Facility Services
Improve the Efficiency of Your Operations with ToolSense
Managing a successful cleaning operation requires efficiency, transparency, and reliability. Yet, outdated processes that rely on Excel, pen and paper and email lead to bottlenecks that hold facility services companies back from achieving their full potential.
If the video embed isn’t working as expected, please find the full video here.
Are these your challenges?
- Struggling to track essential tools like vacuum cleaners, scrubbers, single-disc machines, or cleaning robots across multiple locations.
- Frequent equipment breakdowns caused by reactive maintenance or inconsistent servicing schedules.
- Managing fragmented IoT systems like Kärcher Fleet, Taski IntelliTrail, Hako Fleet, or various Cleaning Robot Clouds (e.g. LionsBot or Pudu) that don’t integrate with each other.
- Finding it difficult to meet safety and compliance standards, such as electrical checks, with outdated, manual processes that rely on Excel and paper.
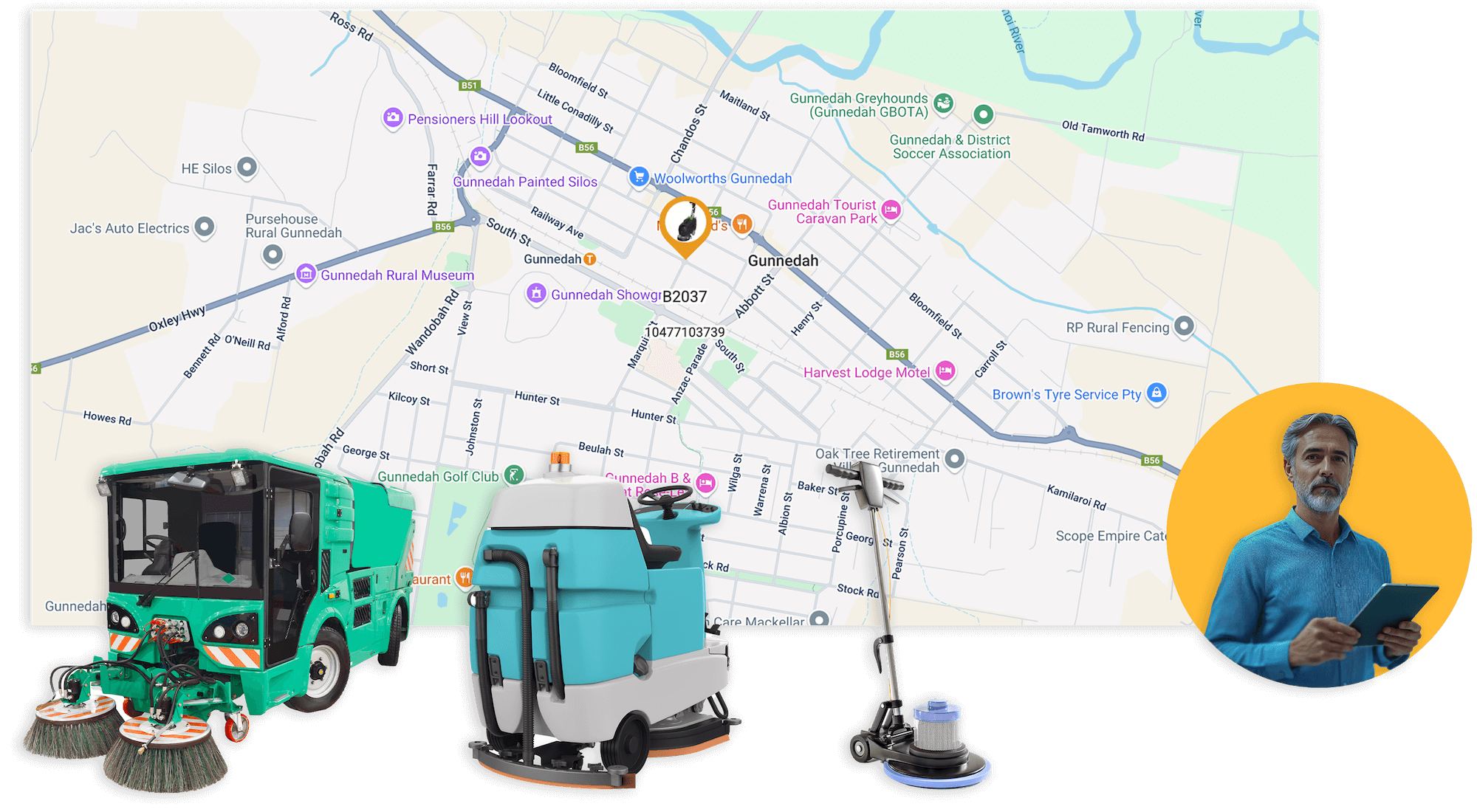
Ready to ditch Excel and Paper?
Join 700+ Operations, Maintenance & Repair Teams Simplifying Their Daily Business
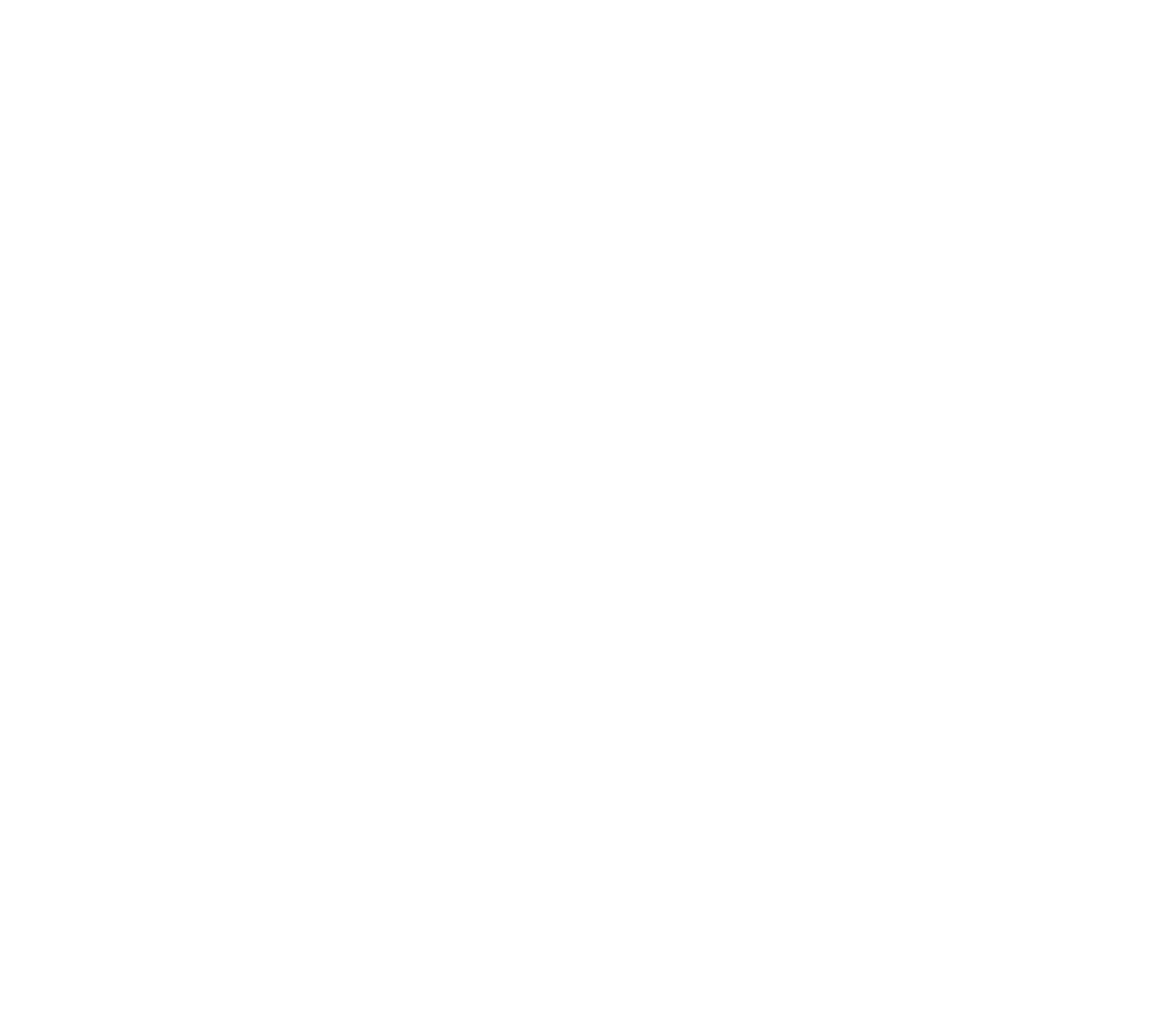
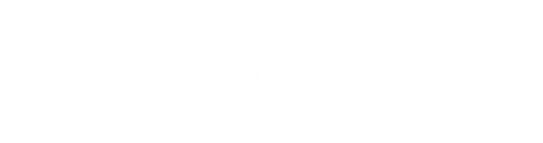
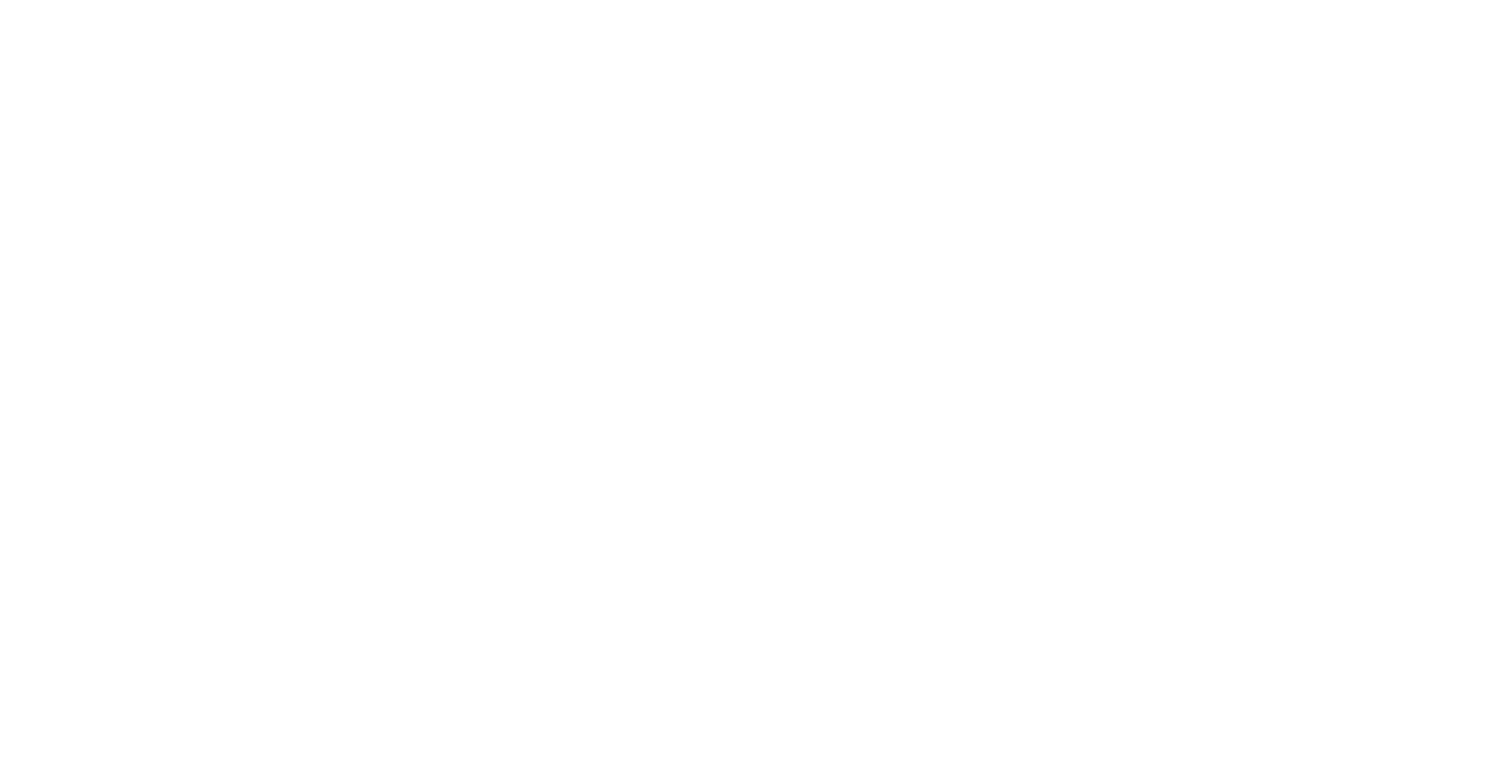
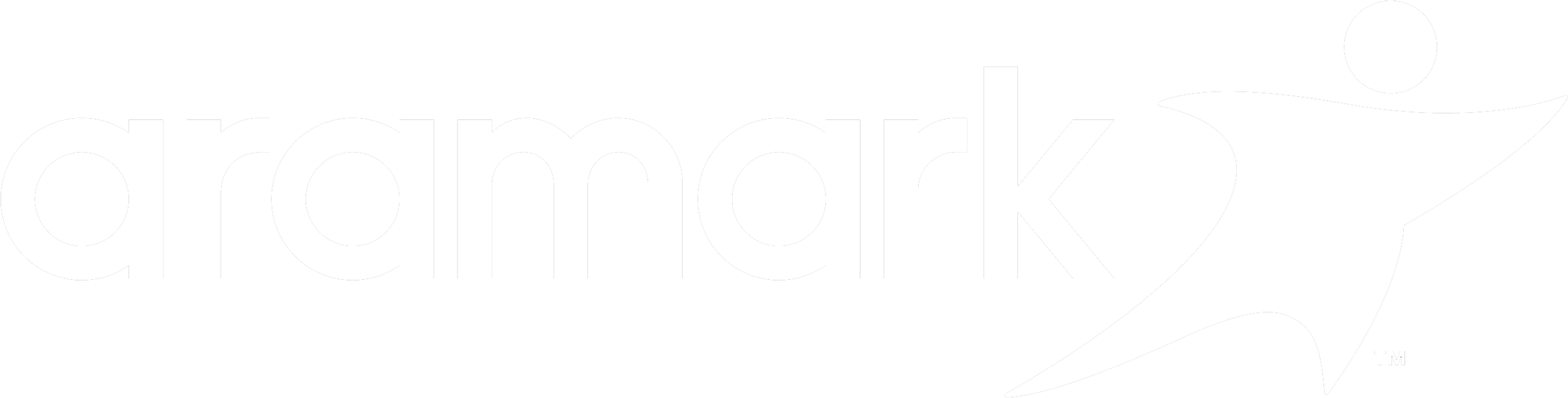
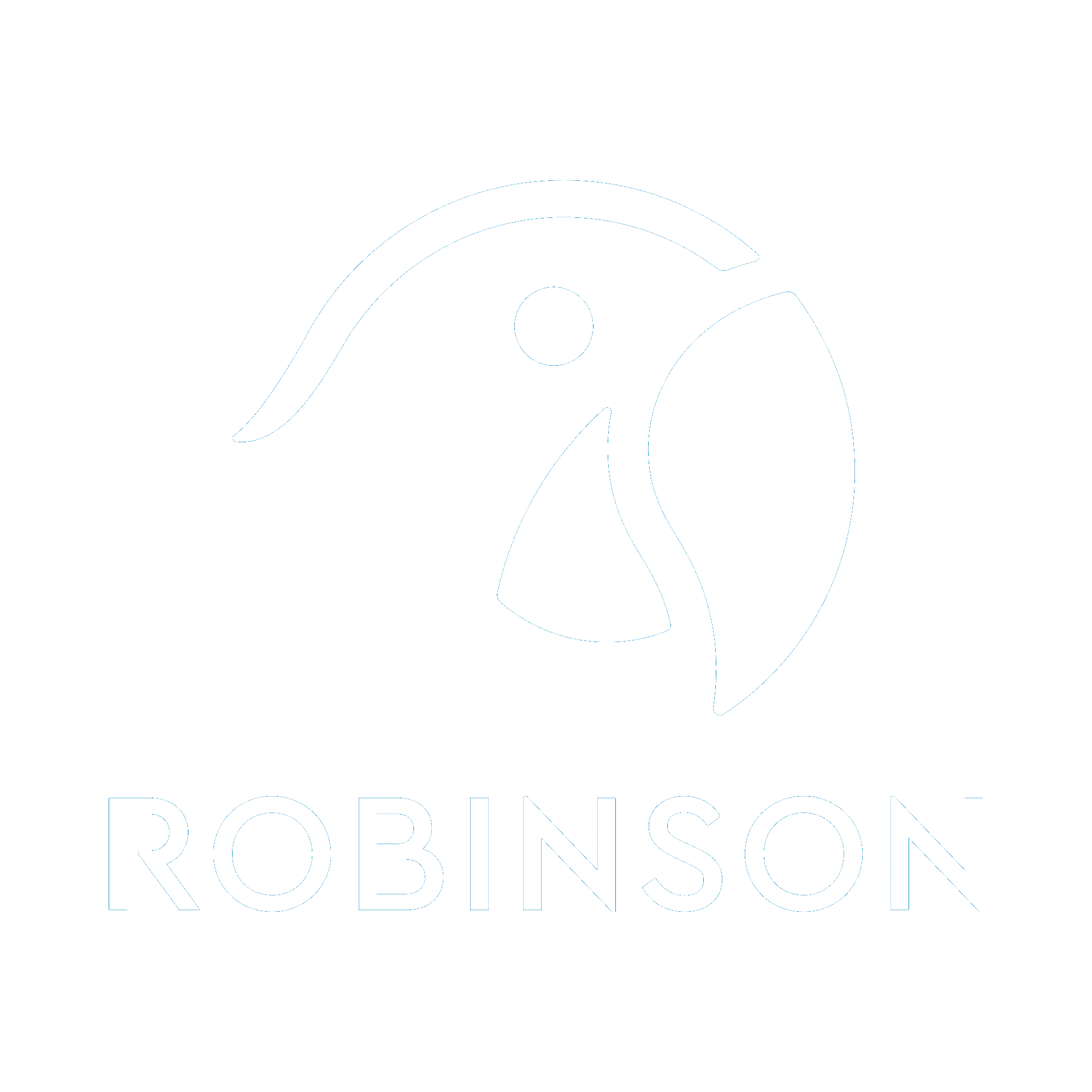
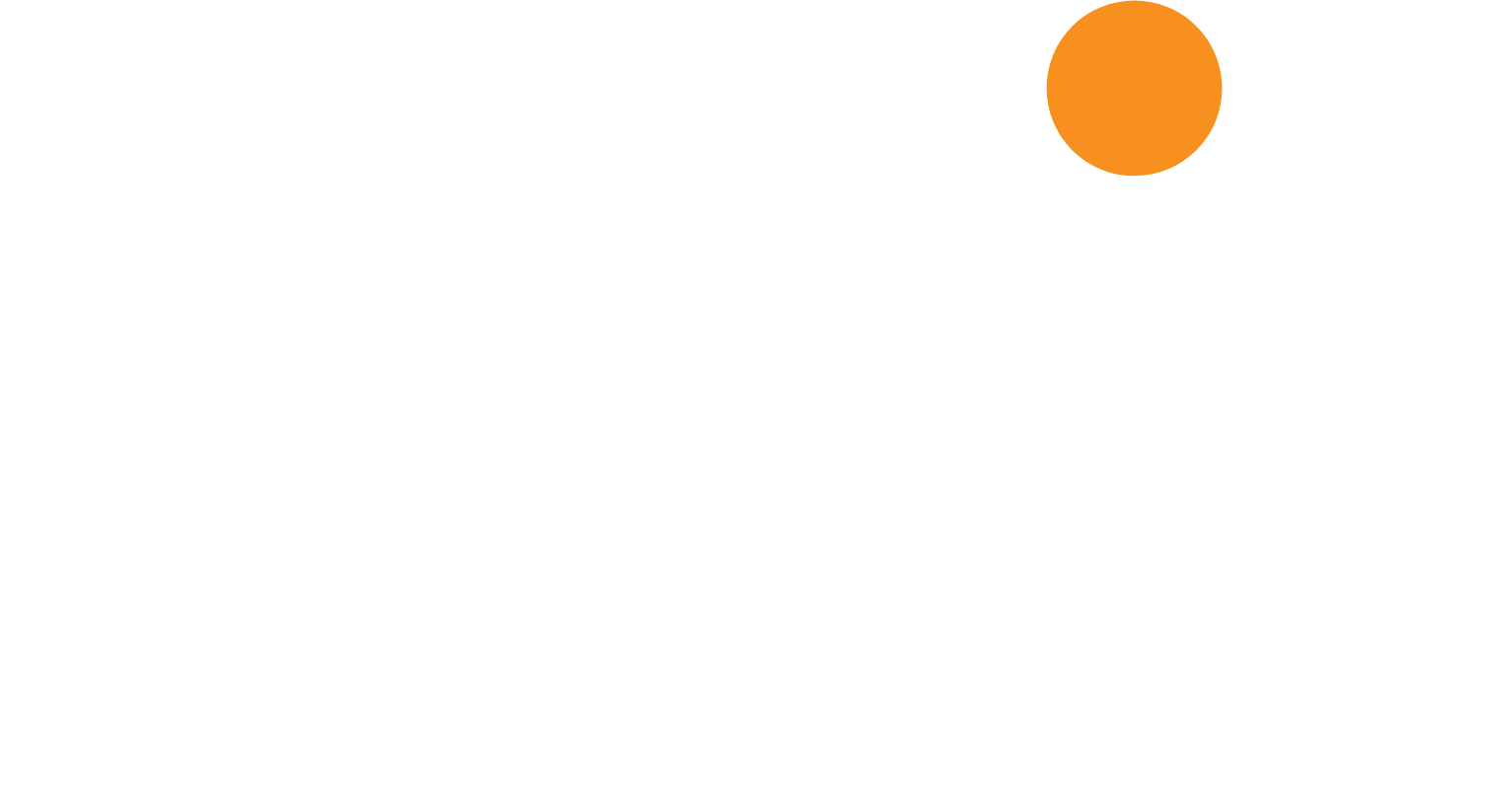
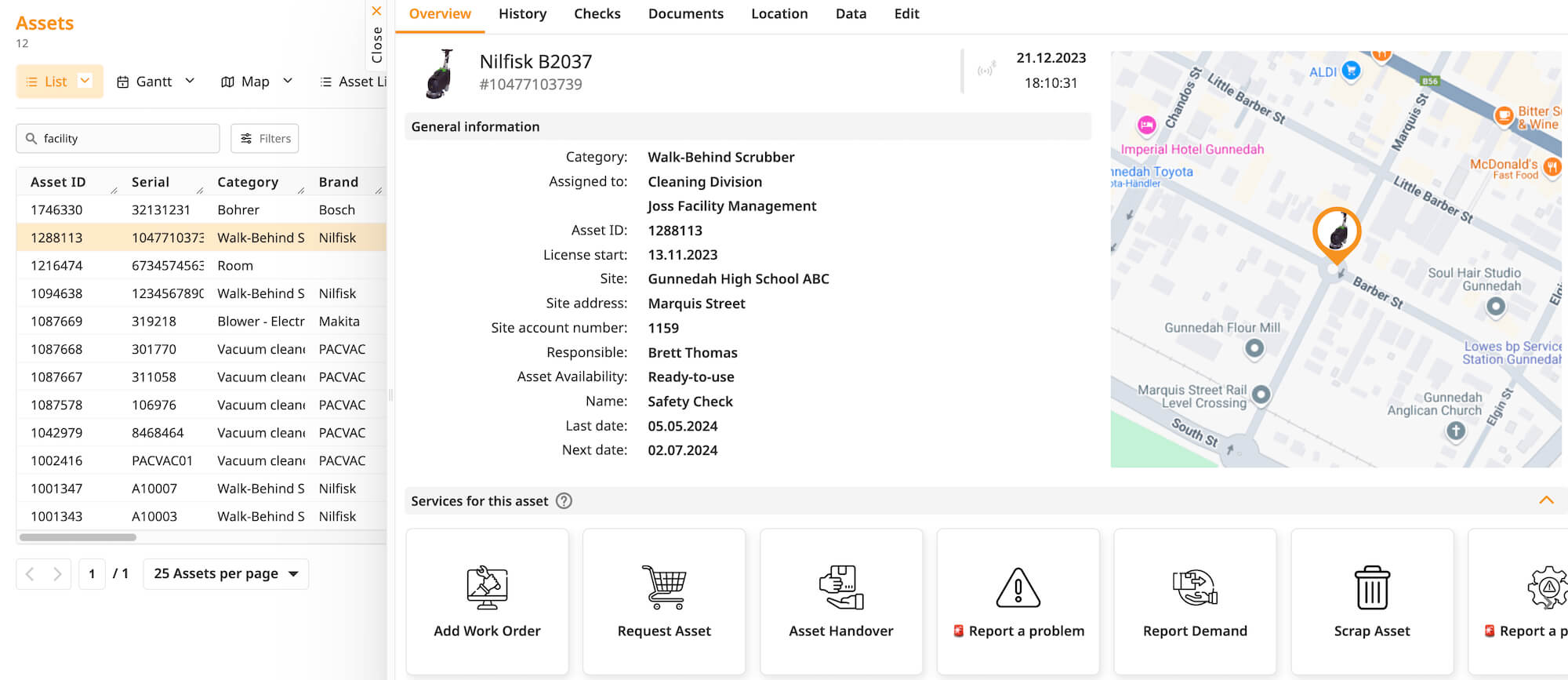
Run Facility Operations Easily
ToolSense is more than a building management software and combines asset management, maintenance management, work order management, and inventory management in one easy-to-use system. Whether you are tracking runtimes, issuing work orders, or keeping an eye on your inventory – the right facility equipment maintenance system will have you covered.
With its intuitive QR code-based approach and IoT integration capabilities, ToolSense empowers facility managers to make data-driven decisions that can reduce maintenance costs by up to 20% while significantly decreasing equipment downtime.
Central Hub for IoT Data
Connect your existing equipment fleet with ToolSense’s IoT trackers and integrations. Gain full visibility into the location, runtime, battery status, and usage of your cleaning machines, vacuum cleaners, vehicles, and tools. We have OEM partnerships with a lot of brands like Tennant, Numatic, i-team, Columbus, and Cleanfix – and can furthermore connect to manufacturer APIs such as Kärcher Fleet, Taski IntelliTrail, and Hako Fleet. Robot fleets from Gausium, Pudu, and others are also fully integrated. All data flows into one central platform – ToolSense.
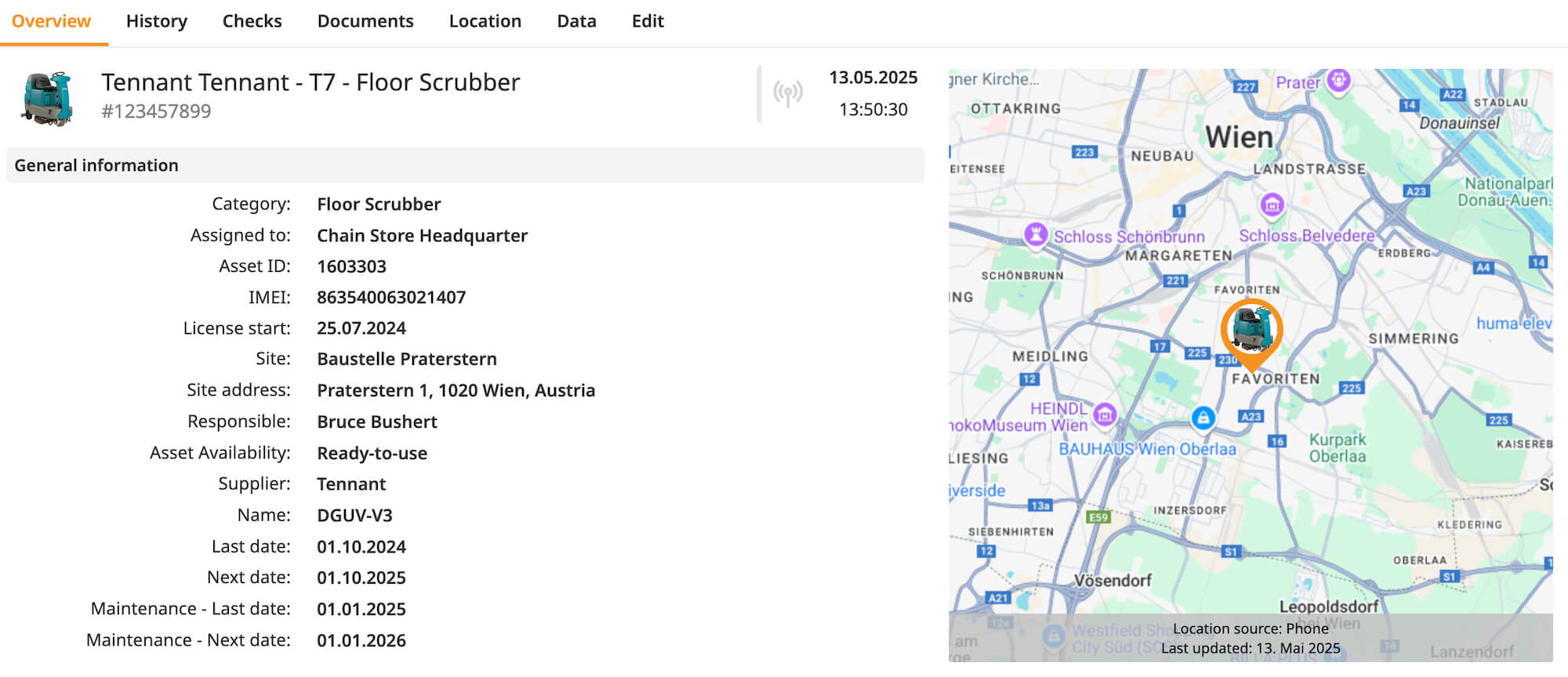
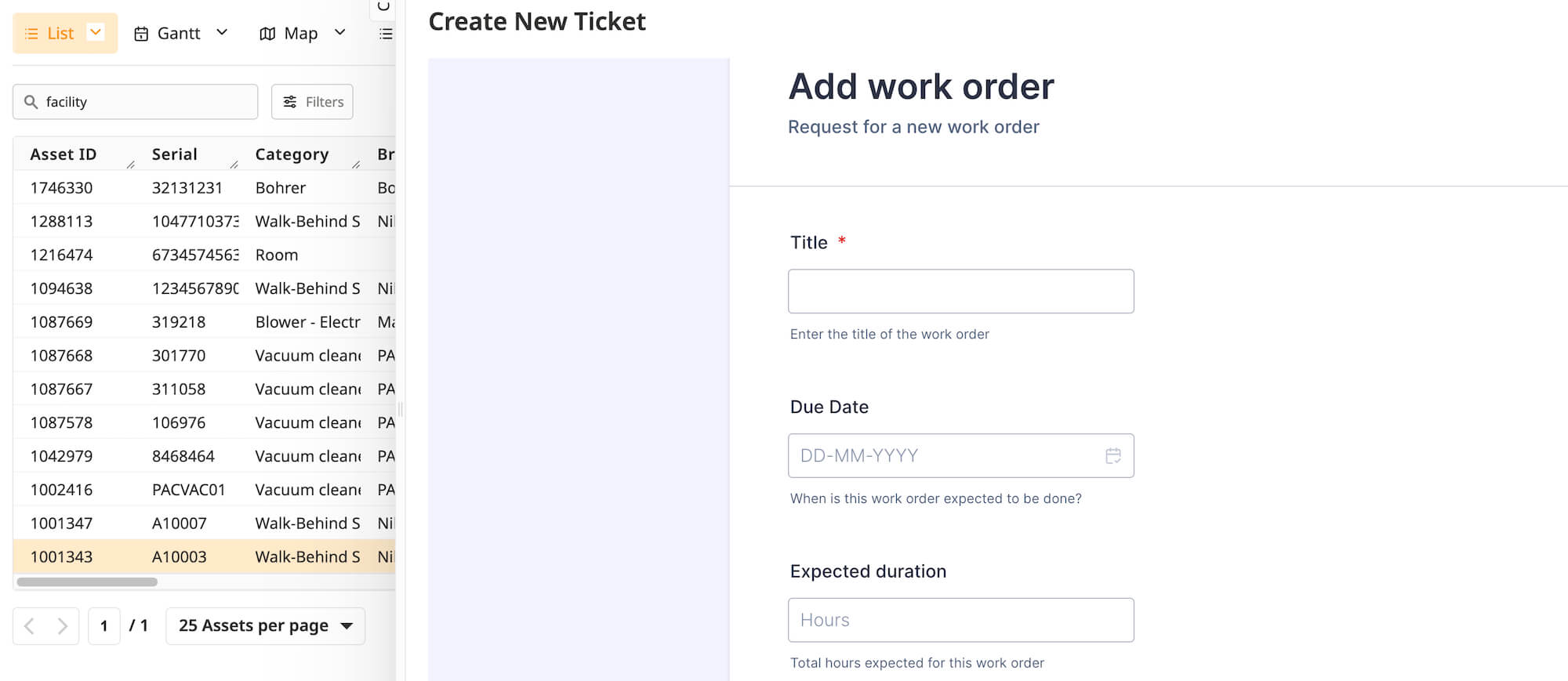
Create Work Orders
A versatile software like ToolSense not only keeps track of your assets, but your work orders as well. A worker can issue a work order through the system, which will be directed to the responsible employee immediately. They can then track the progress and record the results in the computer-aided facility management software, and close the work order once it is completed.
This streamlined workflow significantly reduces administrative overhead and ensures that all maintenance activities are properly documented for future reference and compliance purposes.
Stefan Dörner
Operations Manager
Gonder Facility Services
ToolSense allows us to unify the tracking of our diverse machine fleet and gives us valuable insights into equipment utilization. All our machines get a QR code for inventory purposes. This helps us make better operational decisions and provide validation of our services to customers. It’s a solution I’ve been searching for over a decade.
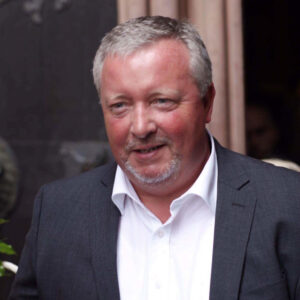
Work Order History
If a work order is issued orally or via e-mail, it can be easily forgotten or end up in your mailbox’s bin. If you are looking to gather data on how your work orders are completed, how much time is needed, and how many work orders your employees issue in a certain time frame, it is important to have access to statistics and your entire work order history. This is why closed work orders aren’t deleted, but filed in the system for later review during your decision-making process.
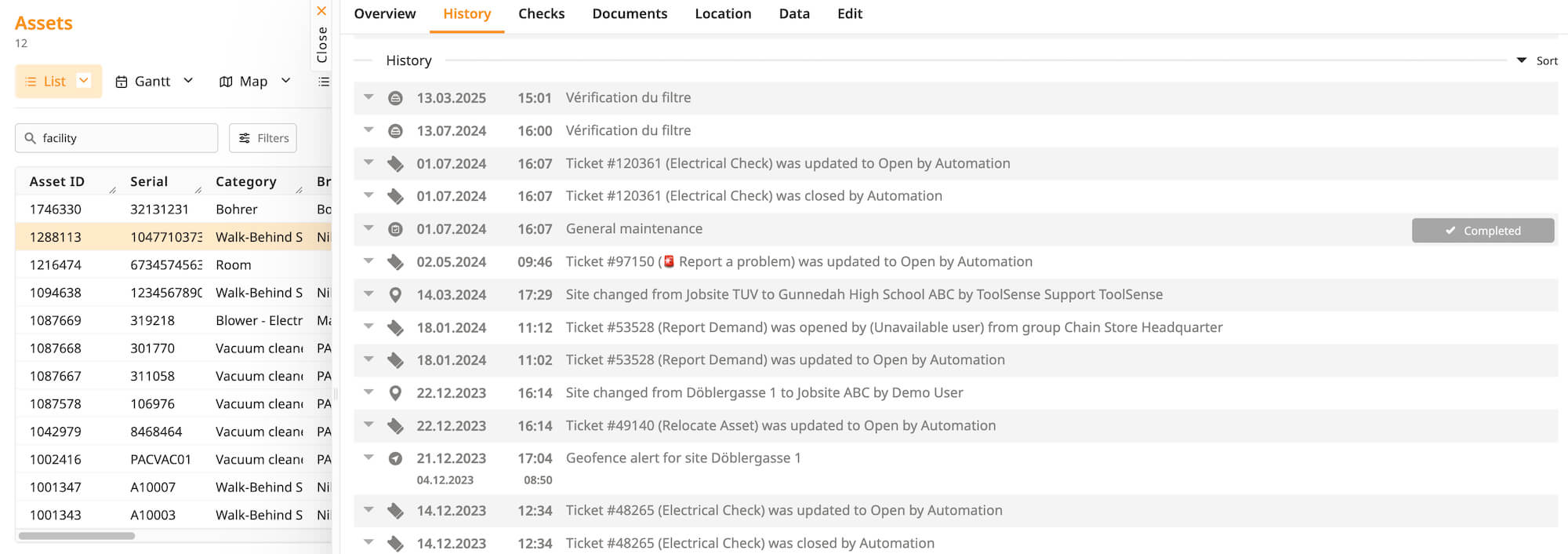
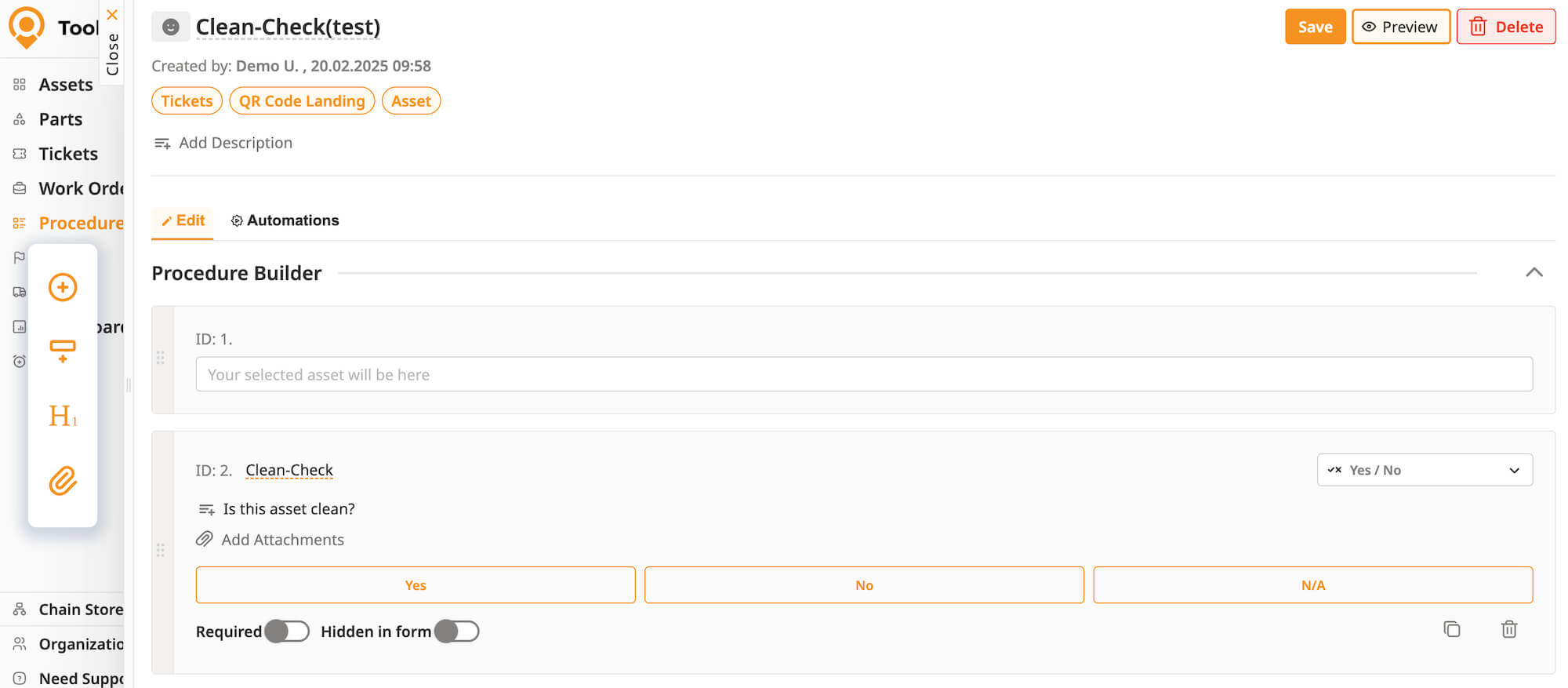
Digitalization of forms and workflows
Upgrading to a modern form of facility management can save your company a lot of time and money and make the entire process more efficient. ToolSense’s asset and facility management software combines everything you need in a single, easily accessible platform that is optimised for desktop and mobile use. Your employees never have to dig through heavy folders ever again because the information that they need is neatly stored in your ToolSense database.
Collaborate Across Your Organisation
To work efficiently and productively, every employee needs to be on the same page and up to date on all tasks and work orders. Especially if a company employs a large number of people, Excel lists, e-mails, and WhatsApp group chats aren’t enough to keep everyone organised.
A software for maintenance and operations that combines asset management and work order management in one platform can help keep everyone in the loop, ease communications, and make sure work orders reach the responsible employee.
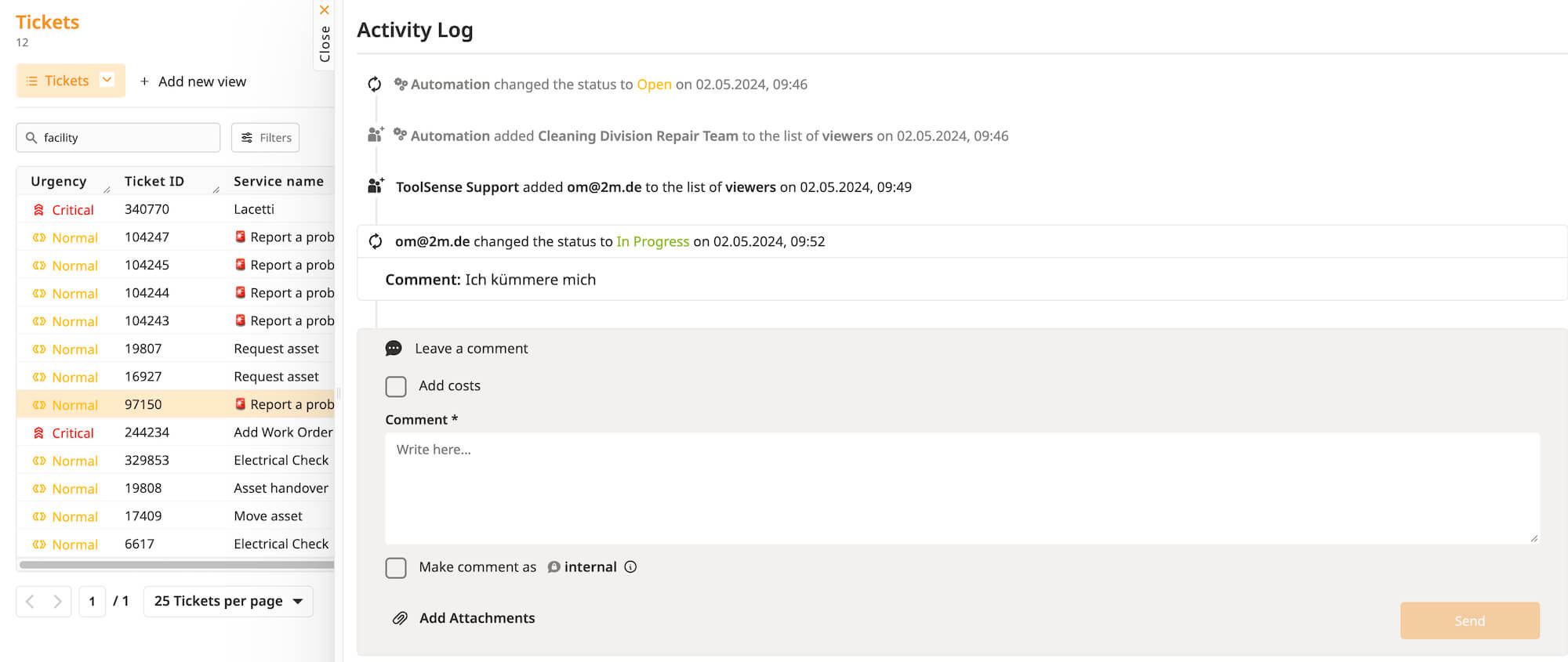
Improve Your Business Impact
Save 20% on machine and repair costs and reduce unplanned scrubber downtime by 70%. Reduce time spent on asset tracking and maintenance coordination by 30%.
Case Study: BLITZBLANK Reinigung
We’ve been partners with ToolSense for almost four years now. We started with the classic machine management solution – equipping our larger machines with ToolSense modules to monitor their operation time, usage, and potential breakdowns. We now use ToolSense for our complete facility vehicle tracking system as well.
In the course of our partnership with ToolSense, we looked for alternative products and came up with the excellent idea of using trackers that connect through the car’s diagnostic interface. We found a solution that allows us to quickly swap vehicles while maintaining the same quality – and at lower costs. Overall, we’ve saved approximately €1,000 per month by switching to this solution.