Road safety is a big concern in many industries that require their employees to drive vehicles on the job. While 94% of serious traffic accidents are the result of human error, these numbers still leave 6% of other, often times avoidable causes, such as faulty systems or broken parts. Drivers can contribute to safer roads by conducting a thorough pre-trip inspection before they head out on a journey. Learn how a pre-trip inspection should be completed with ToolSense, what a pre-trip inspection is, what it entails, and how you can ensure that your employees follow the CDL pre-trip inspection checklist with the help of modern tools.
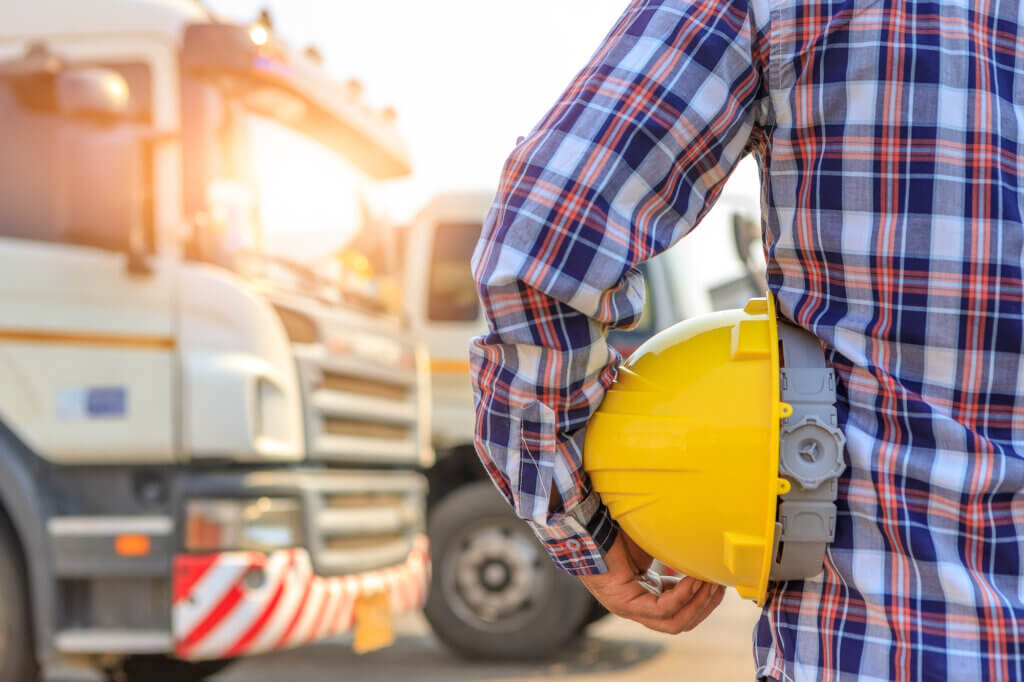
Key Facts
- A thorough pre-trip inspection should be done on any vehicle before it hits the road.
- This ensures that the vehicle is in working order, increases the driver’s safety, and lowers maintenance costs in the long run.
- Depending on whether a driver is checking a CDL Class A, B, or C vehicle, different components of the vehicle need to be checked before every trip.
- Examples from a pre-trip inspection checklist might include suspension parts, coupling, brakes, wheels, emergency equipment, lights, and windshield wipers.
- Pre-trip inspection software offers checklists and the ability to create custom forms to ensure drivers don’t forget a single detail during the pre-trip checks.
What Is a Pre-trip Inspection?
Any vehicle should be thoroughly checked before it hits the road in what is called a pre-trip inspection. This inspection ensures that the car, truck, or another type of vehicle is in working order to prevent expensive repairs as well as traffic accidents. Essentially, pre-trip inspections keep drivers safe by preventing accidents. They also contribute to lower maintenance costs as flaws can be repaired before they can cause further, more extensive damage. Potential malfunctions, failures, or broken parts are discovered during these checks and can be repaired or replaced before the vehicle heads out on the road. Pre-trip inspections have to be undertaken for trucks as well as their trailers and other vehicles that are being used on public roads, such as tractors.
Driving vehicles commercially requires a specific license which, in the United States, is called a CDL (Commercial Driver’s License). Other countries, such as the UK, Australia, and New Zealand, also require commercial drivers to have a specific license. The minimum age for acquiring a CDL is 18 years in the US. However, in interstate commerce, in the state of Hawaii, or when transporting hazardous materials, drivers are required to be at least 21 years of age. The CDL divides the license into three different classes, which all require different CDL pre-trip inspections.
ToolSense is trusted by 700+ companies
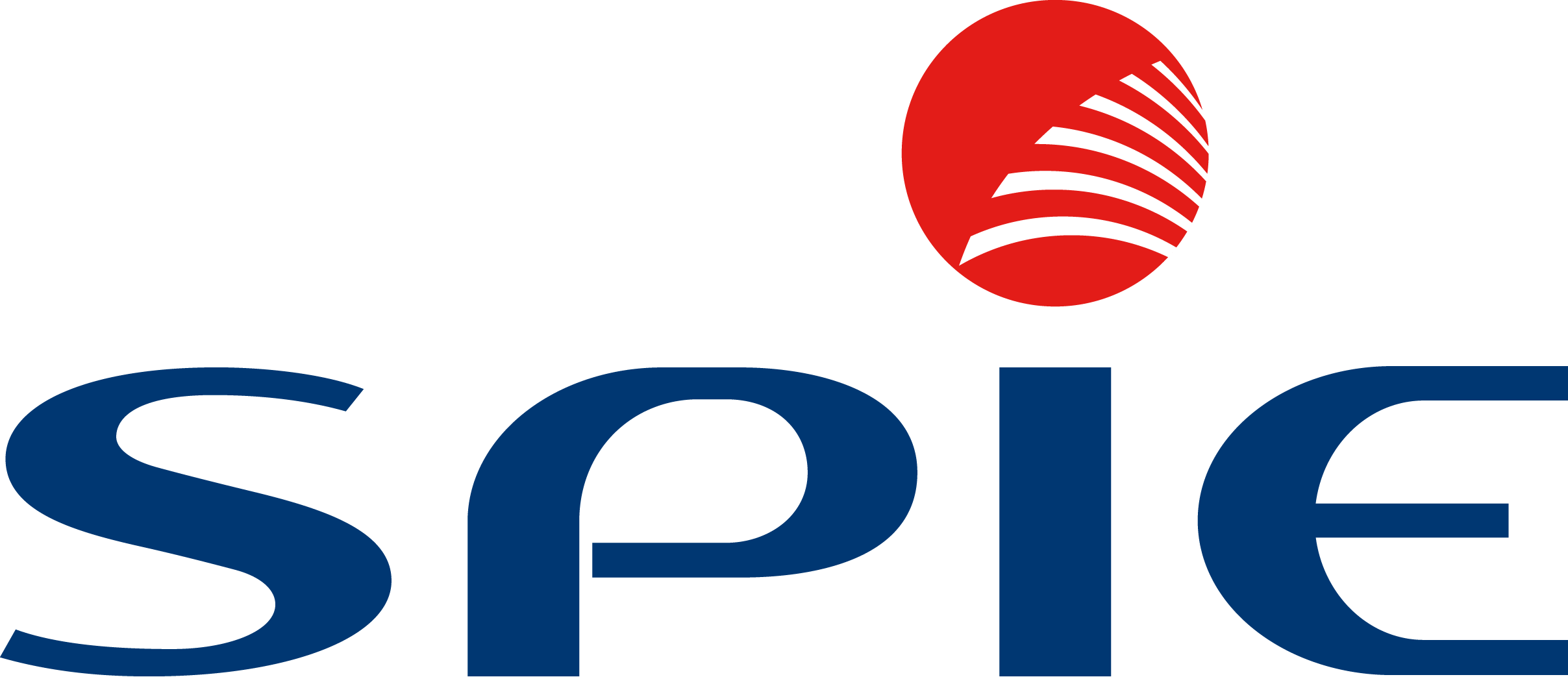
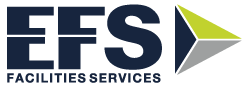
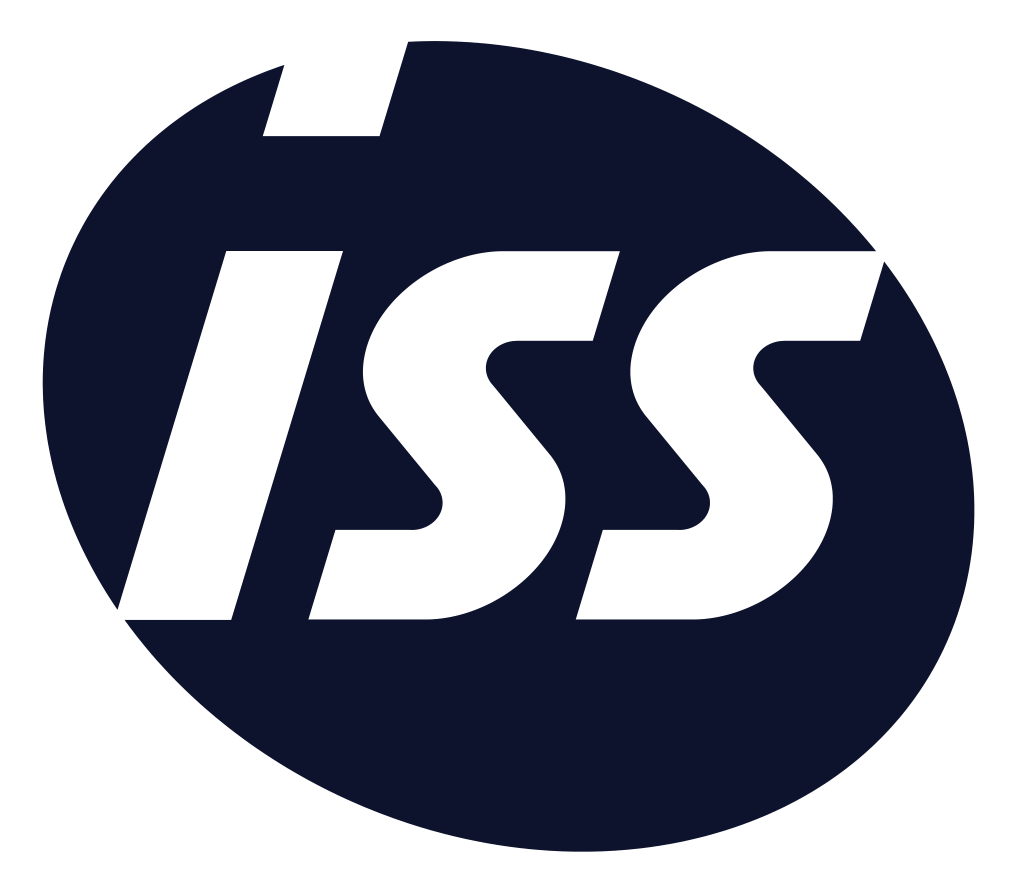
Class A Pre-trip Inspection
CDL Class A includes a combination of vehicles with a gross vehicle weight rating (GVWR) of 26,000 pounds if the towed vehicle weighs over 10,000 pounds. This includes tractor and trailer combinations, truck and trailer combinations, double and triple trailers, livestock carriers, tractor-trailer buses, flatbed trucks, and any vehicle that falls under Class B and C. A Class A pre-trip inspection is necessary for all vehicles that fall under this category.
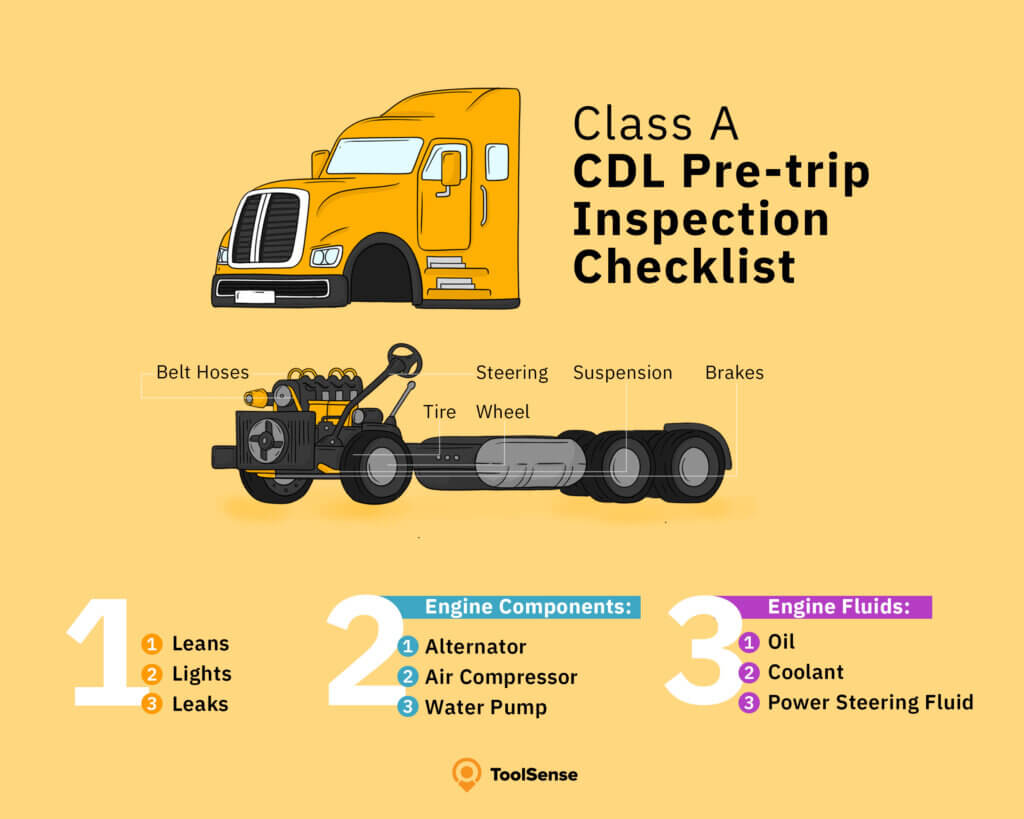
Class B Pre-trip Inspection
CDL Class B includes vehicles with a GVWR of over 26,000 pounds and vehicles towing a trailer of up to 10,000 pounds. This includes straight and box trucks, such as delivery vehicles, large buses, and trucks with small trailers. A driver with a CDL Class B can also drive Class C vehicles. A pre-trip inspection for Class B vehicles is also necessary. A Class B pre-trip inspection is necessary for all vehicles that fall under this category.
Class C Pre-trip Inspection
A CDL Class C allows drivers to operate any vehicle that transports 16 or more passengers, driver included. According to the Hazardous Materials Transportation Acts, a driver with a Class C license is allowed to operate vehicles designed for the transportation of hazardous materials. This includes small HAZMAT vehicles and passenger vans.
Minimum Pre-trip Inspection Requirements
These classes have different pre-trip inspection requirements, depending on what type of vehicle is being checked and what they are carrying. A pre-trip inspection checklist can help drivers remember which components need to be checked specifically, depending on the type of vehicle. However, these are the minimum requirements during a pre-trip inspection:
Service Brake, Including Trailer Brake Connections
The brake systems for both the towing vehicle and the trailer need to be inspected to ensure that the systems are in working order. If undetected, a malfunctioning brake poses a significant hazard. The brake hose should be securely mounted on both ends and not be leaking air. Any cracks, splits, or cuts indicate that the brake hose needs to be replaced or repaired. The brake chamber should also not be leaking air. Slack adjusters and push rods need to be examined during the pre-trip inspection to ensure that push rods have less than 1 inch of play and stay at a 90-degree angle to the brake chamber. The brake pads should not show signs of oil or debris and have a minimum brake pad thickness of 1/4 inch.
Parking Brake
Drivers should insure the parking brakes of both the vehicle and the trailer are in working order by setting the brake and releasing it.
Steering Mechanism
The steering gearbox, air lines and hoses should show no damage or leaks. The hoses should be connected on both sides. The steering shaft should be straight and intact. The rubber on the drag link is properly greased and shows no splits or cuts. During the pre-trip inspection, drivers should make sure that all pins and bolts on the pitman’s arm are secure. According to the Class A pre-trip inspection checklist, tie rods should be secure and show no signs of being bent or broken. The steering wheel should be firmly attached to the steering column.
Sign up now to access the latest market insights and improve your asset operations efficiency.
Lighting Devices and Reflectors
Every pre-trip inspection checklist should include lights and reflectors, meaning these need to be checked by the driver before every trip to make sure they are intact and working. The following lights and reflectors should be inspected before a vehicle hits the road:
- Running lights
- High and low beams
- Turn signals
- Hazard and warning lights
- Brake lights
- License plate lights
- Reflectors
Tires and Rims
Before the vehicle is used, drivers should make sure that no unauthorized wheel rims are used. Tires should not show cuts, abrasions, or bulges. The minimum tread depth is 1.6 mm and tires should be evenly worn. Air pressure levels should also be checked, and drivers should make sure that the valve stem is securely in place and not leaking air. Lug nuts should not show rust or cracks. When the driver checks the axle seal, it should be secure and show no leaks.
Horn
The functionality of the horn should be checked in every pre-trip inspection to ensure that it works in emergencies.
Windshield Wipers
As trivial as windshield wipers may seem, they are a part of every Class A pre-trip inspection checklist. Drivers must ensure wipers and fluid supply are working. The windshield wiper fluid should also be refilled.
ISS Austria
„We wanted to have a solution that does not only track expensive assets but also cheap ones. In Austria, ISS operates over 6,500 cleaning machines alone, without even counting vacuum cleaners and other pieces of equipment. With ToolSense we bring them together on a single platform, leveraging data from IoT hardware and improving maintenance and inspection processes.“
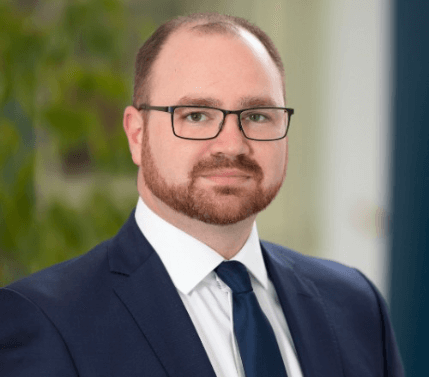
Rearview Mirrors
No CDL pre-trip inspection cheat sheet is complete without the mention of rearview mirrors. All of them should be intact and clean without cracks or damage. Drivers should also ensure that they are properly aligned.
Coupling Devices
When the vehicle is coupled to a trailer, the truck pre-inspection needs to include coupling devices. Air connectors need to be connected on both ends and show no signs of tangling, dragging, or damage. The same goes for the electrical lines, and the safety latch should be in place. The fifth-wheel platform is not allowed to have unauthorized welds and should not show cracks or signs of damage. Drivers should inspect the glad hands to check that the seals are in good condition and not leaking air. Mounting bolts should be tightly in place. The skid plate needs to be properly greased, and the release arm secure in a fully locked position. The kingpin should be firm and secure as well, while showing no cracks or damage. The locking jaw is intact and locks securely around the kingpin. The apron is also mounted and secured with no signs of cracks. The sliding fifth-wheel locking pins need to be in a fully locked position.
Emergency Equipment
Every pre-trip inspection list should include safety and emergency equipment. That means drivers need to ensure that the truck is carrying a functioning fire extinguisher, spare electrical fuses, and reflective triangles.
CDL Pre-trip Inspection Checklist
Tractor, bus, and truck pre-trip inspection checklists look a little different, depending on the type of vehicle that needs to be checked before heading out. With ToolSense you can create custom forms and checklists. Here is an example of what a printable pre-trip inspection checklist might look like:
1. Passenger Side Engine
- Drivers should check the air filter housing and verify that it is mounted securely, and the cover is in place.
- The windshield washer fluid reservoir should be filled to an appropriate level and show no leaks.
- The turbocharger does not leak oil or exhaust.
- The engine air duct is working, has properly secured clamps, and shows no cuts.
- Truck drivers need to inspect the alternator to see that it is securely mounted and does not have broken or loose wires.
- The accessory drive belt should not be cracked or frayed.
- The air conditioner compressor is securely mounted.
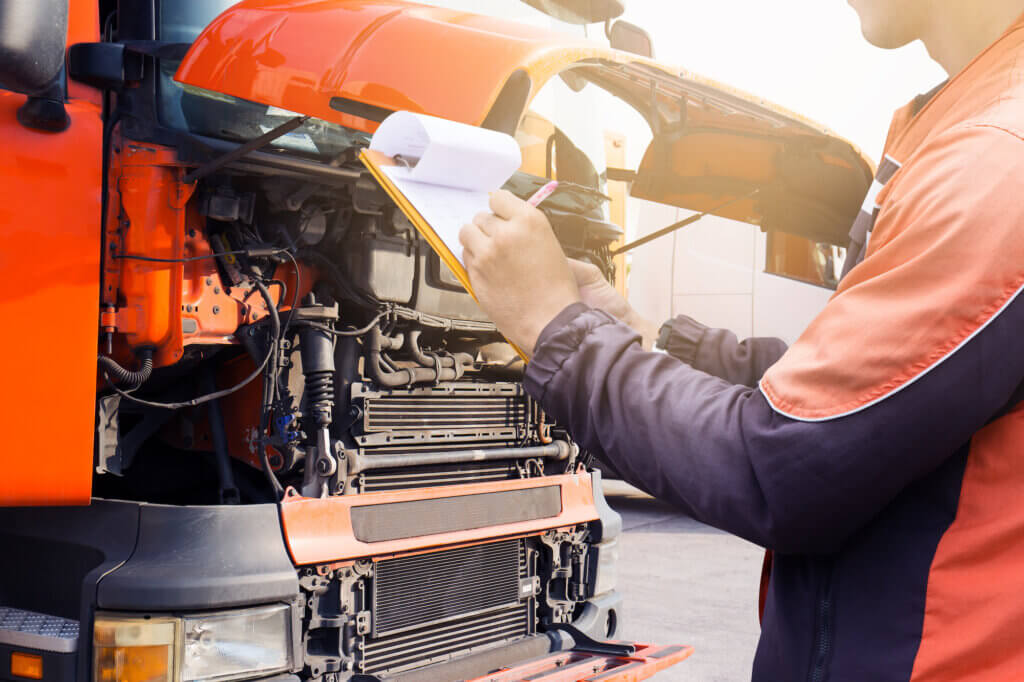
2. Front Brakes
- Truck drivers have to service brakes and ensure that the brake drum and brake lining show no cracks or signs of damage.
- No oil should be leaking from the inner oil seal.
- The slack adjuster should be at the proper angle to the brake chamber. The clevis and cotter pin should be intact.
- Drivers need to make sure that the brake air line shows no bulges or cuts and fits tightly.
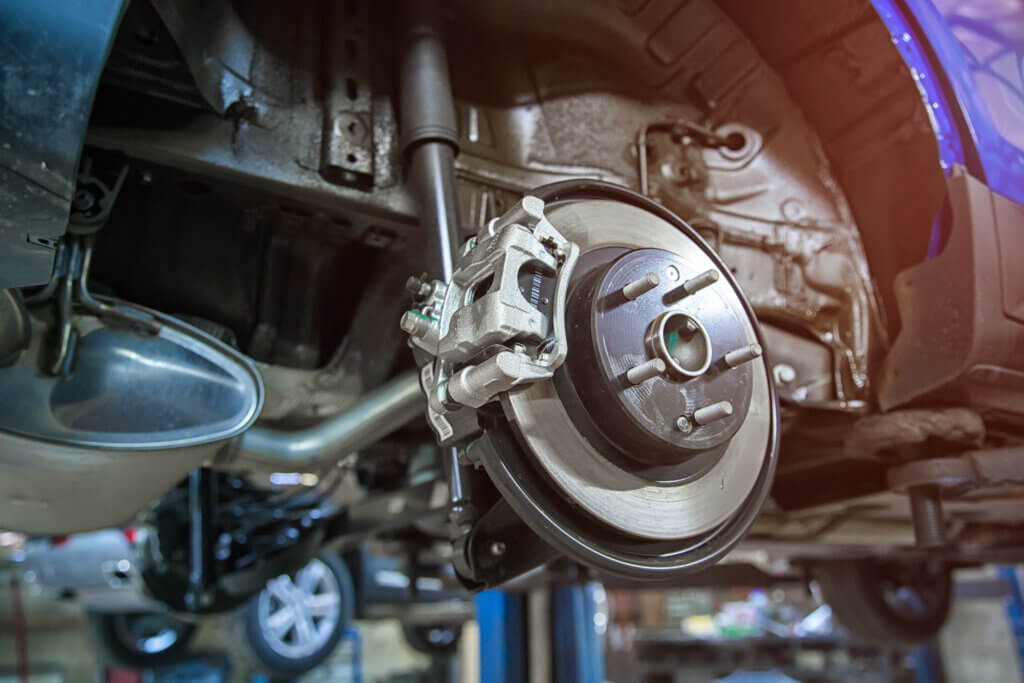
3. Front Wheel
- Truck drivers should check tires for abrasions, bulges, and cuts.
- The minimum tread depth should be 1.6 mm.
- Tires need to have a pressure of 120 PSI.
- The wheels should not be cracked or bent.
- If the hub is sealed, drivers can’t check the level. If it is not, the oil should be at an appropriate level and not leaking. The outer oil seal should not be leaking, either.
- The valve cap has to be in place.
- Drivers must make sure that the lug nuts are not missing, are secure, and show no streaks or shiny areas.
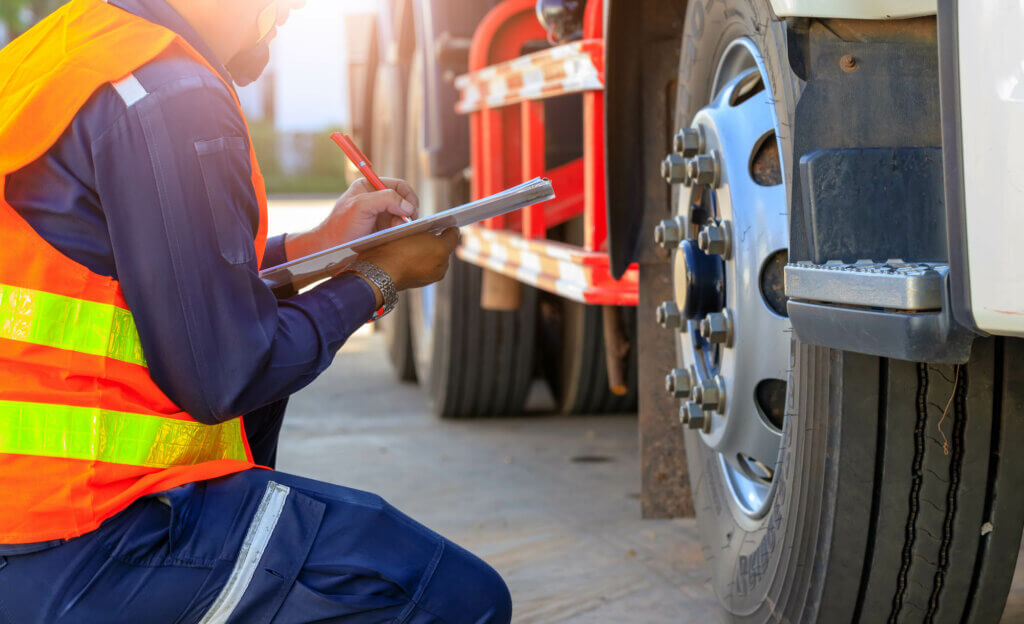
4. Driver Side of Engine
- Truck drivers have to ensure that the radiator brace shows no cracks or missing bolts and that the radiator is securely mounted and not leaking.
- The water pump should not be loose or leaking and show no cracks.
- The fuel water separator and filter show no leaks and are securely mounted.
- The pitman arm or drag link is not cracked, and the castle nut is secured with a cotter pin.
- Drivers need to check the steering gearbox to see that it is secured to its frame and not leaking.
- The power steering reservoir is at an appropriate level and shows no leaks.
- The dipstick shows the right level. The driver needs to secure it after every check.
- The steering shaft is also secure and not loose or damaged.
- There is no damage to the fuel pump and it does not show any cracks.
- The clamps on the engine air duct are secure and it does not show cuts.
- The brake master cylinder and the engine coolant reservoir show the correct fluid levels and do not leak.
- Drivers need to check the oil filler cap to ensure that it is secure and has no cracks.
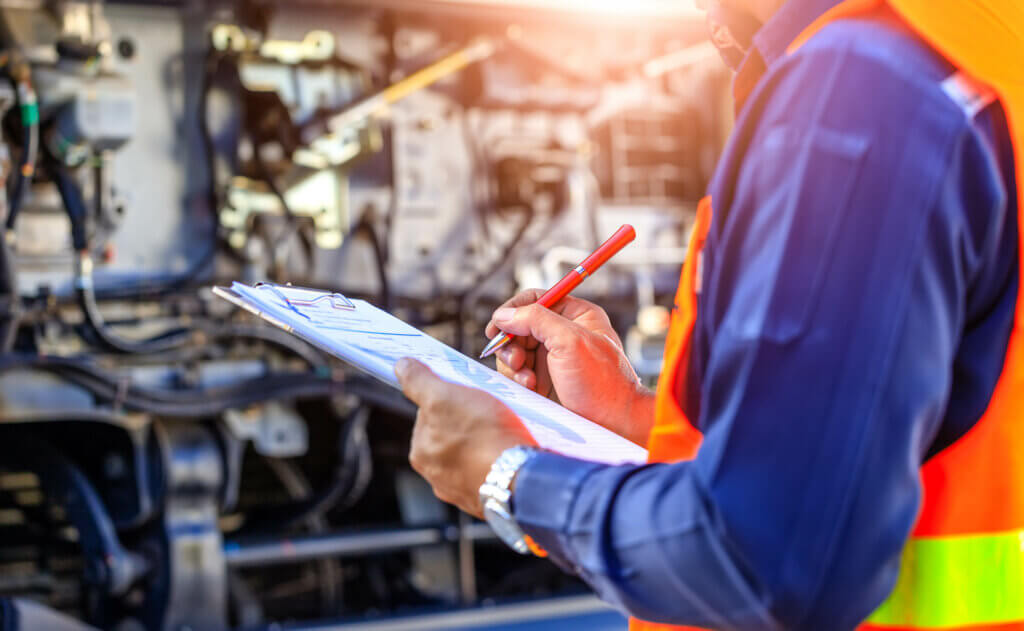
5. Steer Axle Suspension
- The u-bolts are not cracked, loose, or missing their nuts.
- The leak spring does not shift, shows no cracks, and is not loose.
- Truck drivers need to ensure that the tie rod is secure with castle nuts and cotter pins.
- The shock absorbers are securely mounted and not leaking oil.
- The axle shows no cracks.
6. Rear Suspension
- Drivers need to check the spring mount to see that is securely mounted and shows no cracks.
- Just as they did on the front, the rear tires should be checked by the driver for abrasions, bulges, and cuts. Pressure should be 110 PSI and the minimum tread depth is 1.6 mm.
- The shock absorbers are securely mounted and not leaking out.
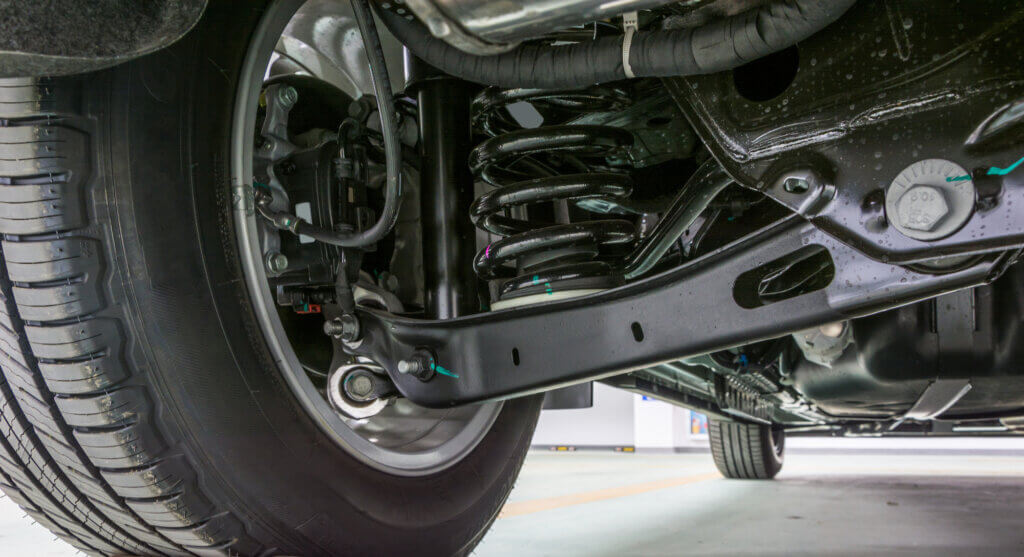
7. Side of Cab
- Drivers should inspect the mirrors to see that they are securely mounted, clean, and not broken.
- All doors should open and close properly, the hinges need to be secure, and there should not be any damage to doors or windows.
- The lights and signals are all working and not cracked.
- When drivers inspect the steps, they should be mounted properly and secured to the skirting.
- The battery box is securely mounted, and the cover is latched.
- The FED cap is secure.
- The gasket, vent, and chain are in place on the fuel cap and tank.
- The side skirting shoes no damage and the panels are secure.
- Drivers need to make sure that the side box is secured and that safety triangles are present.
- The body of the sleeper berth shows no damage, and the sleeper berth windows have no cracks.
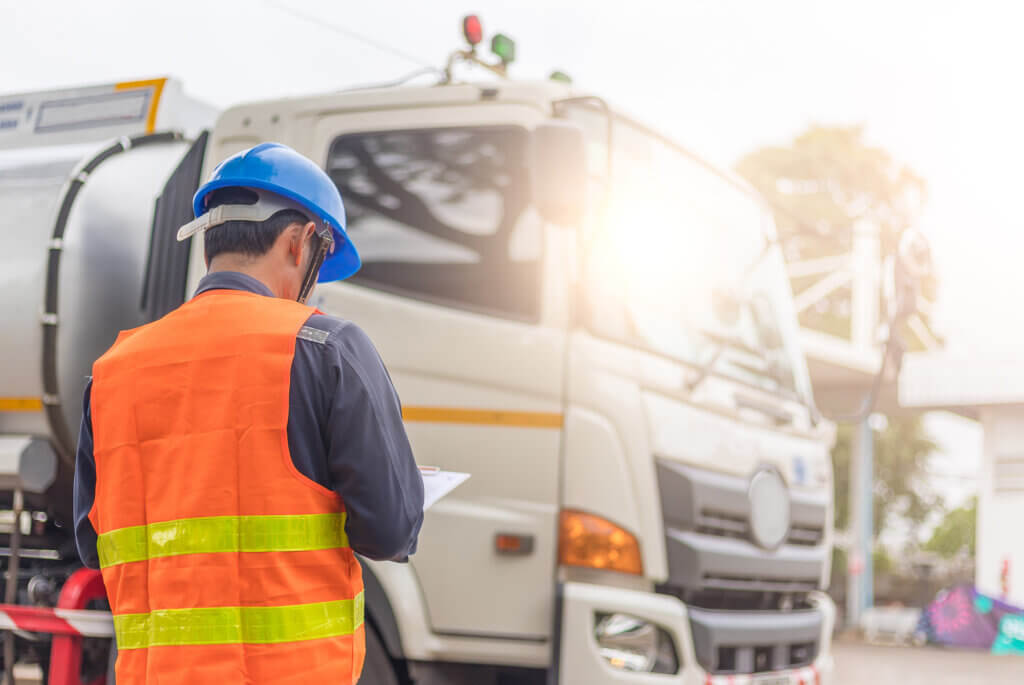
8. Rear of Cab
- When truck drivers are checking the electrical cord, there should be no bare wires or corrosion. The plug at the end of the cord should be intact.
- The airline should not be tangled or worn. The grommets fittings are tight.
- The cab shock absorbers are securely mounted and not leaking oil.
- The cab airbag bellows is securely mounted and not ruptured.
9. Drive Shaft/Rear Frame
- Drivers need to ensure that the drive shaft is not cracked.
- The universal joint does not show cracks, missing bolts, or shiny areas.
- The differential is not leaking oil.
- The frame is straight and does not have non-factory welds.
10. Fifth-wheel Area
- Drivers have to check that the keeper pin and cotter key on the pivot pin are intact.
- The slider lock pins are fully engaged.
- During the inspections, the release arm shows no bent.
- The slider rail and slider stop blocks do not have broken welds or missing bolts.
- The fifth-wheel platform is well-greased and tilted down.
11. Front of Trailer
- The top rail and tracking device have no cracks or collision damage.
- During the pre-trip inspection, clearance lights are working properly.
- The registration is readable.
- The document box is not loose or missing.
- Truck drivers need to ensure that airlines and glad hands have no bulges or cuts, and that the rubber grommets on the glad hands are not damaged.
- The electric hook-up has an intact cover and no broken pins.
- The PM sticker is legible and up to date. The height stickers are legal for the chosen route.
- The placard holder is intact and not missing rivets.
12. Side of Trailer
- Drivers need to check the top rail for cracks and collision damage.
- The clearance lights are operational. The bottom lights are not cracks, show no collision damage, and are not missing bolts.
- The landing gear has no broken welds, the sand pads are secure, and the legs are straight.
- The reflector tape is clean.
- During the pre-trip inspection, placard holder and side panels show no damage and have no missing rivets.
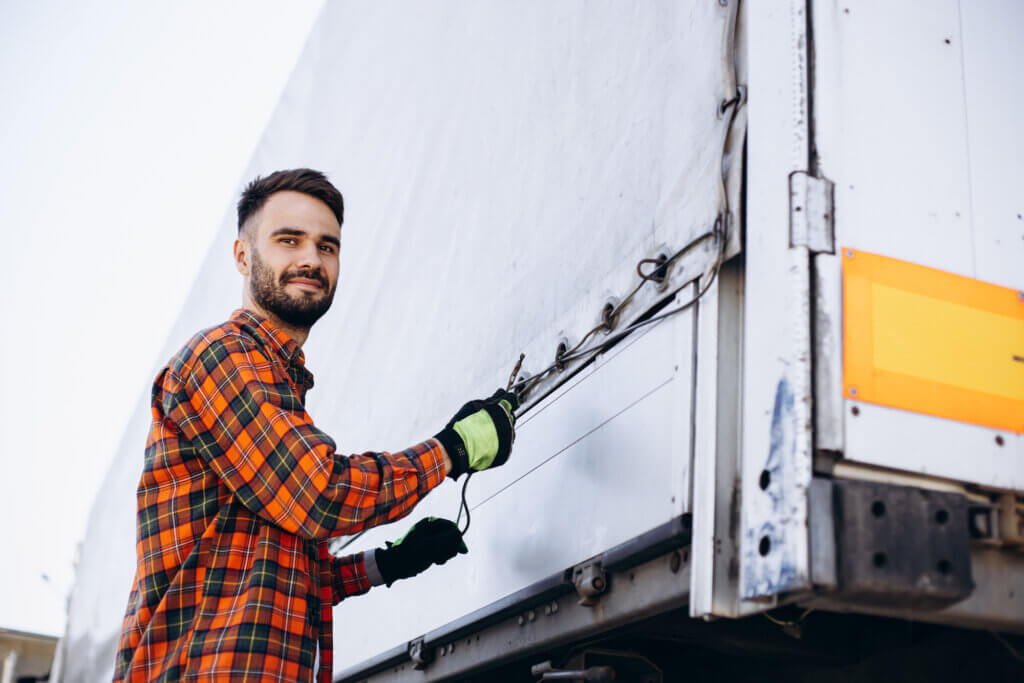
13. Rear of Trailer
- Drivers need to ensure that the latches are secured and not damaged.
- The placard holder is intact and not missing rivets.
- The reflector tape is clean.
- Truckers need to check the lights to make sure they are operational.
- The splash guard’s brackets and guard are secure.
- The license plate is secure and clean, and the light is working.
- The bumper is intact and does not show broken welds.
- Door hooks and hinges are secure, intact, and not missing bolts.
- While checking the door seals, there should be no separation or rubber tubing sticking out.
14. Trailer Suspension
- The airline shows no bulges or cuts and the fittings are tight and not rubbing.
- The axle is neither bent nor broken.
- Drivers need to make sure that clevis pins and cotter key are not missing.
- The slack adjuster is at the proper angle with the clevis pin and cotter pin intact.
- The brake drum is intact.
- Drivers should check tires for abrasions, bulges, and cuts.
- The minimum tread depth should be 1.6 mm.
- Tires need to have a pressure of 110 PSI.
- The spring is not broken or shifted, and sprint mounts show no broken welds.
- While performing a pre-trip inspection, drivers need to make sure that the u-bolts are not cracked or loose.
- The torque rod is securely mounted with the brushing intact.
- The spring brake chamber is also securely mounted with a secured band clamp.
Staying ahead of the requirements for safety inspections without proper tools takes plenty of time and effort. Flexible rules, pre-configured and custom inspections and powerful automations ensure a flawless operation of your assets.
15. Gauges/Inside the Truck
Inside the truck, drivers should check the following readings:
- Tachometer: 1000-1500.
- Water temperature: 180–205 degrees.
- Fuel level should match the visual while looking into the tank.
- DEF level: minimum of one light bar.
- Oil pressure: 25-50 PSI.
- Air pressure: 90-120 PSI.
- Speedometer: 0-60 MPH.
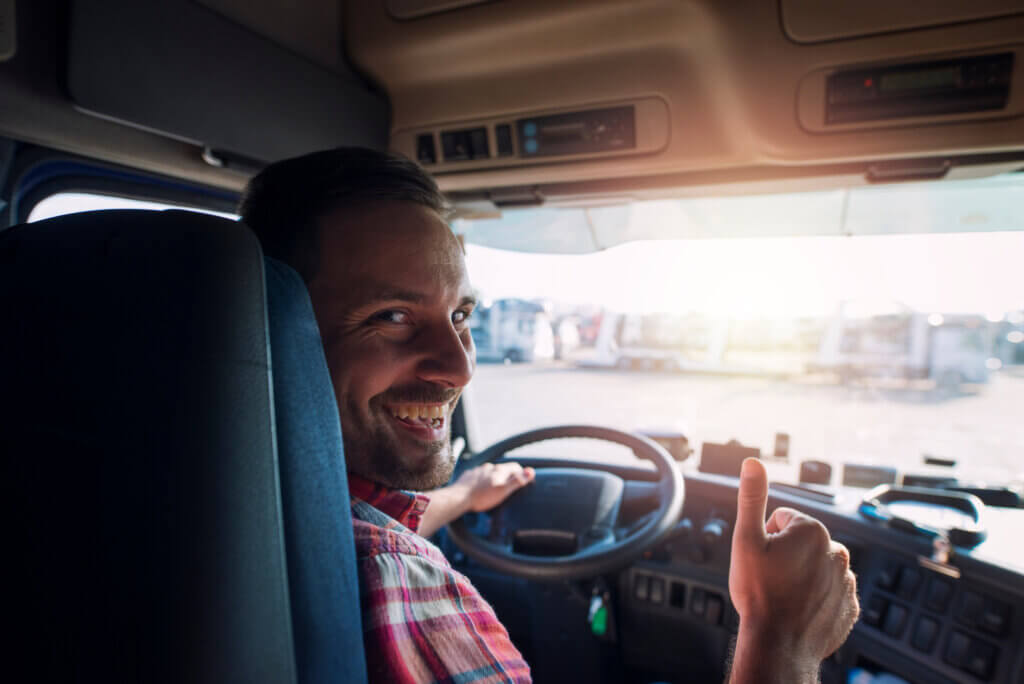
CDL Pre-trip Inspection Video
For more helpful tips on performing a pre-trip inspection, watch the video from Driving-Tests.org: “How to perform a CDL Class A Pre-Trip Inspection and pass in 2023”.
Completing a CDL Pre-trip Inspection Process With ToolSense
A CDL pre-trip inspection might seem like an overwhelming process and a lot of additional work for drivers that are already on a tight schedule, but there are ways to create a smooth and easy process for all employees involved. A printable CDL pre-trip inspection cheat sheet or a pre-trip inspection checklist in PDF format is just one way to make sure drivers don’t forget important details. Another option is a pre-trip inspection app.
ToolSense is a modern asset and fleet management solution that comes with pre-programmed pre-trip inspection forms and checklists and allows drivers to easily check off any parts that have already been inspected. Additionally, companies can create their own custom checklists using a simple form to ensure the lists are suitable for the type of vehicle that is in use. Because ToolSense’s pre-trip inspection software is cloud-based, employees can access important data from their desks as well as on the go with a smartphone or tablet. CDL pre-trip inspection pictures can also be added to the vehicle’s lifecycle folder within the software to ensure that drivers know exactly what to look out for.
Because ToolSense is a well-rounded asset management platform, creating checklists and forms is not the only handy feature it has to offer. Companies can track all of their assets either with modern GPS trackers, Bluetooth sensors, or a simple QR code system. That allows them to keep an eye on location, runtime, downtime, maintenance history, and work orders related to assets and vehicles. All this data is collected and saved in the asset management solution and used in handy analytics tools. Each asset and vehicle has its own lifecycle folder that stores information as well as pictures, videos, and invoices, meaning that everything is kept in one place where it is easily accessible to all employees. In the long run, ToolSense can increase a company’s productivity while saving time and money.
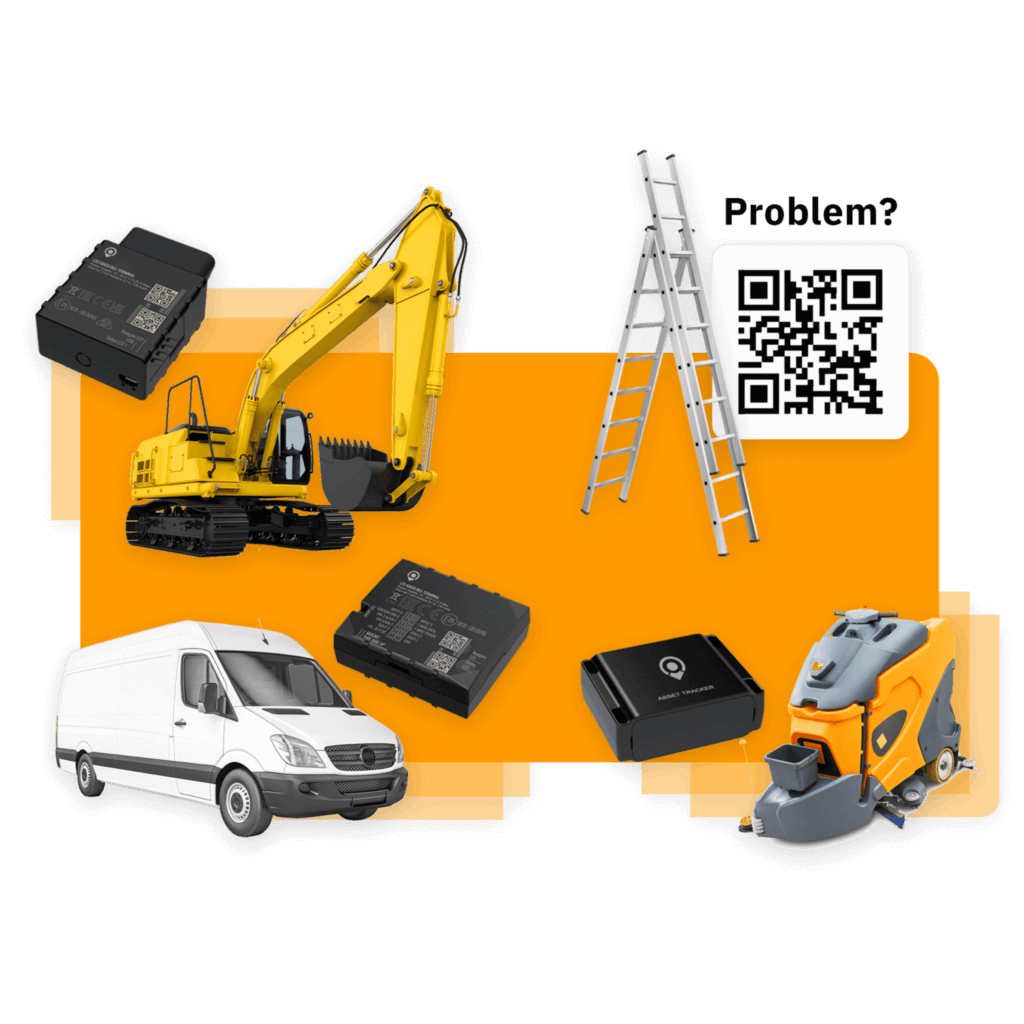
FAQ
A pre-trip inspection is a check of any vehicle before it heads out on the road. This ensures that the truck, bus, car, or tractor is in perfect working order, keeps drivers safe, and helps reduce maintenance costs.
This checklist is specifically designed for a pre-trip inspection of Class A vehicles and includes brakes, suspension parts, wheels, emergency equipment, lights, and more.
Pre-trip inspection Class B checklists were created to inspect vehicles of that class before they hit the road. These can include brakes and air systems, lights, steering, windshield wipers, and more.
A pre-trip inspection tool or software turns regular inspections into a simple and easy process by providing drivers with the information they need to undertake the inspection. This includes using pre-configured pre-trip inspection checklists or creating custom checklists that drivers can use so as not to forget a single detail about the inspection.