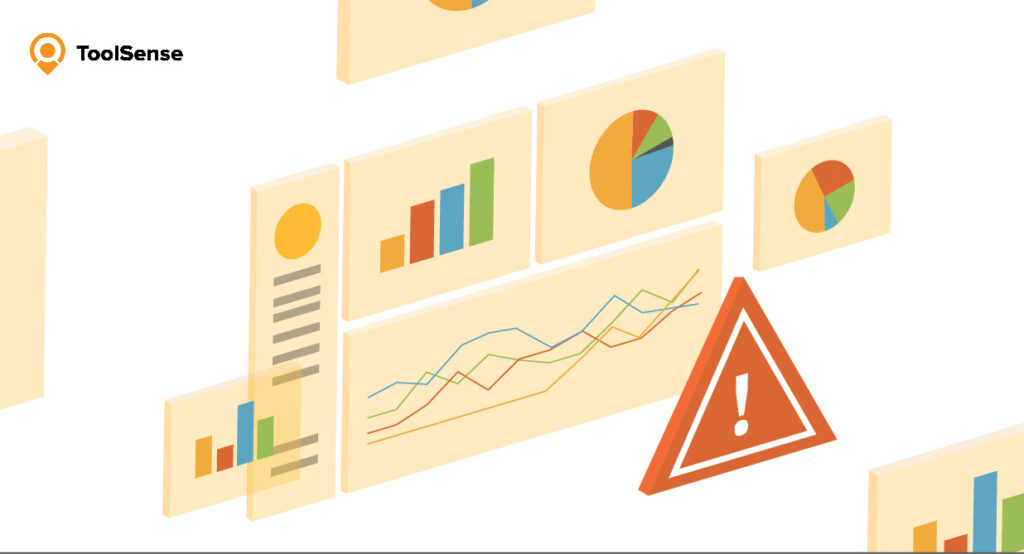
What happens when you only fix equipment after it breaks? Reactive Maintenance, often confused with corrective maintenance, can seem budget-friendly at first. But the long-term costs and frequent downtimes often reveal a different story. This “fix it when it breaks” approach, though necessary for certain assets, can lead to disruptions, safety risks, and reduced equipment life.
Let’s explore the pros and cons of reactive maintenance – and how balancing it with corrective and preventive strategies can boost both efficiency and equipment longevity.
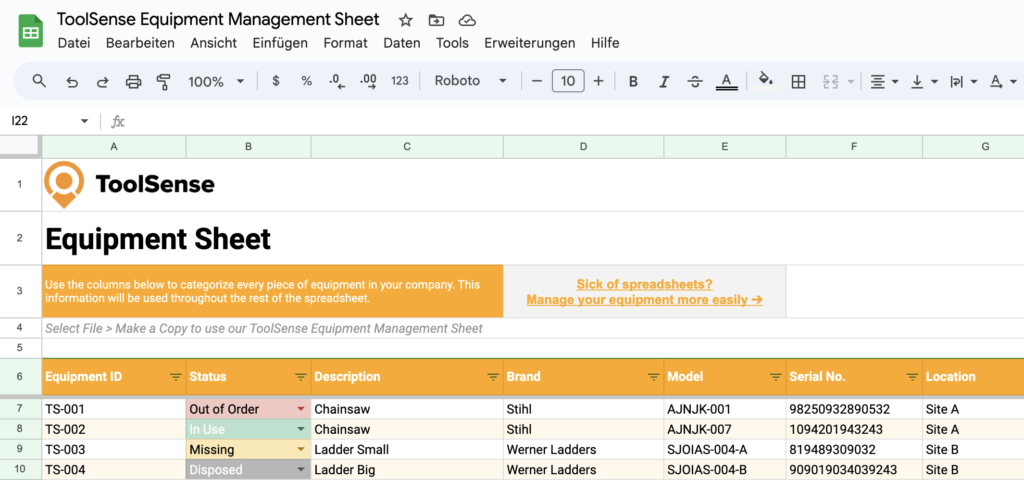
Key Takeaways
- Reactive maintenance is a straightforward approach to handling equipment and machine malfunctions. Rather than planning regular maintenance intervals, this strategy addresses issues only as they arise.
- ToolSense enhances the efficiency of maintenance by offering tools that simplify issue reporting and asset tracking. Through its features like QR code scanning, employees can report problems instantly, ensuring a quick response to any breakdown.
- While reactive maintenance has its place, combining it with preventive strategies is often beneficial. Incorporating a structured planned maintenance strategy can further reduce unexpected issues and unplanned downtime.
- With ToolSense asset tracking and maintenance software, you can take a proactive approach to balancing your maintenance strategies. This powerful combination reduces unexpected costs, minimizes unplanned downtime, keeps critical equipment up and running when needed, and extends asset life through timely preventive maintenance.
ToolSense is trusted by 700+ companies
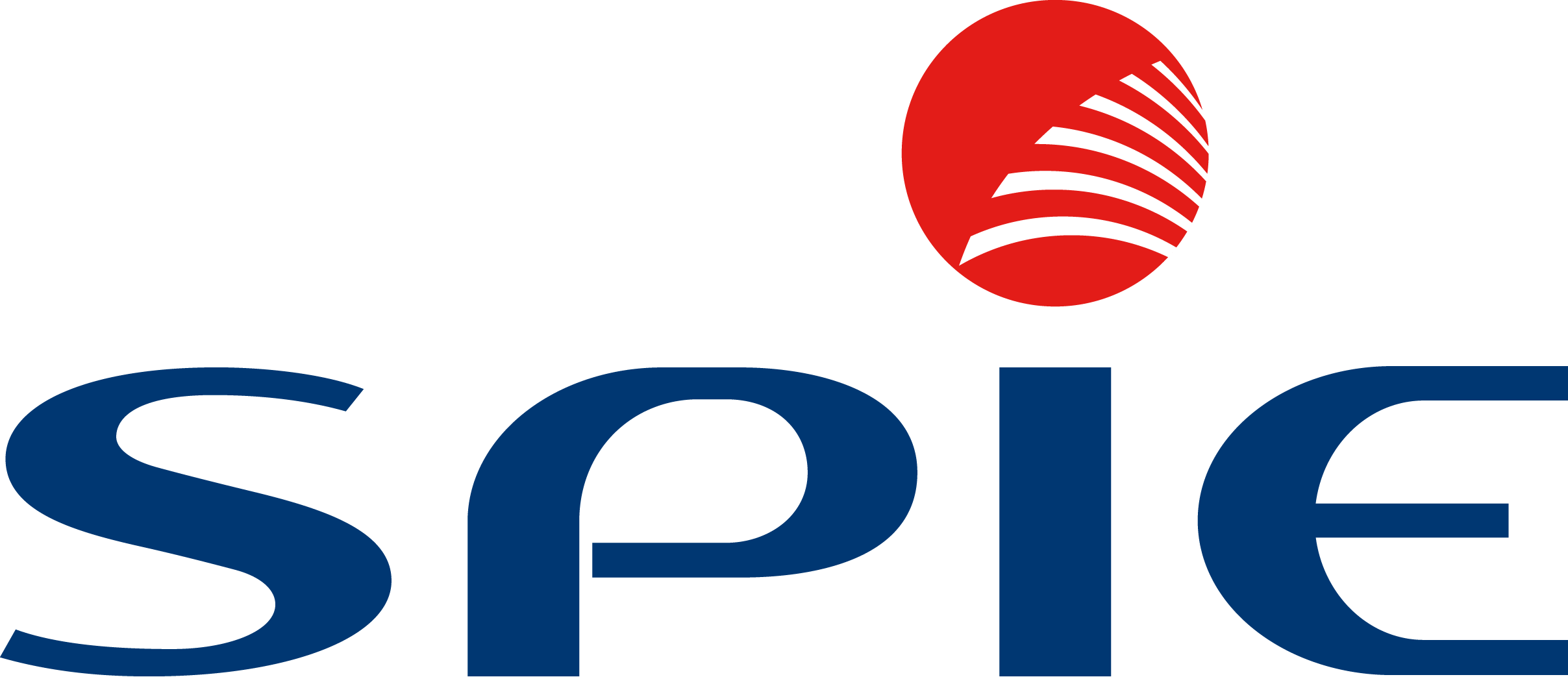
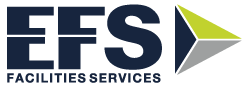
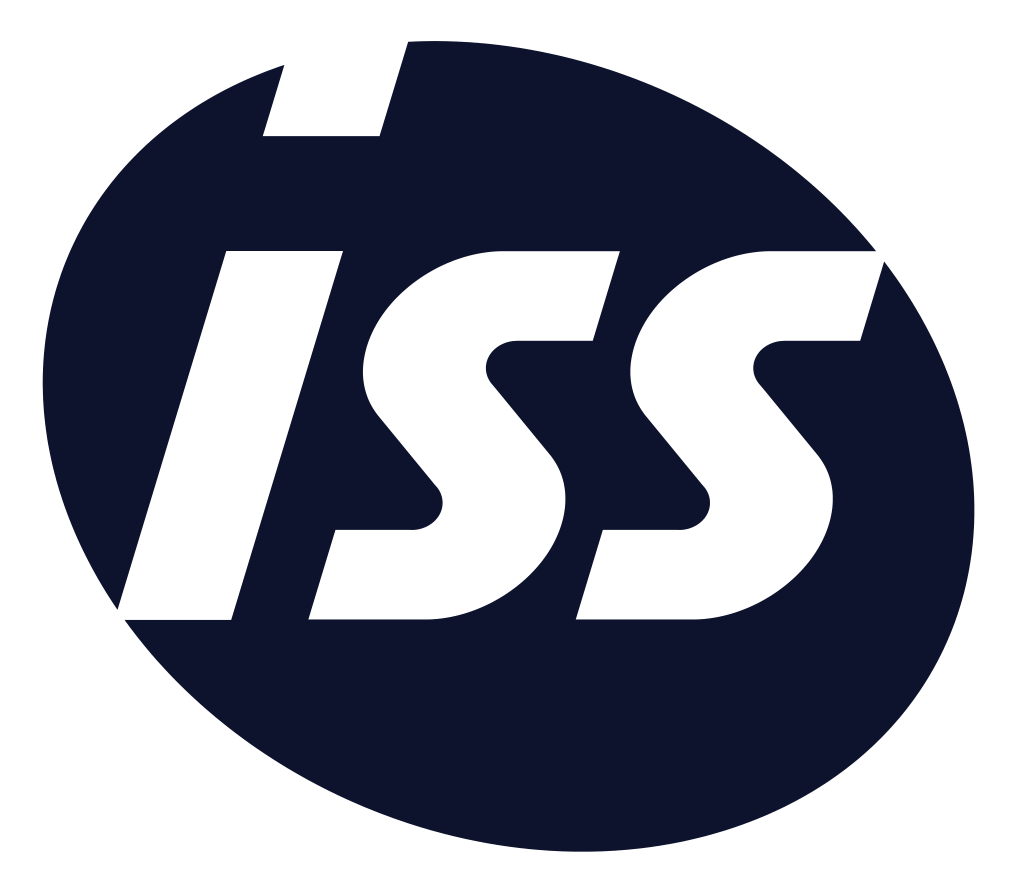
Reactive Maintenance at a Glance
Reactive maintenance is a maintenance strategy that addresses equipment or asset failure only after it happens, before any repairs or maintenance tasks are performed. Unlike preventive maintenance, which involve scheduled inspections and upkeep to prevent issues from arising, responsive maintenance takes a “run-to-failure” approach. This strategy is often summarized by the phrase “if it isn’t broken, don’t fix it”, emphasizing a response-driven model rather than a proactive one.
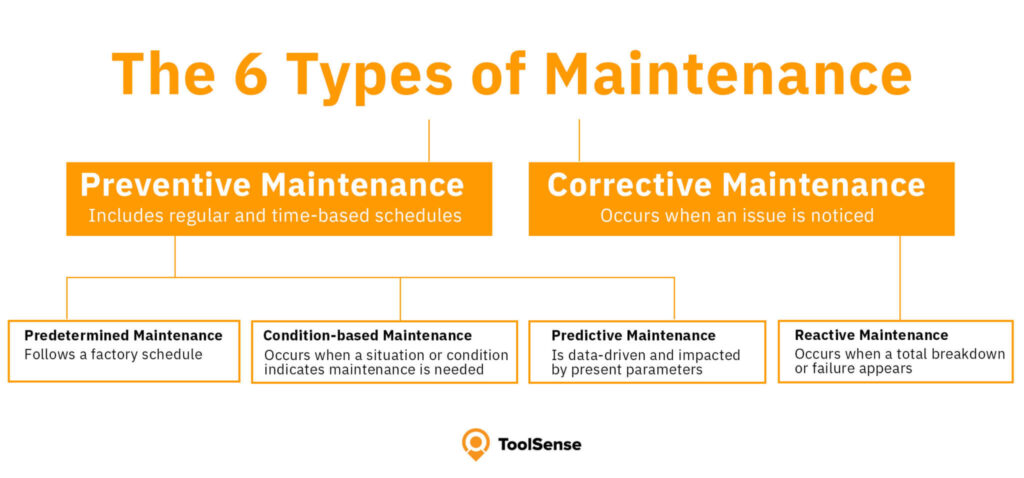
The Different Types of Reactive Maintenance
Responsive maintenance, while straightforward, can be applied in different ways depending on the urgency and nature of the asset involved. Here are the primary types:
Emergency Maintenance
Emergency maintenance is reactive maintenance at its most urgent. When critical equipment fails unexpectedly and creates a safety hazard, halts production, or risks further damage to other systems, immediate action is required. This type of maintenance demands quick response times and can involve significant costs due to unplanned repairs, possible overtime, or the need for immediate parts procurement. Emergency repairs are often reserved for essential assets, where delays could lead to serious operational or safety issues.
Breakdown Maintenance
Breakdown maintenance focuses on repairing or replacing equipment only after it has completely failed or is no longer operational. This approach is typically applied to non-essential assets or those with predictable failure modes, where a breakdown won’t disrupt the overall workflow or create significant safety hazards. Breakdown maintenance can reduce upfront costs, as it doesn’t involve scheduled checks or proactive repairs, but it carries risks, including sudden, unpredictable downtimes.
Run-to-Failure Strategy
The run-to-failure strategy is a planned version of reactive maintenance, where assets are intentionally allowed to operate until they fail. This approach is suitable for equipment that is non-critical, easily replaceable, or inexpensive to repair. Examples include items like lightbulbs, small tools, or inexpensive components that can be swapped out quickly without impacting broader operations. Run-to-failure is particularly effective when replacement costs are low or if replacements are kept readily available.
Managing maintenance across an entire company is quite a challenge. Build custom workflows in our Asset Operations Platform to easily manage maintenance processes for thousand of assets.
The Pros and Cons of Reactive Maintenance
Reactive maintenance can offer some advantages, particularly for certain types of assets or operational needs. However, it also comes with distinct disadvantages that can impact long-term costs and efficiency. Below is a comparison of the pros and cons:
Pros of Reactive Maintenance | Cons of Reactive Maintenance |
Lower Initial Costs: Reactive maintenance requires minimal upfront investment. Since there’s no need for scheduled inspections or routine repairs, companies save on initial planning and labor costs. | Higher Long-Term Costs: Over time, reactive maintenance can be more expensive. Unplanned repairs, especially if they’re frequent or involve complex equipment, often incur higher costs than preventive maintenance. |
Simplified Planning: This approach doesn’t require detailed maintenance schedules or preventive protocols, reducing the need for extensive maintenance planning and tracking systems. | Increased Downtime: Equipment failures are unpredictable, which can lead to unplanned downtimes. For critical assets, these disruptions can cause significant productivity losses. |
Reduced Need for Maintenance Staff: Reactive maintenance doesn’t require a large, dedicated maintenance team. Repairs are done on an as-needed basis, which can lead to smaller staff requirements. | Shortened Equipment Lifespan: Repeated breakdowns without preventive care can accelerate equipment wear and tear, reducing the overall lifespan of assets. |
Flexibility in Resource Allocation: Since maintenance is only performed when an issue occurs, resources can be allocated elsewhere until a failure demands attention. | Safety Risks: For critical equipment, unexpected failures can lead to safety risks for personnel, especially if machinery malfunctions in ways that put workers at risk. |
Reactive Maintenance vs. Proactive Maintenance
Understanding when to use reactive maintenance versus a proactive approach, like preventive maintenance, is essential for effective asset management. While reactive maintenance focuses on fixing equipment after it breaks, proactive maintenance involves regular, planned tasks to prevent breakdowns from occurring in the first place. A well-structured planned routine maintenance strategy can help avoid unexpected issues and unplanned downtime.
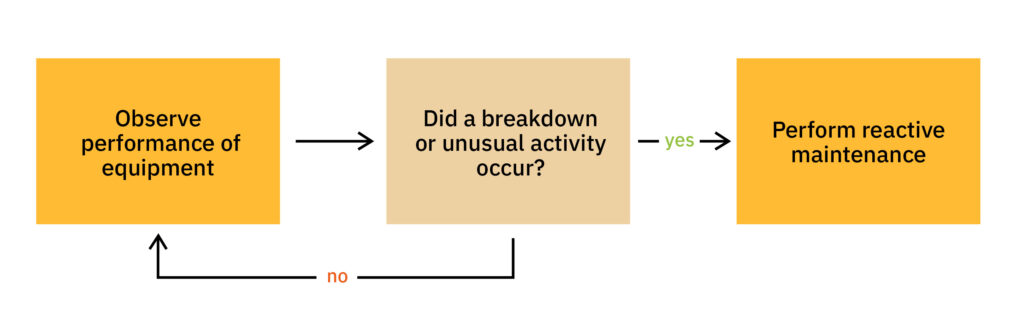
When Reactive Maintenance Makes Sense
Reactive maintenance is best suited for assets that are low-cost, non-critical, or easily replaceable. For example, in a facility with non-essential equipment or tools that are inexpensive to repair or replace, it may not be practical to allocate resources for regular preventive maintenance. In such cases, a run-to-failure strategy can be more cost-effective, allowing assets to operate until failure without affecting broader operations.
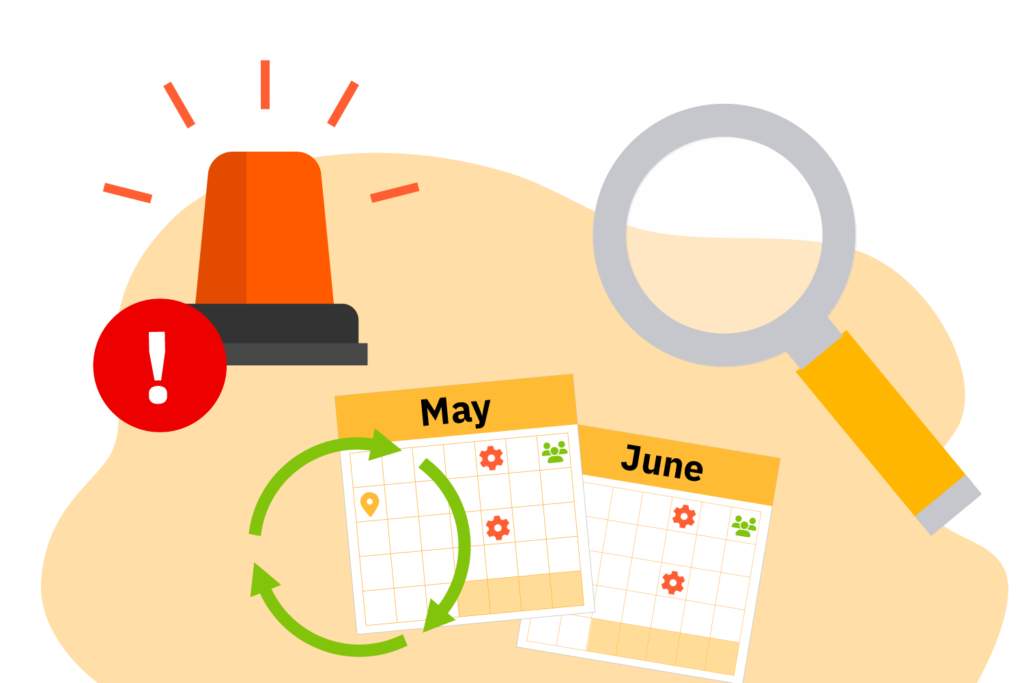
Another scenario where reactive maintenance is beneficial is when equipment usage is infrequent. For instance, assets that are only used periodically may not justify the cost of regular maintenance, making responsive maintenance a logical choice. However, it’s important to evaluate the impact of potential downtime and the availability of replacement parts to avoid unexpected disruptions.
Balancing Reactive with Preventive and Predictive Maintenance
For most organizations, a balance of reactive and proactive maintenance is the optimal strategy. By combining reactive maintenance with preventive and predictive methods, companies can manage resources efficiently, extend asset lifespans, and reduce downtime. Preventive maintenance involves scheduled check-ups and repairs to prevent malfunctions, while predictive maintenance uses data and monitoring to predict failures before they occur.
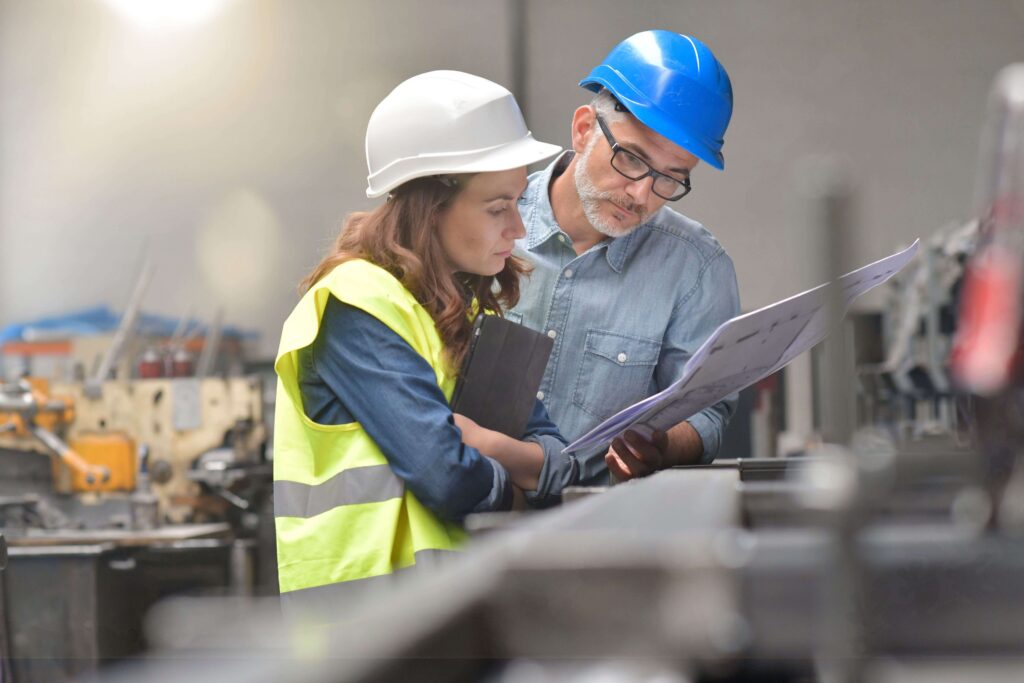
ToolSense: Simplifying Reactive Maintenance and Beyond
ToolSense offers a comprehensive platform that enhances the effectiveness of reactive maintenance and makes asset management more efficient. Through its innovative features, ToolSense not only helps organizations handle maintenance issues as they arise but also integrates proactive elements to reduce unexpected downtime and extend asset life.
Instant Issue Reporting with ToolSense
One of the key advantages of ToolSense is its streamlined issue reporting system. With QR code technology, employees can report equipment malfunctions or maintenance needs instantly. This process is simple: by scanning the QR code on an asset, users can immediately open a maintenance request, describe the issue, and attach relevant photos or videos. This instant reporting capability allows maintenance teams to react faster, reducing the time equipment remains non-operational.
Comprehensive Asset Tracking for Proactive Support
In addition to responsive maintenance features, ToolSense includes asset tracking and maintenance management functionalities that support proactive strategies. Through continuous asset monitoring, organizations can track usage, performance, and maintenance history, enabling them to make informed decisions about when to apply preventive maintenance. ToolSense allows teams to monitor asset runtime and usage data, providing insights that help schedule maintenance activities before issues occur.
This balanced approach, combining reactive and proactive methods, helps you optimize maintenance budgets, reduce unplanned downtime, and extend the lifespan of critical equipment. ToolSense’s asset tracking and maintenance scheduling capabilities allow your organization to adjust maintenance strategies based on asset importance, making it easier to manage high-value assets with preventive care while applying responsive strategies to less essential equipment.
Conclusion: Choosing the Right Strategy for Your Equipment with ToolSense!
Implementing reactive maintenance strategies is a balancing act that depends on the specific needs of your organization, the types of assets you manage, and the resources available. Responsive maintenance, with its “fix it when it breaks” approach, is effective for non-critical, low-cost equipment that can operate until failure without significant impact on overall operations. However, relying solely on reactive maintenance for all assets can lead to unplanned downtime, higher long-term costs, and potential safety risks.
A more balanced approach that integrates routine maintenance strategies, such as preventive and predictive maintenance, can maximize asset uptime and reduce unexpected costs. By implementing ToolSense, organizations can streamline their maintenance processes with instant issue reporting and comprehensive asset tracking, ensuring that problems are addressed as they arise.
Additionally, ToolSense’s proactive features allow teams to schedule maintenance based on asset usage and condition, helping to prevent equipment failure before they disrupt operations.
FAQ
Reactive maintenance refers to a maintenance strategy where repairs or servicing are conducted only after equipment has failed. It’s a “fix it when it breaks” approach, suitable for non-essential or low-cost assets.
Reactive maintenance is measured by the frequency and cost of repairs following equipment failures. In contrast, preventive maintenance is assessed by scheduled maintenance activities aimed at reducing breakdowns. The cost-effectiveness of each method depends on the type and criticality of the assets being maintained.
Reactive maintenance work includes all activities involved in repairing or replacing equipment after it has broken down. This can range from simple repairs to complex parts replacements, depending on the asset and failure severity.
While reactive maintenance has lower upfront costs, it can lead to higher long-term expenses due to unplanned repairs, shortened asset life, and increased risk of operational downtime. For critical equipment, relying solely on responsive maintenance may not be feasible due to the potential impact on production and safety.