Have you ever wondered how smoothly functioning assets can translate into increased productivity and minimized downtime for your business? A well-maintained facility is crucial for ensuring optimal operations, while poorly maintained assets can lead to costly disruptions and even potential safety hazards.
In this comprehensive guide, we’ll explore strategies for solving common maintenance issues to ensure a smooth asset operation, the role of maintenance managers, the benefits of preventive maintenance, and how technology can help you stay ahead of potential problems.
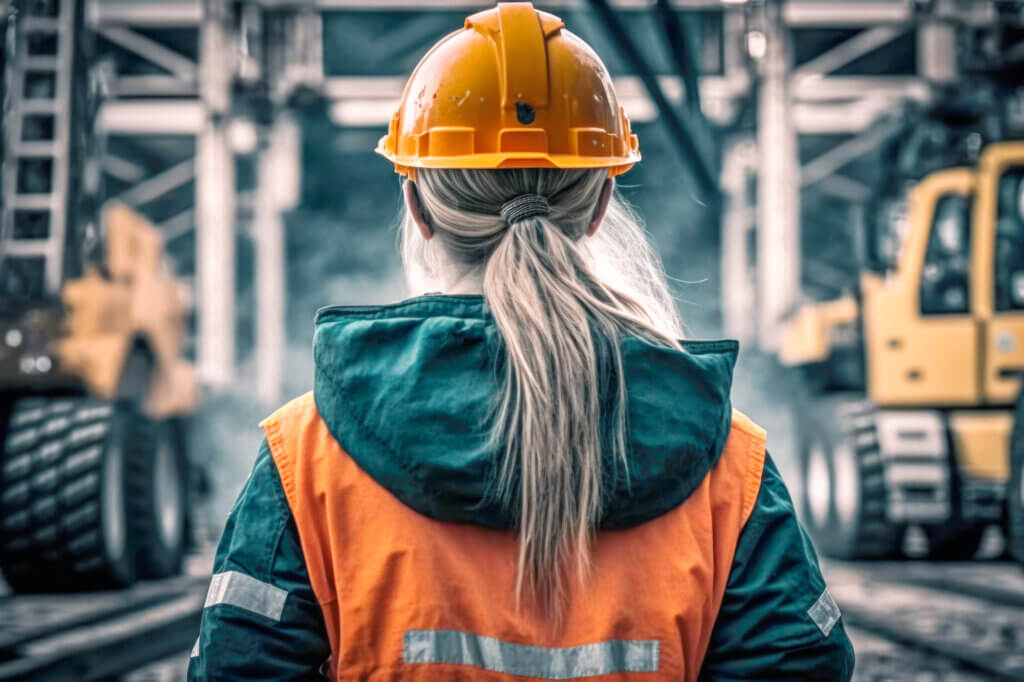
Key Facts
- Maintenance managers must prioritize asset maintenance and allocate resources to address common issues.
- IoT technology can be used for monitoring, maintaining and optimizing assets, resulting in reduced downtime and costs.
- Adopting maintenance management software like ToolSense improves scheduling, work order management, preventive maintenance and asset tracking.
Understanding Maintenance Issues
The importance of maintenance cannot be overstated. Proper maintenance can increase the economic life, lifespan, and productivity of your equipment. However, maintenance managers often face challenges, such as budget constraints, that limit their ability to implement effective maintenance plans. Neglecting asset maintenance can have serious consequences, such as disrupted operations, which can harm productivity and impact employee morale.
Some common maintenance issues include unexpected breakdowns, downtime, and high maintenance expenses. To overcome these problems, maintenance managers must develop strategies that prioritize asset maintenance and allocate resources effectively.
Expert advice
The real challenge lies in balancing the need for maintenance with financial and time constraints, while ensuring that critical assets continue to operate efficiently.
See How Maintenance Management Works With ToolSense
Types of Maintenance Issues
Maintenance issues can be broadly classified into preventive, corrective, and predictive maintenance. Preventive maintenance is particularly important for averting sudden equipment failure and ensuring the smooth functioning of assets, such as forklifts and conveyor belts.
By understanding the different types of maintenance issues and addressing them effectively, maintenance managers can ensure that their equipment remains in optimal working condition, reducing downtime and associated costs.
Depending on how you form your business structure, maintenance can become costly or affordable, create problems or solve them.
Common Maintenance Problems
Frequent breakdowns, downtime, and elevated maintenance costs are some of the most typical maintenance issues faced by maintenance managers. These problems can have significant ramifications, including increased costs, reduced asset life, decreased productivity, and even customer dissatisfaction. It’s therefore crucial to identify and address common maintenance problems before they escalate, to maintain efficient asset operations and avoid potential disruptions.
A proactive approach to facility safety and maintenance is key to addressing common maintenance problems. Some solutions include prioritizing and responding to maintenance requests, developing a preventive maintenance plan, implementing preventive maintenance techniques, utilizing IoT to expedite maintenance solutions, and leveraging maintenance management software.
By implementing these strategies and staying vigilant about maintenance issues, you can ensure the continued smooth operation of your assets.
The Role of Maintenance Managers
Maintenance managers play a crucial role in ensuring the optimal performance of an organization’s assets. They must be able to assess situations and act promptly to address any maintenance issues that arise. To accomplish this, maintenance managers must juggle multiple responsibilities, such as budget constraints, asset maintenance requirements, scheduling considerations, and effective tracking procedures.
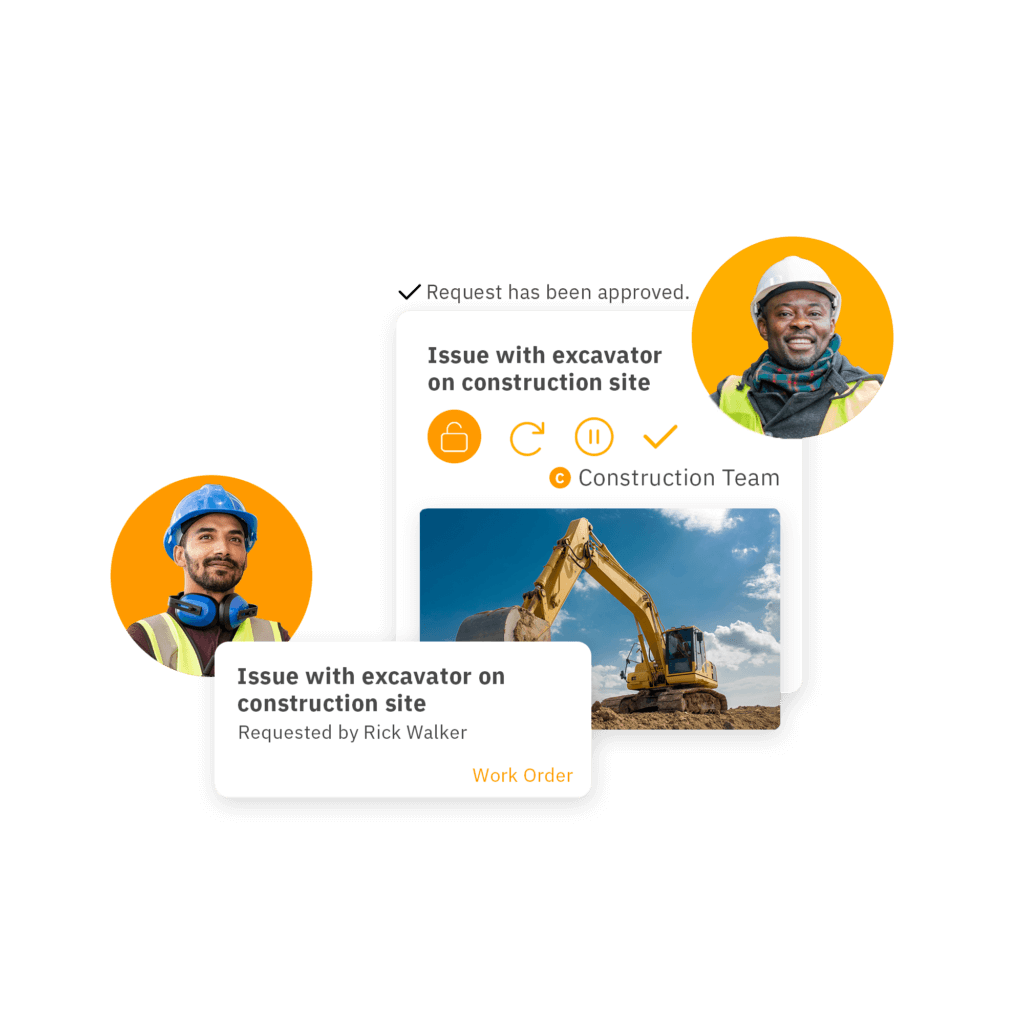
Time planning and asset tracking are particularly important for maintenance managers, as they help ensure that all assets are maintained efficiently and effectively. By staying on top of these tasks, maintenance managers can maximize the availability, utilization, and performance of their organization’s assets, ensuring a smooth-running operation and minimizing the risk of costly disruptions.
Preventive Maintenance Strategies
Preventive maintenance involves creating and executing a strategy to reduce unplanned downtime and extend the service life of assets. It offers numerous benefits, such as minimizing downtime and extending the life of assets, ultimately leading to cost savings and improved operational efficiency.
By developing a preventive maintenance plan and implementing techniques, organizations can proactively address potential maintenance issues before they escalate, ensuring that their assets continue to perform at optimal levels.
The process of developing and implementing a preventive maintenance plan involves identifying assets, creating a maintenance plan, organizing maintenance activities, and tracking performance. Utilizing a Computerized Maintenance Management System (CMMS) software like ToolSense can greatly assist in the development of a preventive maintenance plan, as it provides effective communication and tracking of maintenance activities.
By adopting preventive maintenance strategies, organizations can ensure the continued smooth operation of their assets and minimize the risk of costly disruptions.
We all know that routine maintenance tasks are vital if you want to keep your essential equipment in top shape.
Developing a Preventive Maintenance Plan
An efficient preventive maintenance program encompasses a proactive attitude, training, prevention, prediction, regular corrective action, and stakeholder support. To develop a preventive maintenance plan, organizations must first identify the assets that require maintenance and establish the objectives and priorities of the plan. A CMMS software like ToolSense can be particularly valuable in this process, as it facilitates the tracking and management of maintenance activities, ensuring that all assets are properly maintained.
Once the assets have been identified and the plan has been developed, maintenance managers can then schedule maintenance tasks, verify inventory availability, and organize their maintenance team to ensure the efficient use of time and resources. By staying on top of these tasks with CMMS software, maintenance managers can effectively implement their preventive maintenance plan and ensure the continued smooth operation of their organization’s assets.
Handling Maintenance Issues
Establishing communication channels for maintenance requests is essential for efficiently prioritizing and responding to requests in a timely fashion. By having an on-call maintenance team to address urgent and immediate maintenance tasks, and devising a plan for high urgency and periodic maintenance, organizations can ensure that all maintenance requests are promptly and effectively addressed.
Expert advice
Making it easy to report issues and respond to them is a crucial aspect to successful maintenance management.
Maintenance requests should be prioritized according to urgency and responded to promptly, ensuring that critical assets continue to operate efficiently and minimizing the risk of costly disruptions. By staying on top of these tasks and using tools such as CMMS software, maintenance managers can effectively handle maintenance issues and ensure the smooth operation of their organization’s assets.
Reporting Maintenance Requests with ToolSense
Reporting maintenance issues should be as simple as possible. With ToolSense, you simply scan the QR code that is attached to an asset with your smartphone. A website shows up that guides you through a couple of basic questions. You can add photos, videos, or even voice messages. No account needed, making the process user-friendly and self-explanatory.
Prioritizing and Responding to Maintenance Requests with ToolSense
After an operator reports an issue with one of your assets, ToolSense automatically generates a digital ticket. The responsible employee, for example the site manager, gets notified via e-mail. Reducing unnecessary administrative work with automating even those simple tasks saves you plenty of time down the road.
Using IoT to Solve Maintenance Issues Quickly
The Internet of Things (IoT) has the potential to revolutionize maintenance management by providing real-time monitoring of equipment and assets through the use of IoT devices. This enables organizations to monitor, maintain, and optimize assets to maximize availability, utilization, and performance.
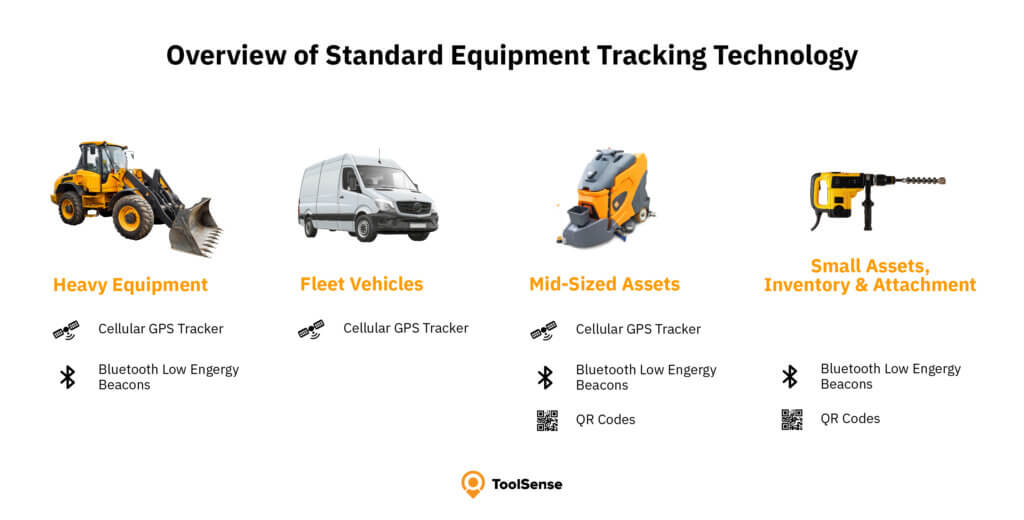
IoT contributes to maintenance management by providing real-time monitoring of equipment and assets through the use of IoT devices. In addition to real-time monitoring, IoT-based predictive maintenance utilizes data collected and analyzed from assets, equipment, or machinery to anticipate potential issues and allow organizations to take preventive measures, thereby reducing unplanned downtime.
IoT data from the ToolSense hardware enables you to create powerful and data-driven workflows. Access parameters like an asset’s runtime or its battery level directly from the ToolSense rules engine.
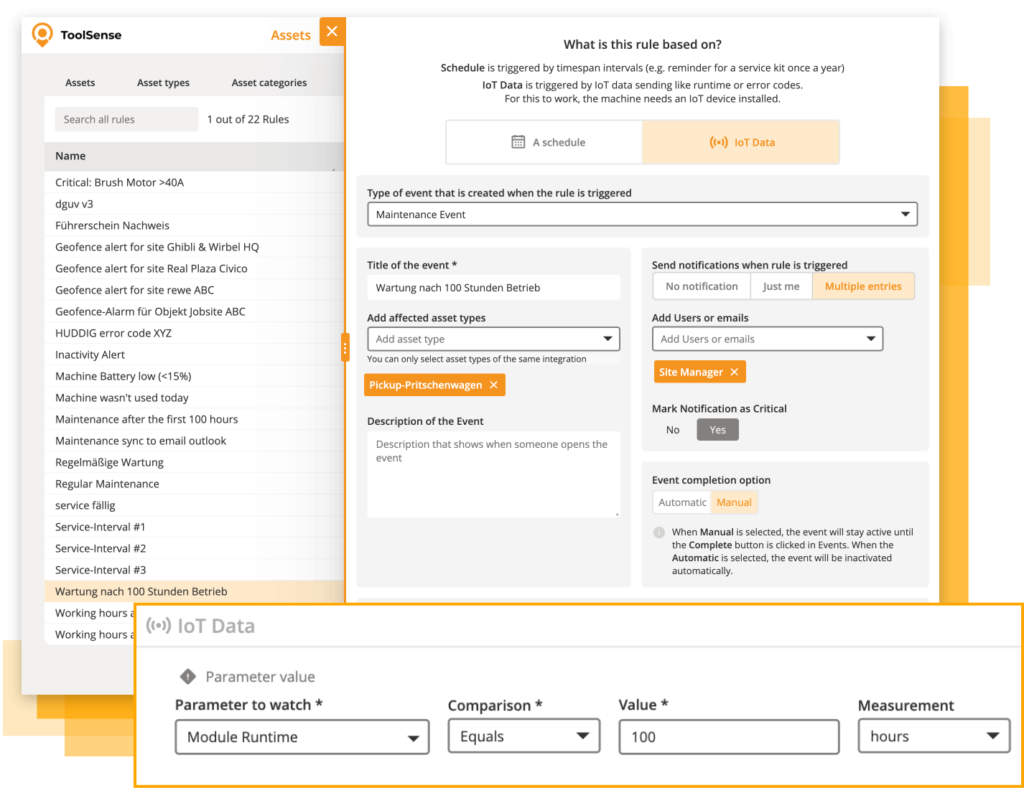
By utilizing IoT for maintenance management, organizations can achieve significant enhancements, including a decrease in maintenance costs and a diminishment in unplanned downtime. Embracing IoT technologies for maintenance management not only helps in optimizing asset performance, but also contributes to the overall success of the organization.
Adopting Maintenance Management Software
Maintenance management software is a computerized system that centralizes maintenance information and facilitates the processes of maintenance operations, thus optimizing the utilization and availability of physical equipment such as vehicles, machinery, communications, plant infrastructures, and other assets. By adopting maintenance management software, maintenance managers can effectively track assets, schedule maintenance tasks, and manage inventory, resulting in improved asset performance and reduced downtime.
When selecting maintenance management software, it is essential to evaluate the features and capabilities of the software, the cost, the user-friendliness, and the customer support provided. Additionally, one should consider the scalability of the software and its ability to integrate with other systems.
By choosing the right maintenance management software, organizations can ensure a successful asset operation, ultimately leading to increased productivity and minimized downtime.
Features of Maintenance Management Software
Maintenance management software typically includes features such as scheduling maintenance, work order management, preventive maintenance, asset tracking, inventory management, and reporting. These features help improve the utilization and availability of physical assets, such as vehicles, machinery, communications, plant infrastructures, and other assets. By utilizing maintenance management software, organizations can effectively manage their assets, ensuring that they remain in optimal working condition.
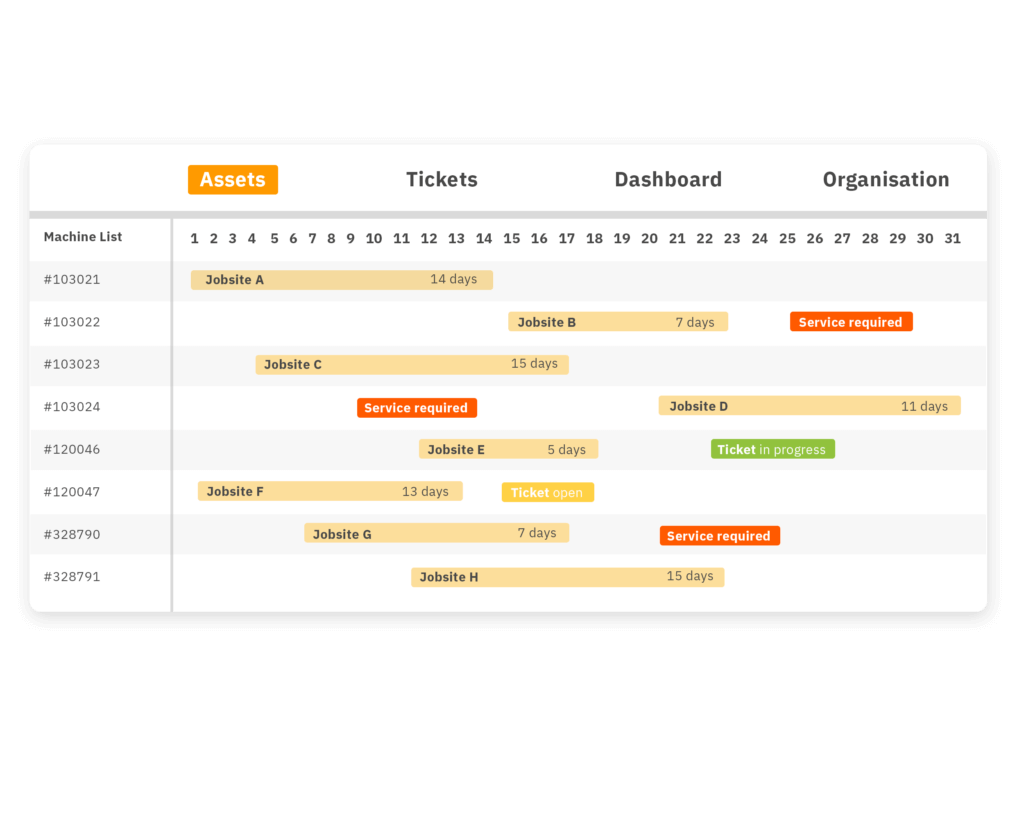
In addition to streamlining the maintenance process, maintenance management software can also assist in asset tracking and maintenance scheduling. By providing accurate and up-to-date information on the status of each asset, maintenance managers can make informed decisions about when and how to schedule maintenance tasks, ensuring that all assets are properly maintained and minimizing the risk of costly disruptions.
Choosing the Right Maintenance Management Software
Selecting the most suitable maintenance management software is essential for a successful asset operation. When evaluating different software options, it’s important to consider factors such as customizability, scalability, deployment options, license pricing model, data importation, training, technical support, software updates, and comprehensive maintenance management functionality. The prioritization of these factors may be influenced by the organization’s specific requirements and objectives, such as the size of operations, number of technicians, types of assets, and cost of equipment failure.
ToolSense is trusted by 700+ companies
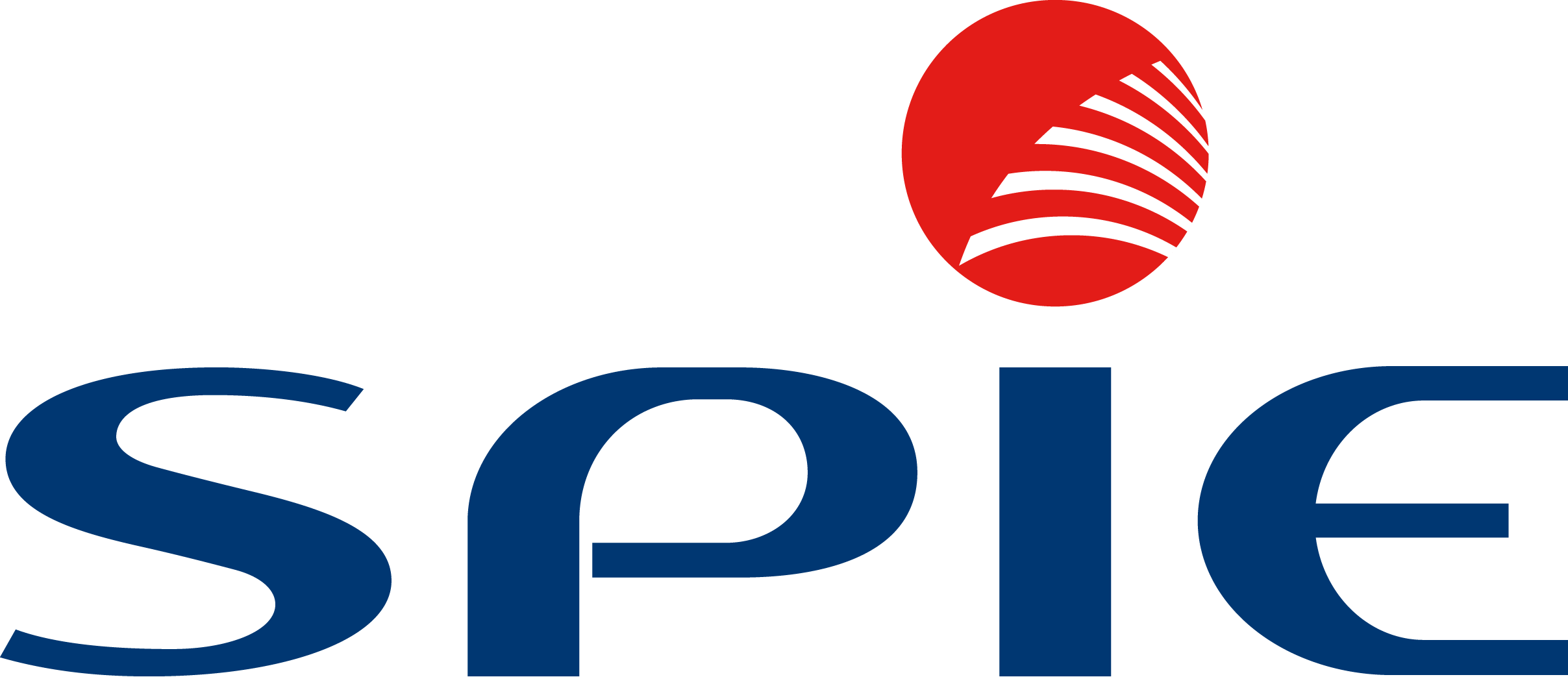
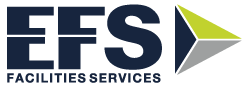
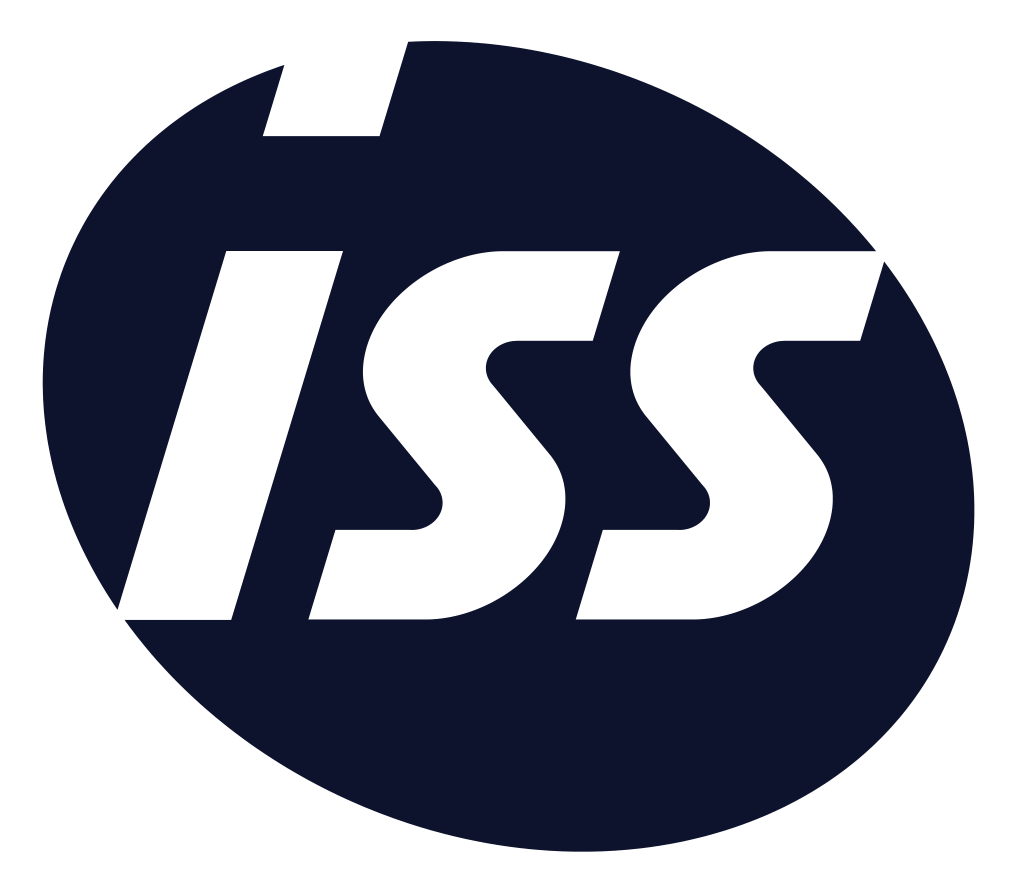
By carefully considering these factors and selecting the most suitable maintenance management software for their organization, maintenance managers can ensure that their assets are well-maintained and operating at peak efficiency. Ultimately, choosing the right maintenance management software is essential for the smooth operation of any organization’s assets, leading to increased productivity and minimized downtime.
Summary
In summary, solving common maintenance issues for smooth asset operation involves understanding the challenges faced by maintenance managers, adopting preventive maintenance strategies, utilizing IoT technology, and choosing the right maintenance management software. By addressing these aspects, organizations can ensure that their assets are well-maintained, operating efficiently, and providing maximum value to their operations.
With the right tools and strategies in place, organizations can proactively address maintenance issues, minimize disruptions, and ultimately improve their overall operational efficiency. By investing in maintenance management and embracing the latest technological advancements, organizations can ensure a successful asset operation and a brighter future.
Frequently Asked Questions
Maintaining your equipment is a crucial step in keeping it running safely and efficiently. Here are 5 examples of preventive maintenance in action: Regularly inspecting and changing filters; lubricating components to reduce friction; monitoring fluid levels; checking for signs of wear or damage; and performing scheduled maintenance according to the manufacturer’s recommendations. With proper maintenance, your equipment can run better for longer—so don’t forget to take the time to give it some care!
Maintenance examples include inspecting and replacing worn parts, lubrication, repairs, and preventative maintenance such as regular cleaning and monitoring. Regular maintenance can greatly extend the lifetime of an asset, improve performance, and make it more reliable eventually.
By utilizing IoT in maintenance management, organizations can quickly identify and solve maintenance issues, resulting in reduced downtime and extended asset life. Examples of how IoT can be used to quickly identify and solve maintenance issues include using sensors to detect equipment failure and leveraging AI to predict maintenance needs.
Maintenance management software typically includes features such as scheduling maintenance, work order management, preventive maintenance, asset tracking, inventory management, and reporting. These features help improve the utilization and availability of physical assets, such as vehicles, machinery, communications, plant infrastructures, and other assets. By utilizing maintenance management software, organizations can effectively manage their assets, ensuring that they remain in optimal working condition.
This article was generated using AI technology and edited and fact-checked by our editorial staff.