Unlocking the full potential of your CMMS can transform your maintenance management. Discover key CMMS best practices that will elevate your system from functional to formidable.
Key Takeaways
- Effective CMMS utilization requires setting SMART goals, embracing mobile capabilities, customizing features to fit needs, and fostering organization-wide commitment for maximizing maintenance management efficiencies.
- Operational efficiency with CMMS can be achieved through standardized processes, real-time asset tracking, detailed maintenance scheduling, leveraging technology for automation, and continuous training for team members.
- Optimal use of CMMS involves not only technological integration like real-time tracking and data analytics but also strategic practices such as goal-oriented process standardization, team empowerment, and a strong emphasis on quality, compliance, and continuous improvement
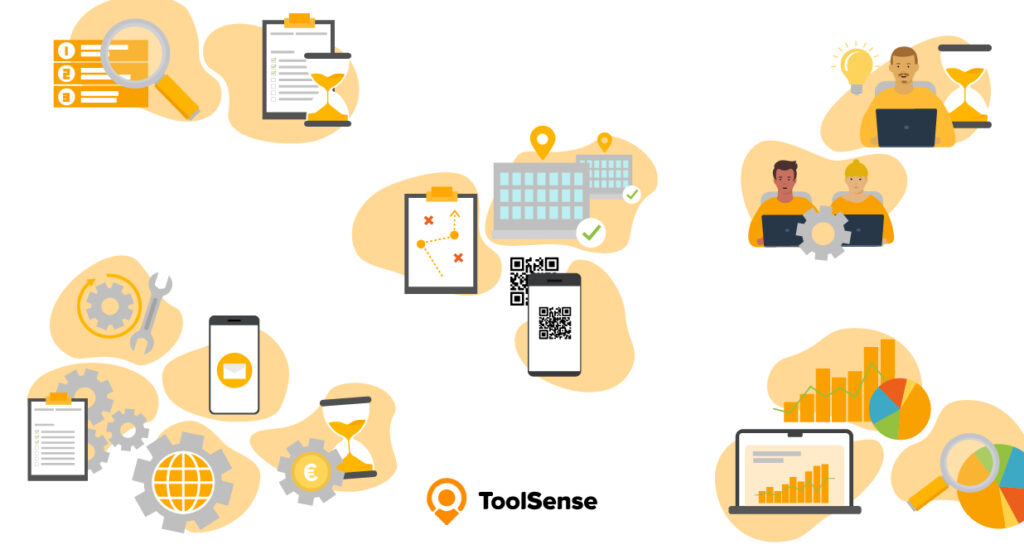
How to Use CMMS Software
Effectively leveraging a Computerized Maintenance Management System (CMMS) involves a range of tasks aimed at centralizing maintenance information and automating management processes. This can lead to marked improvements in both efficiency and effectiveness.
- Establishing clear goals, such as enhancing maintenance operations, controlling costs, and ensuring equipment reliability, is a foundational step that enables you to harness the potential of CMMS software.
- Ensuring organization-wide commitment and understanding is essential. All team members, from technicians to executives, should recognize the benefits of the system and contribute towards a common goal.
- Utilizing mobile applications, often included in CMMS platforms, allows technicians to input and update data on the go, which can significantly improve the speed and accuracy of maintenance activities.
- Asset management implementation is a key aspect, involving strategies to maintain equipment health, aiding in proactive maintenance, and reducing unexpected downtime.
- Developing a maintenance strategy entails planning and coordination to ensure that maintenance activities are carried out efficiently.
- Customizing the system to fit the user’s needs ensures that the most important and frequently used information is easily accessible.
By incorporating these elements into daily operations, CMMS software becomes a powerful tool that simplifies maintenance management and provides a platform for insights and analytics to enhance decision-making.
Continuous improvement and adaptation are crucial, so your strategy should include ongoing training and the appointment of ‘product champions’ to facilitate this. Before delving into relevant best practices, it’s essential to understand the needs of your company first. As these practices are applied, your organization can expect a positive transformation in its maintenance operations.
Understanding Your Organization’s Maintenance Needs
Assessing your organization’s existing maintenance processes and challenges is a critical first step. This assessment will reveal inefficiencies and pave the way for setting SMART goals. These goals will guide the strategic alignment of the CMMS’s functionalities with your maintenance management needs.
Assess Current Maintenance Processes: A thorough needs assessment will uncover specific challenges and help in setting clear and achievable targets for your CMMS implementation, ensuring it becomes a solution tailored to your organization’s needs.
Set Clear Goals and Objectives: Following the assessment, it’s time to set SMART goals for your CMMS deployment. These goals will help categorize maintenance tasks by priority and complexity, driving efficiency and minimizing equipment downtime.
CMMS Best Practices for Operational Efficiency
For operational efficiency, CMMS best practices are essential. This chapter, as well as subsequent ones, will delve into various strategies and techniques to optimize your maintenance management. From embracing technological advancements to meticulous planning, these best practices are designed to streamline operations and enhance the overall effectiveness of your maintenance system, organized into five key categories: Operational Efficiency, Data Management and Analytics, Team Integration and Empowerment, Quality and Compliance, and Innovation and Process Improvement. We`ll start with four CMMS best practices to improve operationla efficiancy
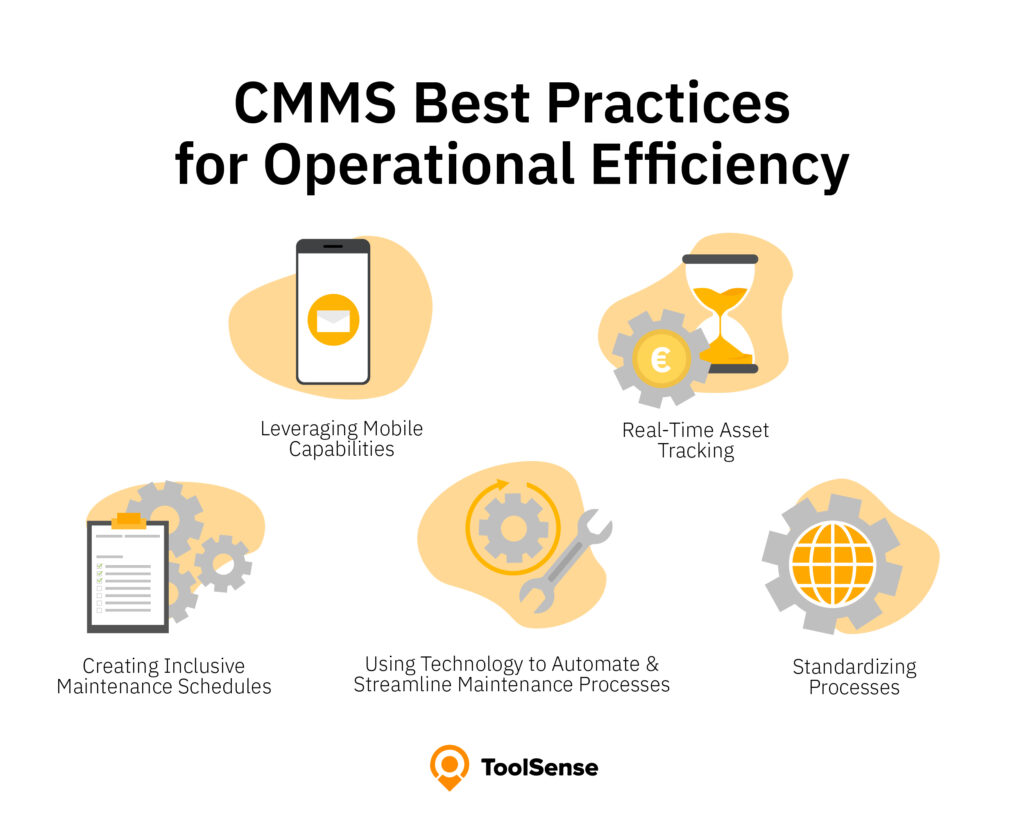
1. Leveraging Mobile Capabilities
Embracing mobile capabilities is crucial in modern maintenance. With mobile access to CMMS like ToolSense, technicians can update work orders on-site, ensuring maintenance standards are met anywhere, anytime.
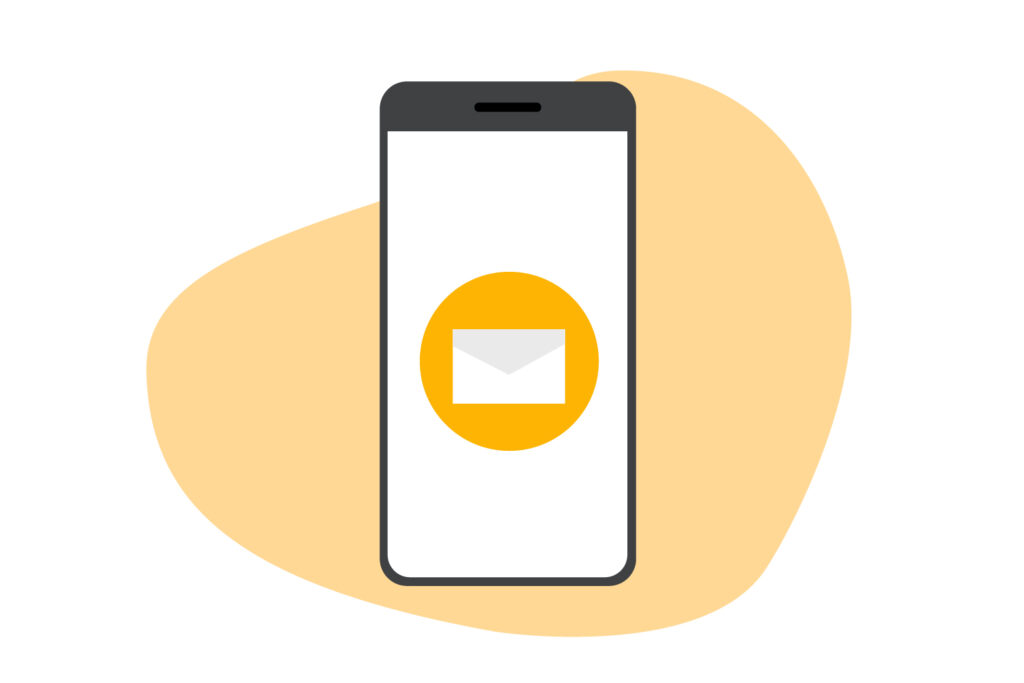
CMMS Insight: ToolSense’s web-based access streamlines maintenance management by allowing technicians to promptly update work orders on-site, reducing delays. It supports seamless information flow with features like photo sharing, electronic document signing, and efficient communication, enhancing decision-making and adherence to best practices.
2. Real-Time Asset Tracking
Implementing real-time asset tracking stands as a cornerstone feature that revolutionizes maintenance management. This method provides instant visibility into equipment status and location, enabling proactive maintenance scheduling that minimizes downtime. Here’s an explanatory breakdown of how this transformative practice works:
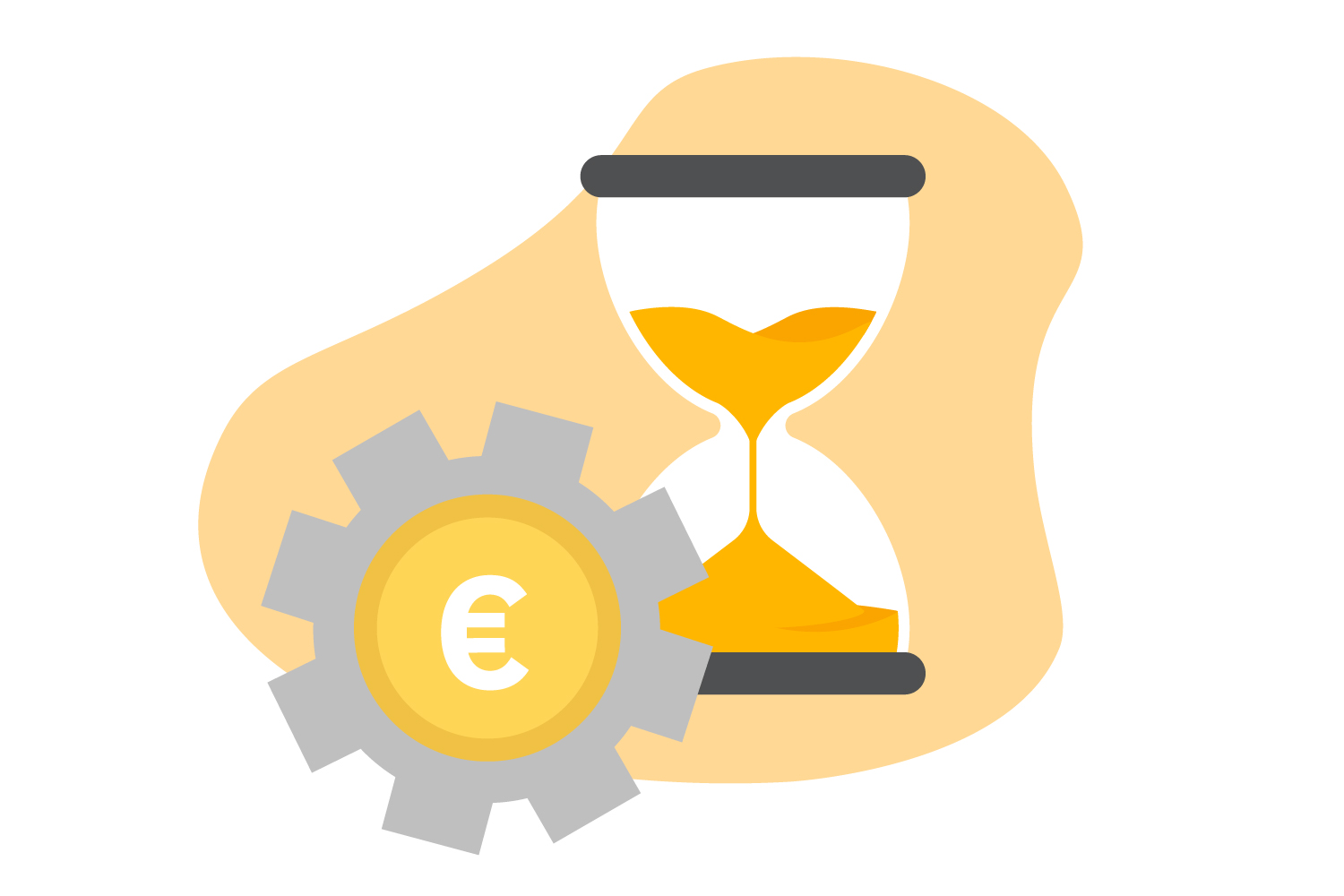
- Monitors Equipment Status and Location: Real-time tracking keeps a constant eye on your assets, giving you immediate insight into where they are and how they’re performing, preventing issues before they escalate.
- Minimizes Downtime: With the data obtained from real-time tracking, maintenance can be scheduled proactively, which means addressing potential problems before they cause operational disruptions.
CMMS Insight: Leveraging ToolSense’s IoT (hardware) capabilities takes asset tracking to the next level. The platform’s intuitive features allow for effortless monitoring of asset conditions. By integrating ToolSense, you gain access to a suite of tools designed to streamline your asset management, ensuring that the right maintenance is performed at the right time, thereby reducing downtime and maintaining operational continuity.
3. Standardizing Processes
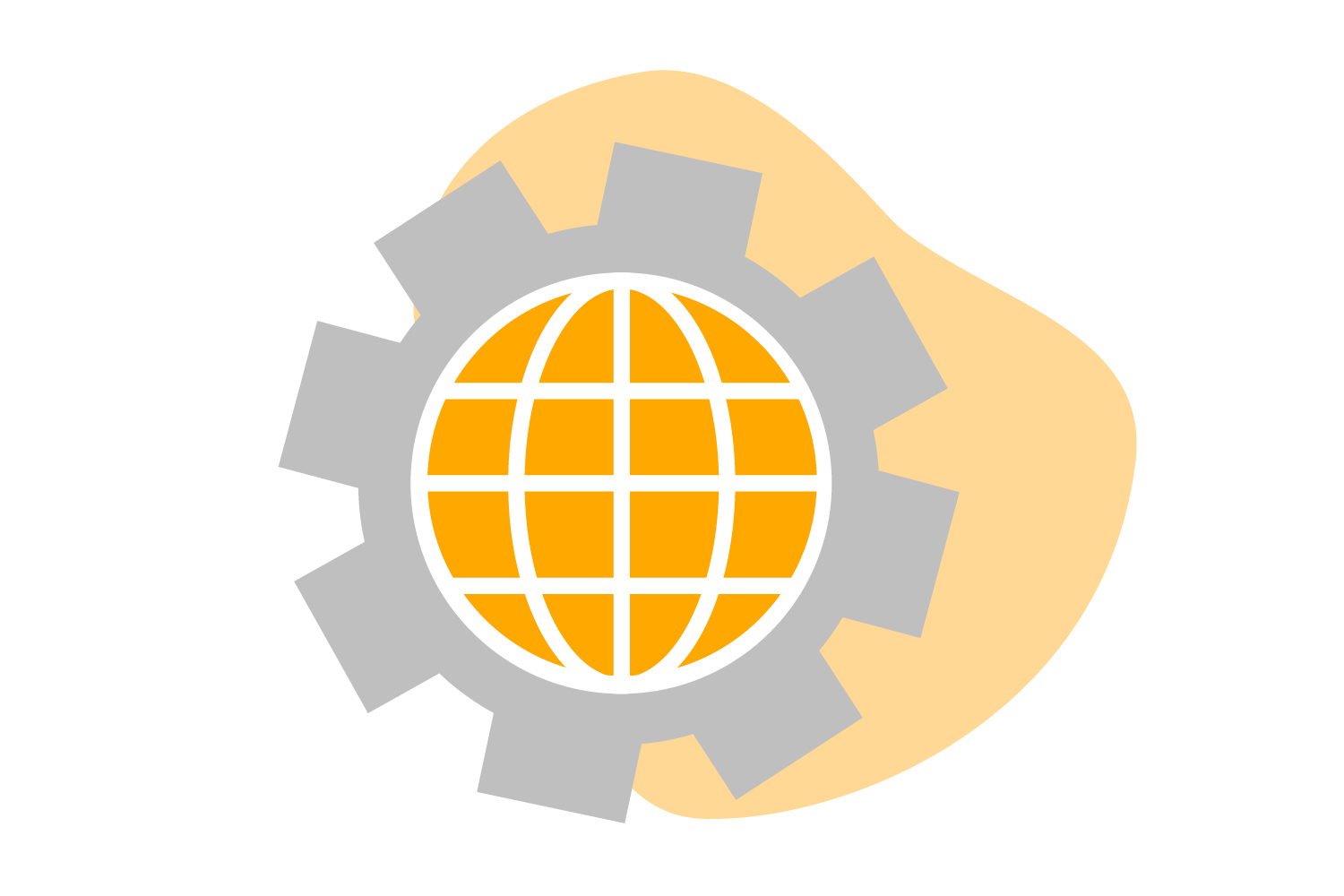
Standardizing processes is crucial for consistent and efficient maintenance operations. It ensures team harmony and eases new staff integration by acclimating them to uniform procedures.
CMMS Insight: ToolSense helps maintain high standards by storing and sharing operating procedures, ensuring technicians perform their tasks uniformly. It also offers tips and reminders for correct process execution, embedding standardization into the maintenance culture.
4. Creating Inclusive Maintenance Schedules
Creating inclusive maintenance schedules is a pivotal best practice that involves more than just marking dates on a calendar. It requires comprehensive planning for inventory needs and clear, detailed work order instructions. This practice is instrumental in reducing equipment failures and minimizing downtime by ensuring that all necessary resources and information are readily available when maintenance activities are scheduled.
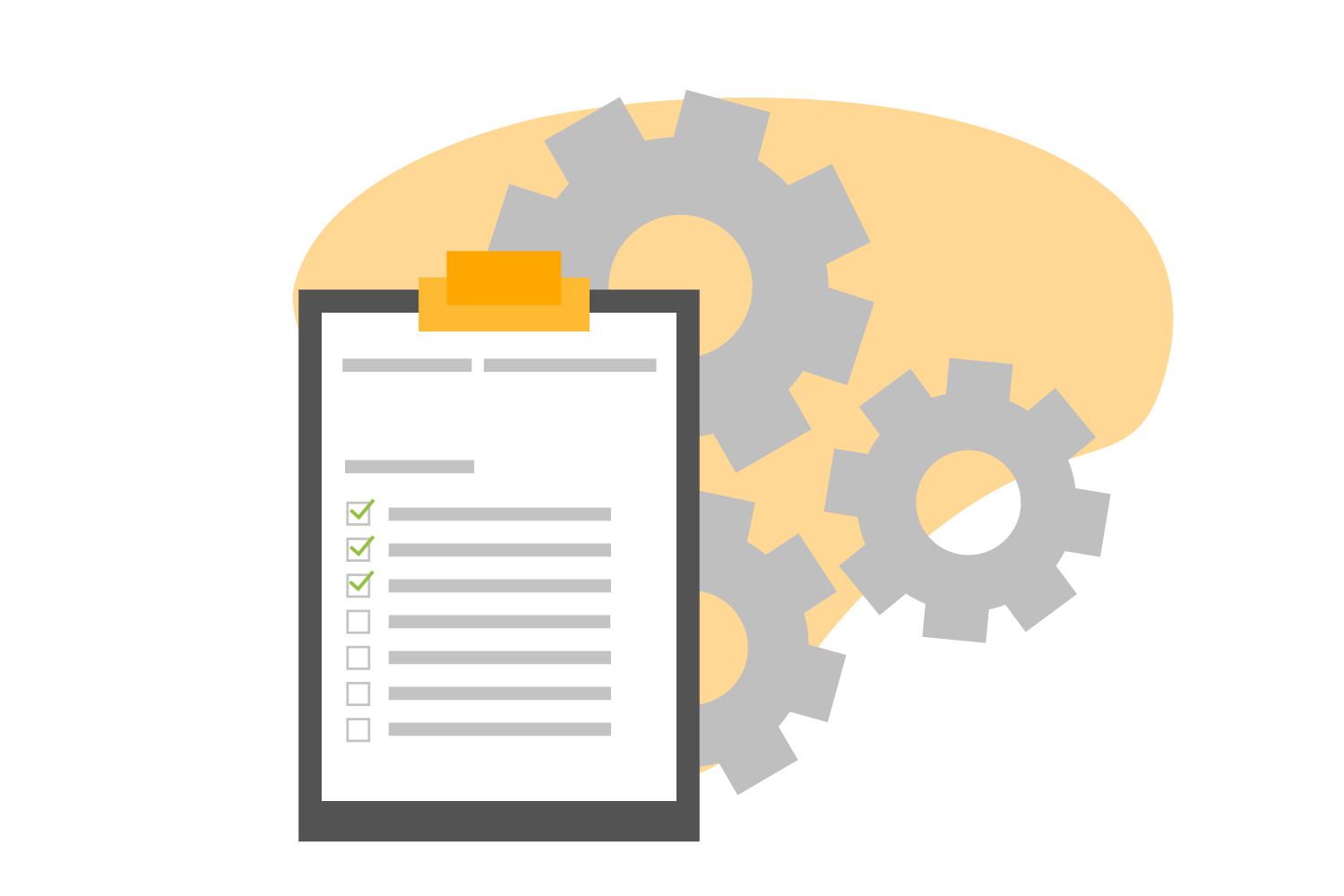
CMMS Insight: Scheduling within ToolSense exemplifies this by allowing for meticulous planning that aligns maintenance work activities with available resources. ToolSense provides a structured approach to maintenance scheduling, ensuring that technicians have immediate access to inventory levels and detailed work order instructions, which is essential for minimizing equipment downtime and optimizing maintenance workflows. By utilizing ToolSense’s scheduling capabilities, organizations can achieve a higher level of operational efficiency and reliability.
5. Using Technology to Automate and Streamline Maintenance Processes
Adopting technology to automate and expedite maintenance processes is pivotal . By defining maintenance standards and tagging assets with QR codes, technology not only enhances efficiency but also meticulously reduces manual errors. This approach fosters proactive maintenance processes and ensures accurate, up-to-the-minute tracking of equipment status.
- Improves Routine Maintenance Through Automation: Automation of notifications and procedures significantly improves routine maintenance. Systems can be configured to send alerts for upcoming maintenance tasks, ensuring timely action and reducing the risk of equipment failure.
- Leads to Improved Maintenance Metrics and Goal Management: With automated processes, maintenance metrics can be tracked more accurately, and maintenance goals managed more effectively. This leads to a clear understanding of maintenance performance and facilitates data-driven decision-making.
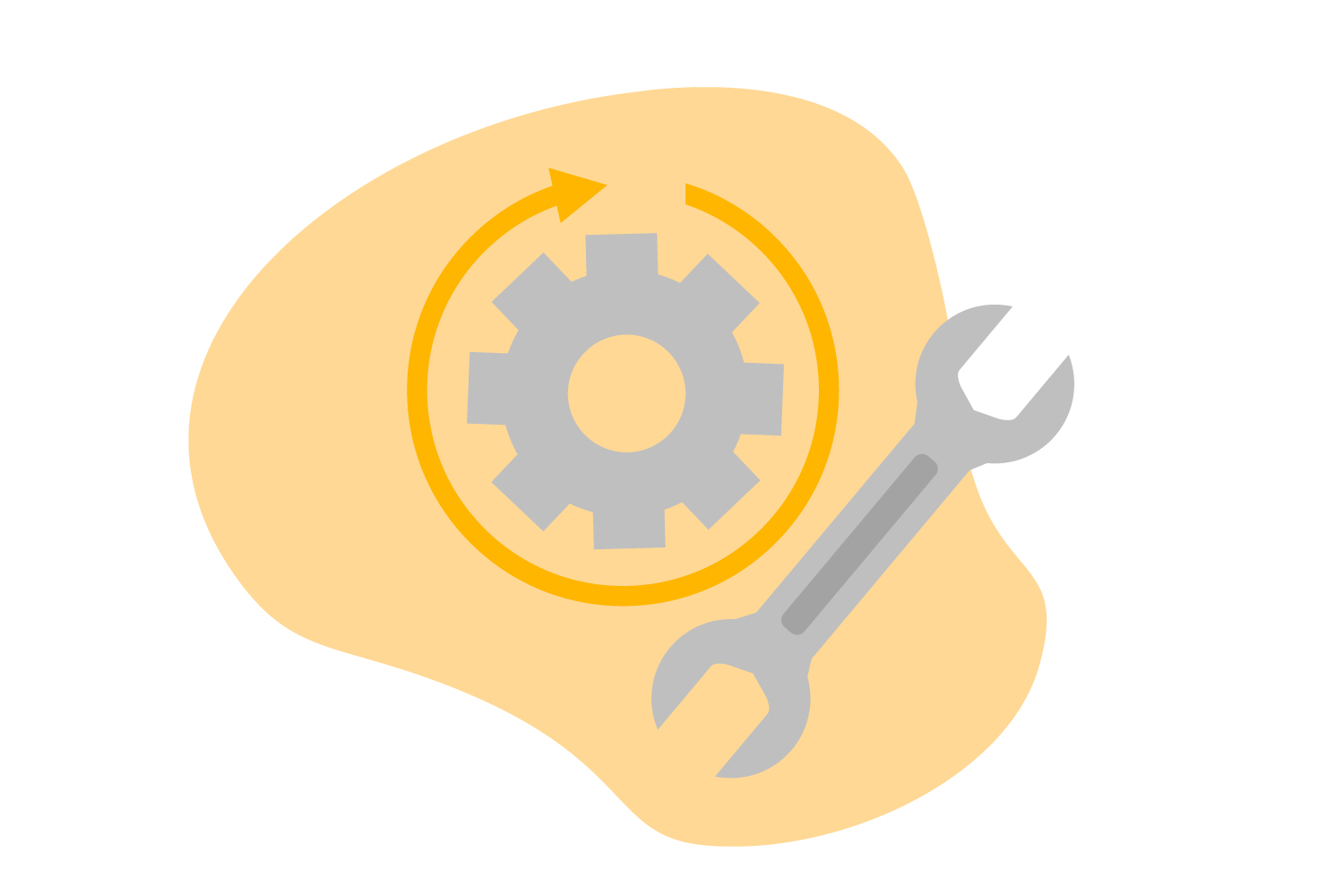
CMMS Insight: ToolSense can be instrumental in automating many maintenance processes, from scheduling to notification. The platform ensures that routine maintenance tasks are never overlooked and that all procedures are followed to the letter. ToolSense’s automation capabilities mean that maintenance managers can set reminders for preventive maintenance, track completion of tasks, and review performance metrics, all within a unified system. This level of automation not only streamlines maintenance operations but also contributes to achieving and surpassing maintenance goals.
CMMS Best Practices for Data Management and Analytics
Data management and analytics, supported by inventory management, are pivotal for effective maintenance management. Using CMMS solutions that feature real-time asset tracking and predictive maintenance helps managers monitor equipment performance and anticipate maintenance needs.
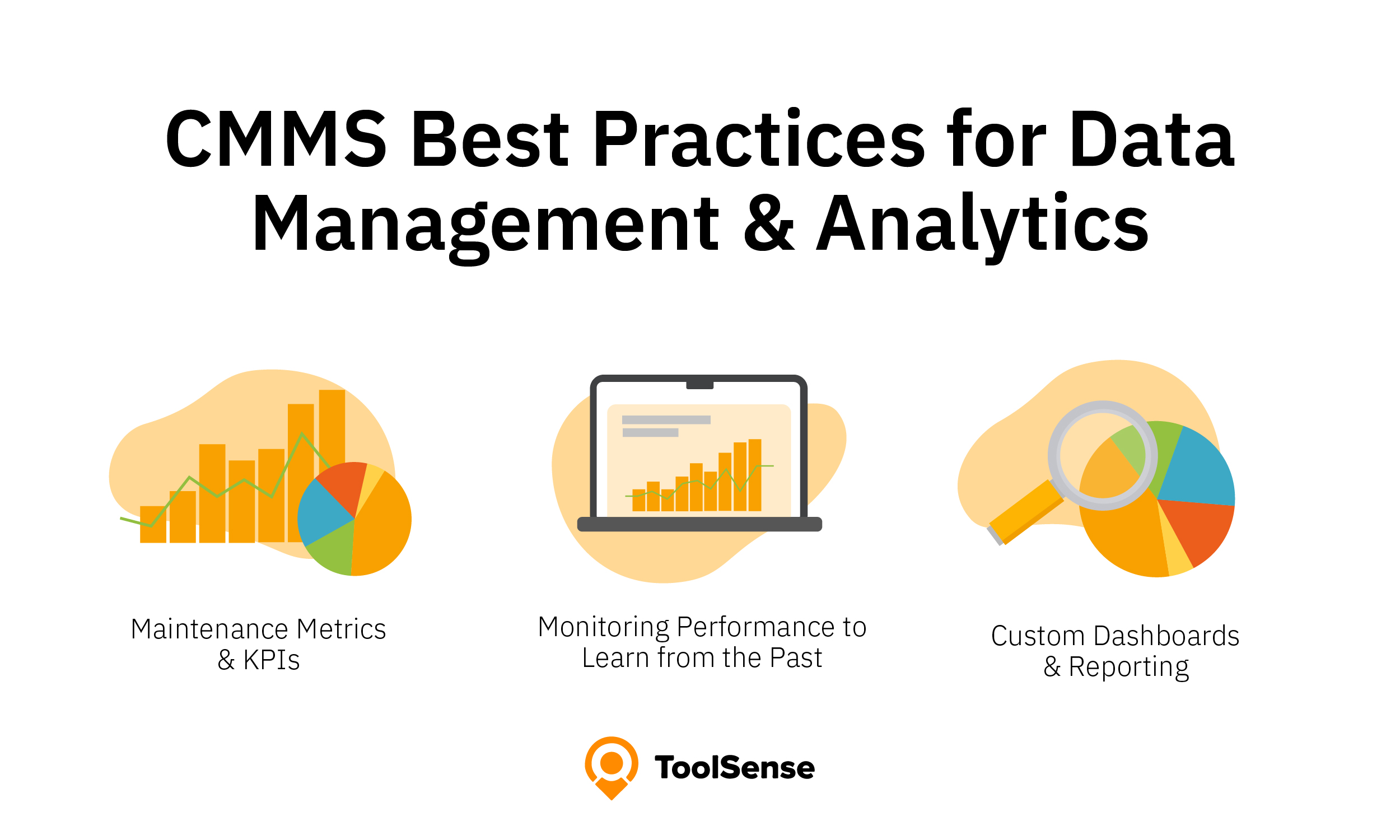
6. Maintenance Metrics and KPIs
Meticulously tracking metrics and key performance indicators (KPIs) is a best practice that serves as a navigational tool in the vast ocean of maintenance data. By systematically monitoring these indicators, organizations can steer continuous improvements and make informed decisions with tangible evidence, providing a transparent view into the performance of their maintenance operations.
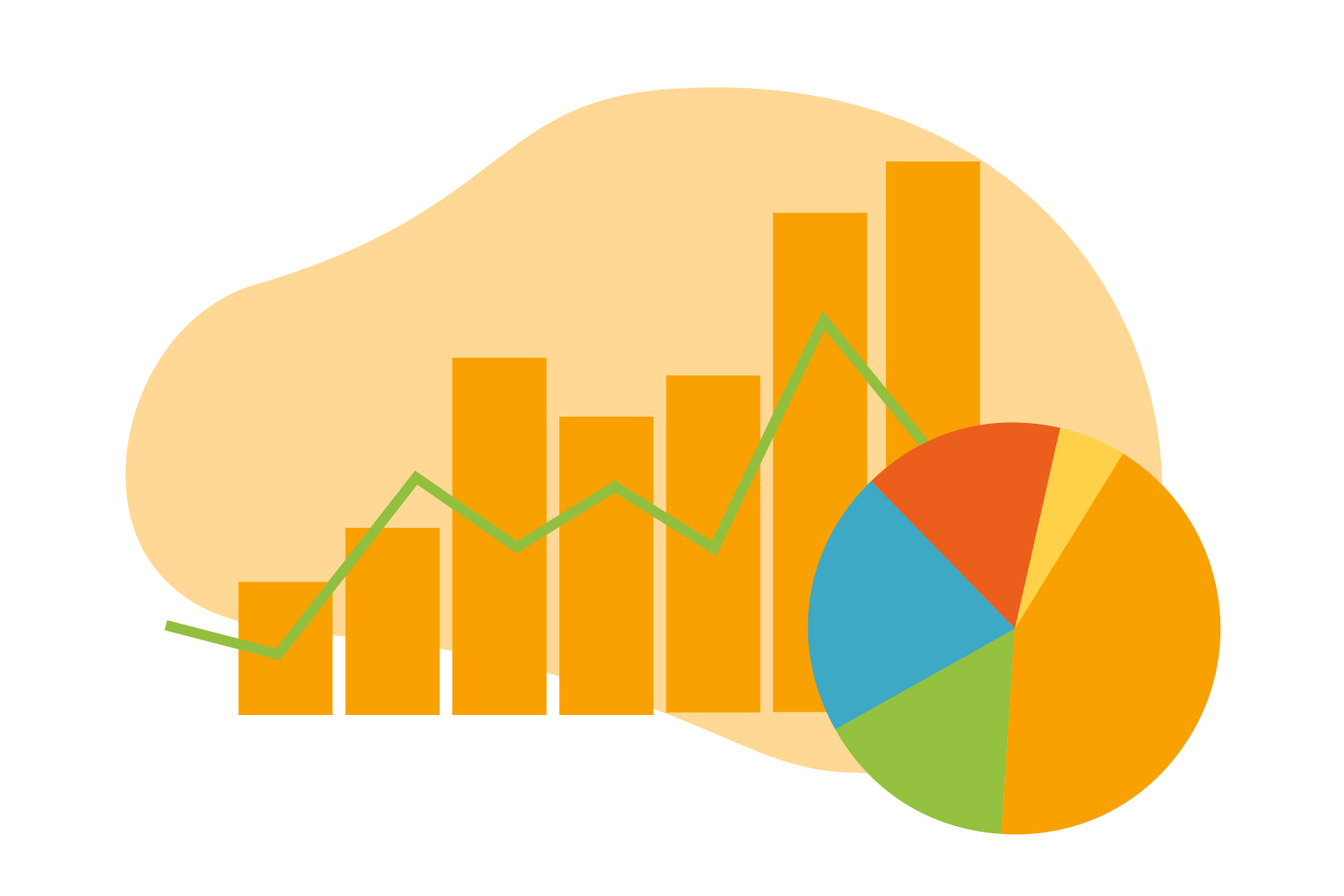
CMMS Insight: Well-defined metrics and KPIs are the compass that guides maintenance managers through the sea of data. ToolSense offers a comprehensive suite of features for generating, tracking, and analyzing these vital statistics, enabling strategic improvements and data-driven decisions that resonate with business objectives.
7. Custom Dashboards and Reporting
Custom dashboards are a best practice that function as the nerve center of your CMMS, enabling you to:
- Tailor data tracking to align precisely with business objectives, ensuring that every piece of information serves a strategic purpose.
- Visualize complex data through intuitive interfaces, simplifying interpretation and accelerating informed decision-making.
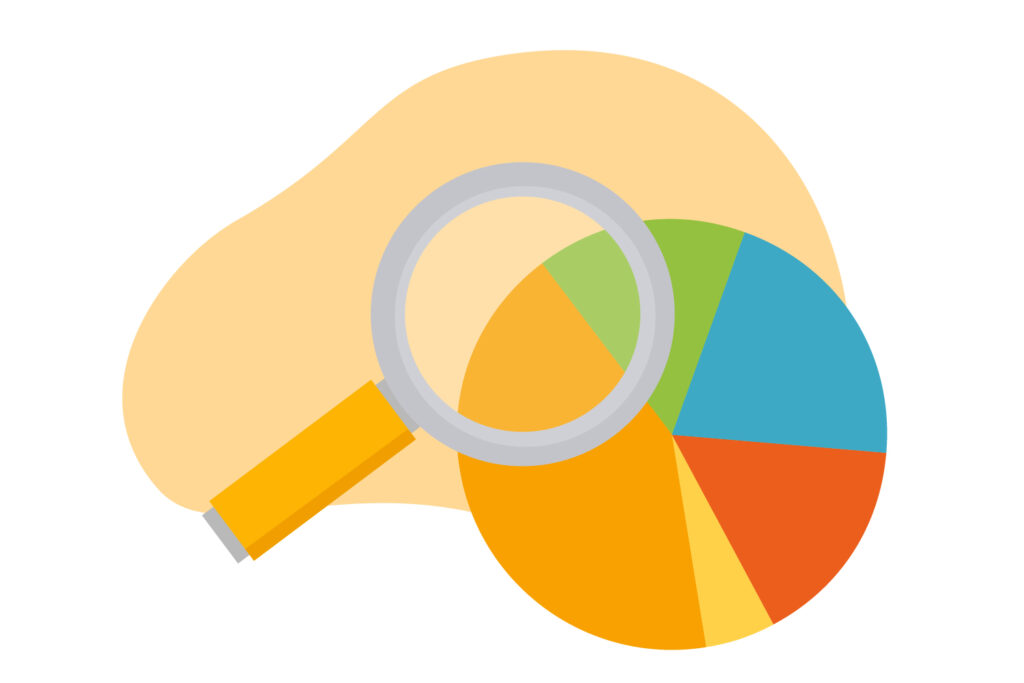
CMMS Insight: ToolSense allows for the customization of dashboards, which can be tailored to highlight the metrics most critical to your organization’s success. This ensures that managers have a clear view of performance against business goals and can make swift, data-driven decisions. Additionally, ToolSense can offer tips on setting up dashboards to track the right KPIs, ensuring that the CMMS aligns with your maintenance management strategy.
8. Monitoring Performance to Learn from the Past
Adopting a best practice approach by analyzing failure histories and parts consumption is crucial for advancing maintenance management. This methodical analysis within CMMS platforms is essential for informing future maintenance planning and driving continuous improvement.
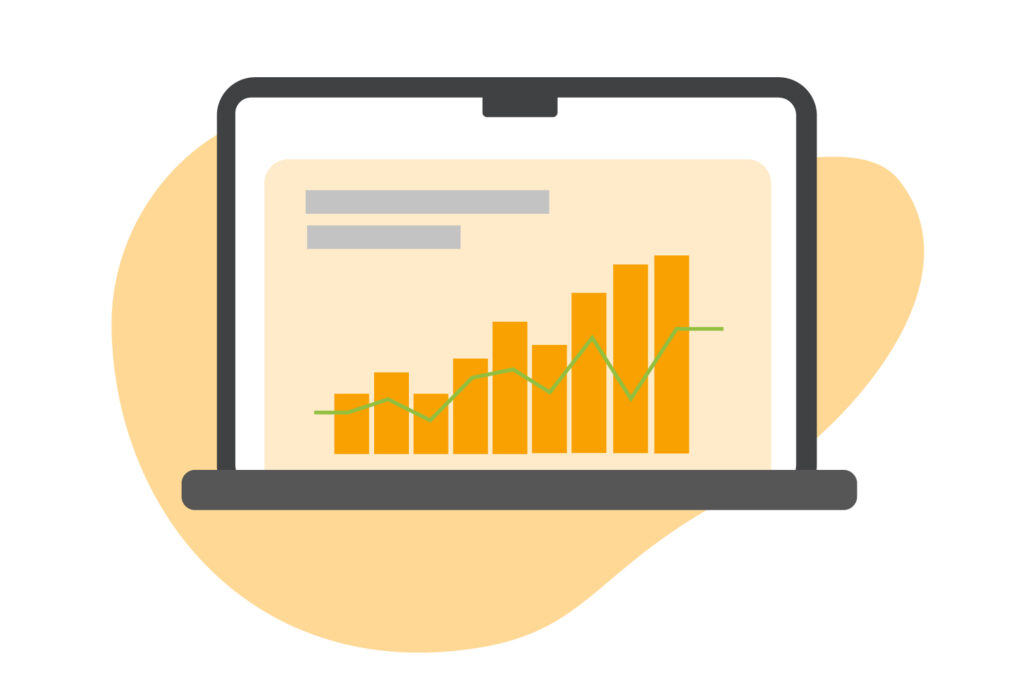
CMMS Insight: ToolSense offers a robust historical data analysis feature that helps maintenance managers to identify and analyze trends in failures and parts usage. This functionality is imperative for preventing recurring issues and optimizing parts inventory. With ToolSense, managers can receive actionable tips and insights that guide the refinement of maintenance planning and the implementation of preventive measures, ensuring that the organization is continuously improving its maintenance operations.
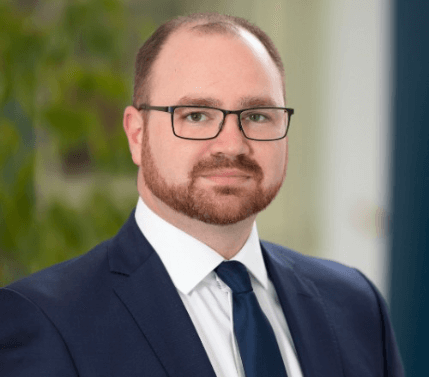
CMMS Best Practices for Team Integration and Empowerment:
A CMMS is only as strong as the team behind it. Best practices for team integration and empowerment ensure the involvement, training, and equipping of everyone, from frontline workers to top management, for full utilization of the CMMS.
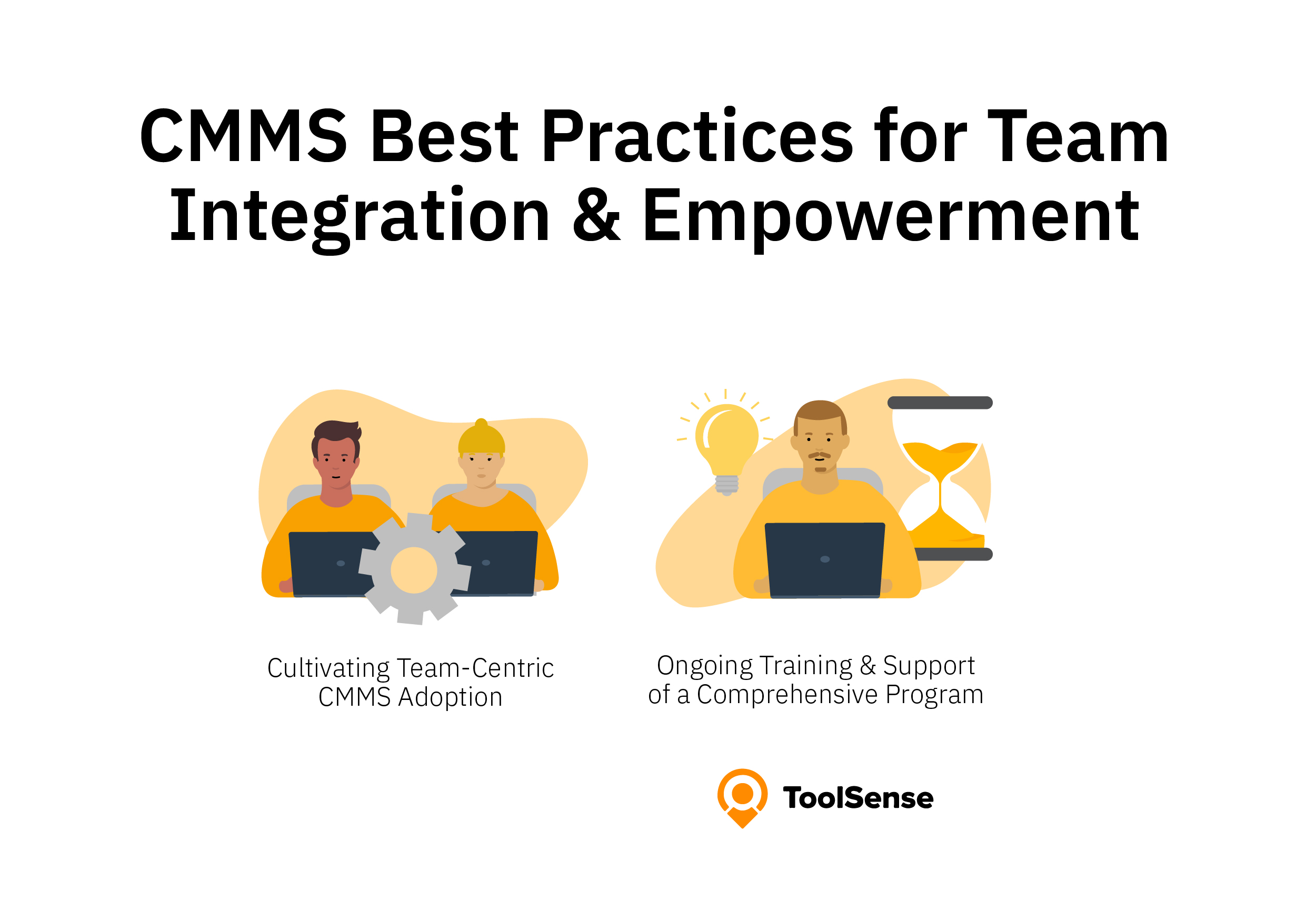
9. Cultivating Team-Centric CMMS Adoption
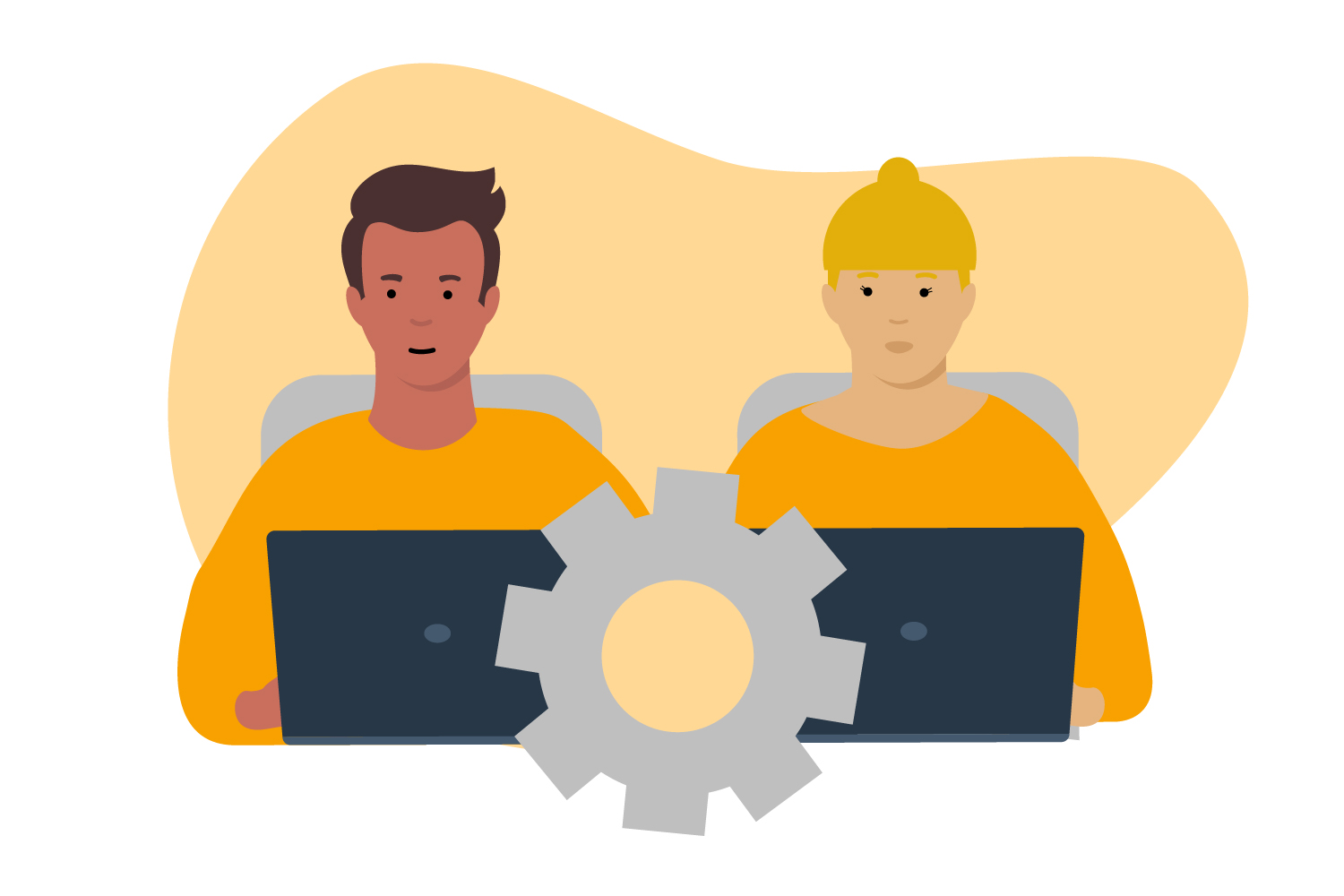
Cultivating a team-centric approach to CMMS adoption involves engaging every layer of the organization, from field technicians to top executives. This inclusive strategy engenders a sense of ownership and accountability across all departments, ensuring that the CMMS is not just a tool, but a part of the organization’s culture.
CMMS Insight: ToolSense boosts teamwork with role-specific interfaces and feedback channels, streamlining everyday workflows. Its mobile features ensure prompt, location-independent maintenance actions. Compre
hensive training resources empower a tech-savvy workforce.
10. Ongoing Training and Support with a Comprehensive Program
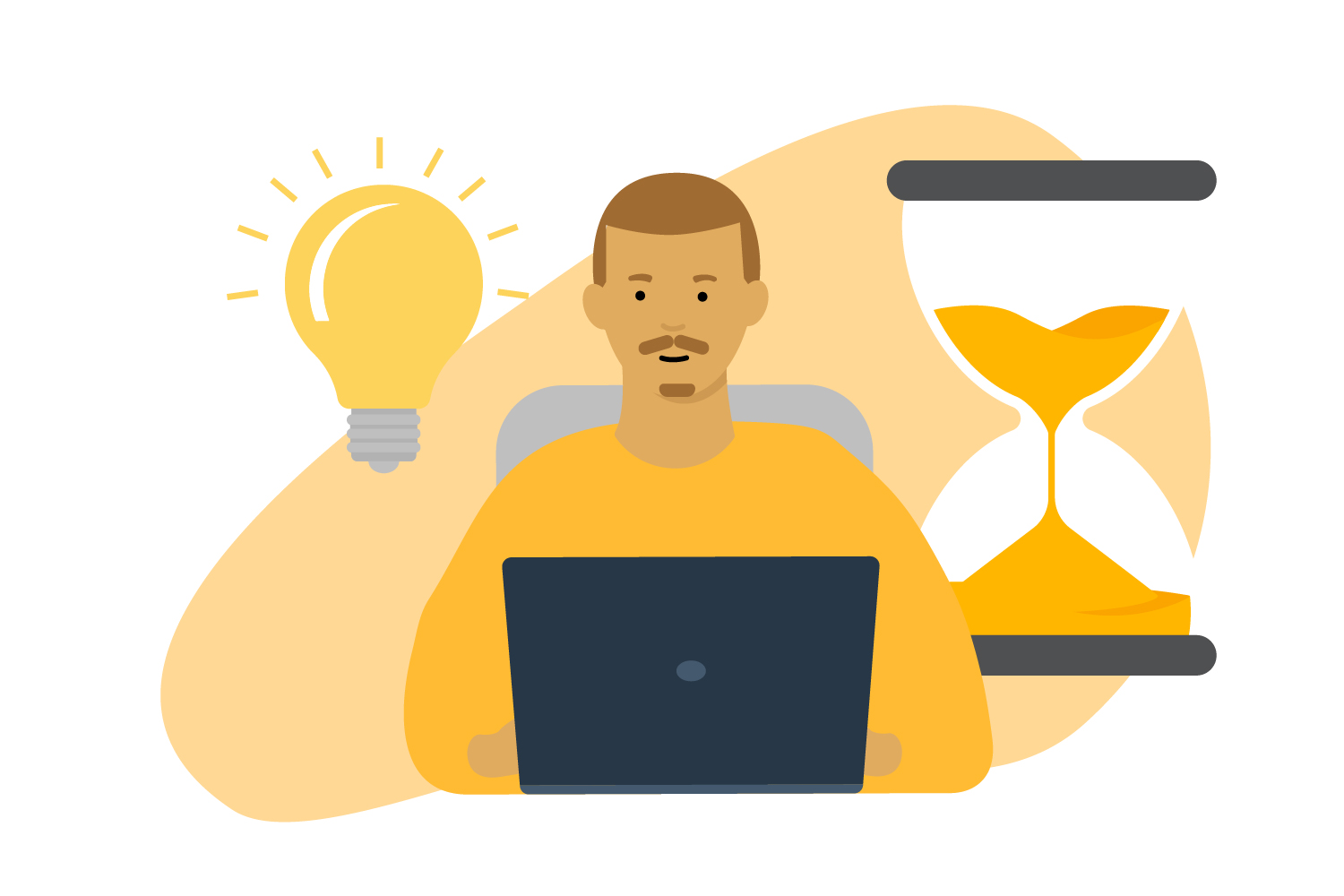
Continuous training and comprehensive support are key to a successful CMMS implementation. Ensuring users are up-to-date with system features and updates is crucial for maintaining system efficiency. Ongoing learning opportunities are vital for user satisfaction and system utilization.
CMMS Insight: ToolSense’s real-time guidance and video-introduction to features simplify onboarding and continuous education. Users can effortlessly learn new features, optimizing the system’s use.
CMMS Best Practices for Quality and Compliance
In CMMS software, quality and compliance focus on placing the right people in appropriate roles, guaranteeing that service providers comply with standards, and maintaining updated maintenance checklists.
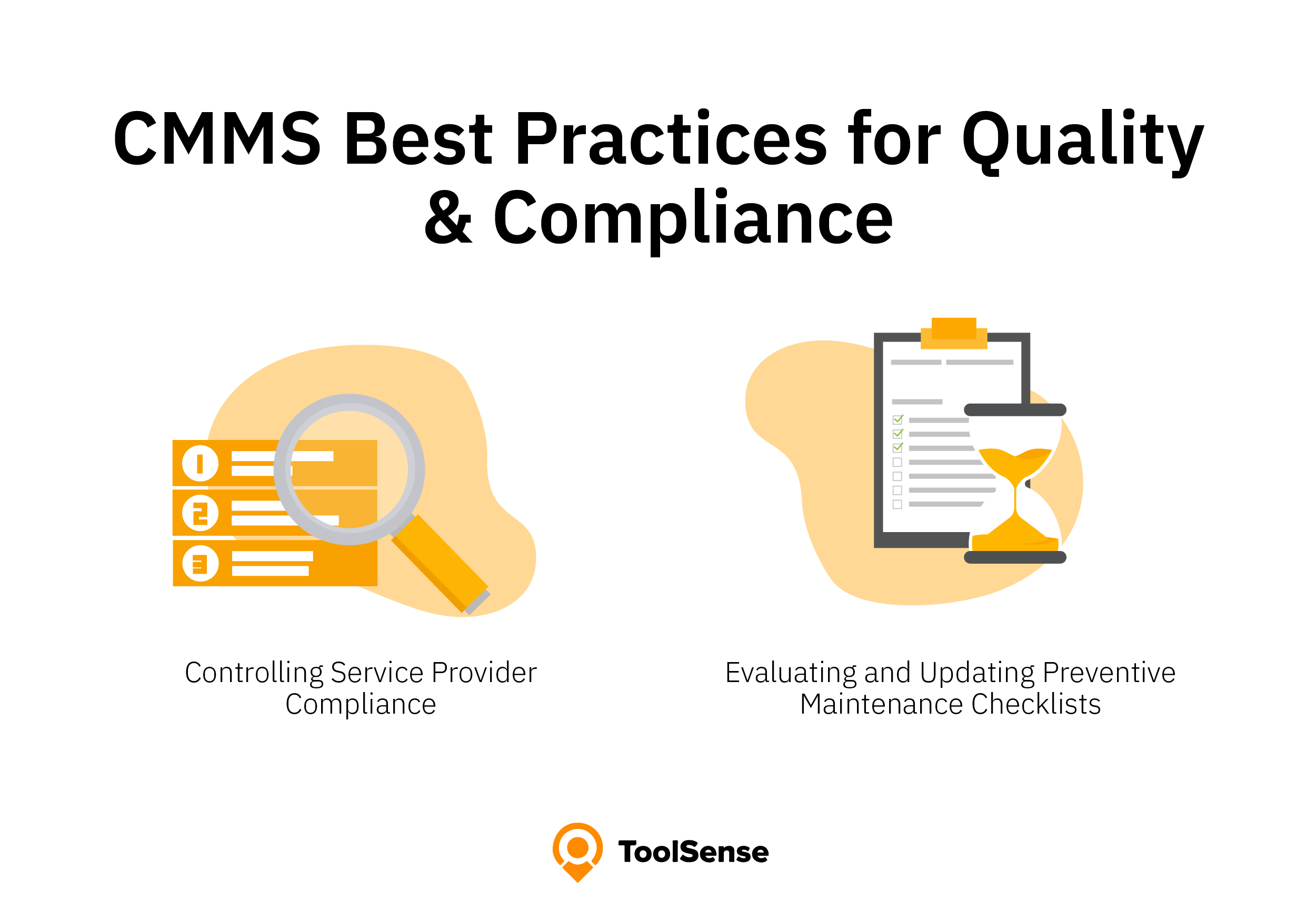
11. Controlling Service Provider Compliance
Ensuring that third-party service providers comply with necessary standards is a crucial best practice in CMMS. This mitigates operational risks and maintains service quality. Integrating compliance management within CMMS systematically tracks and verifies that all contractors meet the required qualifications and standards.
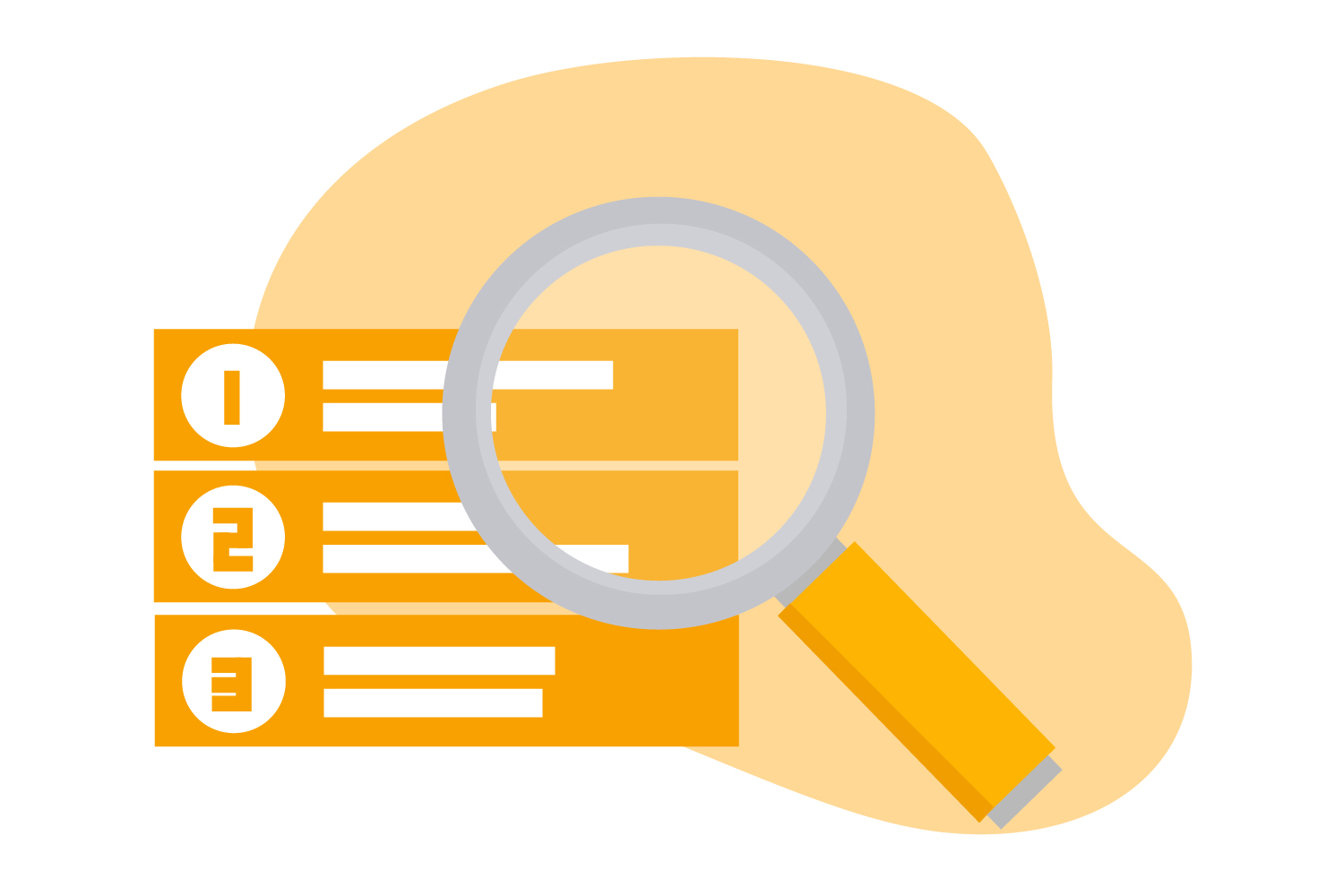
Best Practice Insight: A CMMS greatly enhances maintenance management by keeping a detailed record of contractor certifications and compliance statuses. It can send timely alerts for renewals and verify adherence to standards, ensuring that service providers meet the necessary qualifications consistently.
12. Evaluating and Updating Preventive Maintenance Checklists
Evaluating and updating preventive maintenance checklists is a best practice that ensures your PM tasks stay relevant, effective, and action-oriented. This aligns them with the dynamic goals of the CMMS system, preventing unnecessary maintenance while guaranteeing that critical tasks are carried out.
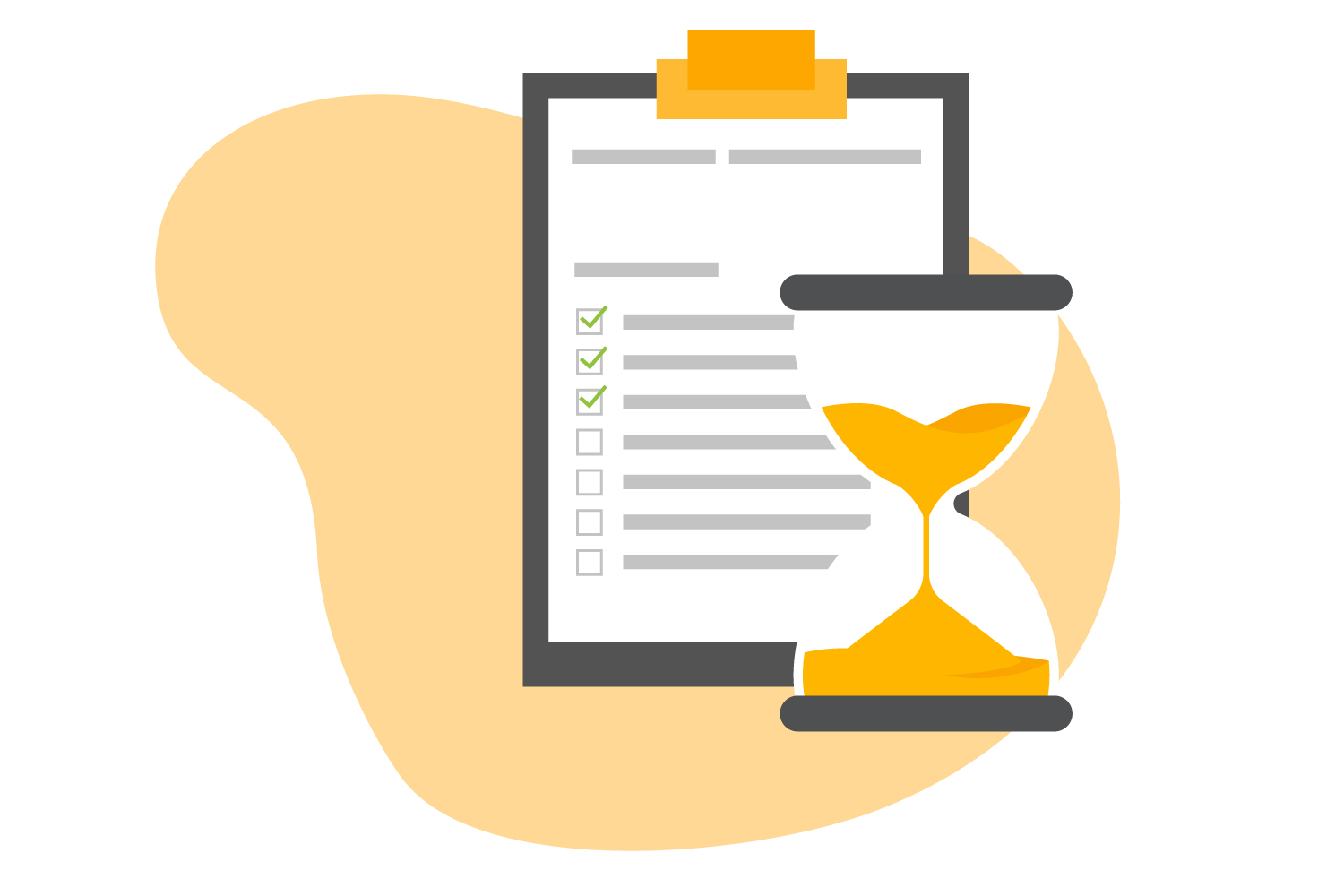
CMMS Insight: Utilizing ToolSense’s preventive maintenance scheduling feature is an excellent tip for keeping these tasks up-to-date. It allows for regular review and adjustments as equipment needs evolve, ensuring that maintenance activities remain aligned with the actual conditions and performance of your assets.
CMMS Best Practices for Innovation and Process Improvement
In CMMS, innovation and process improvement lay the groundwork for enhancing maintenance management. These core principles include:
- Aligning CMMS objectives with organizational goals.
- Ensuring broad stakeholder engagement for comprehensive adoption.
- Extensive training to empower users and optimize system use.
- Standardizing data entry for consistent, accurate information.
- Keeping asset information current for proactive maintenance and downtime reduction.
These foundational elements are interlinked, setting the stage for in-depth exploration of operational efficiency, data management, team integration, quality, compliance, and ongoing innovation in the subsequent sections.
Managing maintenance across all your assets, machines, vehicles and tools is quite a challenge. Build custom workflows in our Asset Operations Platform to easily manage maintenance processes for thousands of assets.
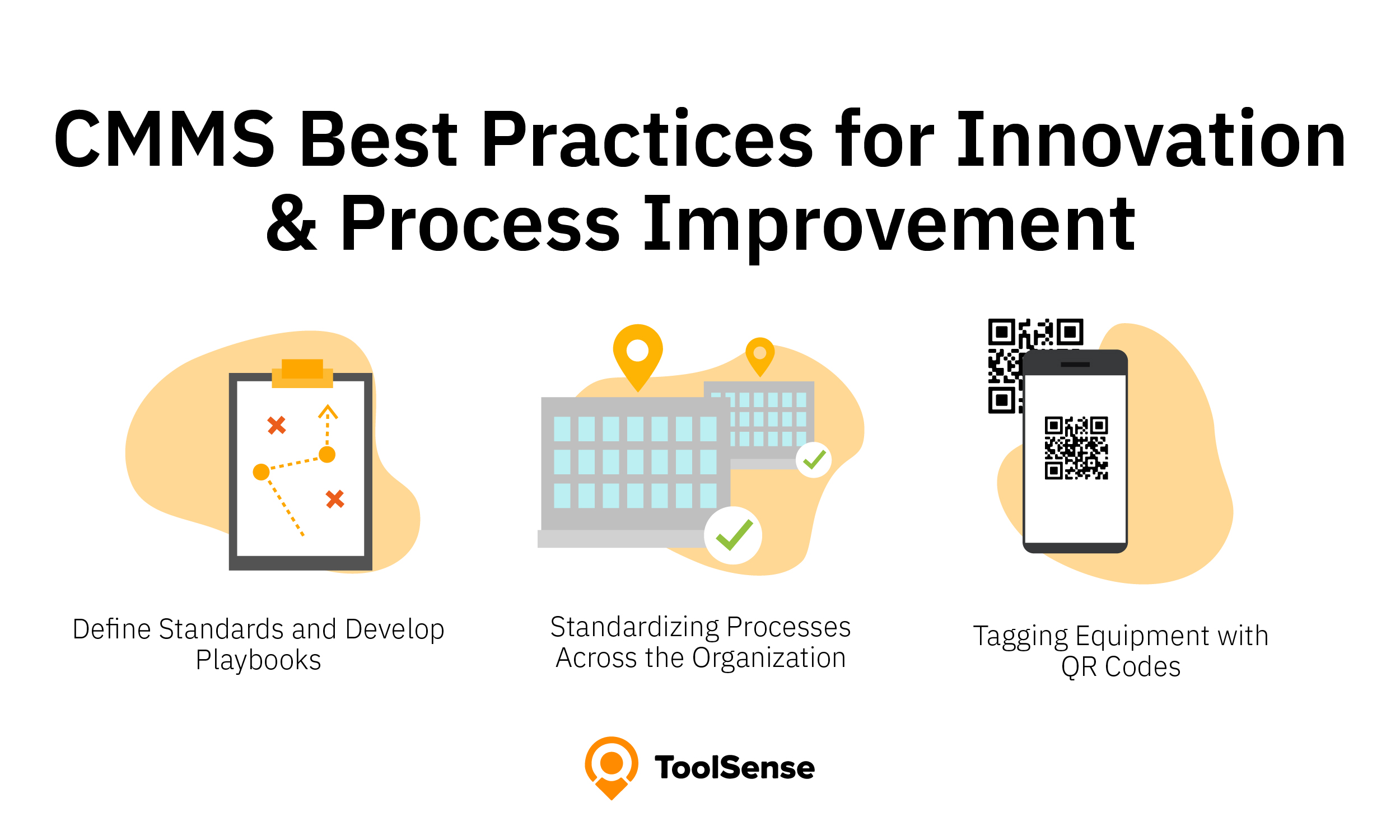
13. Define Standards and Develop Playbooks
Defining standards and developing playbooks is a recognized best practice that benchmarks maintenance quality against industry standards and provides clear instructions for meeting these standards. This approach ensures that maintenance processes are not only automated but also optimized for peak performance.
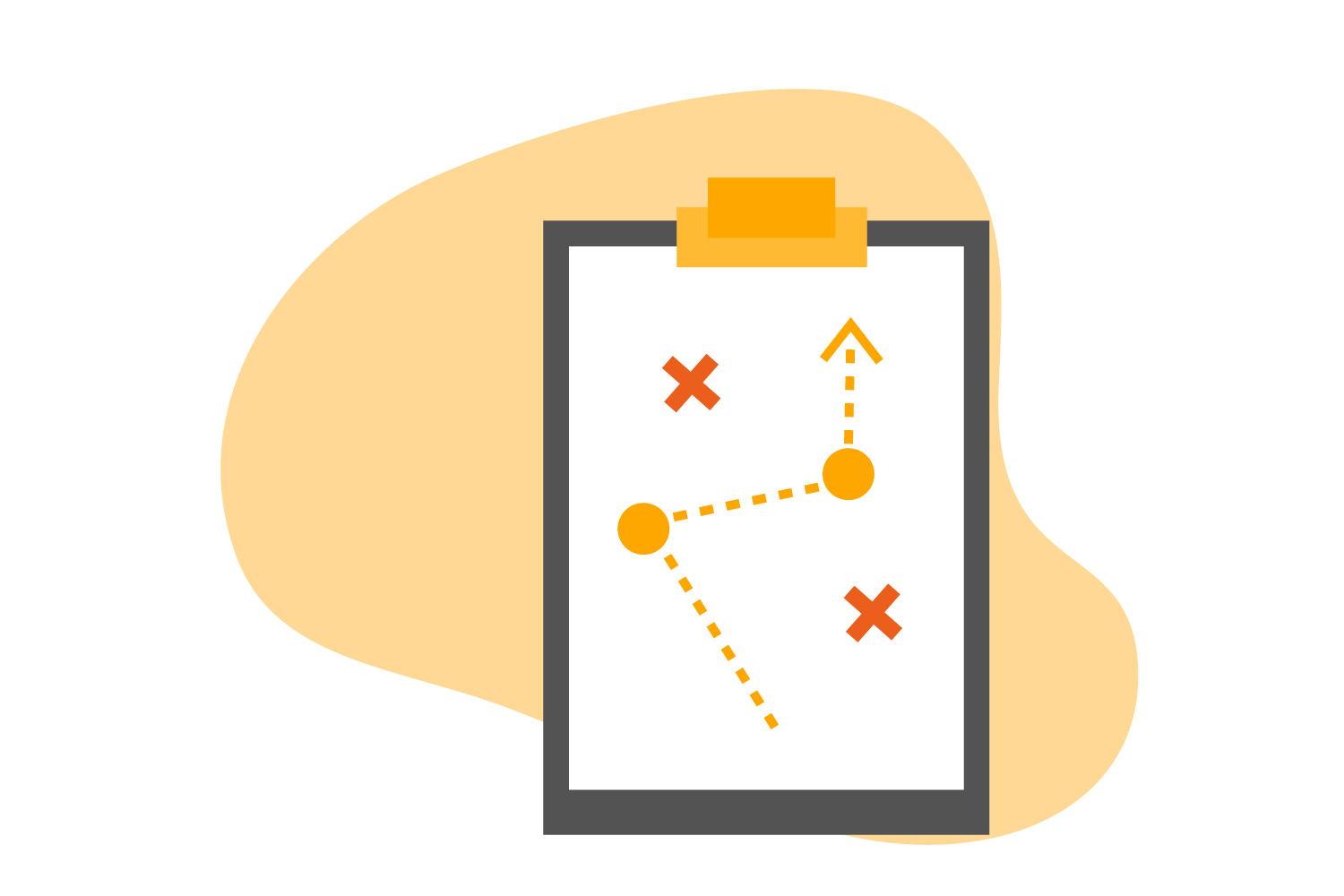
CMMS Insight: ToolSense can serve as a central repository for best practice playbooks, making it simple for teams to access and implement these standards. By utilizing ToolSense, organizations can ensure that their maintenance operations are aligned with industry benchmarks and best practices. Tips for leveraging ToolSense in this capacity include regularly updating the playbooks to reflect the latest standards and encouraging team members to review these guidelines to enhance their understanding and execution of maintenance tasks.
14. Standardizing Processes Across the Organization
Standardizing processes across the organization is a best practice that ensures maintenance procedures are harmonized at all locations, promoting efficiency and consistency to increase productivity. This reduces variability and improves overall maintenance quality. By adopting a standardized approach, organizations can ensure that every team member, regardless of their location, follows the same set of procedures, which streamlines operations and maintains high-quality maintenance work.
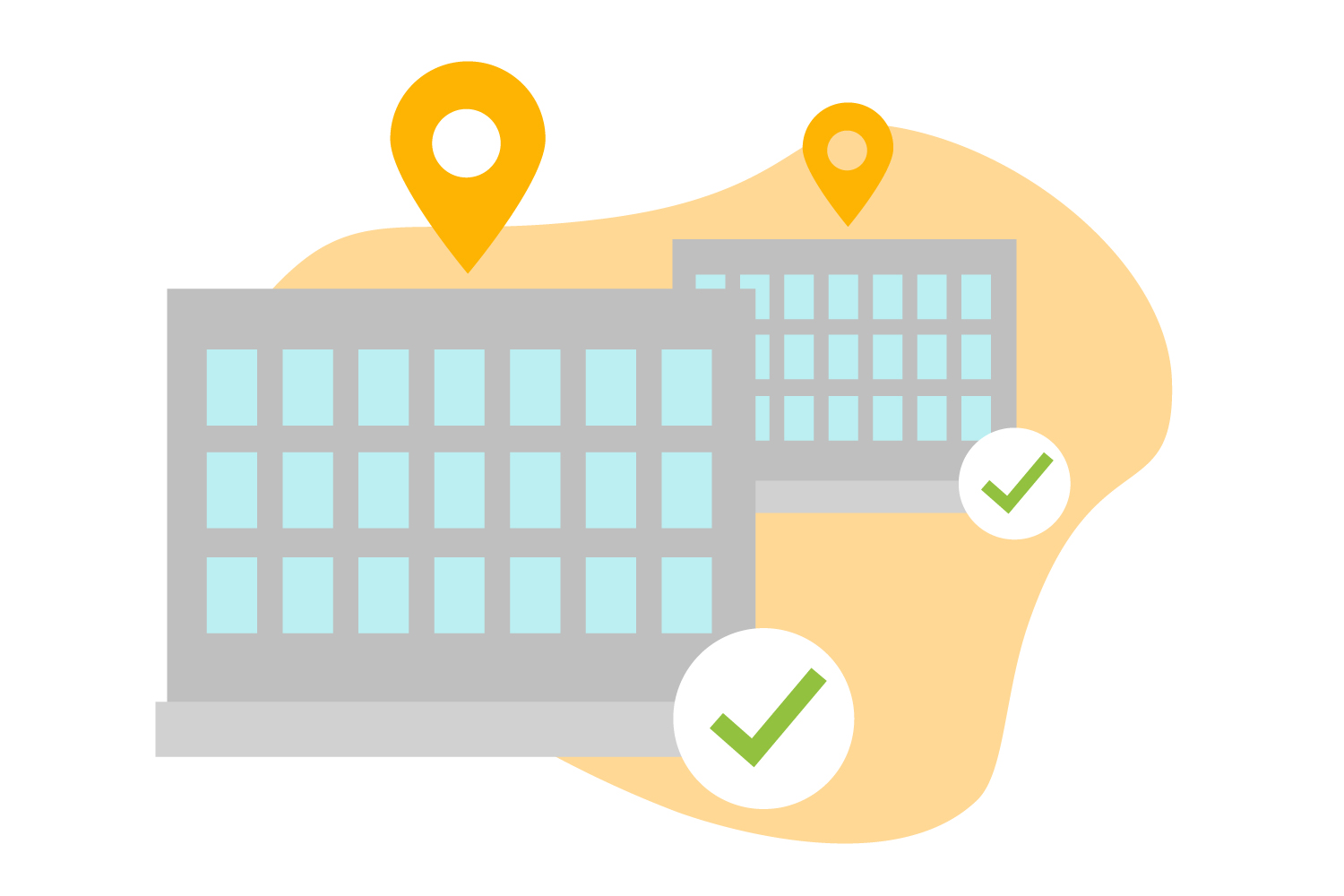
CMMS Insight: ToolSense’s maintenance management software can be effectively utilized across multiple sites to ensure that each location adheres to the same high standards. Tips for implementing this best practice with ToolSense include utilizing its centralized procedure repository to disseminate standard operating procedures to all sites, and employing its training modules to ensure team members are well-versed in these processes.
15. Tagging Equipment with QR Codes
Tagging equipment with QR codes is a recognized best practice that streamlines maintenance management by providing instant access to equipment histories and manuals, thus simplifying documentation and work order management. By implementing QR codes, technicians can swiftly access all necessary information through a quick scan, enhancing efficiency, reducing downtime, and improving maintenance response times.
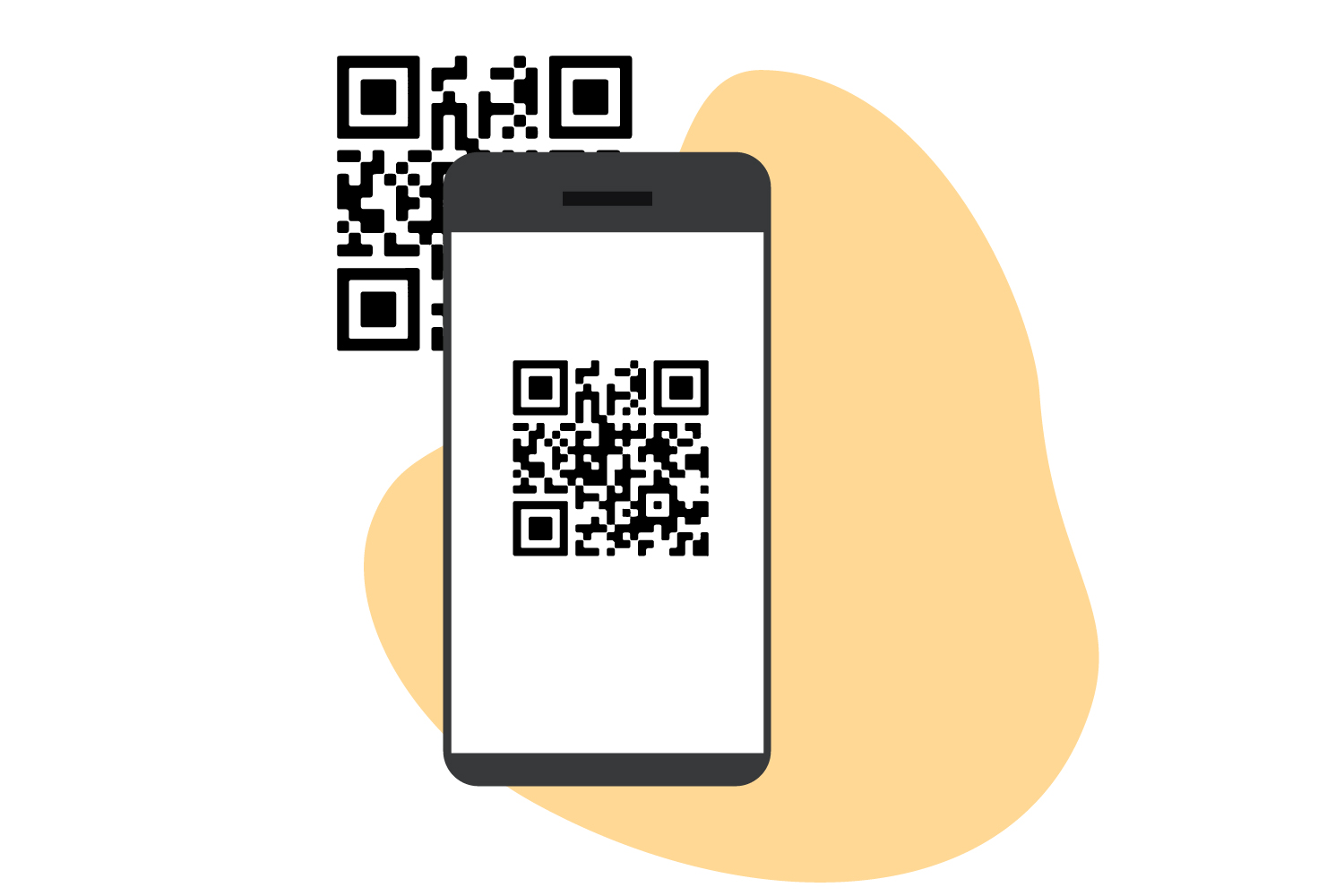
CMMS Insight: ToolSense’s QR code functionality can be leveraged to expedite the process of logging work orders and accessing equipment information. Tips for maximizing the benefits of ToolSense’s QR code capabilities include routinely updating the linked data for accuracy and training maintenance staff on the efficient use of QR scanning for on-the-spot information retrieval.
ToolSense CMMS: An Overview
Adhering to the best practices described in this article, ToolSense CMMS emerges as a perfectly capable solution that streamlines maintenance with a suite of tools for increased efficiency and safety. It replaces outdated methods with a digital solution for comprehensive oversight.
Key features include:
- Effortless Asset Integration: Quick Excel imports for asset lifecycle management.
- Organized Documentation: Centralized storage of all asset-related documents for easy digital access.
- Informed Decisions with IoT: Advanced IoT hardware for tracking machine data, aiding informed decision-making.
- Workplace Safety Management: Regular safety protocols and inspections to maintain a safe work environment.
- Custom Maintenance Workflows: Personalized maintenance reminders and checklists for each asset.
- Minimized Downtime: Proactive maintenance to detect issues early, reducing machine downtime.
- QR Code and Ticketing System: Simplified work order management and spare parts ordering with unique QR codes.
ToolSense CMMS serves industries like construction and hospitality, enhancing maintenance management across numerous assets.
ToolSense is trusted by 700+ companies
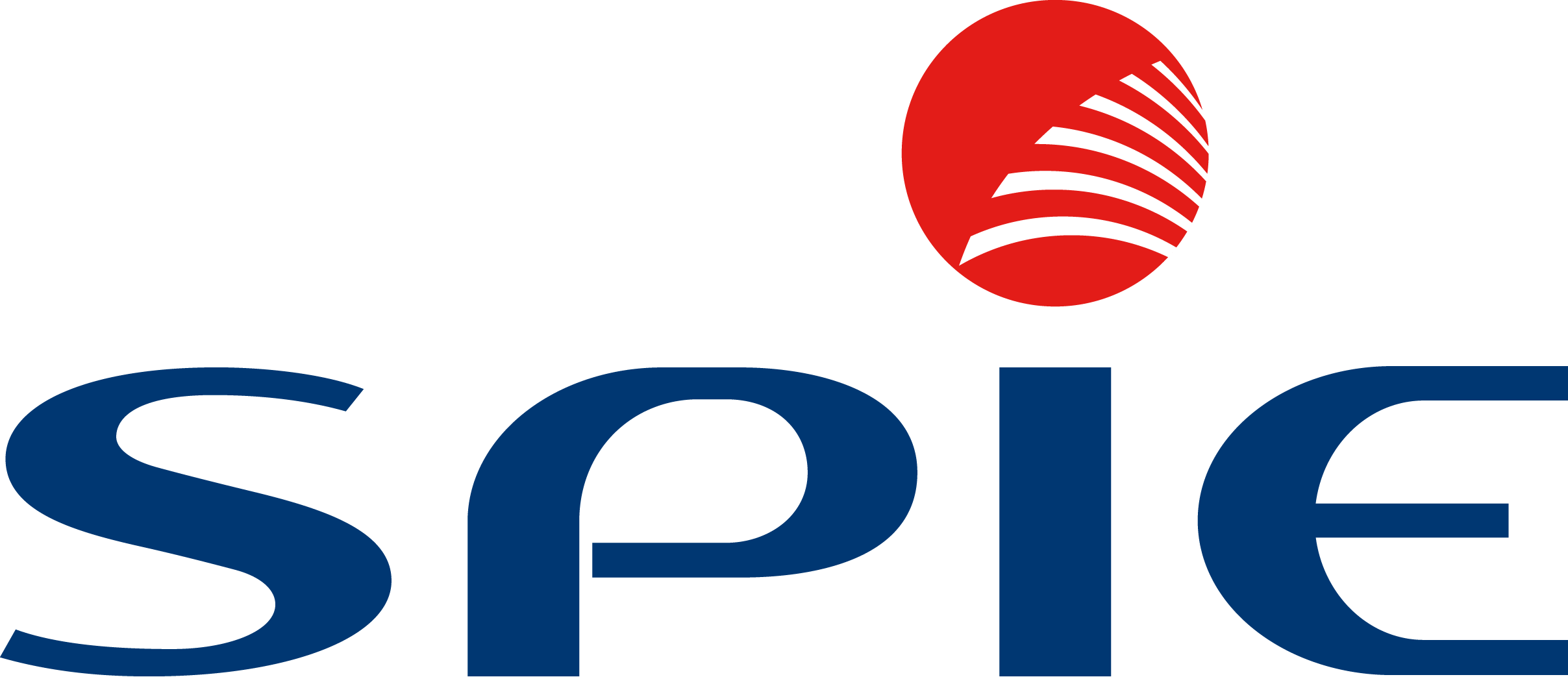
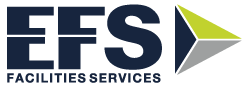
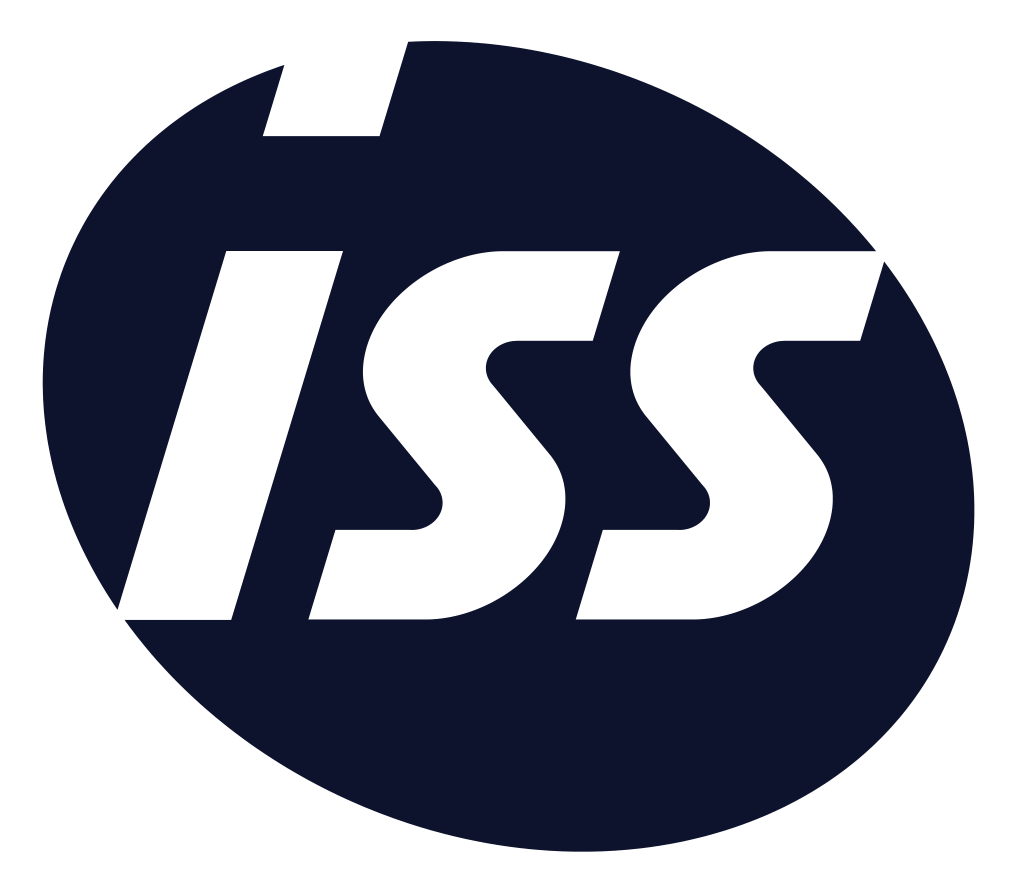
Frequently Asked Questions
The most unique and powerful feature of CMMS is its maintenance scheduling process, which helps managers and technicians smoothly handle maintenance operations for numerous assets and prevents oversight in maintenance scheduling.
Getting the entire organization involved in using a CMMS system is crucial to secure buy-in and support at all levels, fostering a culture of efficiency and continuous improvement. This helps in ensuring successful implementation and utilization of the system.
Leveraging mobile capabilities in a CMMS system enables real-time communication, approval of work orders, task supervision, and progress tracking from remote locations, ultimately boosting productivity and minimizing downtime.
Tracking assets in real-time using a CMMS system is important because it enables organizations to monitor asset health, optimize maintenance scheduling, and enhance overall asset management. This can help prevent costly breakdowns and downtime, leading to improved operational efficiency.
Setting up a comprehensive maintenance schedule in a CMMS system helps organizations streamline preventive maintenance, reduce equipment failures, and minimize downtime.