test should be discarded and replaced.
A thorough, detailed inspection should take place at least once every twelve months, but more often if the equipment is used regularly. Pre-use checks should be undertaken every time the equipment is used.