Maintenance costs are a necessary part of every production facility’s budget. Moreover, they’re often one of the more difficult budget expenses to control. Bringing certainty to maintenance costs enables facilities to responsibly manage both these costs and the equipment that must be maintained.
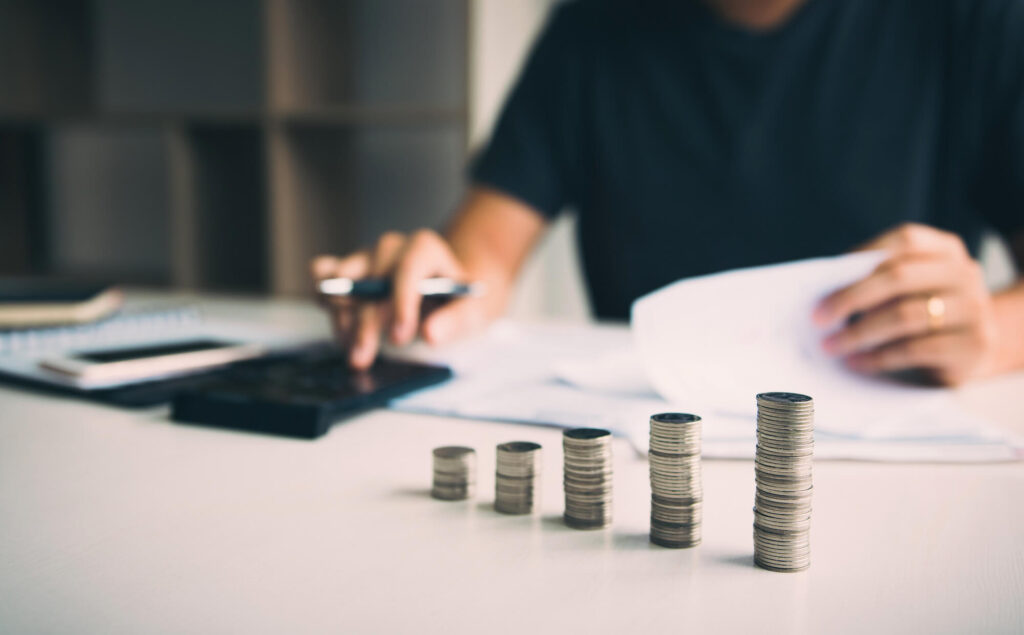
Key Takeaways
- Maintenance costs represent all expenses resulting from your efforts to keep property, plant and equipment in optimal operating condition.
- Reducing maintenance costs is not the primary goal. Reducing expenses will improve profitability to some degree, but the improvement may be limited and short-lived if nothing else is considered.
- The right way to look at maintenance is like an investment. When you do maintenance, you’re not losing money, you’re investing it in your equipment.
What Expenses Are Included in Maintenance Costs?
Maintenance costs are a subset of production costs. And as such, there is a range of what facilities might list as maintenance. Some common types include:
- Lubricants and other regularly replaced supplies.
- Consumable parts that are frequently replaced.
- Consumable parts that are replaced less often but regularly.
- Labour for applying lubricants and replacing consumables.
- Maintenance debt that’s outstanding on equipment.
In many cases, production facilities have some flexibility with regard to how maintenance costs are classified. Facilities may be able to take advantage of this by listing capital expenditures as maintenance costs, and thus bringing down net profit for the period.
Of course, facilities should confirm that this accounting practice is consistent with all federal, state, and local tax regulations. Management should also be aware of the budgetary tactic, so they know why maintenance costs may be higher than expected in a given quarter or year.
ToolSense is trusted by 700+ companies
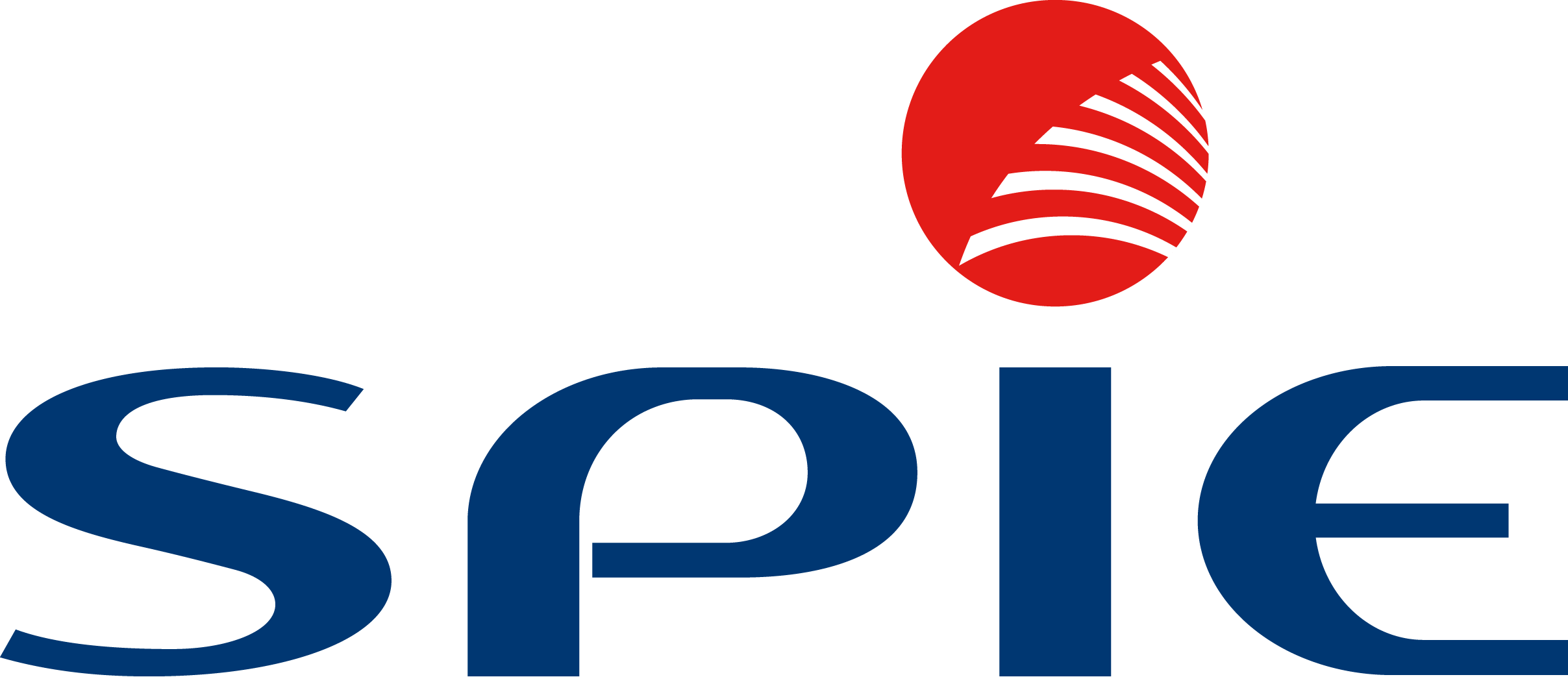
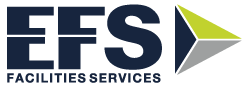
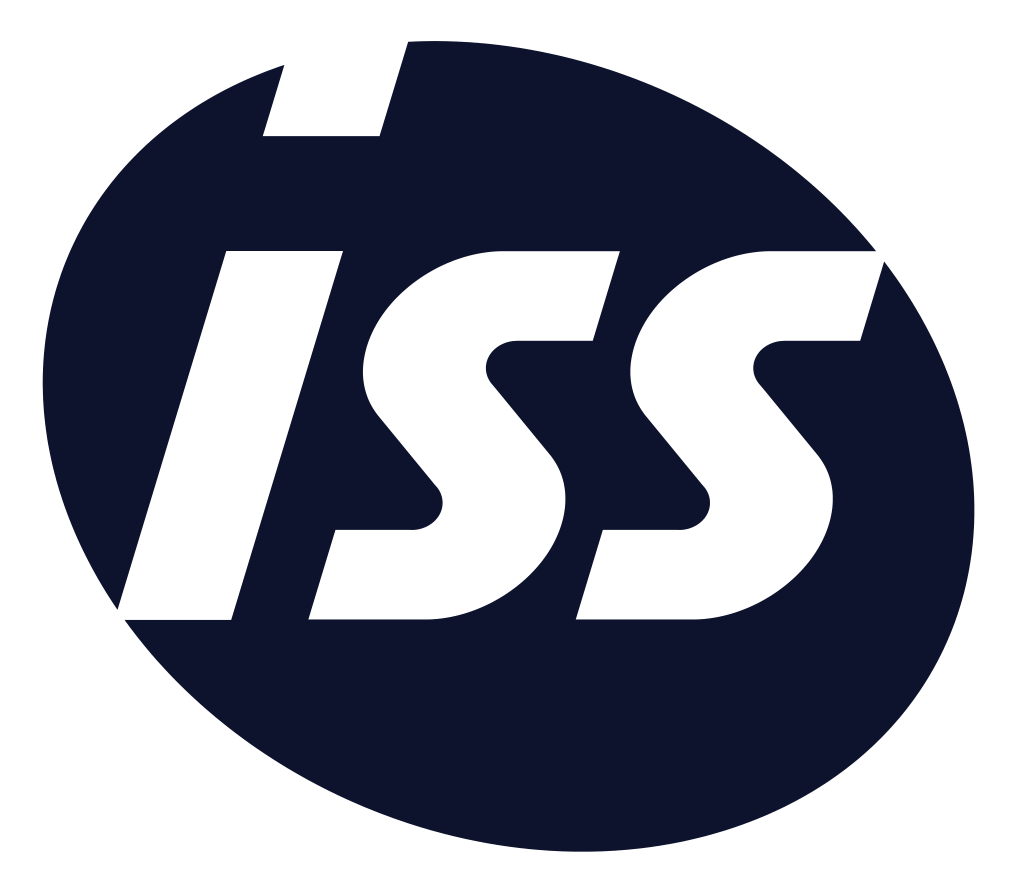
Understanding Differences in Maintenance Costs
Before any specifics about maintenance costs can be discussed, it’s first necessary to appreciate why these costs might vary. In fact, costs frequently vary across facilities and equipment. The following are a few examples of reasons why:
Build-Outs | How production facilities are initially engineered affects virtually every aspect of protection, and especially maintenance. The workflow of a production line impacts how much equipment is used, what loads the equipment bears, and many other details. |
Production Flow | Production flow itself directly influences how much equipment is used and what strain it’s placed under. While some workflows are fixed due to initial engineering, there also are sometimes ways to adjust production flow after a facility is in place. |
Equipment | Variances in the type, quality, and size of equipment largely affect how long these assets will last. Equipment that’s built reliably and used within the manner initially intended will last longer. Inferior equipment and equipment that’s adapted for non-ideal use will wear out sooner and have higher maintenance costs. This issue can be particularly common when a production facility grows or changes, and the same equipment is used afterward. |
Products Produced | The products produced determine how much strain equipment is under, and two identical pieces of equipment will require different maintenance if they handle different workloads. For instance, a conveyor belt that moves metals will wear out much faster than an identical one that carries wood shavings. |
This isn’t a comprehensive list of factors that can lead to different maintenance costs, as there are other details to consider. A maintenance specialist will be able to illustrate these and the many other details that can cause variances in costs.
Tracking Maintenance Costs
Tracking maintenance costs can be a challenge. The first step is to implement a system that accurately tracks operating costs. Once you know how these costs add up, you can begin to formulate a plan to eliminate unnecessary expenses.
Understanding the Roles of Benchmarks
Production facilities may use a variety of maintenance cost benchmarks. However, the usefulness of this data is limited when viewed without context. For example, consider how the following benchmarks could be misleading if no additional information is given.
Maintenance Cost/Unit or Maintenance Cost/Ton
One of the most common benchmarks used is maintenance cost/unit or maintenance cost/ton. This may be favoured by management because it neatly quantifies maintenance within the context of quantity produced, but even this context is limited.
Simply considering maintenance cost/unit doesn’t show what effect those maintenance costs are having on profitability. A well-maintained facility may be more profitable on a per-unit basis than a poorly maintained facility. Even if the maintenance does cost more for the former.
Quantifying maintenance cost/unit also removes the context of time. Taking into account the full benefit of one-time investments, such as in training personnel or purchasing specialized tools, is difficult when only considering the cost per unit.
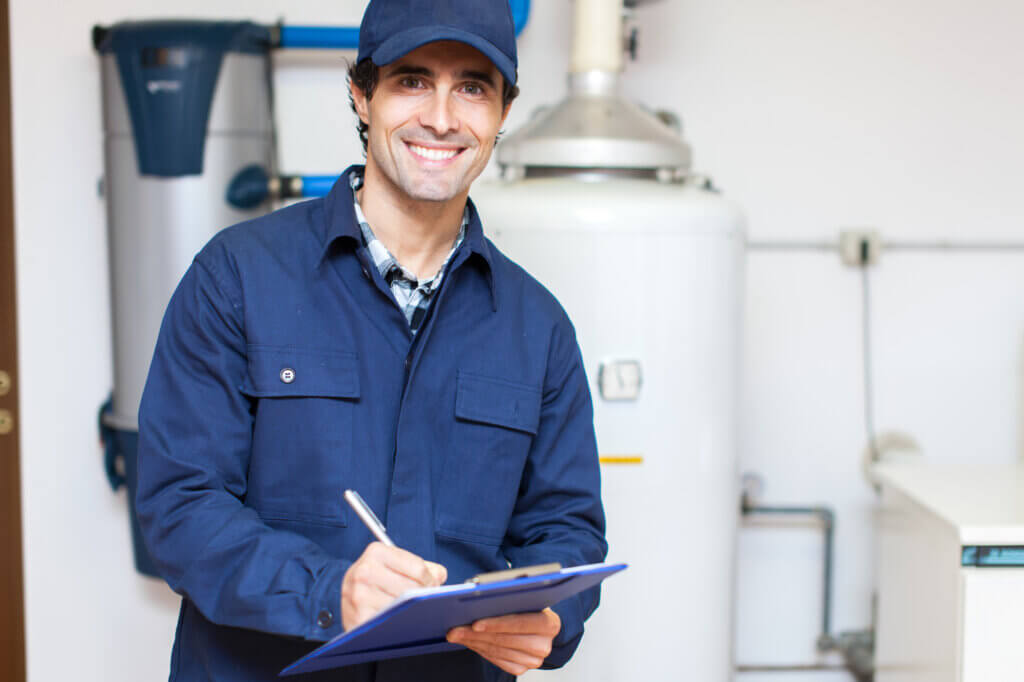
Maintenance Cost/Estimated Replacement Value
Another common benchmark is maintenance cost/estimated replacement value (ERV), with most production facilities aiming to keep this benchmark at 2%.
Placing maintenance costs within the context of replacement costs is helpful, particularly when deciding whether to repair equipment or invest in new equipment. The method doesn’t show trends in maintenance, the effectiveness of a maintenance plan or any other insightful details, however.
Additionally, the maintenance cost/estimated replacement value is often incorrect because accurately estimating ERV can be challenging. Few businesses get the cost of equipment, parts, installation, and training exactly right, and most tend to underestimate some of these expenses.
The math only becomes more complex when considering the different tax write-offs for maintenance expenses vs. capital expenditures, and which expenses can be categorized as which type.
These benchmarks may have limited use when viewed on their own, but they can be useful when placed in a broader context.
ISS Austria
„We wanted to have a solution that does not only track expensive assets but also cheap ones. In Austria, ISS operates over 6,500 cleaning machines alone, without even counting vacuum cleaners and other pieces of equipment. With ToolSense we bring them together on a single platform, leveraging data from IoT hardware and improving maintenance and inspection processes.“
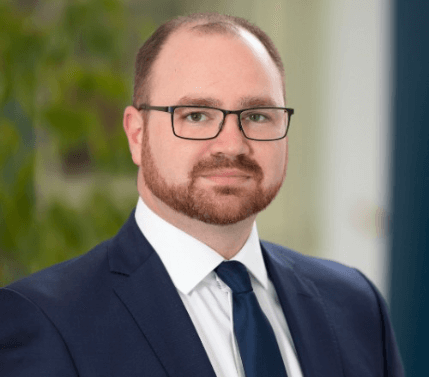
Understanding the Roles of Key Performance Indicators
Key performance indicators (KPIs) provide more granular data on how well maintenance is being managed at a facility. KPI metrics focus more on the actual maintenance data, rather than calculating the general data in light of other factors (i.e., units, tons, or ERV).
Important KPIs for Maintenance
Production facilities may benefit from tracking several different maintenance KPIs. Some of the most important are:
- Maintenance Frequency: How often equipment is being serviced, and how often specific maintenance items are being performed.
- Cost Per Maintenance: How much each maintenance service costs to perform, and the average cost per service across all equipment.
- Replacement Parts Cost: More specific data on how much various parts cost to purchase.
- Labour Costs: More specific data on how much performing preventative and corrective maintenance services cost.
Together, these KPIs show both reliability (maintenance frequency) and cost (per maintenance, replacement parts, labour). They also make it easy to identify trends and make adjustments accordingly.
For instance, an increase in maintenance frequency could indicate ageing equipment, more use or less effective maintenance services. Identifying the KPI with certainty allows the metric to act as an alert, and managers then can determine the underlying cause for the changing KPI trend.
Similarly, rising replacement cost parts could be due to increased breakdowns, increasing supply costs or expedited shipping. Comparing this with other KPIs shows with greater certainty what factors are contributing to escalating maintenance costs.
See How ISS Improved Their Asset and Maintenance Processes With ToolSense
Benchmarks and KPIs Taken Together
When taken together, benchmarks and KPIs become especially powerful tools for managing maintenance costs with certainty. The KPIs provide specific data on maintenance itself, and the benchmarks can add some broader context with regard to production and asset value.
Of course, even broader contexts of overall expenses and profitability should also be considered. Having the benchmarks and KPIs both known is a prerequisite to the full understanding of maintenance, its costs and its roles within a facility.
Reducing Maintenance Costs Isn’t the Goal
A fuller appreciation for maintenance costs in context reveals that reducing maintenance costs isn’t the ultimate goal. While lowering these expenses will improve profitability to an extent, the improvement can be limited and short-lived if nothing else is taken into account.
As an example, consider the extreme of eliminating maintenance costs altogether. A production facility that ceased all maintenance would see expenses decrease and profits increase, perhaps substantially. This benefit would be short, however, as equipment would soon break down and repairs would be needed.
Stopping maintenance entirely is an extreme example, but it illustrates the hidden risks that facilities assume (and often overlook) when skipping routine maintenance services. First, the cost of a repair is almost always higher than the cost of preventative maintenance. Second, the unexpected repair will force production to slow or stop temporarily. These two costs can be neglected until a repair is needed, but then they become much more serious than the maintenance would’ve been.
Managing maintenance across an entire fleet is quite a challenge. Build custom workflows in our Asset Operations Platform to easily manage maintenance processes for thousands of assets.
Hidden Maintenance Cost Formula
A simple formula properly accounts for these two hidden costs:
Hidden Maintenance Cost = (Cost of Repair + Lost Production Cost) x Probability of Breakdown
This should be calculated for an accurate comparison of the costs associated with performing and skipping maintenance services.
Managing Maintenance Costs Is the Goal
The ultimate goal of clarifying maintenance costs should be to manage the expenses wisely.
Maintenance costs should be included in the budget and kept reasonable, but they shouldn’t be reduced at the expense of equipment value or function. The purpose of maintenance is to keep equipment running, after all. That purpose ought to be prioritized.
How to Manage Maintenance Costs Well
Properly managing maintenance costs requires understanding and appreciation, but it’s fairly straightforward to do once a facility is committed to this goal. Some basic steps will ensure maintenance is managed well:
- Prevention: Perform preventative maintenance as scheduled.
- Inspection: Inspect maintenance regularly for wear.
- Plan: Develop a corrective maintenance plan when inspections show extensive wear.
- Schedule: Schedule the necessary corrective maintenance, and make workflow adjustments.
- Perform: Perform the corrective maintenance as planned and scheduled.
- Monitor: Monitor all of these steps, and look for ways to improve the facility’s maintenance.
Find out more about the different types of maintenance in our article “The 6 Types of Maintenance: Definitions, Benefits, Examples”.
Using Analytics to Manage Maintenance Costs
The last step of monitoring should be done with maintenance-specific analytics. Specialized predictive analytics programs will catalogue preventative services and inspections, and the software will be able to predict what repairs will be needed and when they’ll be needed.
Analytics software will also monitor benchmarks and KPIs, keeping managers informed of maintenance costs. With the data and assistance that maintenance analytics provides, it’s easy to bring certainty to the entire situation.
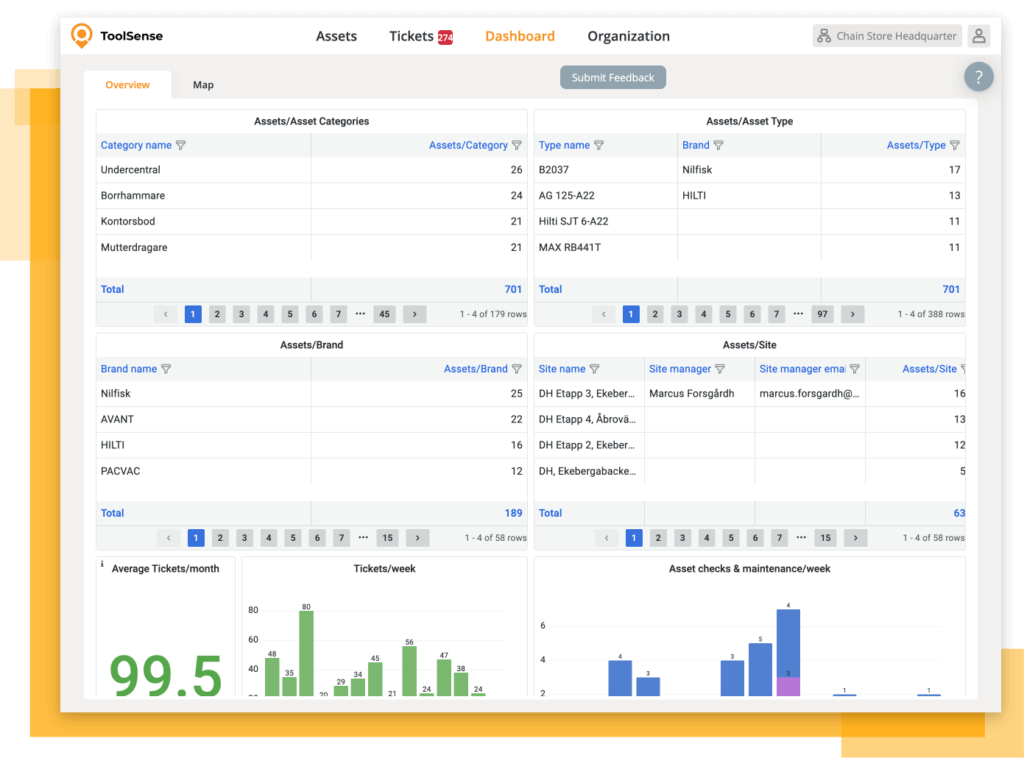
Manage Maintenance and Analytics Better With ToolSense
How much do you really know about your machines? ToolSense’s maintenance management software provides a whole new level of insight. Track locations, equipment downtime, runtime, maintenance costs and all repairs and spare part orders, every ticket and work order while keeping all important files related to your assets in one place. Our cloud-based maintenance management software creates in-depth reporting and analytics you can use to gain a better understanding of your machines and make more economic decisions in the future.
FAQ
The term maintenance cost refers to any cost incurred by an individual or business to keep their assets in good working order. These costs can be spent on general maintenance of items, such as repairing a car or machine.
Equipment maintenance costs include the expenses incurred in a facility for the maintenance and repair of equipment and components that are present throughout the facility.
It can be calculated by dividing the new cost of the equipment by its expected life in hours and multiplying by 70% or 100%. This will give you an estimate of the maintenance and repair costs per hour of operation. Note that this is an average number.
Reactive (run-to-failure), predetermined maintenance, preventive maintenance, corrective maintenance, condition-based maintenance and predictive maintenance.