Managing construction equipment can be a logistical nightmare without the right tools. Equipment maintenance software helps streamline operations, reduce downtime, and improve safety. But which software is the best for your needs? In this guide, we break down the top software options for 2024. Explore how each platform excels in key areas like preventive maintenance, fleet management, and customization. Find the right solution to optimize your maintenance processes and keep your equipment running smoothly.
Our Top Picks
Definition and Overview of Top Construction Equipment Maintenance Software
Construction Equipment Maintenance Software is a specialized tool designed to streamline the management and upkeep of heavy machinery and construction assets. This software automates various maintenance activities, including scheduling preventive maintenance, tracking equipment performance, and managing work orders. By utilizing construction equipment maintenance software, businesses can significantly reduce downtime, enhance operational efficiency, and ensure compliance with regulatory requirements.
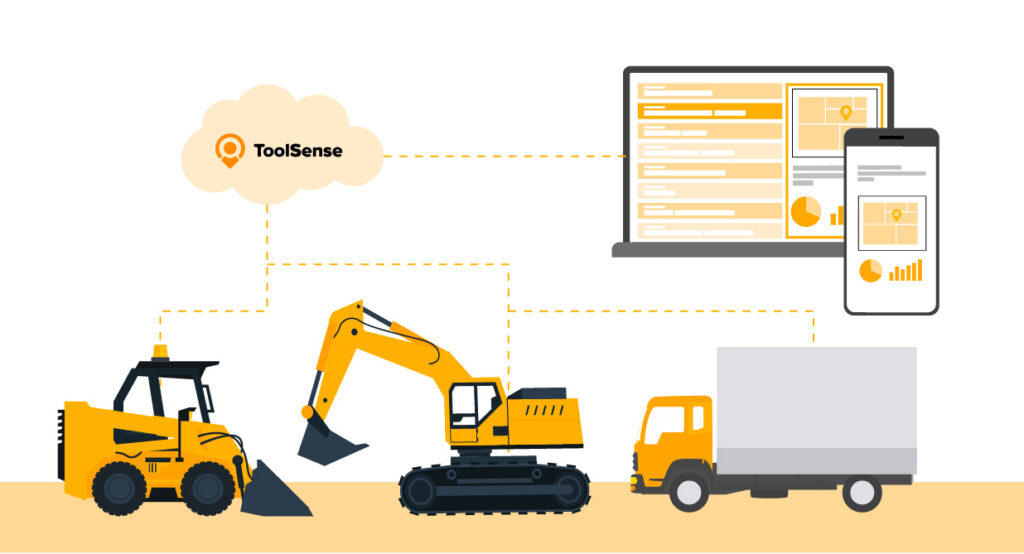
Here are our top choices:
- ToolSense
- Limble CMMS
- Fiix
- Fleetio
- UpKeep
- eMaint
These solutions provide a centralized platform for maintenance professionals to monitor equipment conditions, track maintenance history, and make informed decisions based on key performance indicators. Construction Equipment Software also supports inventory management by keeping track of spare parts and supplies, preventing delays in maintenance tasks due to material shortages. With features like automated reports, sensor data integration, and seamless integration with other systems, construction equipment maintenance software is essential for optimizing equipment performance and achieving significant cost savings.
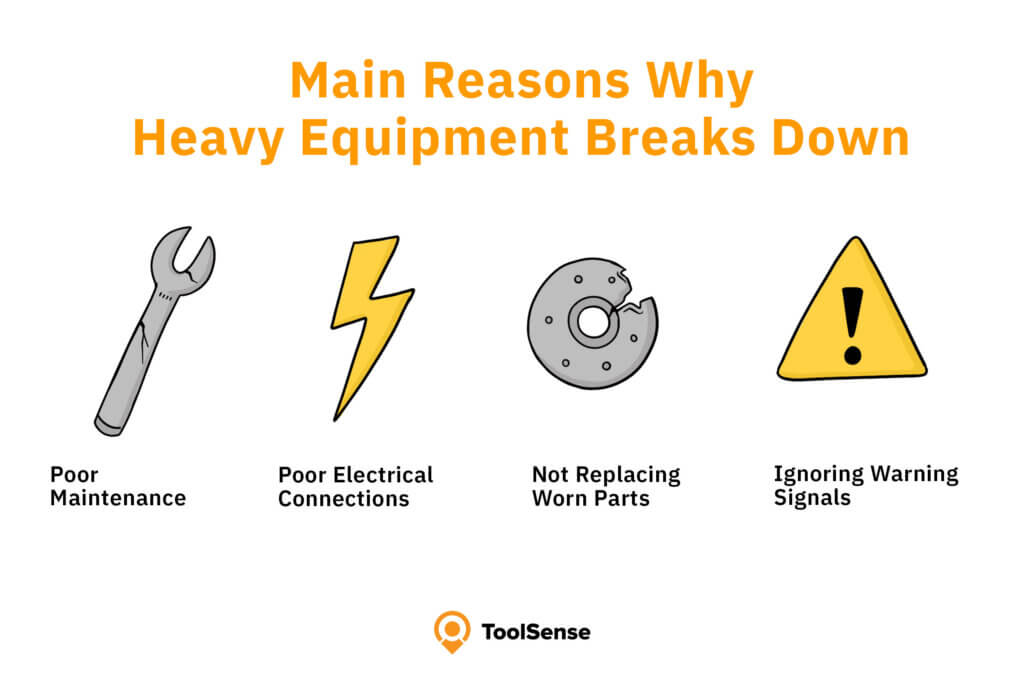
Key Factors to Consider When Choosing Construction Equipment Management Software
Selecting construction equipment maintenance management software involves weighing several key factors to find the best fit for heavy equipment maintenance and construction equipment management. Efficient equipment tracking prevents losses and optimizes tool usage, reducing the risk of misplacement or underutilization.
Advanced scheduling of maintenance tasks minimizes unexpected equipment failures and enhances on-site safety. Regular inspections and servicing through preventive maintenance reduce downtime and extend asset lifespan. Furthermore, centralized work order management improves maintenance planning and execution by organizing maintenance activities requests and maintenance history. Additionally, it is crucial to schedule maintenance activities to ensure optimal performance.
The following factors should be considered:
- Consideration of total ownership costs and return on investment.
- Efficient equipment tracking to prevent losses and optimize tool usage.
- Advanced scheduling of maintenance tasks to minimize unexpected failures.
- Regular inspections and preventive maintenance to reduce downtime.
- Centralized work order management for streamlined maintenance planning.
- Effective inventory management to track spare parts and prevent delays.
- Automated maintenance notifications for enhanced efficiency.
- Reporting and analytics capabilities for informed decision-making.
- Integration with other systems for seamless operations.
- User-friendly interface suitable for varying technical expertise.
- Customization options and scalability to adapt to unique workflows.
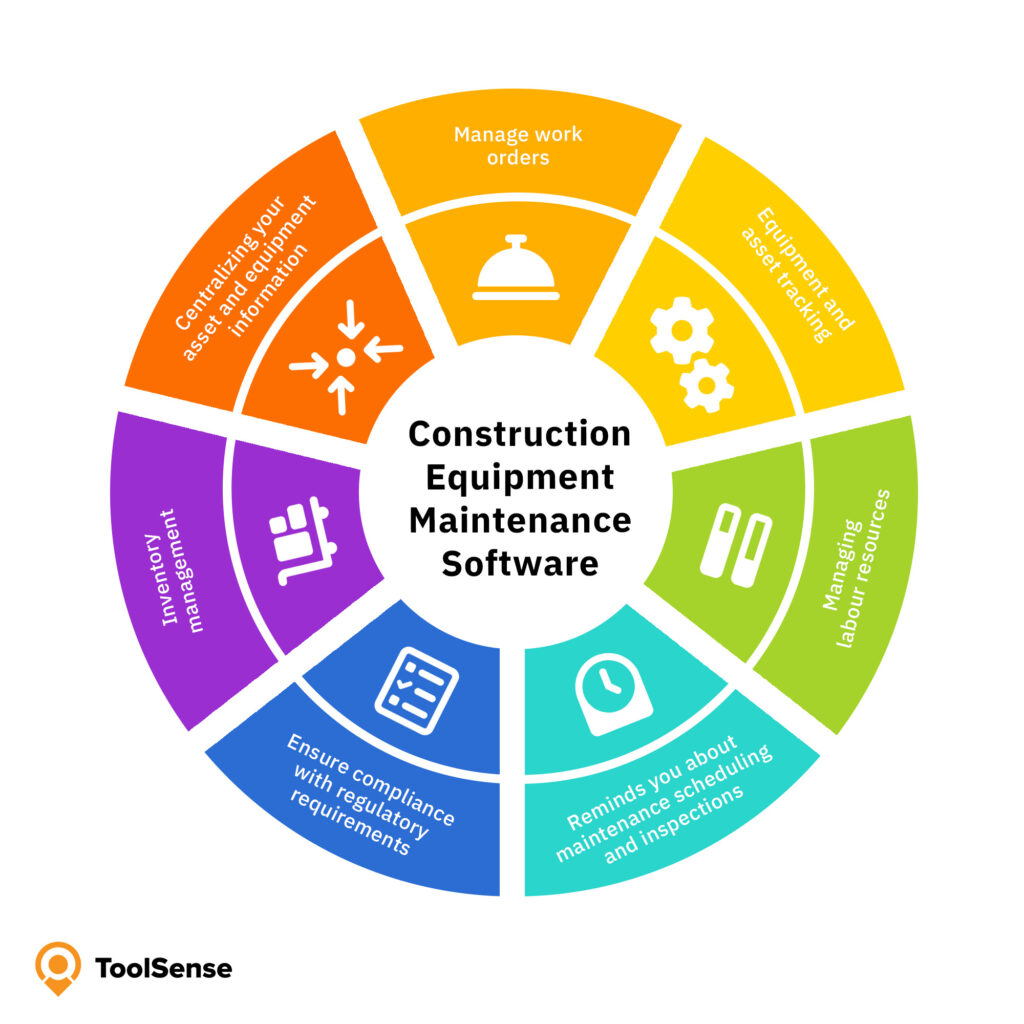
Top 6 Construction Equipment Maintenance Software for Various Needs
Businesses have varied needs for construction maintenance software. Small businesses typically seek budget-friendly, easy-to-use solutions, while large enterprises look for feature-rich tools capable of managing extensive data and complex integrations.
The following sections will provide detailed reviews of the top construction equipment software solutions, highlighting their pros, cons, and unique features.
ToolSense – Best All-in-one Solution
ToolSense excels in comprehensive equipment management, providing a unified platform that eliminates the need for manual tracking methods like Excel spreadsheets. This significantly reduces operational costs and unplanned downtime. Features like easy issue reporting through QR codes and customizable safety inspection checklists streamline asset management and boost operational efficiency.
With ToolSense’s software and equipment maintenance app, you can maximize profits and the lifespan of your heavy construction equipment. Evaluate equipment and vehicle inspections, automate your maintenance workflow and gain insight into asset utilization.
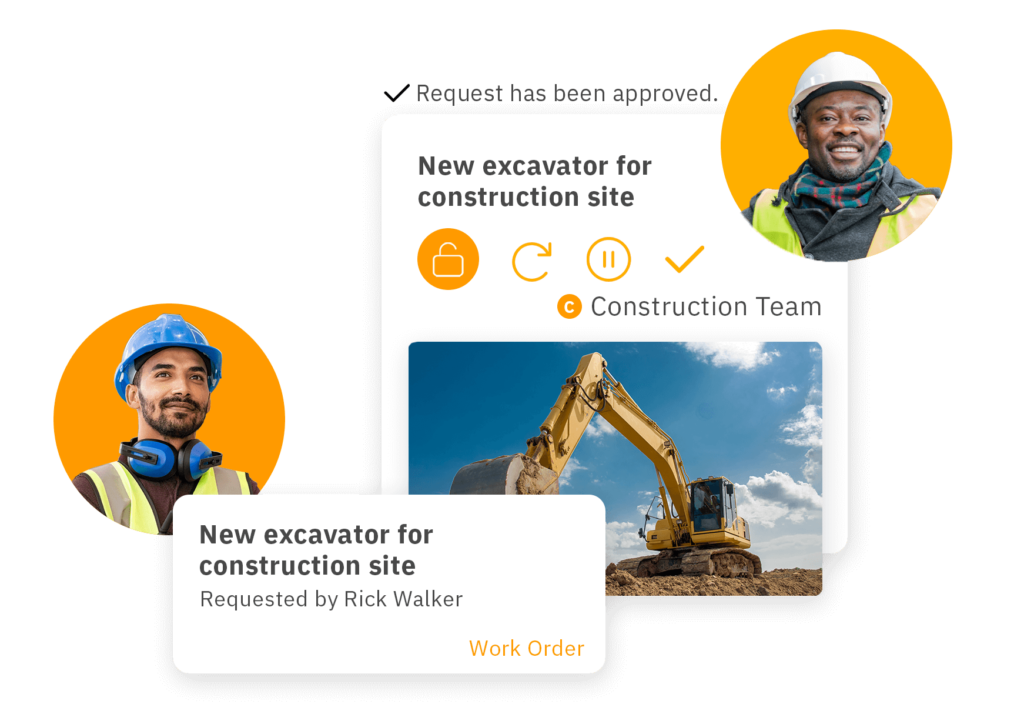
Key Features of ToolSense
- Equipment Data: Record and share construction equipment data from any location effortlessly.
- Simple Workflows: Simplify work requests using a mobile maintenance solution.
- QR Code Issue Reporting: Simplifies the process of reporting issues by scanning QR codes, ensuring quick and accurate communication.
- Real-time IoT Data Tracking: Monitors equipment and assets in real-time to prevent breakdowns and enhance maintenance efficiency.
- Policy Digitization: Allows for the creation and management of digital policies, ensuring all safety protocols are up-to-date and easily accessible.
- Checklist Creation: Facilitates the creation of customizable checklists to ensure compliance with safety standards.
- Comprehensive Reporting: Provides robust real-time reporting capabilities to track safety performance and identify trends.
- Seamless Integration: Integrates with existing systems to centralize safety data and improve operational efficiency.
- Mobile Accessibility: Ensures that safety management tasks can be performed from any location using mobile devices.
- User-friendly Interface: Designed for ease of use, encouraging employee engagement and simplifying safety management tasks.
- Excellent Customer Support: Offers robust support and training resources to help users get the most out of the software.
Pros:
- Comprehensive asset management
- Easy issue reporting through QR codes
- Customizable safety inspection checklists
- Track your construction fleet’s critical data from anywhere
- Manage your entire preventive maintenance workflow
Cons:
- May have a learning curve
- Requires initial setup of IoT hardware
Pricing:
ToolSense offers a free 30-day trial and a free demo tour as well. The exact monthly prizing is tailored to the unique needs of each client and is available upon request.
Rating:
- Ease of Use: 5
- Features: 5
- Customer Support: 4.5
- Security: 4.5
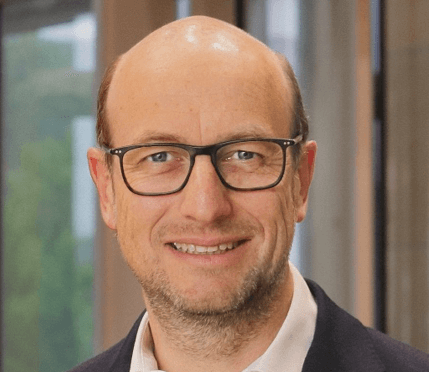
Limble CMMS
Limble’s heavy equipment maintenance software is an all-in-one CMMS solution designed to extend asset lifespan, optimize performance, and reduce downtime. It helps businesses shift from reactive to proactive maintenance with features like preventive maintenance templates, real-time tracking, spare parts inventory management, and data-driven reporting.
The software streamlines maintenance tasks, lowers labor costs, and improves productivity while providing easy-to-use mobile access. It’s tailored for industries managing high-value equipment to improve overall operational efficiency.
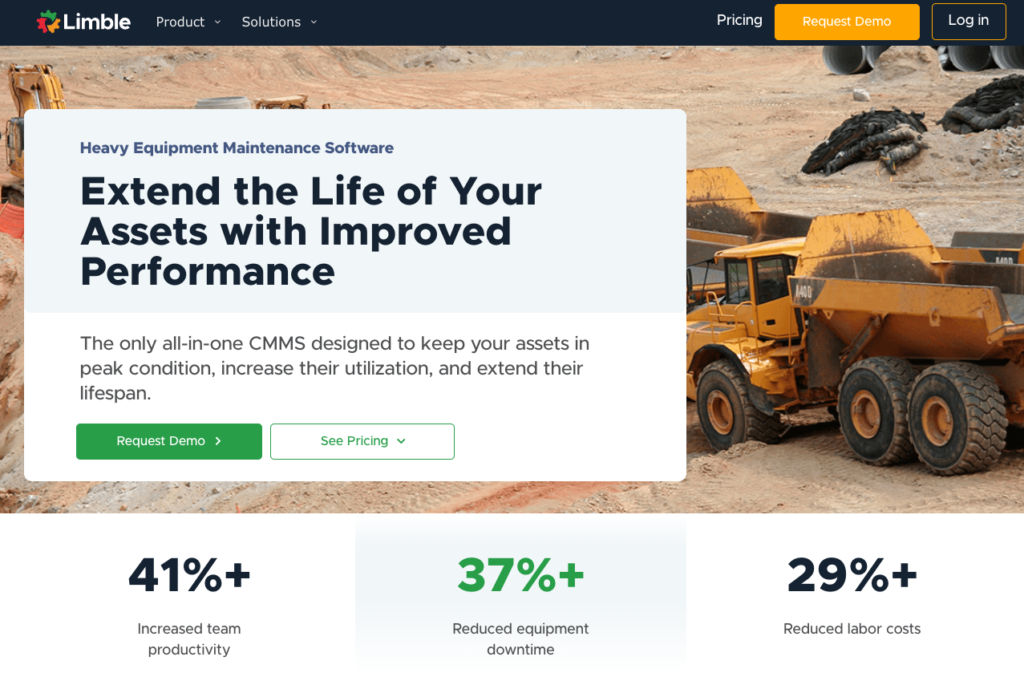
Key Features Limble CMMS:
- Preventive maintenance scheduling
- Real-time asset tracking
- Spare parts inventory management
- Data-driven reporting and analytics
- Work order management
- Mobile access for on-the-go maintenance
- Reduces equipment downtime and labor costs
- Extends asset lifespan through proactive maintenance
Pros:
- Simple and easy-to-learn interface
- 24/7 support
- Automated preventive maintenance schedules
- Comprehensive reporting
Cons:
- Limited customization options
- May be overkill for small operations
Pricing:
Basic (free), Standard ($28 per user/month), and Premium Version ($69 per user/month) available.
Rating:
- Ease of Use: 5
- Features: 4
- Customer Support: 4.5
- Security: 4.5
Fiix
Fiix stands out for its extensive integration capabilities, ideal for businesses seeking streamlined operations through seamless connections. The software integrates with thousands of systems, including popular fleet management tools, via APIs. Partnerships with firms like ZenduIT, MachineMax, and Verizon Connect further enhance its integration capabilities.
Though Fiix’s integration features are robust, the initial setup might be complex and costly. Nevertheless, the seamless data transfer and extensive partnership network make it a powerful tool for enhancing operational efficiency.
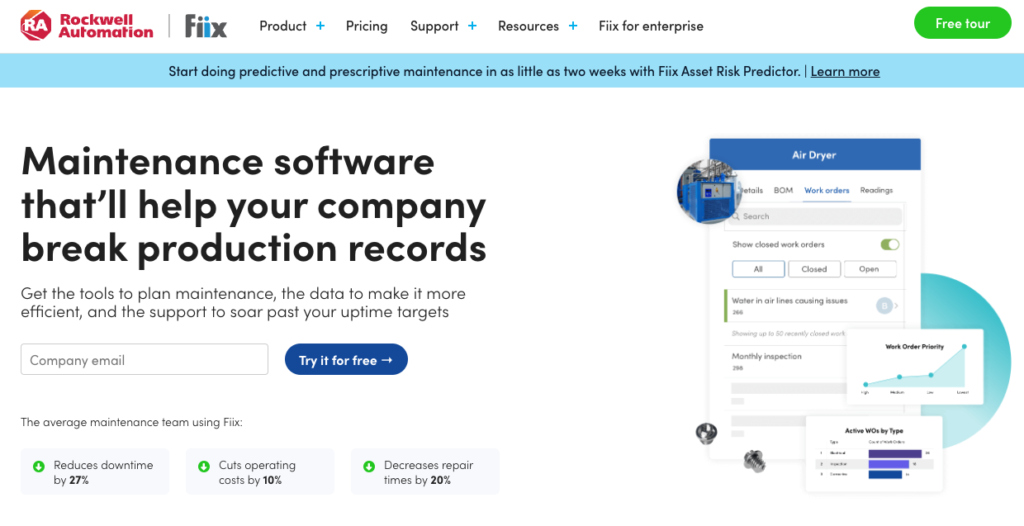
Key Features Fiix:
- Easily create, manage, and track work orders. Automate work order assignments and analyze them with insights reports.
- Track asset performance, build asset hierarchies, and access asset details instantly, including maintenance history.
- Schedule maintenance tasks based on time, usage, or sensor data to reduce equipment downtime.
- Manage spare parts inventory with alerts for low stock and parts forecasting to prevent stockouts.
- Customizable dashboards and detailed reports allow tracking of key performance indicators (KPIs) like maintenance costs and downtime.
Pros:
- Extensive integration capabilities
- Seamless API connections
- Partnerships with major companies
Cons:
- May be complex to set up
- Potentially high costs
Pricing:
Free, Basic ($45/User/Month) and Professional Plan ($75/User/Month) available.
Rating:
- Ease of Use: 5
- Features: 4
- Customer Support: 4.5
- Security: 4
ToolSense is trusted by 700+ companies worldwide
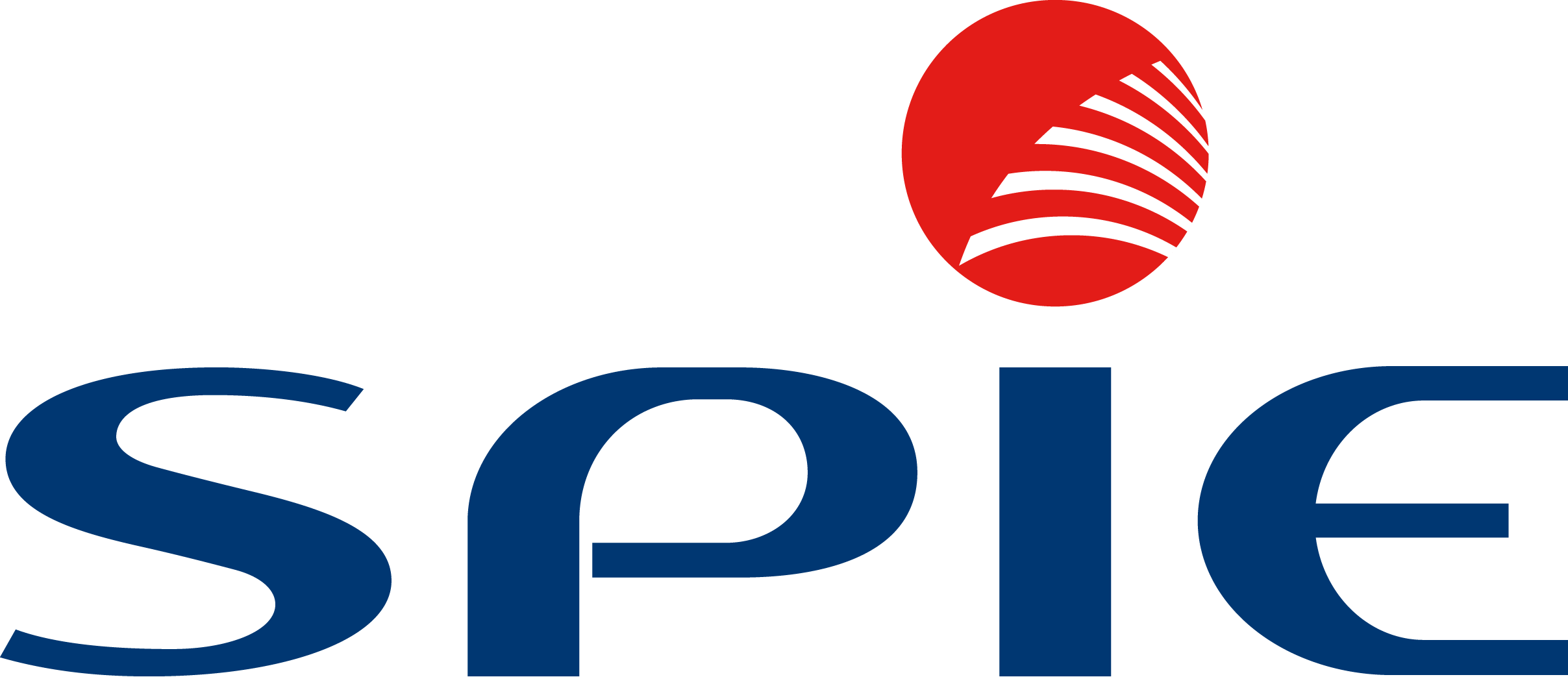
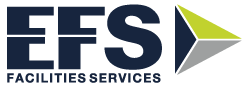
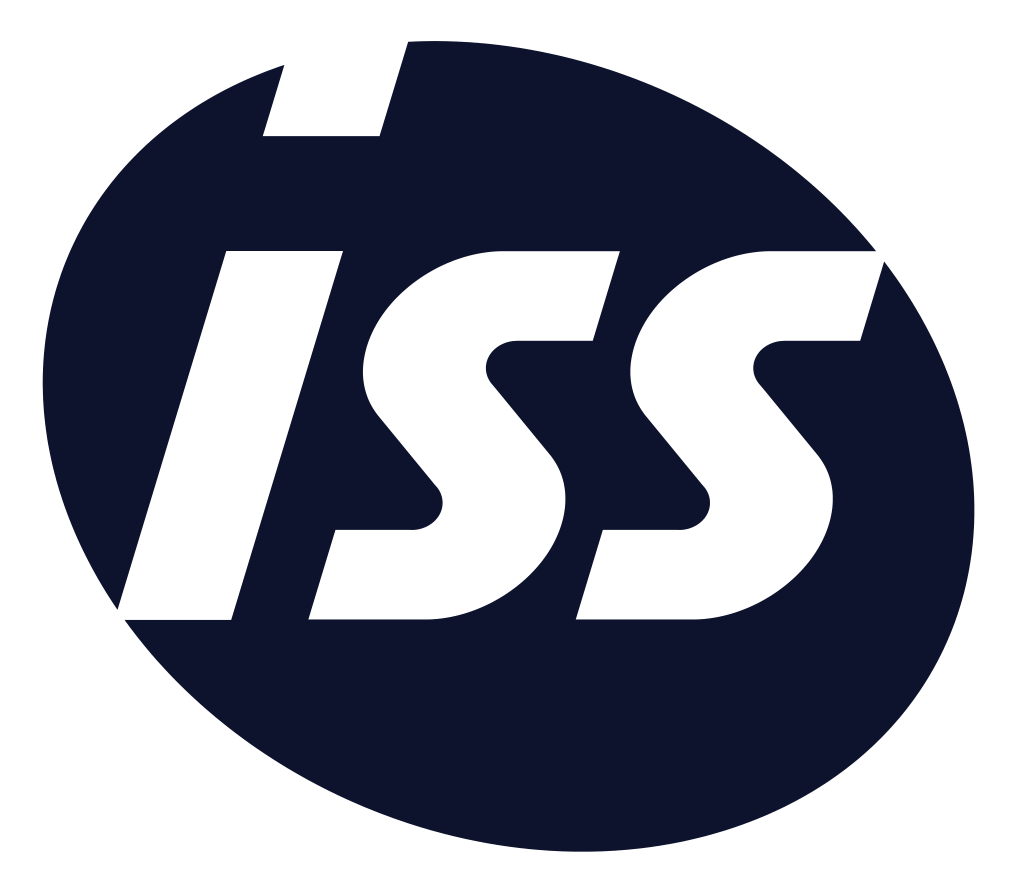
Fleetio
Fleetio excels in managing all aspects of construction equipment and vehicle operations on a single platform. It provides detailed tracking of asset utilization, helping businesses determine the true total cost of equipment. Customizable reporting features measure operational success and provide insights into fleet performance.
While Fleetio’s robust features focus primarily on fleet management, it may not suit companies seeking a more comprehensive maintenance solution. The higher learning curve may require initial training. Nonetheless, it remains a top choice for detailed fleet management.
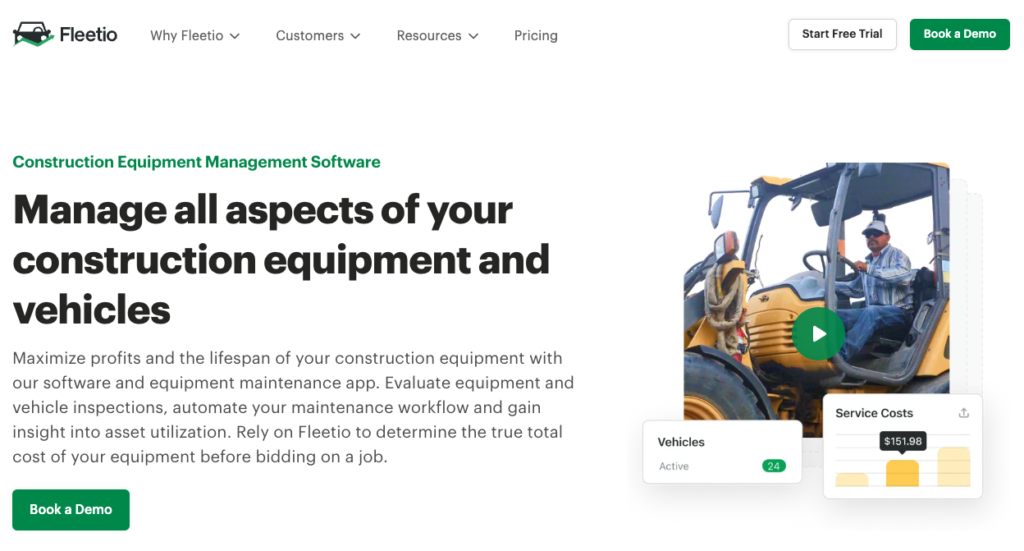
Key Features of Fleetio:
- Easily manage and track the location, usage, and condition of construction equipment in real-time.
- Automate maintenance schedules based on usage, meter readings, or time intervals to prevent breakdowns and extend equipment life.
- Streamline maintenance workflows by managing work orders digitally, assigning tasks, and tracking their completion.
- Perform equipment inspections using mobile devices to ensure equipment is safe and operational.
- Track spare parts inventory and receive alerts for low stock levels to avoid delays in repairs.
- Manage equipment maintenance from anywhere with a mobile app that supports offline functionality.
Pros:
- Comprehensive fleet management
- Detailed tracking of asset utilization
- Customizable reporting features
Cons:
- Limited to fleet management
- Higher learning curve
Price:
- Essential ($5/Vehicle/Month), Professional ($7/Vehicle/Month) and Premium Plan ( ($10/Vehicle/Month) available.
Rating:
- Ease of Use: 4,5
- Features: 4.5
- Customer Support: 4
- Security: 4
UpKeep
UpKeep is a mobile-first solution, allowing maintenance teams to manage operations and work orders from any location. Users can efficiently create, manage, and complete work orders, blending traditional methods with modern technology. Mobile access enables field personnel to easily obtain essential information and updates while on-site, boosting productivity and safety.
UpKeep excels in mobile accessibility, though its limited desktop functionalities and reliance on internet access may pose challenges. For teams always on the move, its real-time updates and seamless mobile access make it an excellent choice for increasing uptime and tracking key performance indicators.
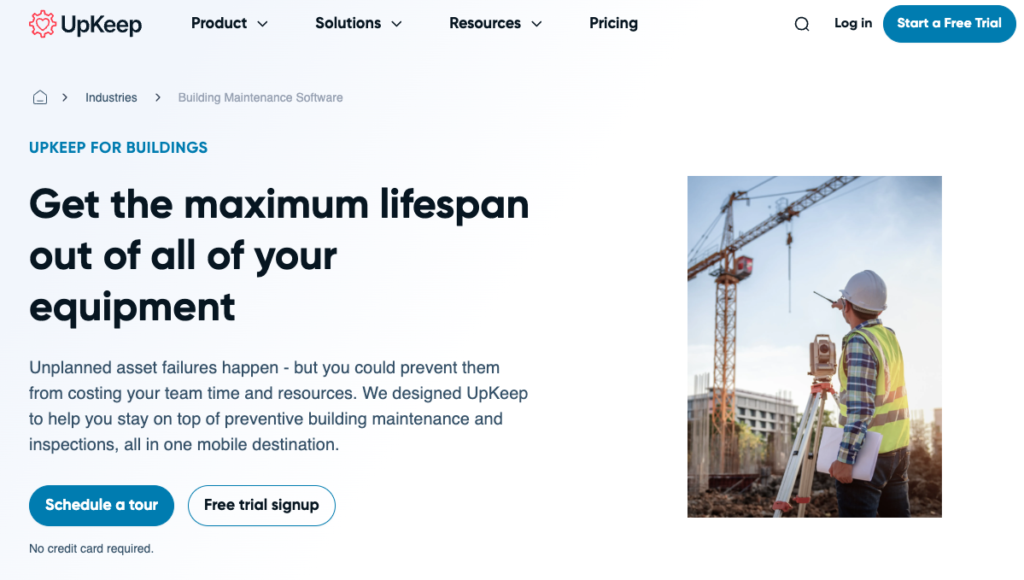
Key Features of UpKeep:
- Create, assign, and track work orders efficiently.
- Automate and schedule maintenance tasks to avoid unexpected equipment breakdowns.
- Track the location, condition, and lifecycle of construction equipment.
- Manage spare parts and equipment inventory with real-time tracking and low-stock alerts.
- Enable field technicians to access work orders, update equipment status, and conduct inspections via a mobile app.
- Generate reports on maintenance activities, costs, and equipment performance for better decision-making.
Pros:
- Mobile-first design
- Efficient work order management
- Real-time updates
Cons:
- Limited desktop functionalities
- Requires internet access
Pricing:
Starting from $20/month per user to custom pricing. Free trial available.
Rating:
- Ease of Use: 5
- Features: 4.5
- Customer Support: 4.5
- Security: 4
eMaint
eMaint offers a highly adaptable platform for equipment maintenance, allowing users to modify features based on specific operational requirements. Custom work order templates can include necessary documents and images. Interactive floor planning tools enable users to visualize asset locations and statuses.
eMaint supports multi-site, multilingual environments, allowing companies to personalize settings for language and currency. Although the extensive customization options come with a steeper learning curve and higher costs for premium features, eMaint’s ability to efficiently tailor the software to specific operational requirements makes it a standout choice.
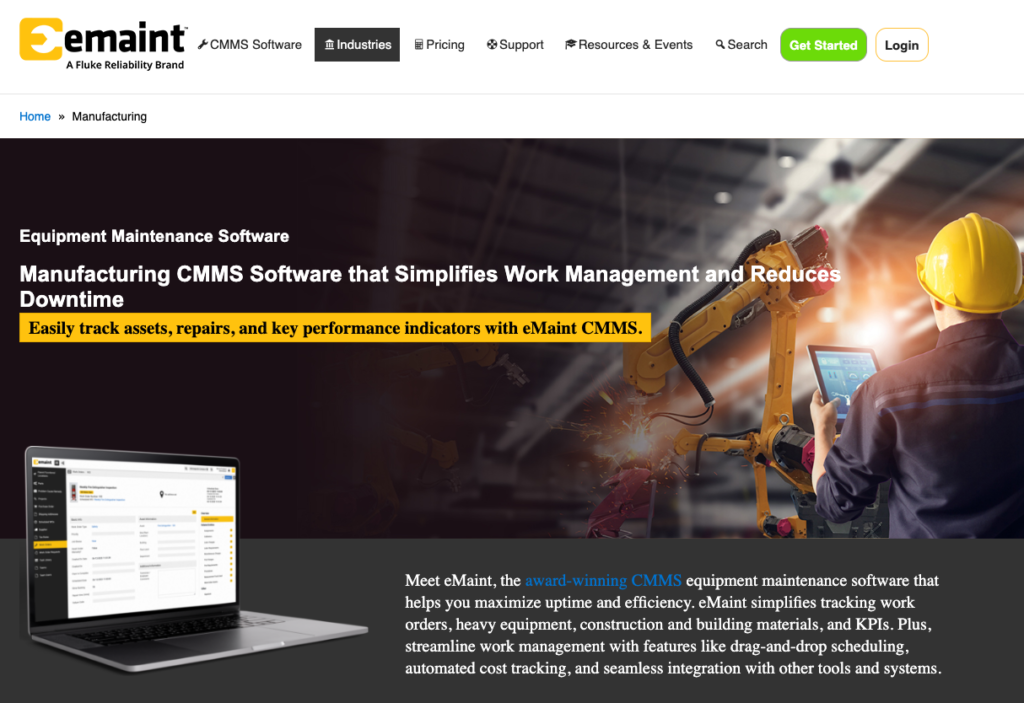
Key Features of eMaint:
- Easily create, track, and manage work orders, including multi-asset work orders, with customizable templates and automated workflows.
- Plan and schedule preventive maintenance using an intuitive, drag-and-drop calendar that helps prevent equipment downtime by triggering work orders based on asset health data.
- Track real-time status and history of assets, view interactive floor plans, and access asset details through mobile devices or barcode/QR code scanning.
- Monitor inventory levels, track spare parts across multiple locations, and automate reordering to prevent shortages and overspending.
- omplete work orders, manage tasks, and access asset information in the field, even offline, through a mobile app that syncs data once reconnected.
- Generate real-time reports on KPIs such as equipment downtime, response times, and preventive maintenance ratios to optimize maintenance operations.
Pros:
- Highly adaptable platform
- Custom work order templates
- Multi-site, multilingual support
Cons:
- No free version
- Higher cost for premium features
Pricing:
Team ($69/User/Month), Professional ($85/User/Month) and Enterprise Plan (contact for pricing) available.
Rating:
- Ease of Use: 4
- Features: 4.5
- Customer Support: 4.5
- Security: 4.5
How to Choose the Best Construction Equipment Maintenance Software
Choosing the best construction equipment maintenance software requires assessing several key factors to ensure it meets your needs. Start by considering essential features like asset management, work order management, and reporting analytics, which are crucial for effective maintenance management.
Consider integration capabilities next. Software that integrates with other systems, such as accounting and project management tools, enhances operational efficiency and ensures data accuracy by facilitating a single point of entry. Additionally, a user-friendly interface is essential for personnel with varying levels of technical expertise.Finally, evaluate customization options and scalability. The software should adapt to unique workflows and grow with your expanding fleet and operational needs. Consider total ownership costs and potential return on investment, beyond the initial purchase price. By carefully assessing these factors, you can select the best software to meet your maintenance costs and enhance operational efficiency.
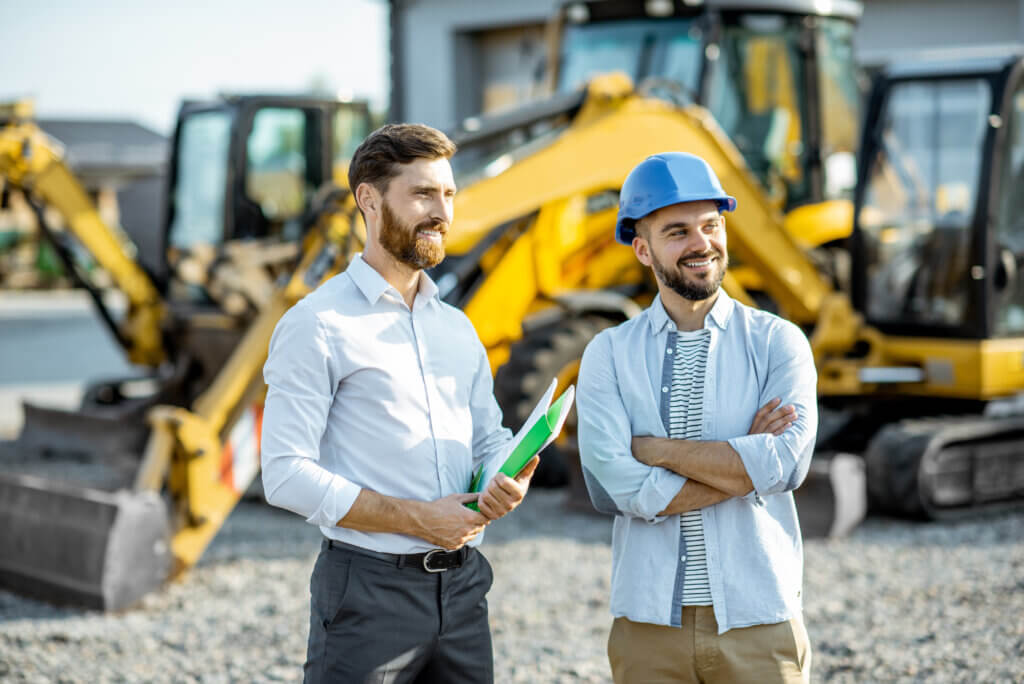
Conclusion: Choose ToolSense for the best all-in-one solution
ToolSense stands out as the top all-in-one preventive maintenance software due to its comprehensive asset management and workflow automation capabilities. The software integrates real-time IoT data, allowing users to make informed maintenance decisions and streamline operations.
With its user-friendly interface and mobile accessibility, ToolSense is designed to scale with businesses and accommodate growing asset portfolios without compromising functionality. Choosing ToolSense ensures that you have the best software to manage your assets efficiently and effectively.
Calculate How Much Money You Can Save With ToolSense!
ToolSense is trusted by 700+ companies
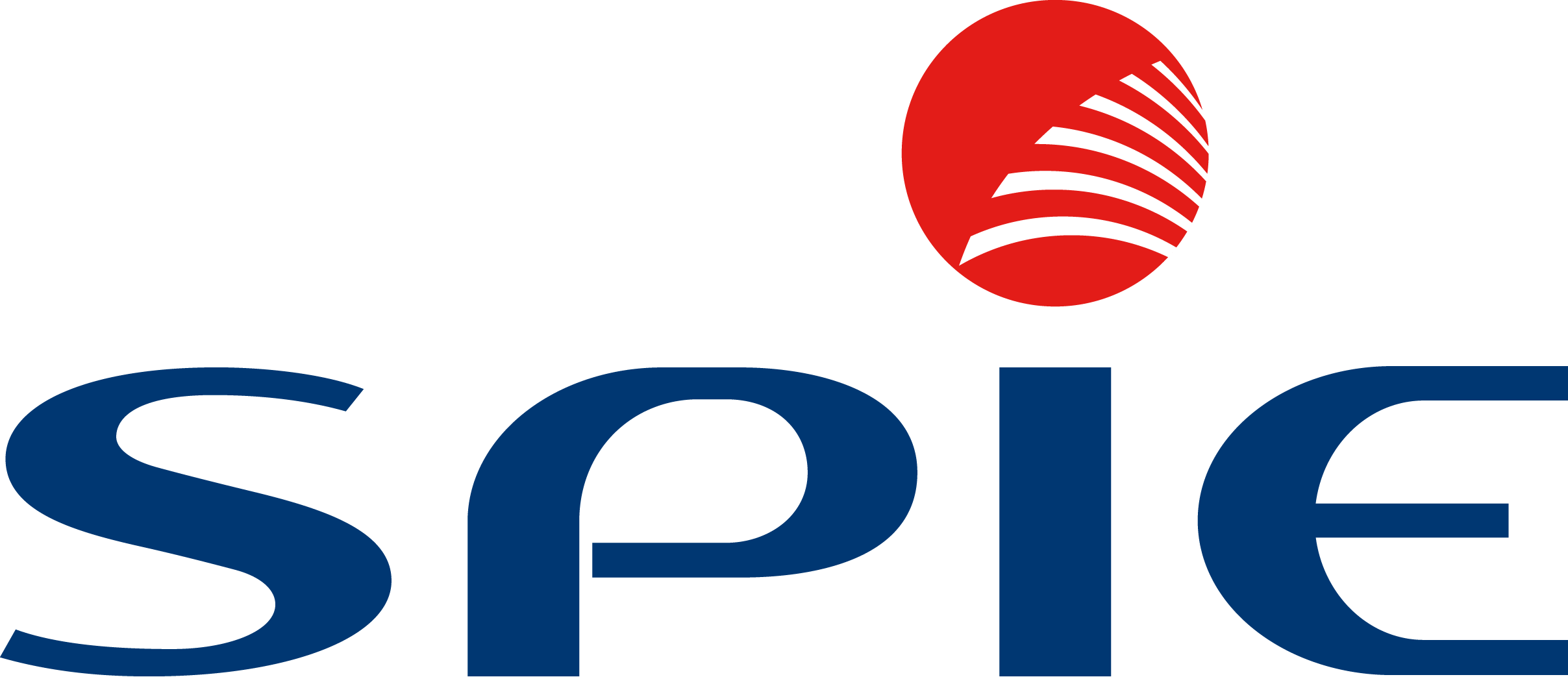
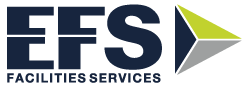
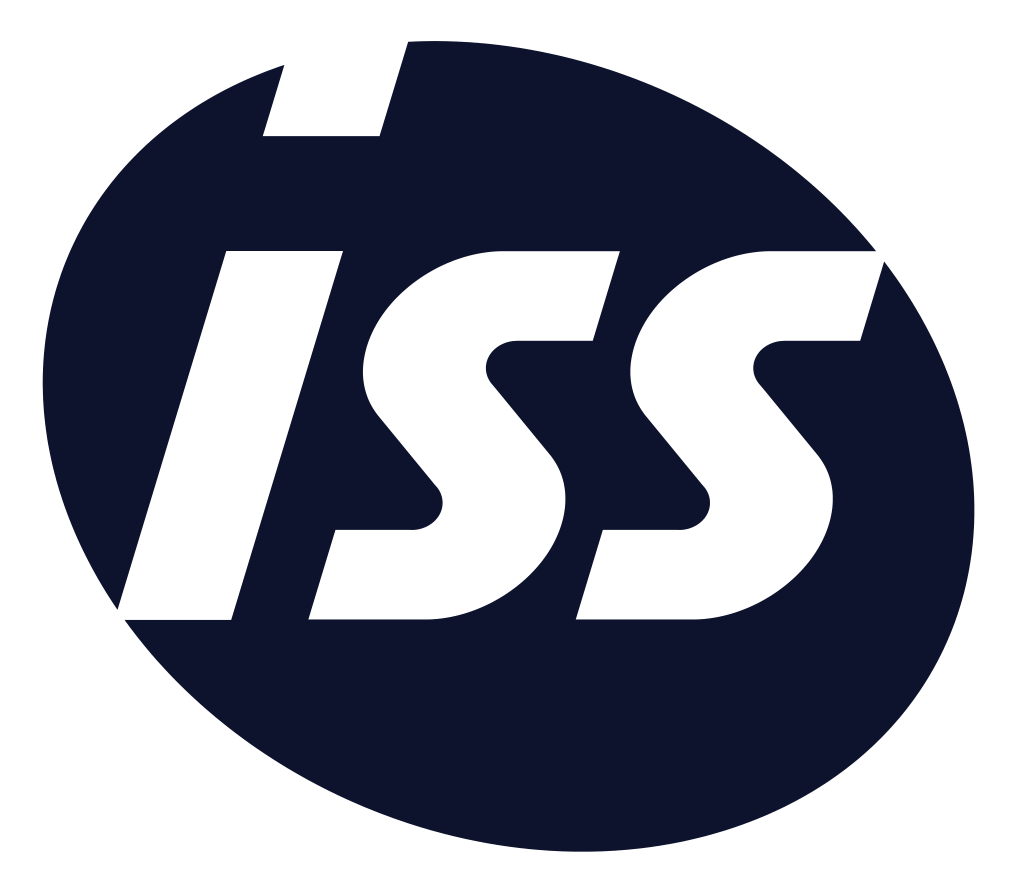
Frequently Asked Questions About Construction Equipment Maintenance Software
Construction equipment maintenance software is a digital tool used to manage the maintenance, repairs, and overall lifecycle of construction heavy machinery. It helps schedule preventive maintenance, track equipment usage, and monitor spare parts inventory to reduce downtime and extend equipment life. The software often includes mobile access, work order management, and reporting features to optimize maintenance workflows and improve operational efficiency
ToolSense is highly regarded for its comprehensive asset management capabilities, providing a unified platform that streamlines the management of all construction equipment. Other good software solutions include Limble CMMS and UpKeep.
ToolSense enhances preventive maintenance by automating schedules and delivering detailed reporting, which minimizes equipment downtime and helps avert potential failures. ToolSense also backs up your data, takes care of all security installs and updates, and manages all regular maintenance on the services.
ToolSense stands out for its exceptional integration capabilities, connecting with thousands of systems via APIs for seamless data transfer and updates. This allows businesses to effectively streamline their operations.
Using ToolSense enhances mobile accessibility by allowing maintenance teams to manage operations and work orders from anywhere, leading to real-time updates and increased productivity. This ensures that your team can stay efficient, regardless of location.
The software solutions presented in this article, and their ranking, reflect both our opinion and that of our customers. While we can’t claim to have looked at them with complete objectivity, we do believe we offer a top-notch solution. Not convinced yet? We warmly invite you to form your view during our complimentary 30-day trial period.