Have you ever wondered how businesses keep track of countless spare parts, ensuring they’re available right when needed? Imagine the intricate dance of organizing, tracking, and maintaining these parts – a task both crucial and challenging. This blog post dives into the world of parts inventory management, revealing strategies that merge efficiency with innovation. Discover how ToolSense Parts Inventory Management Software transforms this complex process into a streamlined, cost-effective operation, balancing just enough inventory without excess or shortage.
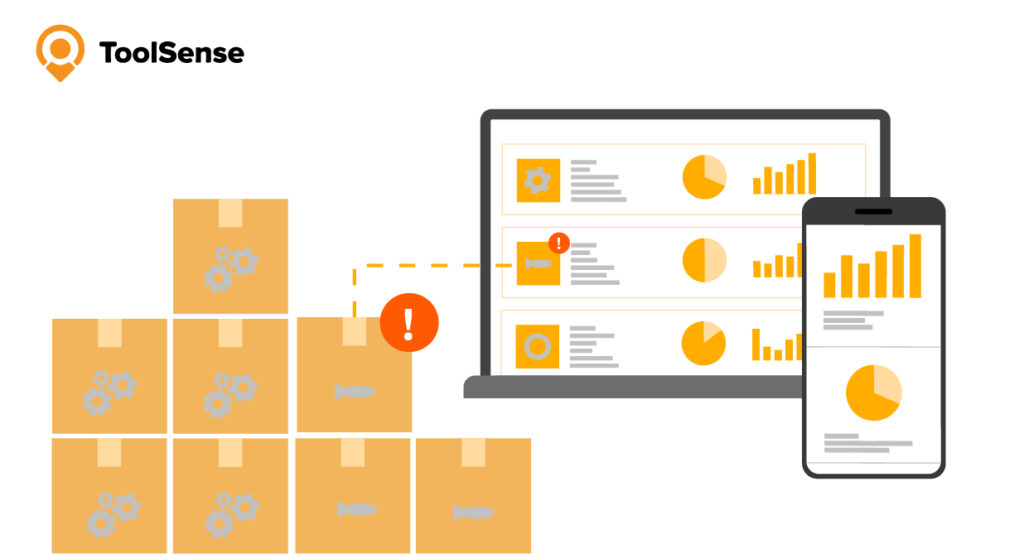
Key Takeaways
- Parts inventory management is essential for asset-intensive industries, leading to cost savings and increased efficiency.
- Strategies such as ABC/XYZ analysis, criticality analysis and the right software solution can optimize inventory management.
- ToolSense Parts Inventory Management Software provides a comprehensive solution to manage spare parts efficiently. With ToolSense, you can keep track of your inventory, machines, tools, and equipment and automate workflows.
The Importance of Parts Inventory Management
Parts inventory management is significant in asset-intensive industries, aiming for productivity, decreased downtime, and cost reduction. It is necessary for the smooth functioning of operations that employees have easy access to inventory data and the whereabouts of spare parts. Given the possible interruption to production schedules due to new equipment downtime, including spares for such equipment in spare parts management systems becomes necessary.
Implementing a well-organized parts inventory management system, such as ToolSense, can lead to significant cost savings, increased productivity, and enhanced overall efficiency. By streamlining processes and reducing the risk of equipment downtime, organizations can ensure that they always have the necessary spare parts on hand without incurring excessive inventory holding costs.
What Exactly Is Parts Inventory Management?
Parts inventory management entails organizing, tracking, and preserving spare parts to guarantee their accessibility for maintenance and repair operations. To achieve this efficiently, organizations can utilize inventory control systems, such as ABC analysis. ABC analysis is a method used to categorize inventory according to the items’ consumption value, with A components having the highest consumption value, B components having an intermediate consumption value, and C components having the lowest consumption value. Maintaining inventory accuracy is crucial for effective ABC analysis.
Another method for categorizing inventory items based on the variability of their demand is XYZ analysis. This method, when managed effectively using a computerized maintenance management system (CMMS), can help organizations optimize their asset management. Conducting criticality analysis, which determines which parts are essential for the successful operation of a system and which parts are of lesser importance, is also crucial in optimizing inventory levels.
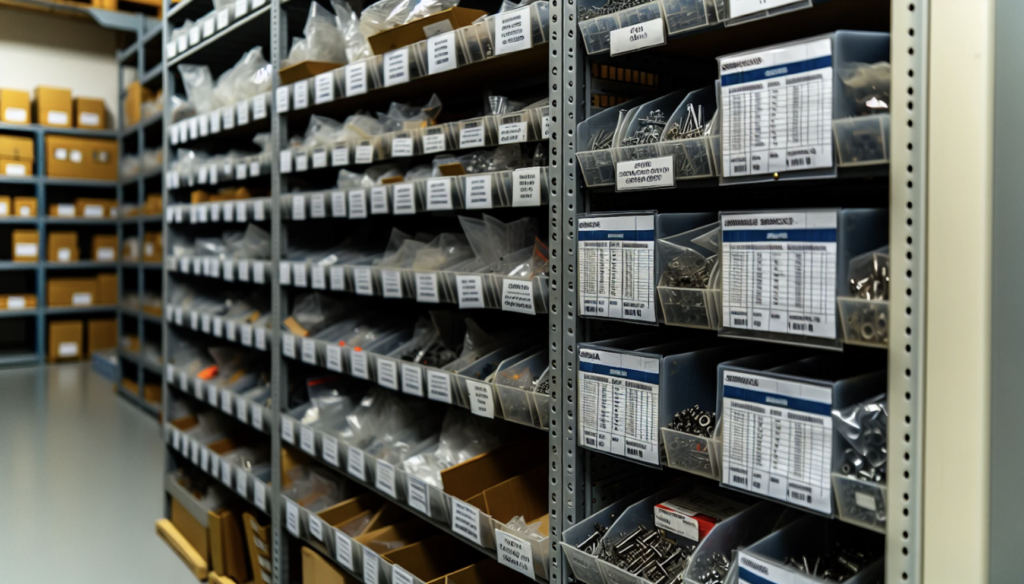
Benefits of Effective Parts Inventory Management
Effective parts inventory management can result in:
- Heightened productivity
- Reduced downtime
- Cost savings
- Enhanced overall efficiency
Maintaining critical replacement parts not only minimizes employee downtime but also prevents inaccuracies, including wrench time assessments. Adhering to best practices for parts inventory management can help organizations reduce costs and ensure that essential spare parts are accessible when required.
Efficient Parts Inventory Management: 6 Strategies to Optimize Your Stock
Managing spare parts inventory is a notable challenge due to balancing both inventory levels and service requirements. This requires consistent oversight and evaluation. Efficient parts inventory management strategies allow organizations to optimize stock levels, simplify processes, and enhance overall operations effectively. Standard operating procedures (SOPs) ensure that employees are aware of the company’s standards for repairing assets, outlining the most effective means of resolving common equipment issues and preserving essential machinery. Utilizing a simple maintenance management software, like ToolSense, is an effective way to implement best practices for work order management. This allows for real-time accountability and accurate inventory records.
1. Adopting a Proactive Maintenance Strategy
Reactive maintenance involves addressing equipment failure or unexpected issues as they arise. On the other hand, proactive maintenance involves regular inspections, preventive measures, and planned maintenance to forestall breakdowns and guarantee optimal equipment performance. The implementation of a proactive maintenance strategy in parts inventory management can provide several benefits like preventing equipment failure, increasing asset availability, reducing maintenance costs, and perfecting inventory control.
Proactive maintenance can significantly reduce potential downtime by:
- Reducing the chances of malfunctions and breakdowns.
- Improving the reliability and availability of equipment.
- Minimizing the risks associated with operating unreliable assets.
- Taking preemptive measures to prevent machine downtime.
- Optimizing the equipment’s performance for maximum efficiency and consistent output.
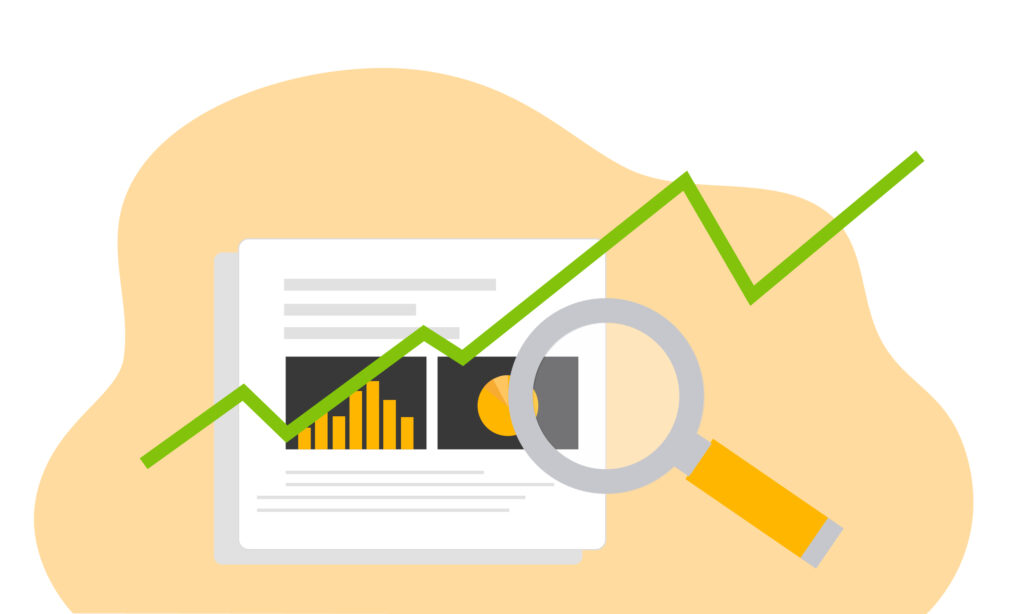
2. Utilizing Parts Inventory Management Software
Inventory management software, such as ToolSense, provides organizations with access to real-time inventory data, making decision-making easier when managing parts inventory. A CMMS consolidates essential maintenance data in one centralized location, accessible by personnel relevant to the maintenance process, including technicians, managers, and stakeholders. All parties involved are relying on a single source of truth for accurate, up-to-date information. This ensures everyone has the same set of information at all times.
Inventory management software, also known as an inventory control system, is designed to:
- Track, manage, and organize a company’s surplus parts inventory.
- Provide real-time inventory tracking and accurate information regarding inventory levels, locations, and conditions.
- Automate tasks to minimize human error and avoid inventory discrepancies, maintenance delays, and cost overruns.
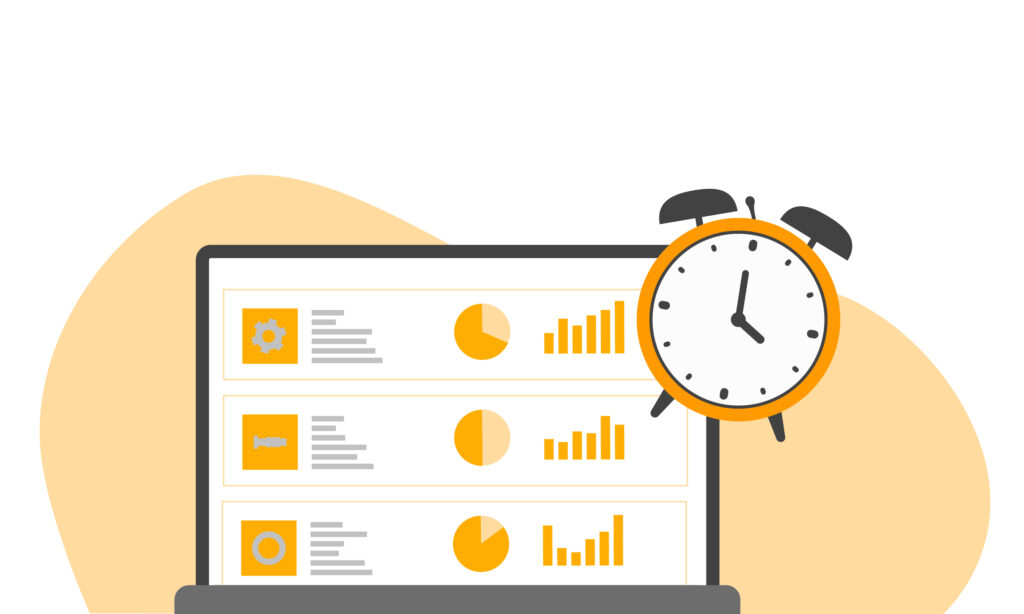
3. Implementing Inventory Control Best Practices
The most effective techniques for inventory control include categorization, labeling, and regular audits, which help maintain accurate stock levels and reduce costs. The implementation of inventory control best practices is necessary to provide organizations with accurate inventory data for easier decision-making.
Organizations can effectively implement spare parts inventory control best practices by:
- Categorizing and labeling their spare parts inventory system.
- Utilizing digitization and automation to monitor inventory levels.
- Performing regular audits.
These practices not only help maintain accurate stock levels but also contribute to overall cost savings, including reduced inventory costs, and improved efficiency in parts inventory management.
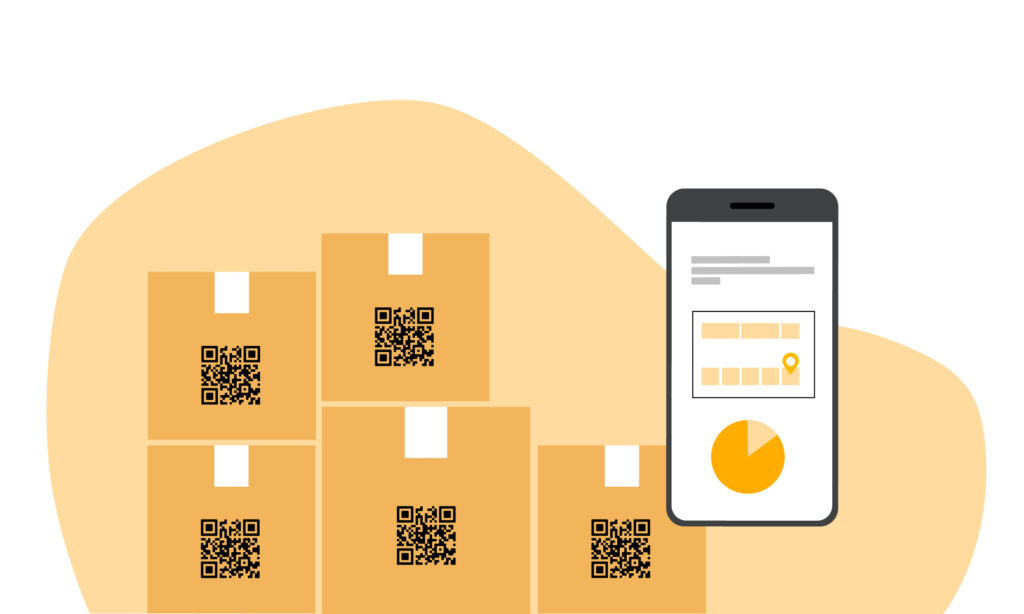
4. Optimizing Stock Levels and Replenishment Techniques
Organizations must strike a balance between having sufficient spare parts on hand and incurring the costs of storage and upkeep. There are three types of spare parts inventory:
- Surplus inventory: parts not in use in the immediate future.
- Stock parts: regularly maintained in inventory.
- Non-stock parts: not typically kept in inventory.
With the use of stock replenishment techniques, organizations can ensure the availability of spare parts when and where needed, without the cost of maintaining excess inventory. Stock optimization techniques seek to balance the need for sufficient spare parts with the associated costs of storage and upkeep. By optimizing stock levels and employing effective replenishment techniques, organizations can ensure parts availability without excess inventory, balancing holding and stock-out costs.
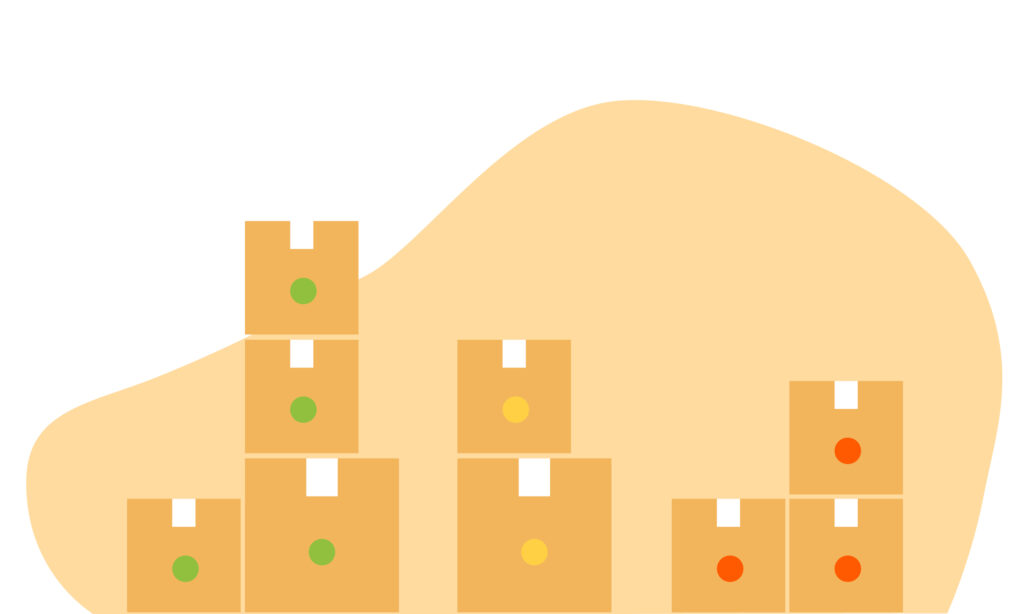
Managing your inventory shouldn’t be hard. That’s why Excel, WhatsApp or Pen & Paper are not the right tools to efficiently manage your asset operations. No matter the manufacturer or type—with ToolSense you are good to go.
5. Enhancing Supplier Management
Supplier management activities ensure optimal efficiency in parts inventory management. Supplier selection is critical as it guarantees a dependable and consistent supply of superior quality parts that fulfill the organization’s requirements. Negotiating contracts and terms with suppliers is essential for creating a beneficial agreement that outlines the expectations of both the organization and its suppliers.
Supplier management involves:
- Sourcing
- Selecting
- Negotiating contracts
- Monitoring supplier performance
Monitoring supplier performance has several benefits, including:
- Ensuring the fulfillment of contract terms by suppliers.
- Identifying potential problems and areas for improvement.
- Enhancing supplier management.
- Ensuring the timely delivery and quality of spare parts.
- Contributing to efficient parts inventory management.
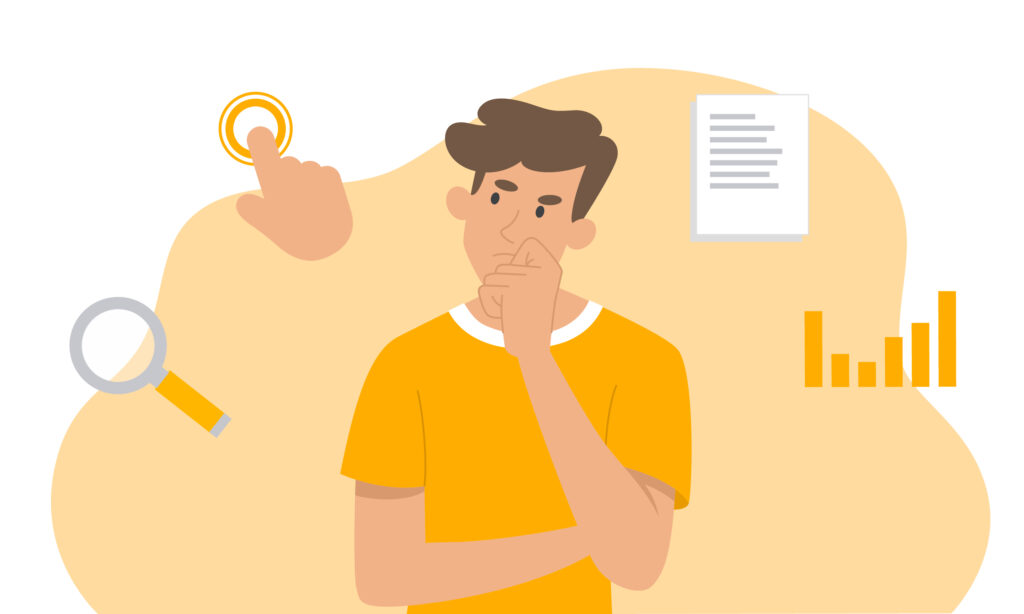
6. Training and Security Measures
Security measures aid in maintaining inventory accuracy, preventing theft, and ensuring adherence to standard protocols. Organizations can implement a “parts counter” with controlled access, badges, or key cards to control access, and cameras to monitor inventory access.
Employee training is essential for ensuring that standard processes and procedures, as well as any technology used to optimize spare parts inventory management, are followed. Staff training is crucial in mitigating inventory loss and enhancing security, as it imparts the necessary knowledge and skills to effectively manage shrinkage issues and implement security protocols, such as access control and surveillance systems.
Furthermore, training encourages employees to stay vigilant and proactive in detecting and preventing theft, thus contributing to overall loss reduction.
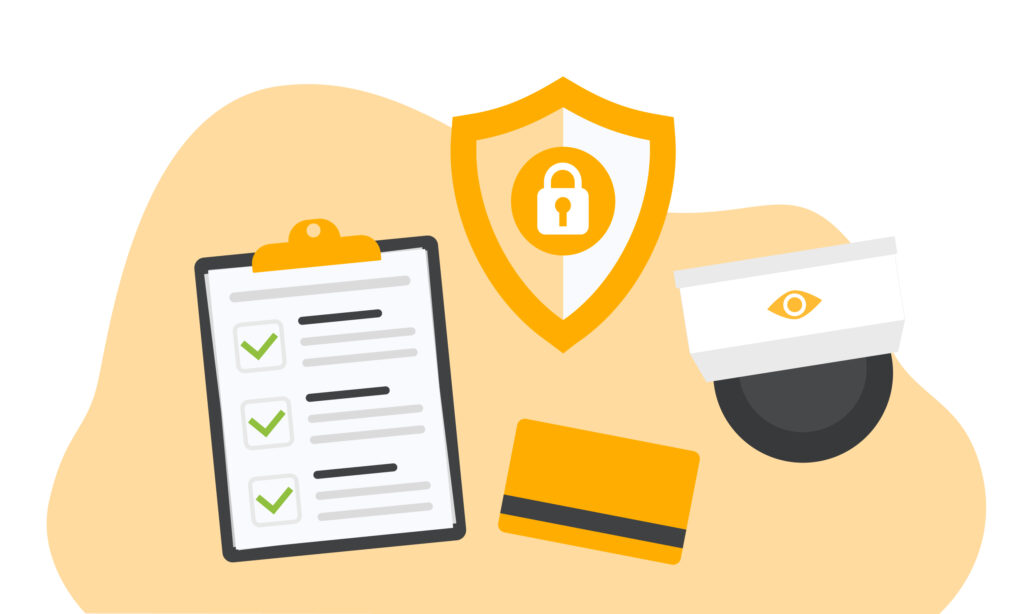
ToolSense Parts Inventory Management Software: A Comprehensive Solution
ToolSense Parts Inventory Management Software provides a comprehensive solution for managing spare parts inventory, optimizing processes, and enhancing overall efficiency. The software offers a range of features, including real-time inventory tracking, real-time inventory value, reorder points and low stock alerts, as well as purchase management and supplier management features. ToolSense spare parts management system is designed to streamline inventory management and ensure that your spare parts are always readily available, making it easier to track spare parts when needed.
ToolSense software facilitates streamlined processes by providing real-time visibility into inventory levels, automating inventory tracking and replenishment, and optimizing inventory management workflows. It helps reduce manual data entry and errors, improves accuracy in inventory counts, and enables efficient inventory planning and forecasting. Furthermore, the software integrates with other systems such as ERP and CRM, enabling seamless data exchange and improving overall operational efficiency.
Features:
- Real-Time Asset and Inventory Tracking
- Advanced Analytics Dashboard and Reporting Tools
- Automated Workflows for Asset and Maintenance Management
- Mobile Accessibility for On-the-Go Management
- Customizable Reports for In-depth Analysis
- Preventive Maintenance Scheduling
- Comprehensive Asset Lifecycle Management
- Fleet Management
- Work Order Management
- Inventory Management
- Document Storage and Safety Compliance Features
- Custom Checklists and Notifications
- SSO, Integrations & Languages
- IoT Hardware Compatibility
Conclusion
Asset-intensive industries require efficient parts inventory management. The implementation of best practices and use of advanced tools such as ToolSense Software can markedly enhance an organization’s productivity, cost savings, and overall operations. As businesses strive to stay competitive in today’s demanding landscape, investing in parts inventory management is not only a wise decision but a necessity for long-term success.
ToolSense is trusted by 700+ companies
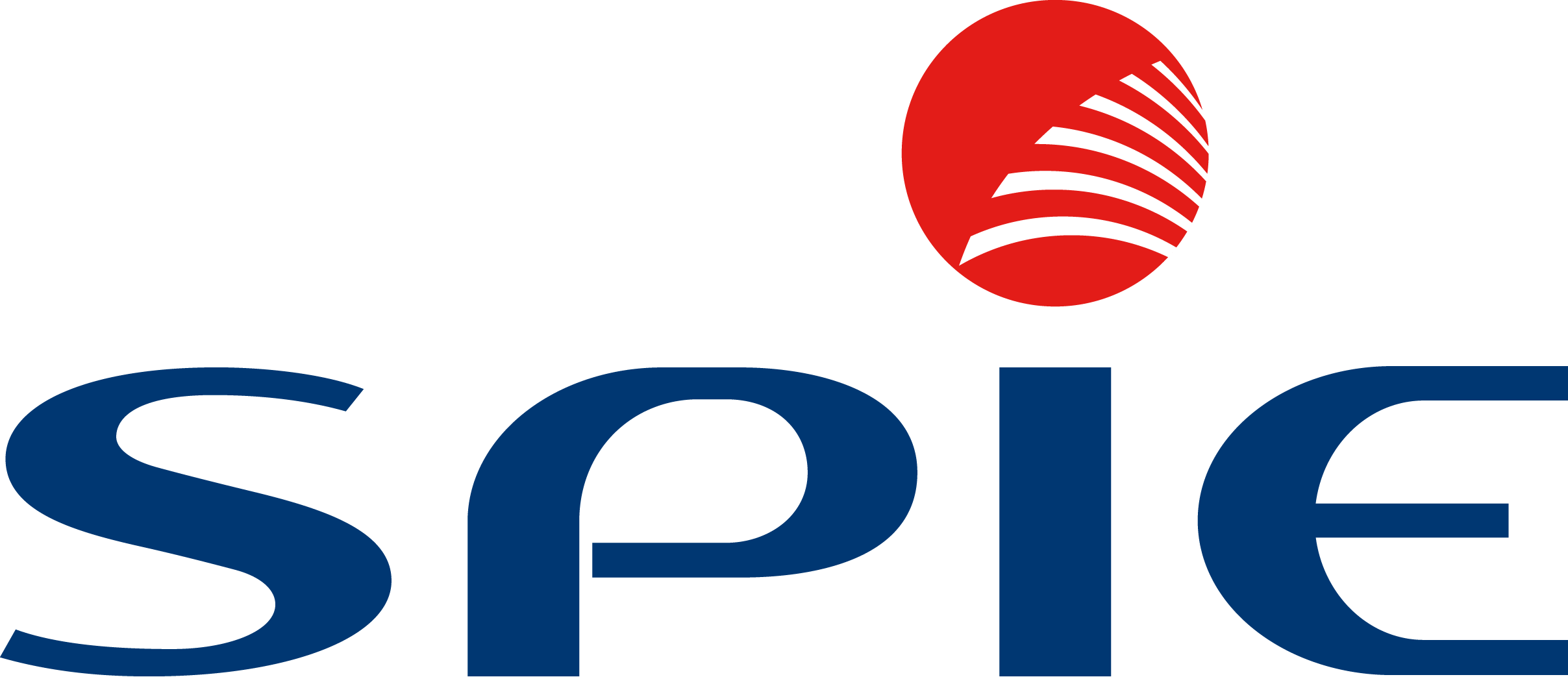
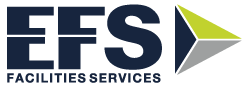
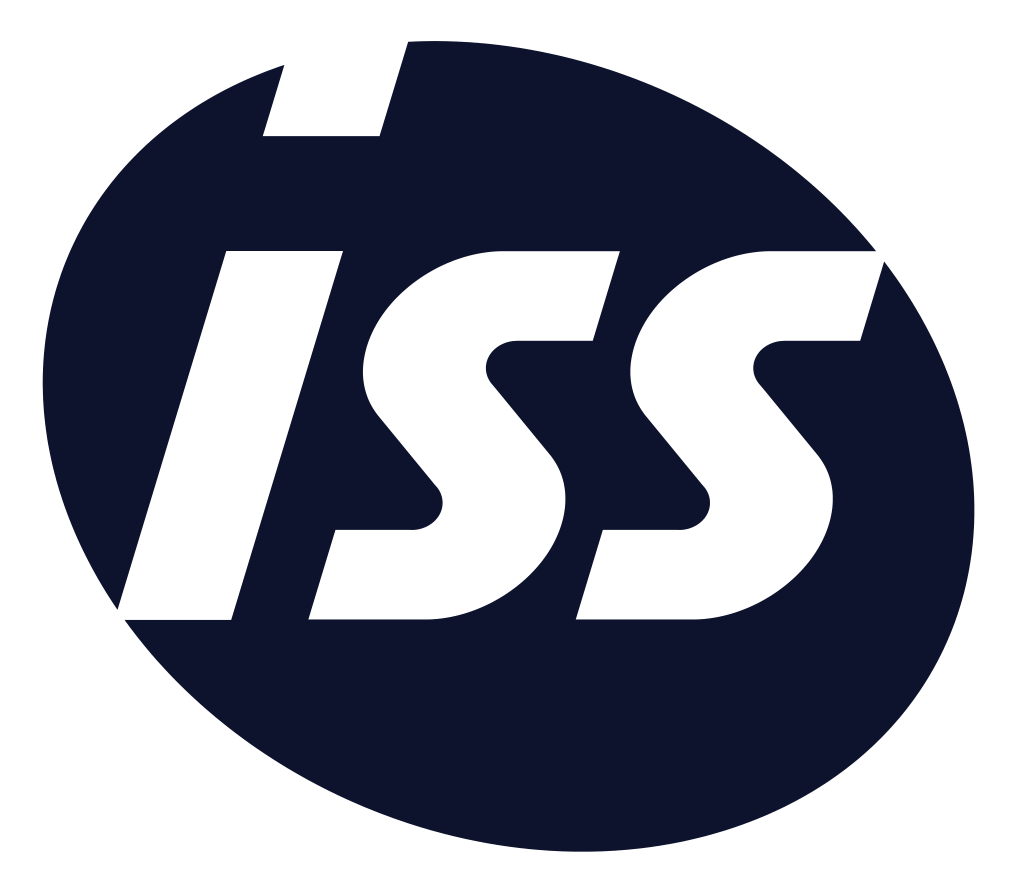
Frequently Asked Questions
Managing inventory for parts requires organizing and tagging each part, creating a robust inventory list, handling the reordering process, maintaining accurate bills of materials, forecasting demand, and training employees.
Inventory management aims to streamline inventories, and common methods include JIT, MRP, EOQ and DSI.
Reactive maintenance responds to equipment issues after they arise, while proactive maintenance takes preventive steps to anticipate and avoid them.
Software can optimize parts inventory management by providing real-time tracking, automating inventory tracking and replenishment, and optimizing inventory management workflows. This results in reduced manual data entry, errors, and enables efficient inventory planning and forecasting.
To ensure successful inventory control, categorize products, label them appropriately, audit regularly, incorporate automation and digitization, and maintain an accurate bill of materials.