Everything You Need for a Smooth Food & Beverage Production
Keep your food and beverage production running at maximum efficiency and safety – with the top-rated ToolSense Asset Operations Platform.
No credit card required
Great reviews on

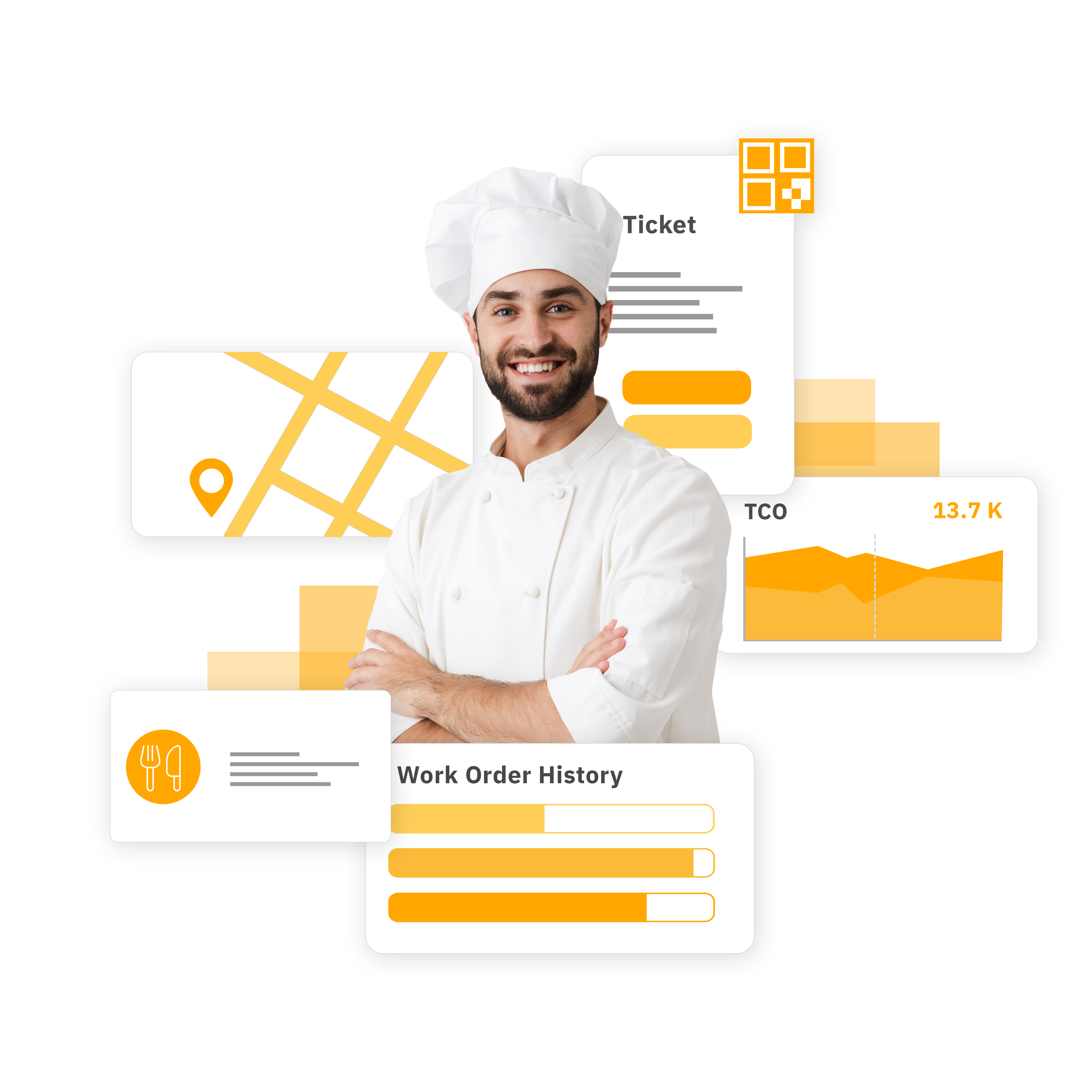
Ready to ditch Excel and Paper?
Join 700+ Operations, Maintenance & Repair Teams Simplifying Their Daily Business With ToolSense
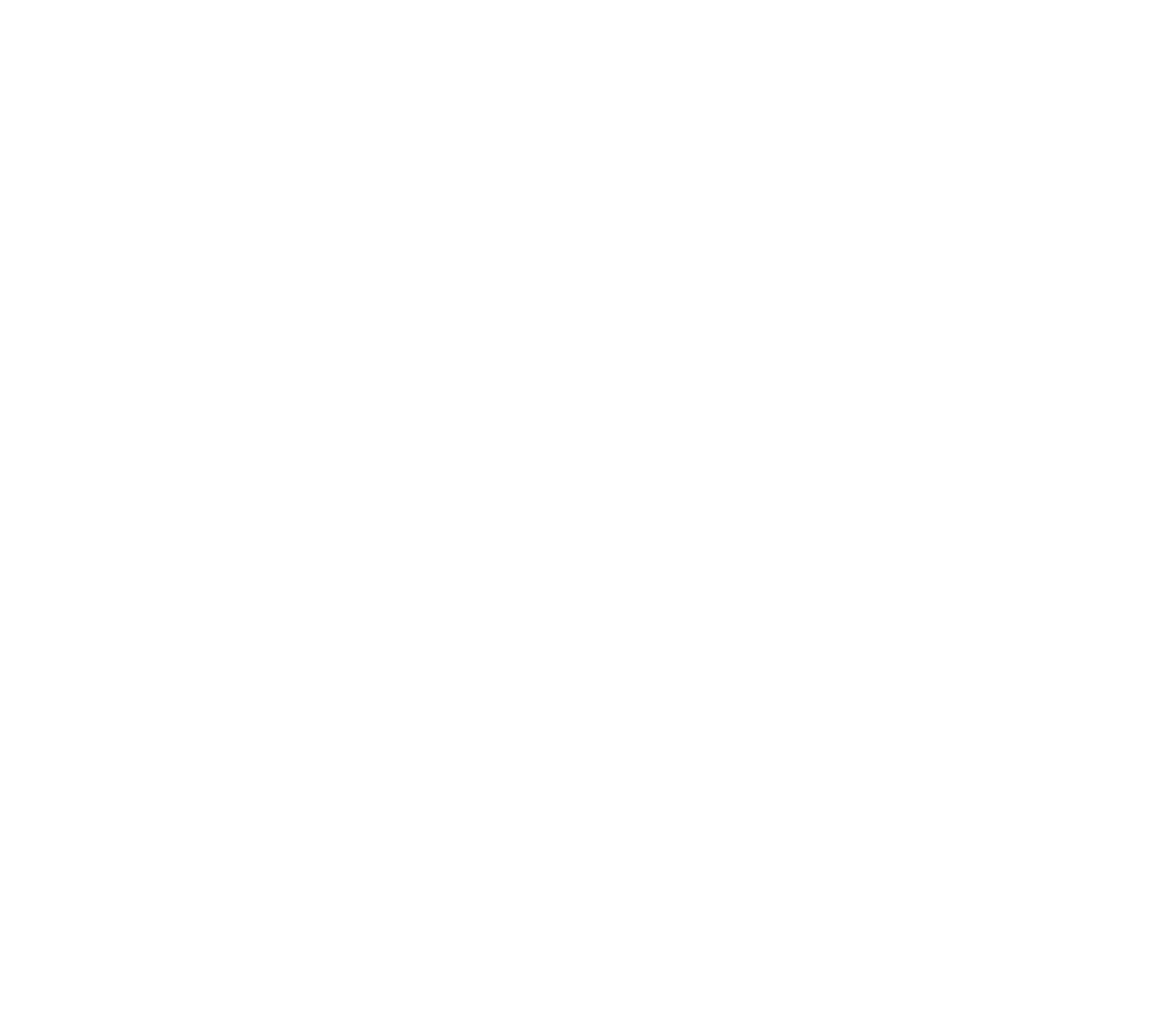
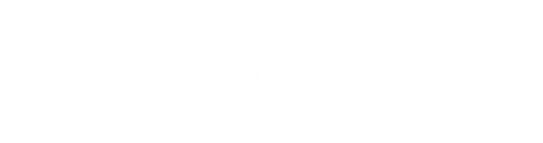
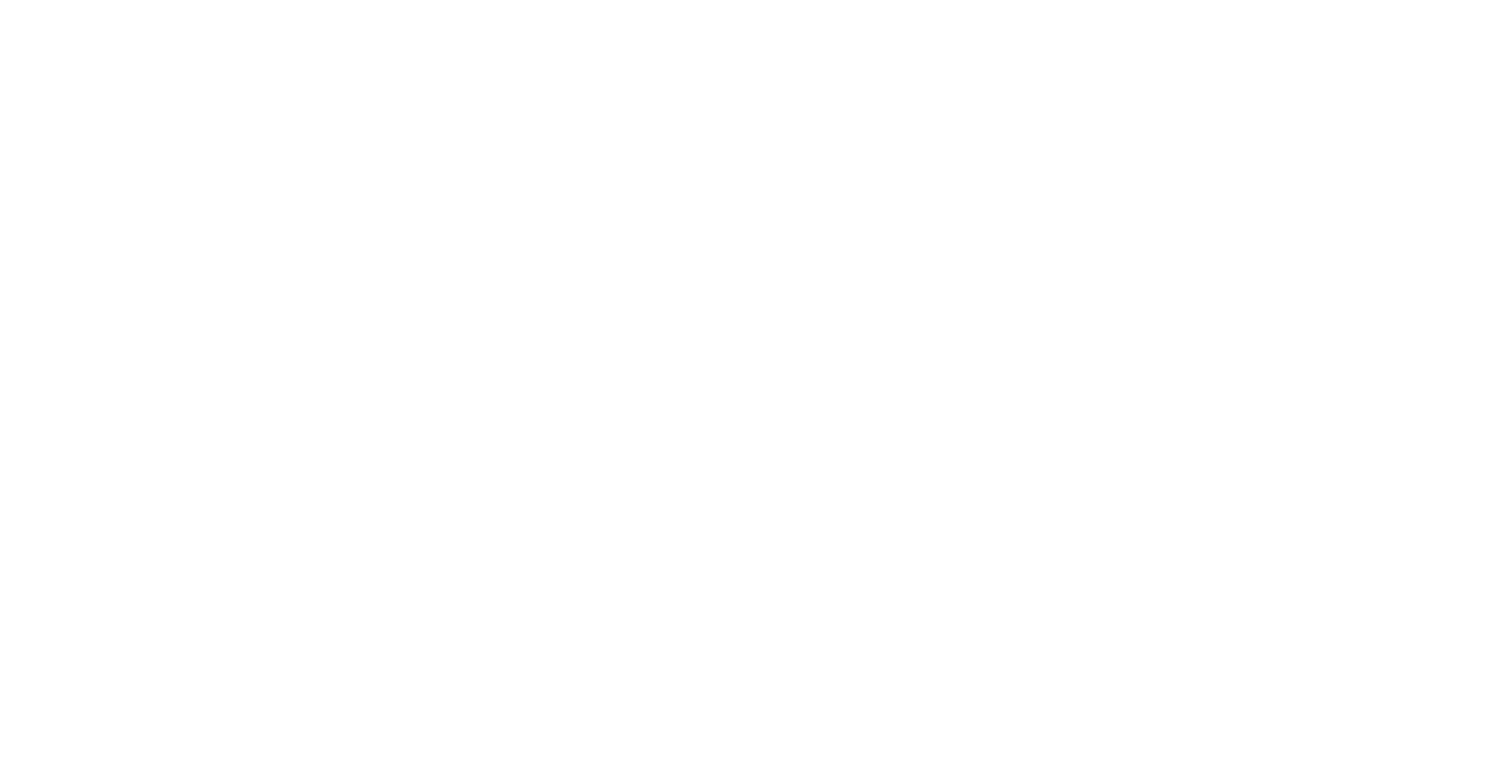
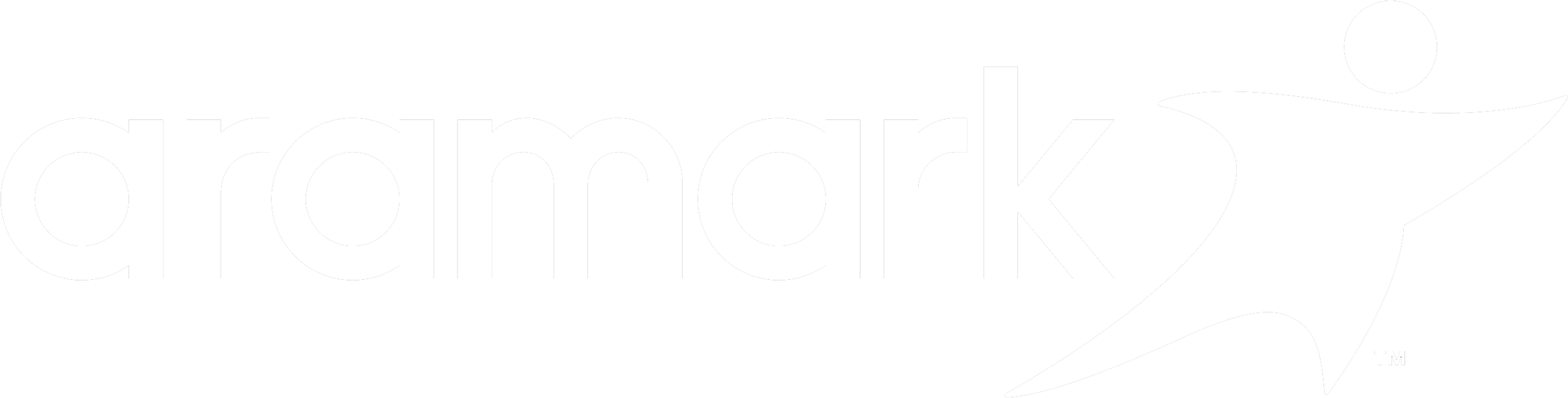
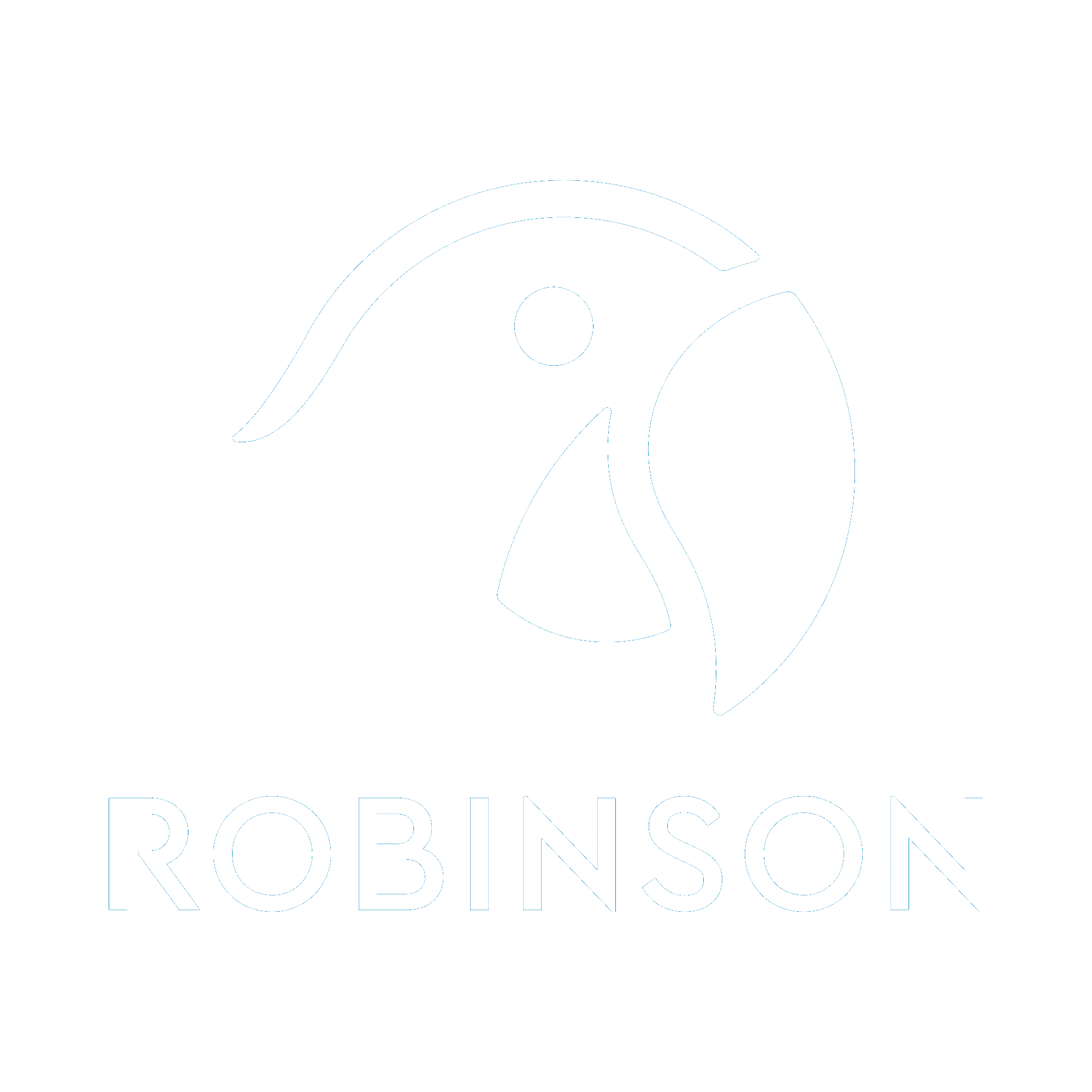
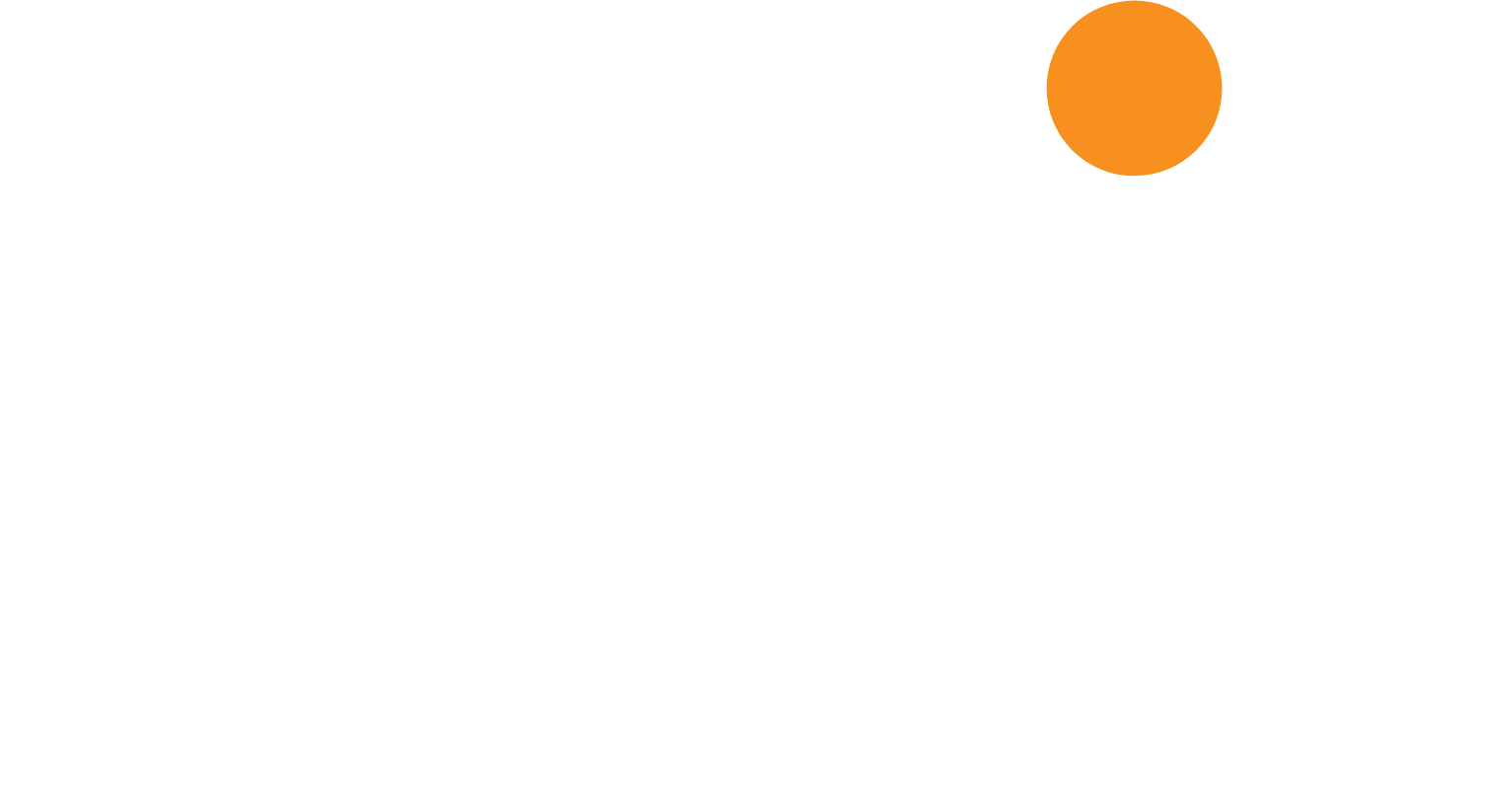
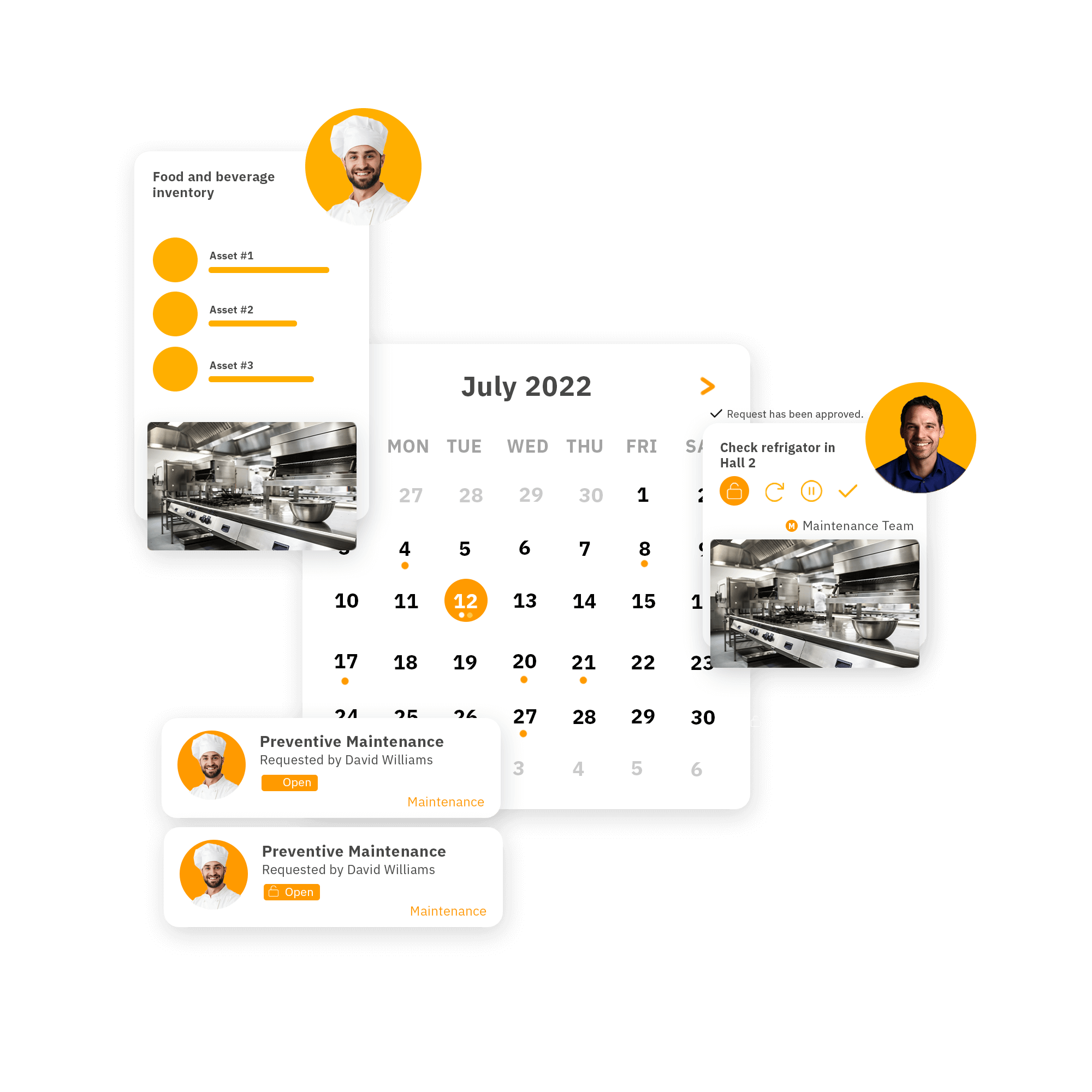
Keep Your Food and Beverage Production Running Smoothly and Safely
Stricter rules exist for food and beverage productions than for most manufacturing industries, so there are even more details to keep in mind during the process. The right management system can help you keep an overview of all areas of production, including asset management, work order management, inventory management as well as health and safety regulations to keep your production running smoothly at all times.
Maintain Equipment and Quality Control
During preventive maintenance audits, regular wear and tear, as well as unexpected faults, can be discovered and fixed before these minor flaws turn into bigger problems that lead to machine breakdowns. ToolSense’s asset management software will make it easy for you to schedule maintenance appointments and record their result. You can also determine maintenance intervals. In that case, the software will notify you of upcoming inspections. With a working preventive maintenance program in place, you’ll have a direct positive impcat on your business that won’t go by unnoticed.
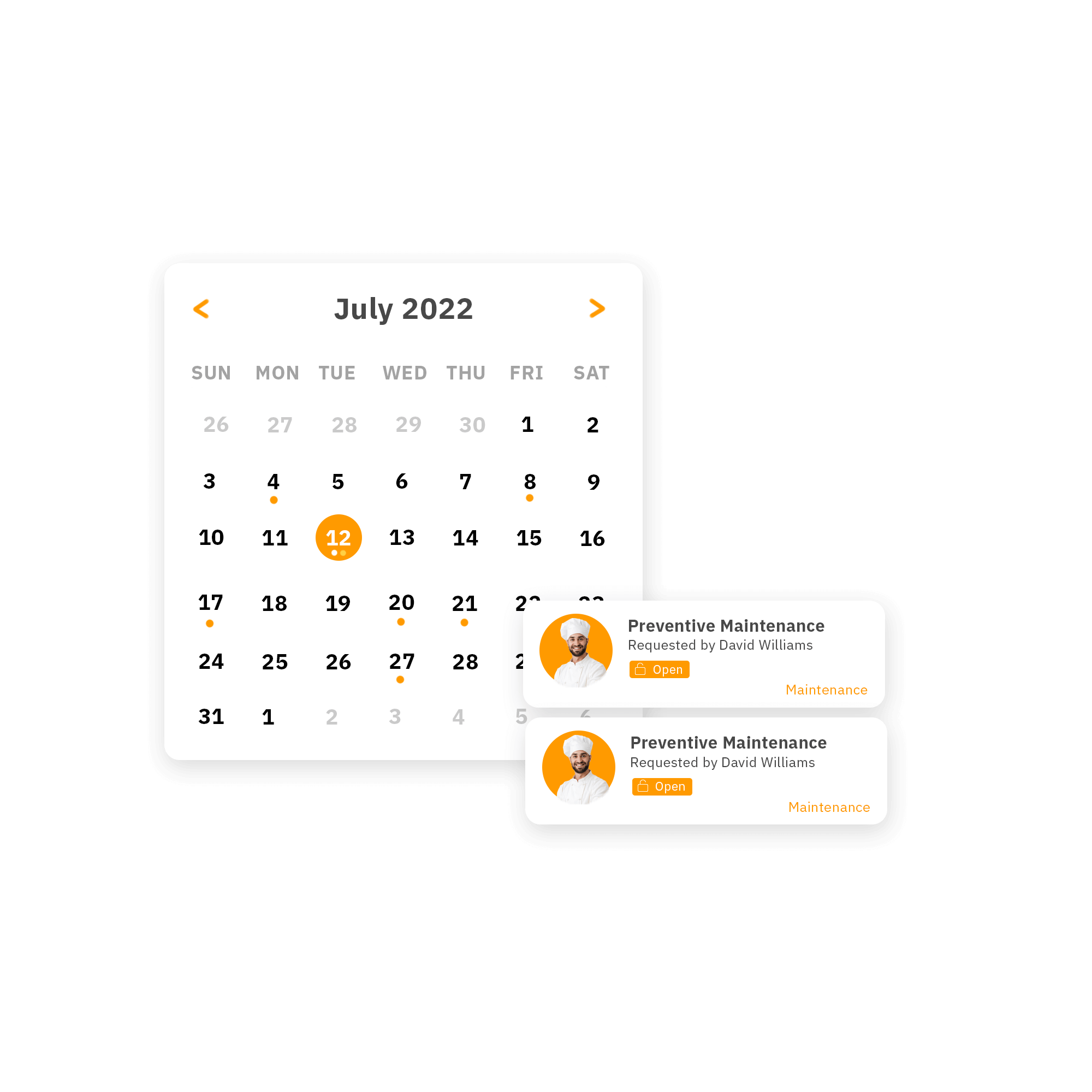
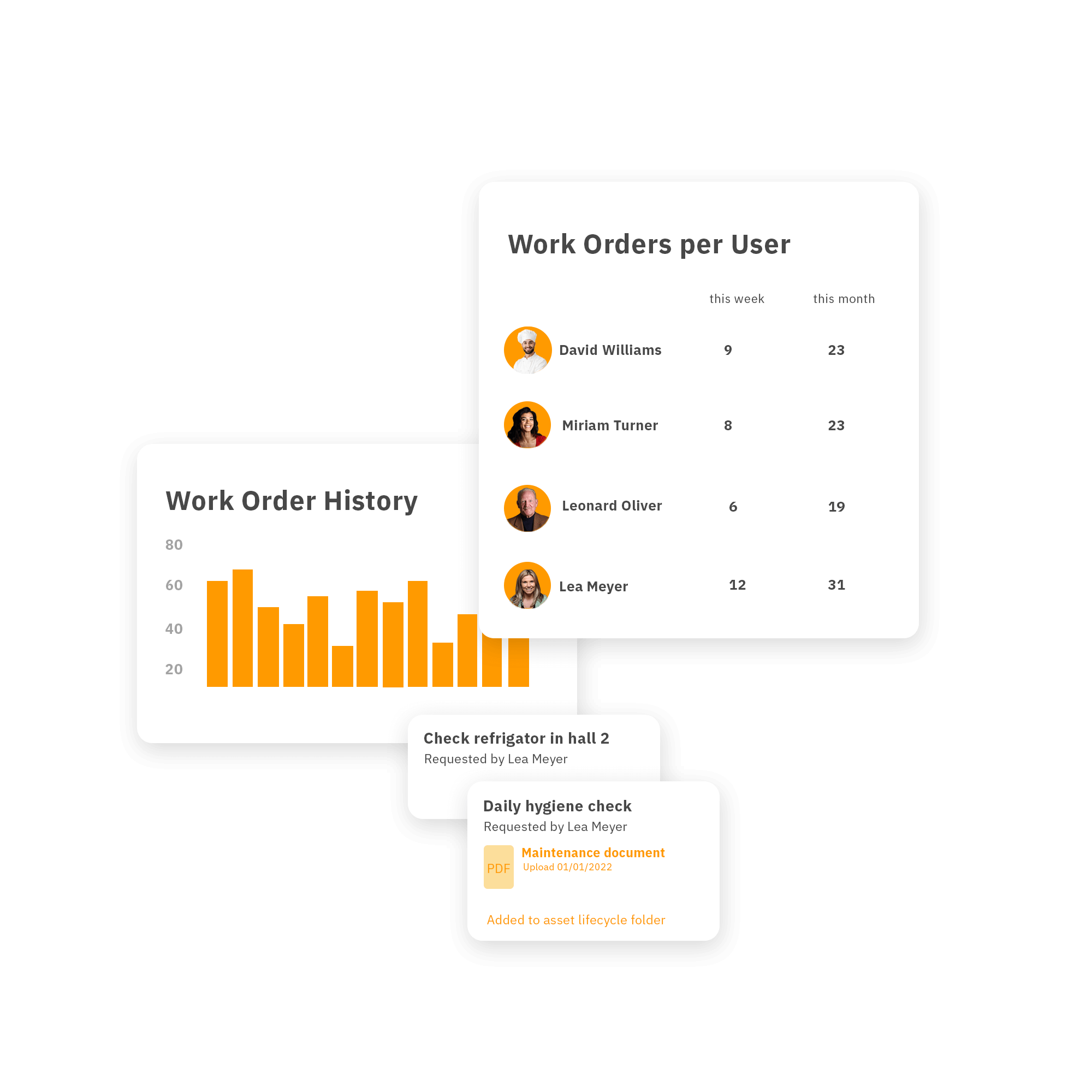
Manage a Complete Digital Audit Trail
A software for maintenance and operations leaves a complete digital audit trail that makes your maintenance tasks transparent and comprehensible for every employee involved. Every step is recorded in the system and filed in your machine’s lifecycle folder, making it easy for you to review audit details long after an inspection or repair is finished. This data can also be used for analytical purposes to determine whether to repair, replace, or retire an asset.
Perform Checklists and Inspections
To make sure your employees are following a strict protocol and every health and safety regulation is being adhered to, you can use ToolSense’s management software that allows you to create custom checklists so that technicians know exactly what to look out for during inspections. It also makes it easier to coordinate multiple employees and figure out which tasks have already been completed.
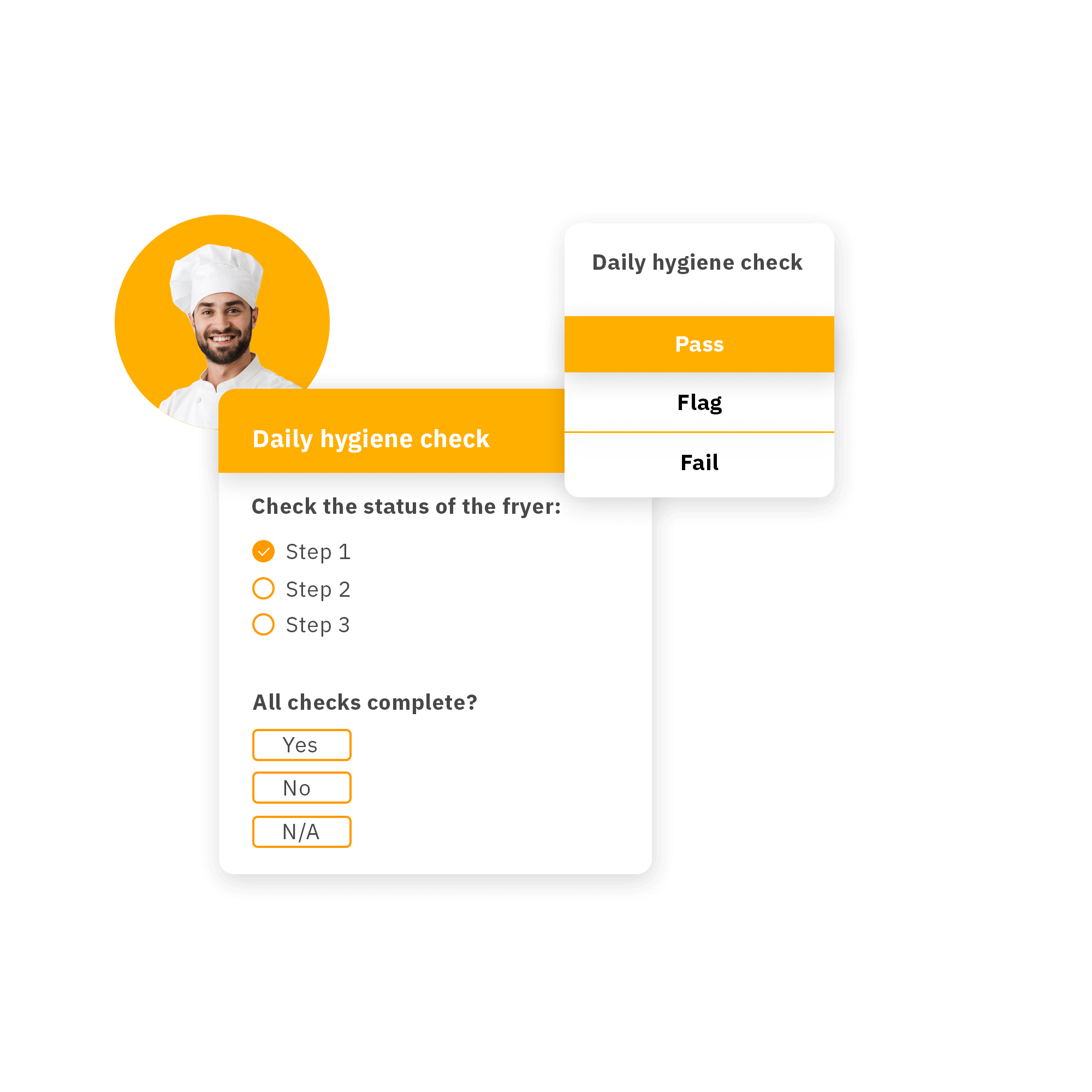
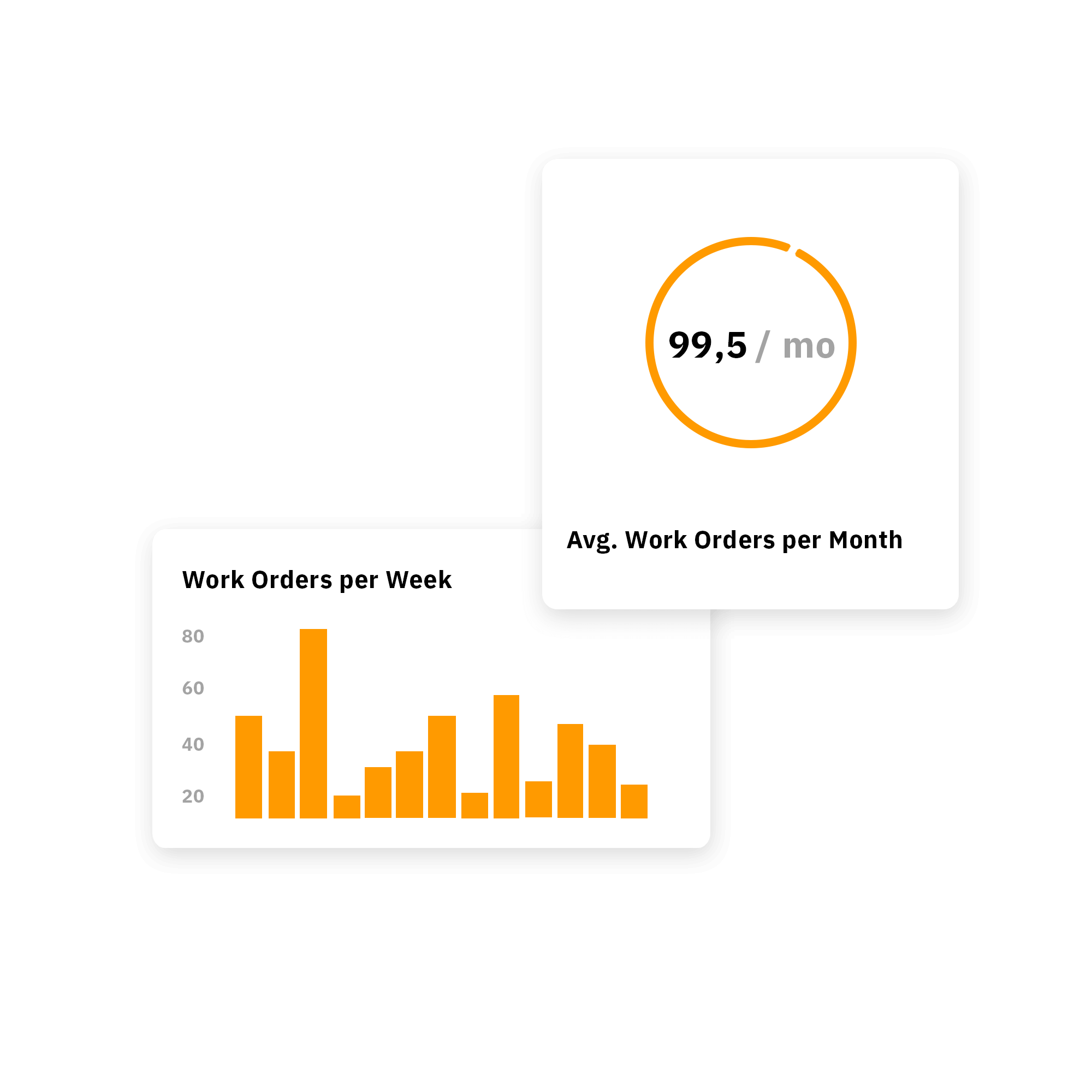
Reporting and Analytics
An asset management software like ToolSense offers many useful features, including powerful reporting and analytics tools. The system records important data, such as runtimes, breakdowns, location, repair costs, and much more, which can be used in your company’s decision-making process. ToolSense can show you exactly where costs arise, how long your employees take to execute work orders, and which assets are the most profitable.
Advantages of Using ToolSense for Food and Beverage
Focus and Alignment on Work Orders
ToolSense’s system combines asset management and inventory management, but also focuses greatly on work orders to make your day-to-day workflow easier and more transparent. Once a work order is issued through the system, the responsible employee is notified and can track their progress until the work order is closed.
IoT Solution for the Next Level
An array of interconnected assets can seamlessly exchange data through the network, which allows for clever automation and gathering of useful machine information. That is why ToolSense doesn’t just offer a software for maintenance and operations, but the respective hardware, too. You can choose between various trackers and GPS modules, or opt for the unobtrusive QR code method.
Easy QR Code Implementation
The maintenance management software issues a unique QR code that is assigned to each asset. If an employee uses the machine, wants to request a repair, or is about to finish an inspection, they can scan the QR code using their smartphone or tablet. Because ToolSense’s platform is suitable for desktop and mobile use, your employees can work from anywhere even if your assets aren’t stationary.
Asset Management Has Never Been so Simple
From location to runtimes – ToolSense collects and saves all important data surrounding your assets. Whenever a breakdown occurs or a machine is being repaired, the asset management software keeps tabs on the progress and stores every incident in your machine’s lifecycle folder.
Work Orders, Ticketing and Checklists
To make work orders especially convenient, ToolSense works with a smart ticketing system. Whenever an incident occurs – breakdowns, repair requests, spare part orders – a ticket is opened and forwarded to the person in charge. With useful checklists, they can track the work order’s progress and close the work order once it is completed. For transparency reasons or if it is needed for analytical purposes – the work order history is stored in the related asset’s lifecycle folder.
Unique Integration of Suppliers
Working with suppliers can involve a lot of paperwork or e-mails. Instead of going through heavy folders or your e-mail inbox in search of information, you can easily integrate your suppliers into the food and beverage management software. That means all the information you ever need – be it related to assets or work orders – can be found in one place in just a few clicks.