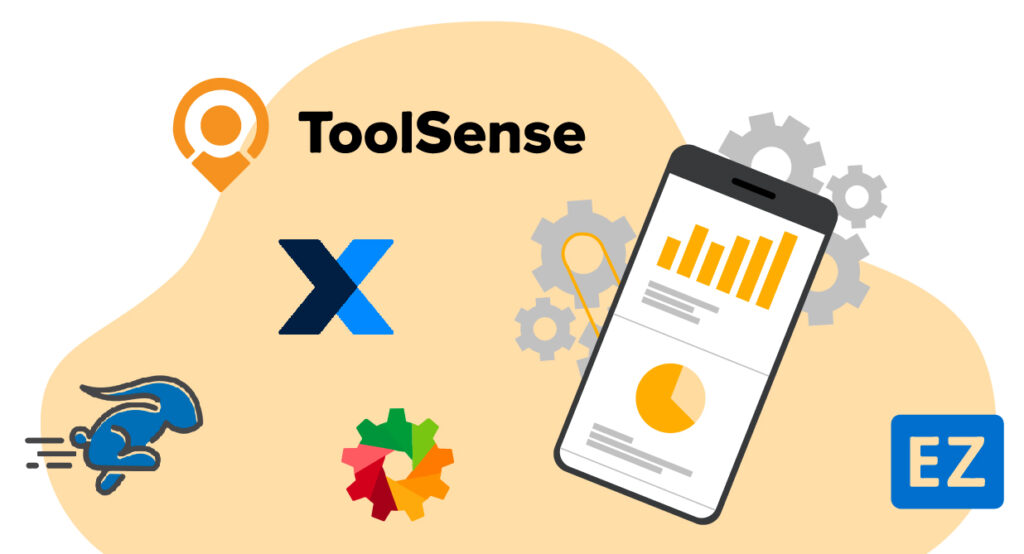
Are you struggling to keep up with complex maintenance schedules and asset management? The right maintenance management software can be your solution. Whether you’re a maintenance manager seeking to streamline operations or an organization aiming to enhance efficiency, the perfect repair and maintenance software is out there. We’ll help you navigate the options, ensuring you find a maintenance software program that not only addresses your unique challenges but also stands out in the realm of maintenance software management.
Our Top Picks
Key facts
- ToolSense leads the ranking of best maintenance management software solutions, with a special focus on IoT integration, QR code system, and cross-industry usability.
- Maintenance management software helps companies reduce unplanned downtime by up to 75% and save 20% on maintenance costs.
- The most important features of modern maintenance management software are work order management, preventive maintenance, and asset management including complete equipment oversight.
What Is Simple Maintenance Software?
Maintenance software is a system that consolidates all maintenance-related data and offers features to streamline the entire maintenance management process. This software is utilized by organizations across industries and sizes to:
- Optimize maintenance activities
- Boost efficiency
- Reduce costs
- Minimize downtime, including preventive maintenance tasks.
Various types of repair and maintenance software are available to cater to different requirements, such as computerized maintenance management software (CMMS), enterprise asset management (EAM), enterprise resource planning (ERP), and asset performance management (APM). These systems offer key features such as tracking overall equipment effectiveness (OEE), OSHA-related incident tracking, work order assignments based on staff availability, preventive maintenance scheduling, mobile work order management, and project management tools – all aimed at reducing maintenance costs.
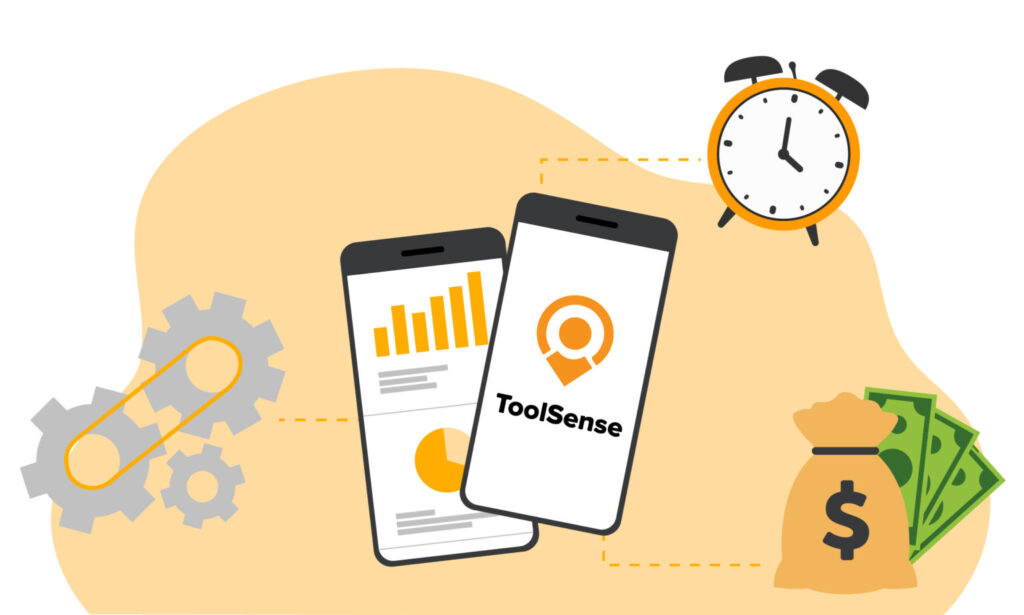
Overview: Best Simple Maintenance Management Software Solutions (Top 6)
In this overview, we will be introducing the top maintenance management software solutions in the market, each excelling in different aspects to cater to various organizational requirements. Read on to discover the best solution for your organization’s maintenance needs.
ToolSense (#1)
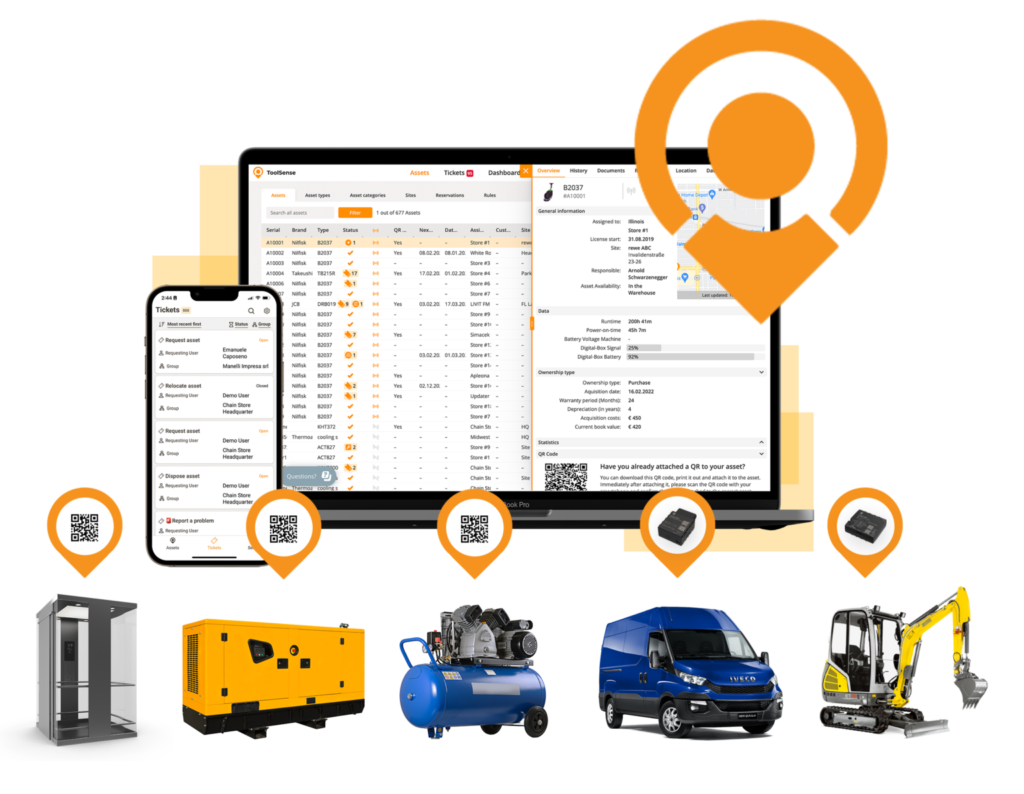
ToolSense is a robust and user-friendly CMMS and repair and maintenance software, meticulously designed to assist businesses and maintenance managers in managing maintenance processes for a wide array of equipment. What sets ToolSense apart is its ability to:
- Provide comprehensive visibility into your maintenance processes through a centralized repository. This feature ensures that you have quick and easy access to the complete history of each asset, maintenance schedules, and other vital details. This level of transparency is critical in making informed decisions and planning future maintenance strategies.
- Optimize equipment uptime, streamline maintenance operations, and significantly reduce costs. By enhancing equipment uptime, businesses can avoid unexpected downtimes that can negatively impact productivity and customer satisfaction. Moreover, streamlined maintenance operations mean your team can work more efficiently, saving time and resources.
- Cater to teams across various industries, including construction, facility management, aviation, healthcare, and hospitality. This versatility makes it an ideal solution regardless of your industry or the complexity of your maintenance needs.
Essential features are:
- Enterprise Preventive Maintenance Software
- Reporting & Analytics
- Easy-to-Use QR Code & Ticket System
- Maintenance & Repair Tracking & Planning
- Create Powerful Maintenance Workflows
- Independence from Manufacturers
- Comprehensive visibility into maintenance processes
- Asset tracking and inventory management
Pros:
- ToolSense leads the ranking of best simple maintenance management software solutions, with a special focus on IoT integration, QR code system, and cross-industry usability.
- Maintenance management software helps companies reduce unplanned downtime by up to 75% and save 20% on maintenance costs.
- The most important features of modern maintenance management software are work order management, preventive maintenance, and asset management including complete equipment oversight.
- While affordable solutions start at around $35-50 per user/month, enterprise solutions like ToolSense offer individualized pricing models for larger companies.
Cons:
- Free users are limited to a 30-day trial. However, this trial period allows potential users to explore and understand the software’s capabilities before making a commitment.
- Feature-rich and comprehensive interface, which might take some time to get used to
- QR code solution is dependent on internet connectivity
Pricing:
Free 30-day trial available. There is also an option for a free personal tour as guided walk-through to get to know the software. All prices are individualized and tailored to the specific needs of each customer and available upon request.
Rating:
- Functionality: 4.5/5
- Ease of Use: 4.5/5
- Integration: 5/5
- Support: 5/5
- Value for Money: 5/5
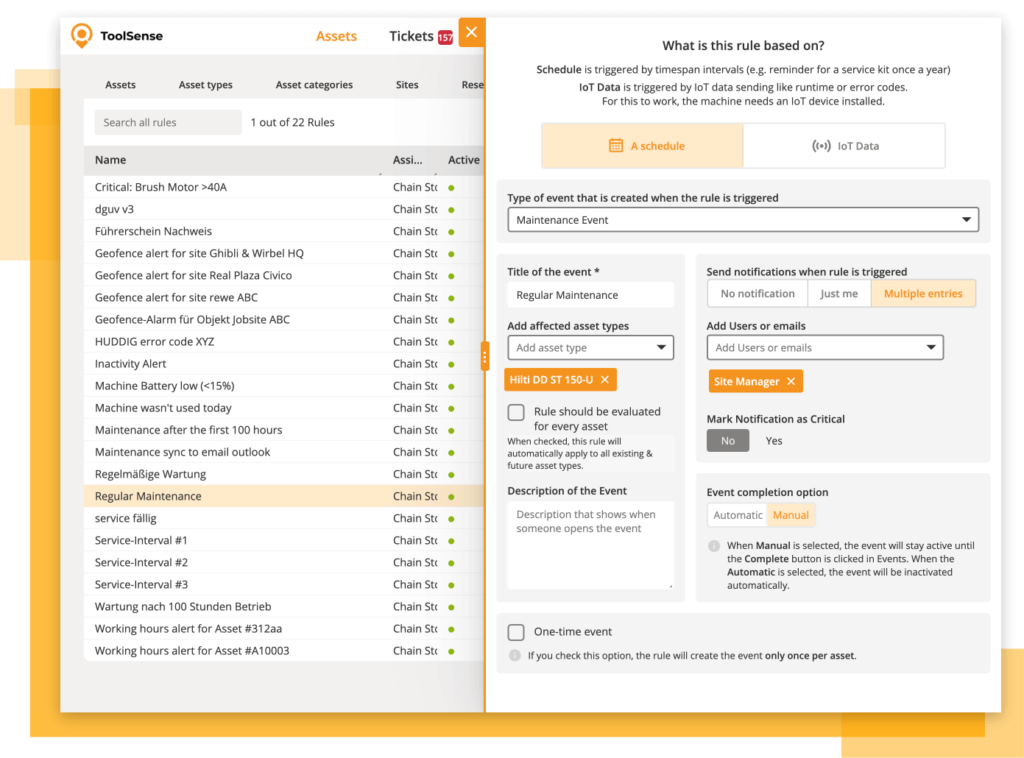
ToolSense has demonstrated its versatility and effectiveness across a wide spectrum of industries. Here are some of the key sectors where ToolSense has been successfully integrated and provided significant value:
- Construction: In the construction industry, ToolSense helps manage and schedule routine maintenance for heavy machinery and tools, ensuring optimal uptime and reducing unexpected breakdowns that can delay projects.
- Facility Management: For facility management, ToolSense provides efficient tracking of all maintenance tasks, from HVAC systems to elevators, ensuring a smooth operation and comfortable environment for occupants.
- Healthcare: In healthcare facilities, ToolSense ensures medical equipment is kept in optimal condition, contributing to patient safety and effective treatment outcomes.
- Hospitality: For the hospitality industry, ToolSense helps maintain everything from kitchen equipment to guest amenities, ensuring an excellent guest experience and high customer satisfaction rates.
In each of these industries, ToolSense has been recognized for its user-friendly interface, comprehensive maintenance management features, and the ability to customize the software to meet unique industry needs.
ToolSense is trusted by 700+ companies
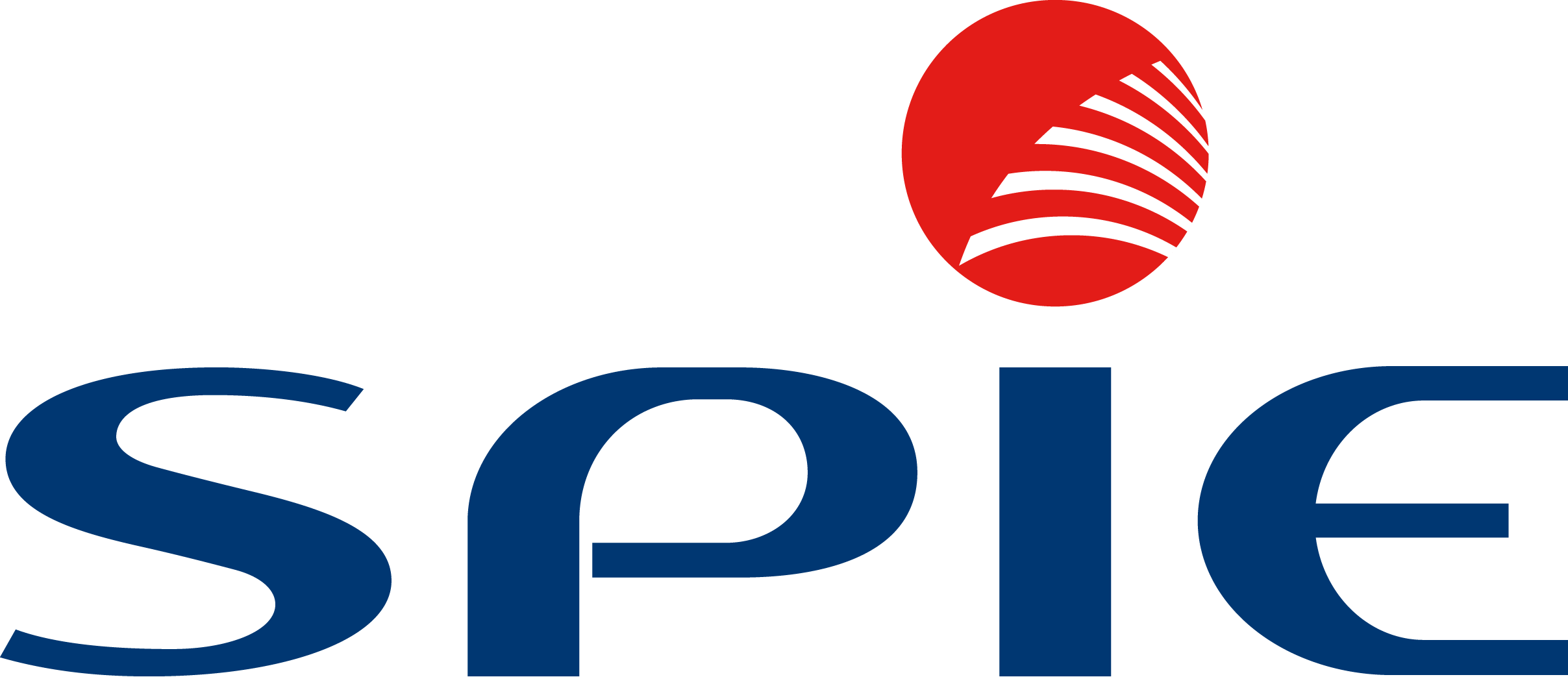
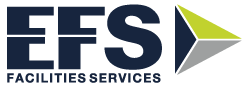
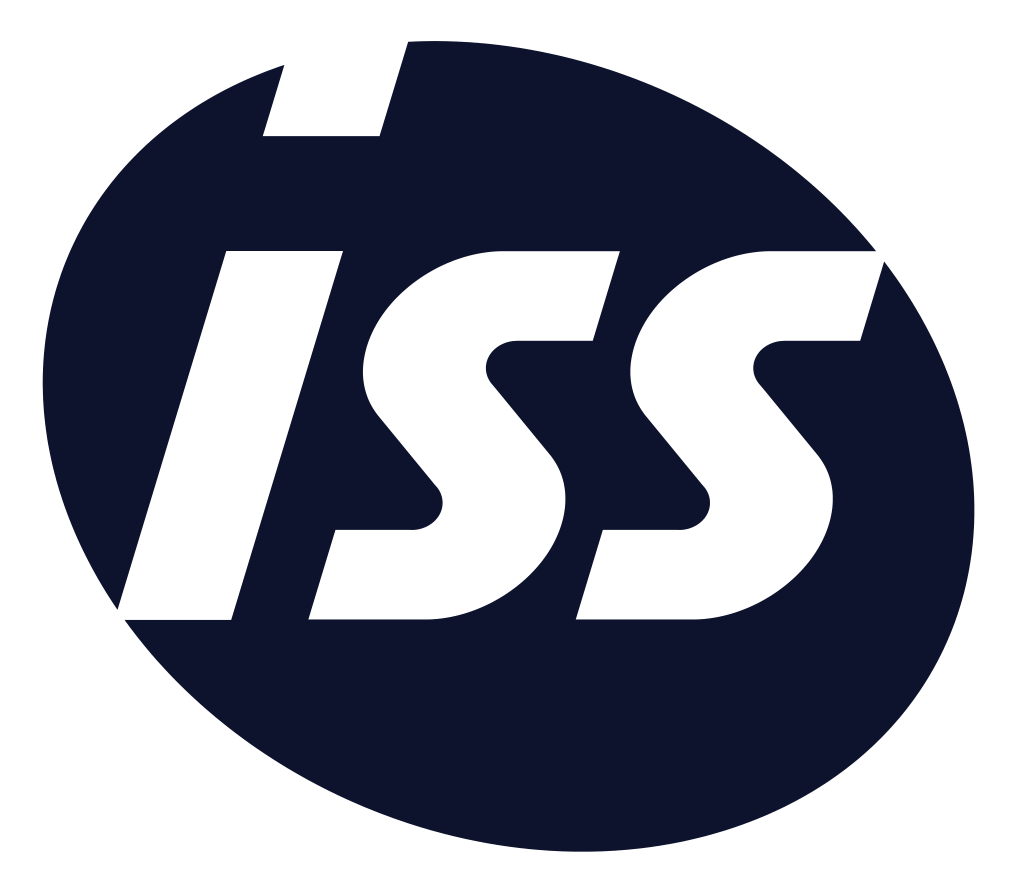
MaintainX (#2)
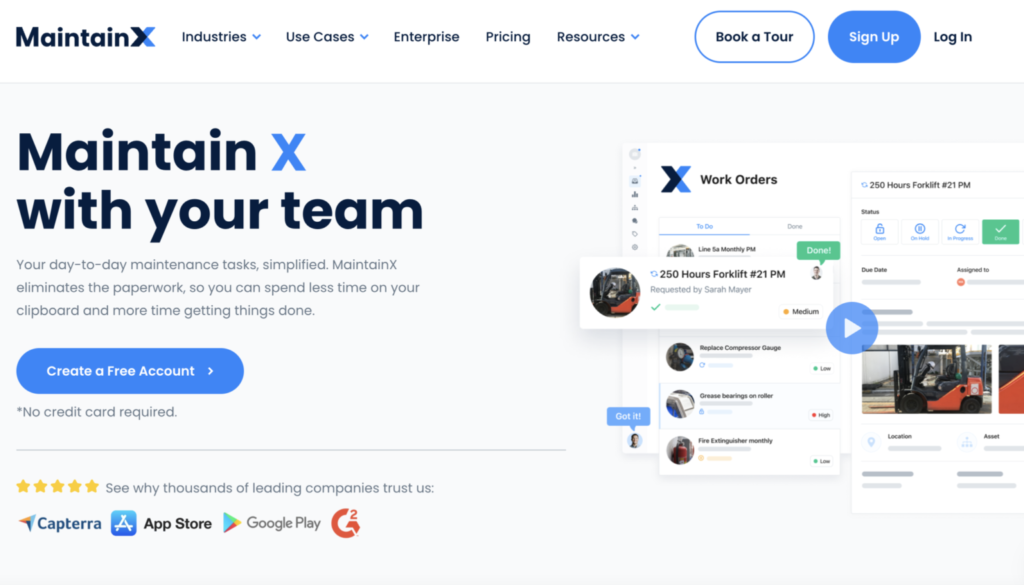
MaintainX is a mobile-first maintenance planning software that focuses on simplifying maintenance, safety, and operations. It helps companies in various industries improve equipment uptime by connecting people and data. With MaintainX, you can create, assign, and monitor work orders and work requests, Schedule preventive maintenance tasks, manage checklists and inspections, track parts inventory and more.
Essential Features are:
- Maintenance, safety, and operations management
- Equipment uptime improvement
- Work order creation and monitoring
- Preventive maintenance scheduling
- Parts inventory tracking
Pros:
- Simplifies maintenance, safety, and operations
- Improves equipment uptime
- User-friendly interface for seamless transition from paper or other CMMS
- Boosts productivity and collaboration
Cons:
- Limited customization options
- No geolocation feature
- No integration to IoT-technologies (Internet of Things)
- Asset Management only on surface level
- No QR code / NFC tag technology
- Limited access to API
Pricing:
Various pricing plans are available, from Basic to Enterprise. The Essential plan is available for $16 per user/month, and the premium plan is offered at $49 per user/month. For larger organizations, there is an Enterprise plan with a custom pricing model. A free plan is also available for smaller teams.
Rating:
- Various pricing plans are available, from Basic to Enterprise. The Essential plan is available for $16 per user/month, and the premium plan is offered at $49 per user/month. For larger organizations, there is an Enterprise plan with a custom pricing model. A free plan is also available for smaller teams.
Limble CMMS (#3)
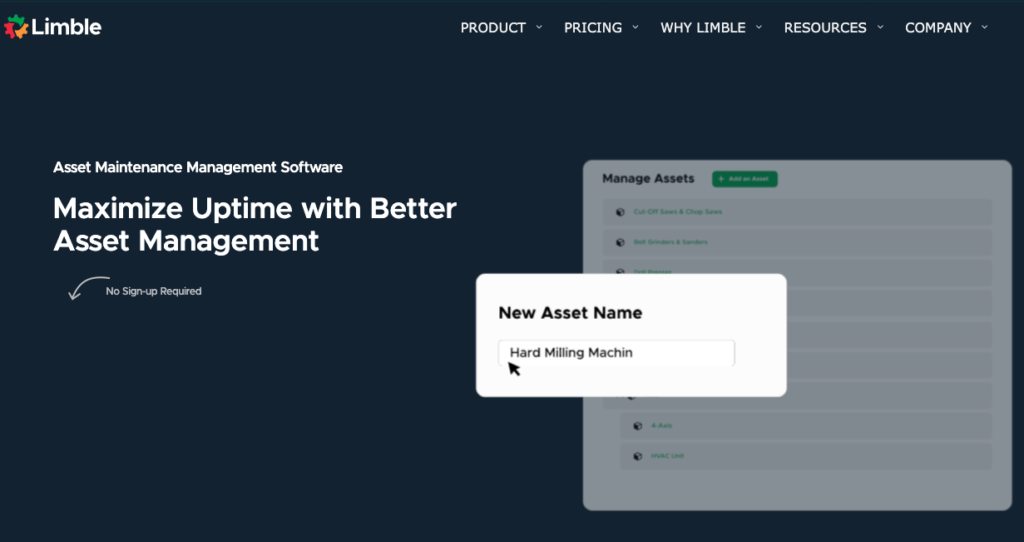
Limble CMMS is a mobile-first maintenance management software that focuses on preventive maintenance and asset management. It provides users with easy-to-use mobile apps for technicians to quickly perform tasks and stay updated on maintenance activities, inventory, and asset management. Limble CMMS also offers a comprehensive module for enterprise asset management, making it a suitable choice for organizations looking to optimize their maintenance operations and asset performance.
Essential Features are:
- Mobile Maintenance App
- Work Orders management
- Preventative Maintenance
- Asset Management
- Work Requests management
- Reports and Dashboards
- Parts/Inventory Management
- Predictive Maintenance
Pros:
- Emphasis on preventive maintenance and asset management
- Easy-to-use mobile apps for technicians
- Comprehensive module for enterprise asset management
- Automatic syncing of maintenance work orders across all devices
Cons:
- Slightly higher price point compared to other solutions
- Challenging Mobile-Version
- Limited customization options
- The back end was not designed as an asset based CMMS
- No integration to IoT-technologies (Internet of Things)
- Asset Management only on surface level
- No QR code / NFC tag technology
Pricing:
Free basic plan available. Standard for $23 per user/month. Premium+ for $59 per user/month. Enterprise only on demand.
Rating:
- Functionality: 4.5/5
- Ease of Use: 4.5/5
- Integration: 4/5
- Support: 4/5
- Value for Money: 4/5
eMaint CMMS (#4)
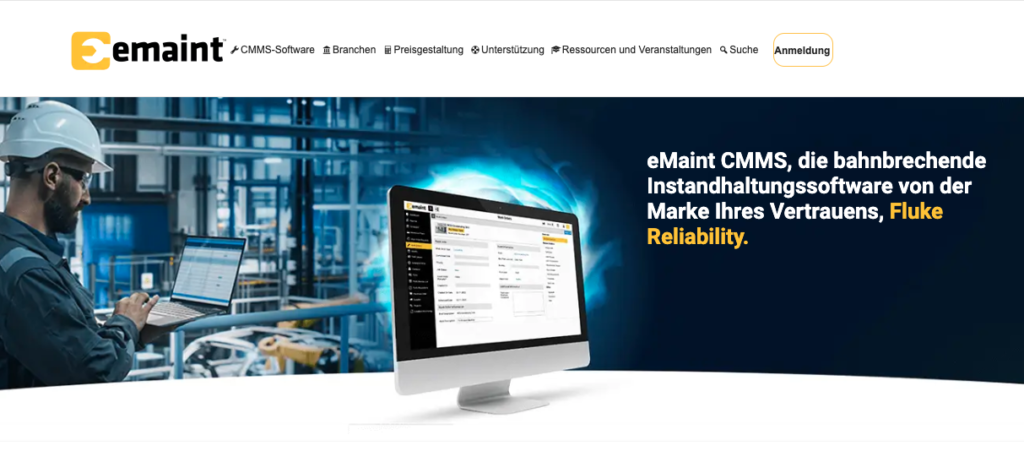
eMaint is a comprehensive CMMS that offers a wide range of features to help organizations streamline their maintenance management process. With its efficient work order management, preventive maintenance scheduling, and comprehensive reporting and analytics capabilities, eMaint provides a complete solution for managing maintenance tasks and improving asset performance. The software is trusted by users across various industries, making it a popular choice for organizations looking to enhance their maintenance operations.
Essential Features are:
- Work order management
- Preventive maintenance scheduling
- Comprehensive reporting and analytics
- Asset tracking and management
- Inventory management
Pros:
- Centralizes and optimizes maintenance operations
- Comprehensive reporting and analytics
- Work order management should be efficient.
- Managing work orders with efficiency helps to save time and resources.
- Preventive maintenance scheduling
Cons:
- Pricing information not readily available
- The interface may feel outdated compared to newer solutions
- Some features may require additional purchases
- No integration to IoT-technologies (Internet of Things)
- Asset Management only on surface level
- No QR code / NFC tag technology
Pricing:
No unconditional free trial available (Sales-Contact necessary). Prices start at $69 per user per month in the „3 User Package“.
Rating:
- Functionality: 4.5/5
- Ease of Use: 4/5
- Integration: 4.5/5
- Support: 4/5
- Value for Money: 4/5
EZOfficeInventory (#5)
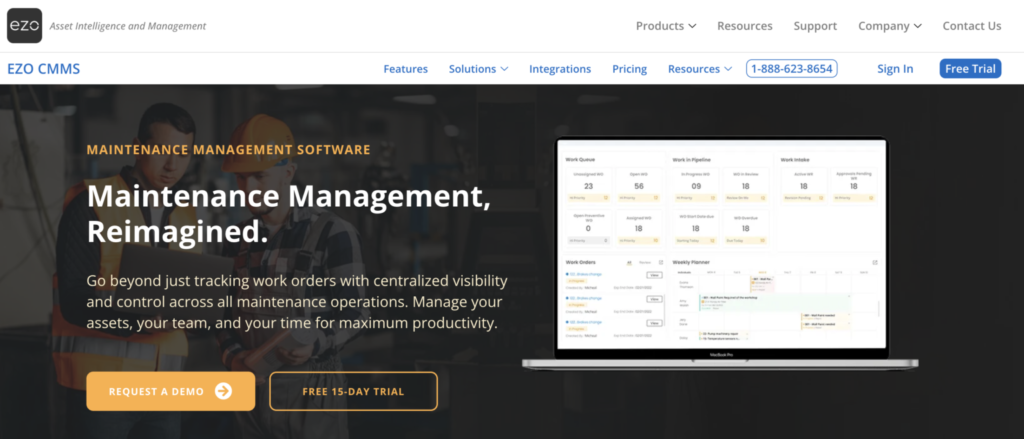
EZOfficeInventory is a comprehensive asset and maintenance management solution designed to meet the needs of businesses of all sizes. With EZOfficeInventory, organizations can track and manage their assets, streamline maintenance operations, and optimize equipment rental processes. The software offers features such as centralized control over maintenance operations, coordinated communications and data management, historical data and analytics for insights, and preventive maintenance workflows.
Essential Features are:
- Asset and maintenance management
- Centralized maintenance operations control
- Coordinated communications and data management
- Historical data and analytics
- Preventive maintenance workflows
Pros:
- Centralized control over maintenance operations
- Coordinated communications and data management
- Historical data and analytics for insights
- Preventive maintenance workflows
Cons:
- Pricing may be higher for smaller businesses
- Limited integrations with other software
- Lacks some advanced features offered by competitors
- No work order management
- No ticketing
- No checklist creation
- No inventory & parts management
Pricing:
Free 15-day trial; $35/month for Essential plan, $45/month for Advanced plan, $55/month for Premium plan. Contact sales for custom enterprise quota.
Rating:
- Functionality: 4/5
- Ease of Use: 4.5/5
- Integration: 4/5
- Support: 4/5
- Value for Money: 4/5
Timly (#6)
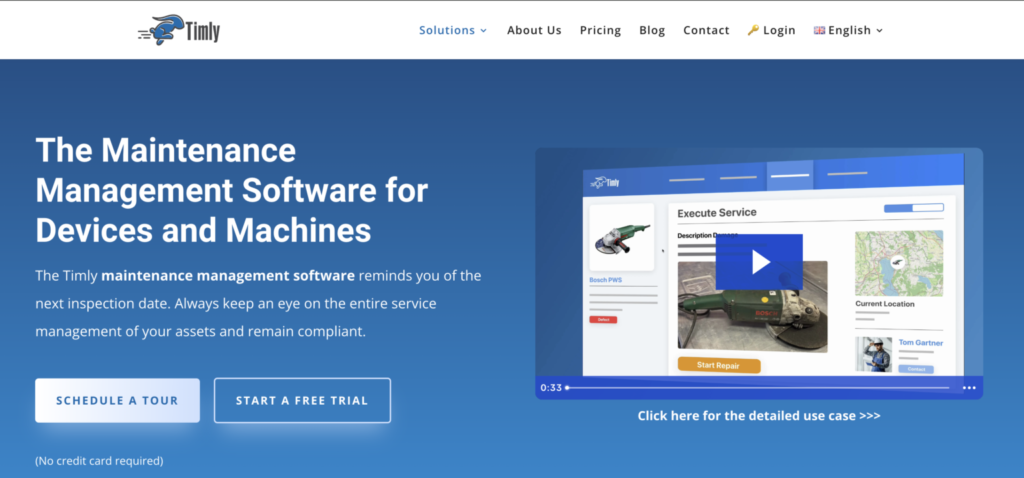
Timly is a digital maintenance planning software designed for modern businesses. It provides a comprehensive overview of your equipment, machines, and systems, allowing you to efficiently manage and schedule maintenance tasks. With Timly, you can easily track upcoming inspection dates and ensure compliance with service management regulations. The software is suitable for companies from different industries, including IT, furniture, tools, machinery, vehicle fleet, and facilities.
Essential Features are:
- Digital maintenance planning
- Equipment, machines, and systems overview
- Inspection date tracking
- Service management regulation compliance
Pros:
- Efficient management and scheduling of maintenance tasks
- Easy tracking of upcoming inspection dates
- Ensures compliance with service management regulations
- Suitable for various industries
Cons:
- Pricing information not available
- Limited customer support outside of business hours
- Additional features may come with extra costs
- May not integrate well with some existing systems
- No ticketing or work order management
- No integrated checklists etc.
- No integration to IoT-technologies (Internet of Things)
- Asset Management only on surface level
- Not enterprise-ready (SSO etc.)
- No checklist creation
Pricing:
Free Trial available. Plans start from 145/month (Essentials+) and offer all access for unlimited users.
Rating:
- Functionality: 4/5
- Ease of Use: 5/5
- Integration: 4/5
- Support: 4/5
- Value for Money: 3/5
How Does Maintenance Management Software Improve Operations?
Functionality & Use: Computerized Maintenance Management Software (CMMS) automates and manages work orders, preventive maintenance, and asset tracking, leading to increased efficiency and minimized downtime. It’s mobile functionality allows quick task execution and real-time updates on activities, inventory, and asset management.
Central Repository: CMMS acts as a central database for all maintenance-related data, including history and work order statuses. This comprehensive data storage aids in informed decision-making and optimizing maintenance operations.
Key Purposes: CMMS is designed to:
- Organize and streamline maintenance activities.
- Plan and schedule preventive maintenance.
- Track equipment efficiency and maintenance tasks.
- Analyze operations for continuous improvement.
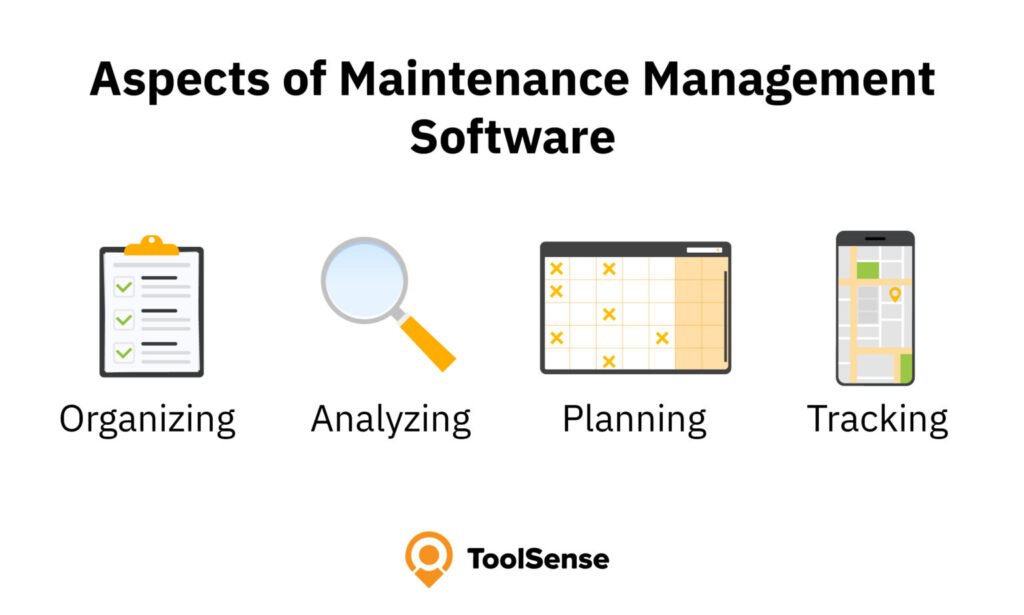
Benefits Across Industries: Used by diverse organizations, CMMS contributes to:
- Enhanced connection and visibility of maintenance operations.
- Cost optimization and downtime reduction.
- Effective tracking of equipment effectiveness (OEE) and compliance (e.g., OSHA incident tracking).
- Efficient management of work orders, maintenance schedules, and projects.
Features: Notable features of CMMS include:
- (Mobile) work order management for on-the-go task handling.
- Project management tools for comprehensive maintenance oversight.
- Dispatch management and interoperable platforms for seamless operations.
By leveraging these capabilities, CMMS turns maintenance planning into a strategic advantage for any organization, irrespective of its size or industry.
Different Types of Simple Maintenance Software
There is a wide variety of maintenance programs available, ranging from simple to complex systems. Basic systems are designed to handle work orders and requests effectively. On the other hand, enterprise asset or computerised maintenance management systems (EAM/CMMS) cover all maintenance activities like stock management and reporting.
Asset Performance Management (APM) solutions optimize asset dependability and accessibility by gathering and analyzing real-time data to evaluate value and risk.
Enterprise Asset Management (EAM) software provides an overview of a facility’s assets throughout their lifespan, while Enterprise Resource Planning (ERP) software facilitates the management of day-to-day business activities and the exchange of data between processes, including maintenance.
Parts & Inventory Management (IM) software supports the acquisition and distribution of products through purchase orders, data connectivity, and the tracking of stored materials.
Work Order Management Software (WO) software focuses on measuring adjustable KPIs, creating templates for faster data collection, scheduling repeat orders to remind technicians of vital equipment maintenance and capturing real-time values and eliminating the need for paper records.
This provides a more efficient and environmentally friendly approach to managing preventative maintenance tasks and handling maintenance requests.
Understanding Key Features of Simple Maintenance Management Software
Having explored the various types of maintenance software, let’s now delve into the key features that these tools generally (should) offer overall. Maintenance management software typically provides a comprehensive suite of features, including:
- Work order management
- Comprehensive asset histories
- Inventory management
- Maintenance history
- Maintenance reporting
- Preventive maintenance scheduling
- Capability to enable the maintenance team
By offering these features, these software solutions aim to optimize the availability, utilization, and reliability of equipment, keeping assets in optimal working condition and reducing the risk of costly downtime. Implementation of a maintenance management software solution that aligns with the specific needs of an organization enables maintenance teams to operate smoothly, efficiently, and cost-effectively.
How to Choose the Right Computerized Maintenance Management Software (Buyers Guide)
In the selection of the best maintenance planning software for your organization, consider the following factors:
- Features and capabilities
- Level of vendor support
- Integration with existing systems
- Software’s scalability to include other maintenance functions
- Pricing
In evaluating the cost-effectiveness of maintenance management software, consider factors like:
- Functionality
- Usability
- Customizability
- Scalability
- Potential for integration
- Mobile availability
- Total cost of ownership
- ROI
- Technical assistance
- User feedback
Taking these factors into account will ensure your investment in a software solution that offers the best value for money.
The cost of maintenance management software varies between providers and is typically contingent on the number of users and the feature package. Prices usually range from $35 to $150 per user per month, while pay-per-license models generally range from $500 to $8,000. To get the most out of your investment, it’s crucial to choose a software solution that offers the features and support your organization needs while staying within budget.
To help you make an informed decision, we have compiled a list of the top maintenance management software solutions, along with a summary of their key features and estimated pricing.
Conclusion: Comparison of the 6 Best Simple Maintenance Management Software
By considering the unique needs of your organization, you can choose the best simple maintenance management software that will optimize your maintenance operations and improve overall efficiency.
As our analysis has shown, ToolSense stands out as the leading solution due to its unique combination of features: comprehensive visibility into maintenance processes, advanced IoT integration, and an easy-to-use QR code system. The platform’s versatility makes it ideal for various industries, from construction to facility management and healthcare.
What truly sets ToolSense apart is its ability to help organizations achieve tangible results – reducing unplanned downtime by 75% and saving 20% on machine and maintenance costs. The software’s user-friendly interface, coupled with powerful features like asset tracking, work order management, and preventive maintenance scheduling, makes it a comprehensive solution for modern maintenance challenges.
Managing maintenance across an entire fleet is quite a challenge. Build custom workflows in our Asset Operations Platform to easily manage maintenance processes for thousands of assets.
FAQs
ToolSense centralizes all asset data, streamlines maintenance workflows, and reduces costs by minimizing downtime through real-time tracking and automated processes.
Yes, ToolSense includes features like preventive maintenance scheduling and automated reminders, ensuring equipment stays in optimal condition while reducing unexpected breakdowns.
ToolSense uses IoT integrations, QR codes, and GPS tracking to provide real-time insights into the location and usage of assets, even for equipment across multiple sites.
Absolutely. ToolSense caters to various industries, such as construction and facility management, and is suitable for businesses of all sizes thanks to its customizable features and easy onboarding.
The software solutions and the respective rankings presented in this article reflect both our opinion and that of our customers. While we can’t claim to have looked at them with complete objectivity, we do believe we offer a top-notch solution. Not convinced yet? We warmly invite you to form your view during our complimentary 30-day trial period.